- お役立ち記事
- For production engineers in the electronic equipment manufacturing industry! How to improve soldering quality by setting the reflow oven temperature profile
For production engineers in the electronic equipment manufacturing industry! How to improve soldering quality by setting the reflow oven temperature profile
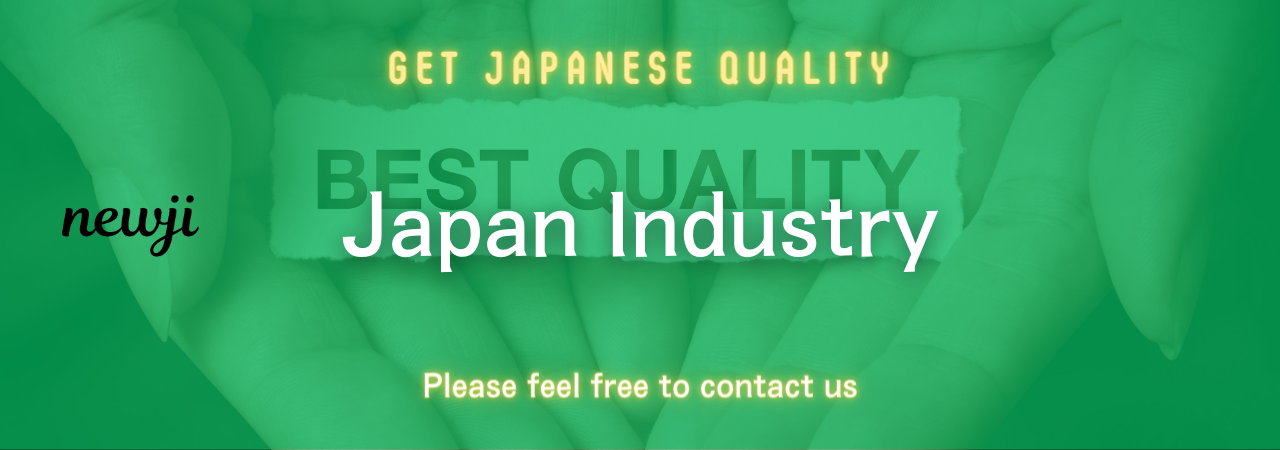
目次
Understanding the Importance of Reflow Oven Temperature Profile
For production engineers in the electronic equipment manufacturing industry, improving soldering quality is crucial for ensuring product reliability and performance.
A key factor in achieving this is the accurate setting of the reflow oven temperature profile.
This profile dictates how the solder paste is liquefied and solidified during the assembly process, greatly influencing the quality of the solder joints.
By understanding and optimizing this temperature profile, engineers can significantly enhance the quality of the products being manufactured.
The Basics of Reflow Soldering
To improve soldering quality, it’s essential first to understand what reflow soldering is.
This process involves the use of a reflow oven, which melts solder paste to form welded bonds between electronic components and printed circuit boards (PCBs).
The temperature profile within the oven dictates how effectively this bonding process occurs.
This profile is divided into several stages, including preheat, soak, reflow, and cooling, each playing a critical role in forming reliable solder joints.
Preheat Stage
The preheat stage aims to gradually raise the temperature of the electronic components and the PCB to prevent thermal shock.
Thermal shock can cause the components to crack or warp, leading to faulty connections and poor soldering quality.
During this stage, uniform heating is also crucial to evaporate any volatile fumes present in the solder paste.
Soak Stage
Once the preheat stage is complete, the temperature is maintained during the soak stage.
The purpose of this phase is to activate the flux in the solder paste, which facilitates the removal of oxides and helps the solder flow more effectively.
Uniform activation across all components and boards ensures consistency throughout the soldering process.
Reflow Stage
The reflow stage is where the actual melting of the solder occurs.
The temperature profile reaches its peak during this phase, allowing the solder to liquefy and create secure connections between components and the PCB.
The key here is to ensure the temperature is just right: hot enough to melt the solder quickly but not so hot that it damages the components.
