- お役立ち記事
- How production management leaders in the automotive industry should know how to increase on-site efficiency using cell production methods
How production management leaders in the automotive industry should know how to increase on-site efficiency using cell production methods
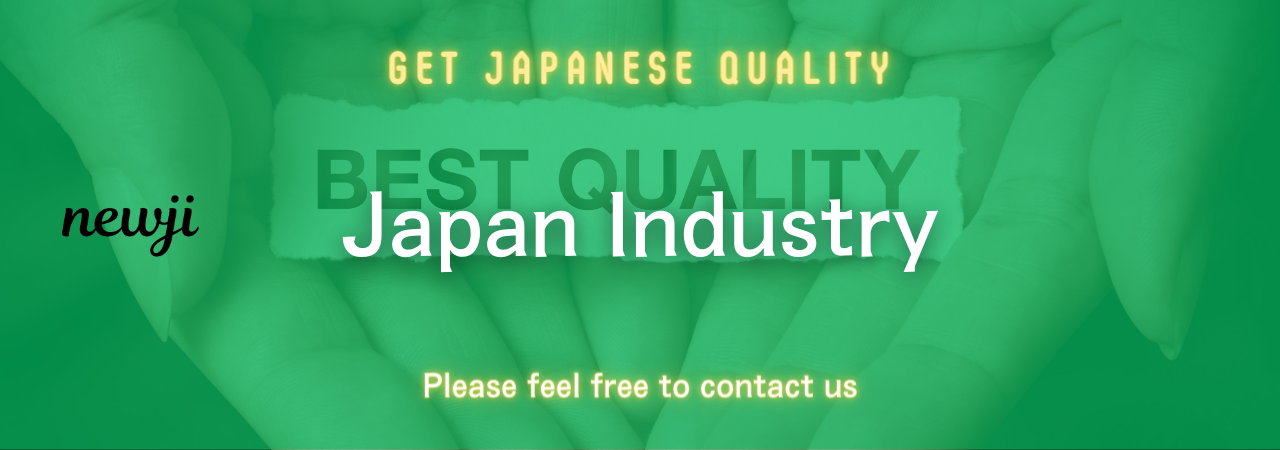
目次
Understanding Cell Production in the Automotive Industry
The automotive industry is a complex network where efficiency and productivity are key to success.
With constant demand for new technology and quicker production timelines, industry leaders are always on the lookout for methods to streamline their processes.
One such method that has gained popularity is cell production.
But what exactly is cell production, and how can it benefit automotive production management?
In this article, we’ll explore these questions and provide insights into how this method can increase on-site efficiency.
What is Cell Production?
Cell production is a manufacturing method where workstations or cells are arranged to facilitate workflow in a more seamless manner.
Each cell is responsible for completing a specific segment of the production process.
This ensures that tasks are completed in a continuous flow rather than in isolated steps.
In traditional assembly lines, each worker or machine performs a single task repetitively.
In contrast, cell production allows for flexibility and the opportunity for cross-training employees to handle various tasks within a cell.
This leads to a more dynamic and adaptive production process.
Benefits of Implementing Cell Production
There are several benefits associated with implementing cell production in the automotive industry:
Increased Efficiency
The primary advantage of cell production is the increase in efficiency.
By optimizing the layout of workstations and reducing unnecessary movement, cell production minimizes wasted time.
Workers can focus on completing tasks without the interruptions and delays that are often present in traditional assembly lines.
Improved Quality Control
With cell production, each team can take ownership of the quality of their output.
Smaller teams working within cells can identify and address issues more quickly than in a larger, segmented production line.
This constant attention to quality helps maintain high standards and reduces the need for extensive inspections down the line.
Flexibility and Adaptability
Cell production allows production lines to be more flexible and adaptable.
Since workers are cross-trained, they can be moved between tasks or cells to address bottlenecks or increased demand.
This agility is crucial in the fast-paced automotive industry where production requirements can change rapidly.
Employee Satisfaction
Employees working in cell production systems often report higher job satisfaction.