Cooling Stage
Finally, the cooling stage solidifies the solder, locking the components into place.
This stage needs to be controlled carefully to prevent the formation of defects such as voids or cracking.
A properly cooled joint is essential for the long-term reliability of the product.
Optimizing the Reflow Oven Temperature Profile
For production engineers, optimizing the reflow oven temperature profile is a critical step in enhancing soldering quality.
This requires an understanding of various factors, including the properties of the solder paste and the components being soldered.
Tailoring the Profile to the Solder Paste
Different solder pastes require different temperature profiles.
Lead-free solder paste, for example, typically necessitates higher temperatures compared to traditional lead-based pastes.
Understanding the thermal characteristics and recommended profiles provided by the solder paste manufacturer is vital for setting the optimal profile in the reflow oven.
Considering Component Sensitivity
Electronic components vary widely in their thermal sensitivity.
Components like plastic connectors may not withstand the same heat levels as metal or ceramic parts.
By identifying the most sensitive components on the PCB, engineers can adjust the temperature profile to accommodate these parts without compromising soldering quality.
Performing Test Runs
Before starting full-scale production, it’s beneficial to perform test runs with different temperature profiles.
This helps determine how effectively the solder paste is reacting at various temperature levels, allowing for fine-tuning of the profile.
Using thermal profiling tools can provide insights into how heat is distributed across the board, helping to achieve consistent results.
Monitoring and Adjusting
Regular monitoring of the reflow process is crucial for maintaining high soldering quality.
Changes in the PCB layout, components, or paste formulation may necessitate adjustments to the temperature profile.
Ongoing assessments help ensure that the profile remains optimized for current production conditions.
Implementing Best Practices in Reflow Soldering
Beyond setting the temperature profile, adhering to best practices in reflow soldering can further boost quality.
Ensuring Cleanliness
Contaminants such as dust or residue can interfere with the soldering process and compromise joint quality.
Keeping the PCB and components clean prior to assembly is essential for avoiding defects.
Aligning Components Precisely
Proper alignment of components before entering the reflow oven ensures that the solder forms connections exactly where needed.
This involves precise PCB layout design and accurate placement during assembly.
Maintaining Equipment Performance
Regular maintenance of the reflow oven is crucial for its optimal performance.
Ensuring that heating elements and conveyors function correctly will help in achieving consistent temperature profiles and, consequently, high-quality soldering.
Conclusion
For production engineers striving to improve soldering quality in the electronic equipment manufacturing industry, the reflow oven temperature profile is a fundamental element.
By understanding the importance of each stage in the reflow process, tailoring the profile to the specific solder paste and components, and implementing best practices, engineers can greatly enhance the reliability and performance of their products.
With careful monitoring and adjustments, achieving high-quality soldering is well within reach.
資料ダウンロード
QCD調達購買管理クラウド「newji」は、調達購買部門で必要なQCD管理全てを備えた、現場特化型兼クラウド型の今世紀最高の購買管理システムとなります。
ユーザー登録
調達購買業務の効率化だけでなく、システムを導入することで、コスト削減や製品・資材のステータス可視化のほか、属人化していた購買情報の共有化による内部不正防止や統制にも役立ちます。
NEWJI DX
製造業に特化したデジタルトランスフォーメーション(DX)の実現を目指す請負開発型のコンサルティングサービスです。AI、iPaaS、および先端の技術を駆使して、製造プロセスの効率化、業務効率化、チームワーク強化、コスト削減、品質向上を実現します。このサービスは、製造業の課題を深く理解し、それに対する最適なデジタルソリューションを提供することで、企業が持続的な成長とイノベーションを達成できるようサポートします。
オンライン講座
製造業、主に購買・調達部門にお勤めの方々に向けた情報を配信しております。
新任の方やベテランの方、管理職を対象とした幅広いコンテンツをご用意しております。
お問い合わせ
コストダウンが利益に直結する術だと理解していても、なかなか前に進めることができない状況。そんな時は、newjiのコストダウン自動化機能で大きく利益貢献しよう!
(Β版非公開)