Cross-training opportunities provide not only skill development but also variety in daily tasks.
By working in smaller teams, employees often feel a greater sense of camaraderie and achievement, fostering a positive work environment.
Steps to Implement Cell Production
Transitioning to a cell production method requires careful planning and execution.
Here are some steps that production management leaders can take to implement cell production effectively:
Analyze Current Processes
Before making any changes, conduct a thorough analysis of existing production processes.
Identify areas where bottlenecks occur, where waste is evident, and where improvements can be made.
This analysis will help in designing effective cell layouts that address specific issues.
Design the Layout
Designing the layout is crucial in establishing a working cell production system.
Arrange workstations in a way that promotes easy flow and movement.
Consider the logical sequence of tasks and how materials and information will move through each cell.
Layouts should minimize downtime and maximize connectivity between tasks.
Cross-Train Employees
A successful cell production system relies heavily on the flexibility of employees.
Provide training sessions that equip workers with the skills they need to effectively perform multiple tasks within a cell.
Encourage skill sharing and peer learning to promote a culture of continuous development.
Monitor and Adjust
Once the cell production system is in place, continuously monitor its performance.
Collect data on cycle times, quality metrics, and employee feedback.
Use this data to identify areas for further improvement and adjust processes as needed.
Regular monitoring ensures that the cell production method remains effective and continues to yield desired outcomes.
Challenges of Cell Production
While cell production offers many benefits, it’s important to acknowledge and prepare for potential challenges:
Initial Setup Costs
Transitioning to a cell production system may require significant investment in terms of rearranging existing facilities, purchasing new equipment, and training employees.
It’s essential for production leaders to budget for these costs and weigh them against the long-term benefits of increased efficiency.
Change Management
Implementing cell production often involves substantial changes in the workplace.
Change management strategies should be employed to ensure smooth transitions.
This includes communicating the benefits of the new system to employees, addressing any concerns, and providing support during the adjustment period.
Balancing Workloads
Maintaining balanced workloads across cells is crucial to prevent bottlenecks and maintain efficiency.
Production leaders must carefully monitor workflow to ensure that no cell is overwhelmed or under-utilized.
Dynamic scheduling and clear communication can help achieve this balance.
Conclusion
Cell production is a powerful method that offers numerous benefits for the automotive industry, from increased efficiency and improved quality control to enhanced employee satisfaction.
By carefully planning and implementing cell production, leaders in the automotive sector can drive their production lines to new heights of excellence.
The shift towards cell production is not without its challenges, but with dedication and strategic planning, these challenges can be effectively managed.
With the demand for automotive innovations on the rise, embracing cell production methods is a step toward ensuring that production capabilities can meet the industry’s evolving needs.
資料ダウンロード
QCD調達購買管理クラウド「newji」は、調達購買部門で必要なQCD管理全てを備えた、現場特化型兼クラウド型の今世紀最高の購買管理システムとなります。
ユーザー登録
調達購買業務の効率化だけでなく、システムを導入することで、コスト削減や製品・資材のステータス可視化のほか、属人化していた購買情報の共有化による内部不正防止や統制にも役立ちます。
NEWJI DX
製造業に特化したデジタルトランスフォーメーション(DX)の実現を目指す請負開発型のコンサルティングサービスです。AI、iPaaS、および先端の技術を駆使して、製造プロセスの効率化、業務効率化、チームワーク強化、コスト削減、品質向上を実現します。このサービスは、製造業の課題を深く理解し、それに対する最適なデジタルソリューションを提供することで、企業が持続的な成長とイノベーションを達成できるようサポートします。
オンライン講座
製造業、主に購買・調達部門にお勤めの方々に向けた情報を配信しております。
新任の方やベテランの方、管理職を対象とした幅広いコンテンツをご用意しております。
お問い合わせ
コストダウンが利益に直結する術だと理解していても、なかなか前に進めることができない状況。そんな時は、newjiのコストダウン自動化機能で大きく利益貢献しよう!
(Β版非公開)