- お役立ち記事
- Ink adjustment methods to improve the comfort of writing instruments that new employees in the research and development departments of stationery manufacturing companies should learn
Ink adjustment methods to improve the comfort of writing instruments that new employees in the research and development departments of stationery manufacturing companies should learn
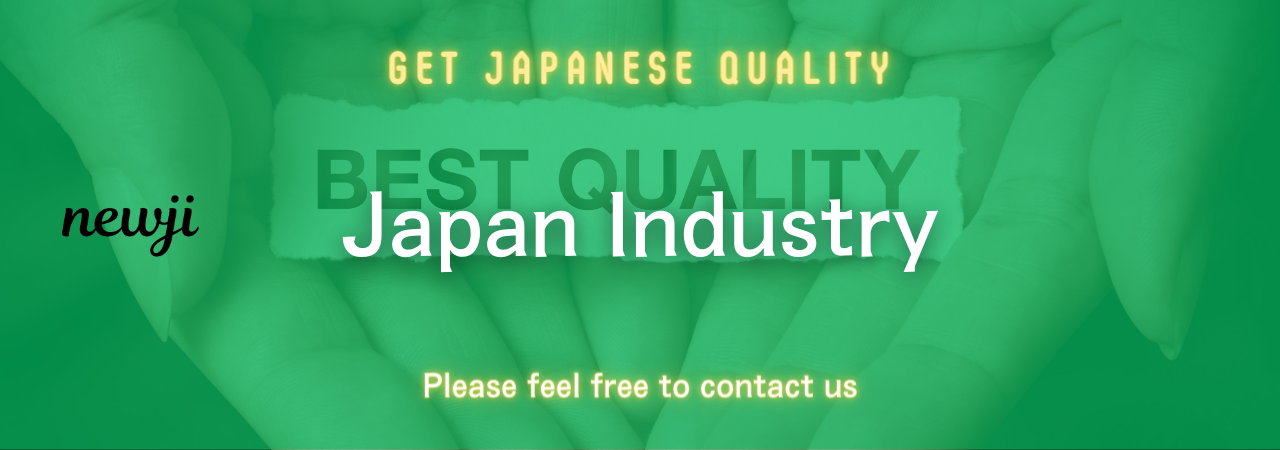
目次
Understanding Ink Viscosity and Its Impact on Writing Comfort
For new employees in the research and development departments of stationery manufacturing companies, understanding ink viscosity is crucial.
Ink viscosity refers to the thickness or thinness of the ink, which significantly influences the writing experience.
Different viscosities can affect how smoothly the pen glides across the paper, the drying time of the ink, and the ease with which it flows from the pen.
A high viscosity ink will be thicker, potentially leading to a more controlled flow but possibly causing the ink to drag on the paper.
On the other hand, low viscosity ink is thinner and can provide a smoother experience but risk leaking or smudging.
Adjusting ink viscosity is a balancing act that can enhance the user’s comfort and satisfaction with their writing instrument.
Choosing the Right Pigments for Consistent Color Quality
Selecting appropriate pigments is another vital aspect of developing comfortable writing instruments.
Pigments contribute to the color and opacity of the ink, and their quality can affect the ink’s performance on paper.
New R&D employees should aim to use pigments that provide strong color consistency and vibrancy while maintaining smooth flow properties.
Experimenting with synthetic and natural pigments can offer varying results.
Synthetic pigments might offer more intense colors and better consistency, whereas natural pigments can bring unique shades and textures.
Testing different pigment combinations will allow for a greater understanding of how they interact with various ink formulations.
Understanding Solvent Combinations for Optimal Ink Flow
The role of solvents in ink formulations is to help dissolve other components and manage the viscosity and drying time.
An optimal solvent combination can ensure that the ink flows smoothly and dries quickly without smudging.
Common solvents include water, alcohols, and oils, each offering distinct properties.
Water-based inks are popular for their non-toxic and easy-to-clean nature.
Alcohol-based solvents evaporate quickly, making them ideal for fast-drying inks, while oil-based solutions often provide richer, more vibrant colors.
Research and development employees should explore how different solvent ratios can improve writing comfort by testing for smooth flow and quick drying attributes.
Adjusting pH Levels to Enhance Ink Performance
Ink pH levels are a significant factor that can affect both ink performance and the lifespan of writing instruments.
Maintaining a balanced pH ensures that the ink is not too acidic or alkaline, which can lead to corrosion or dysfunctional pen parts.
Neutral pH levels are often considered ideal to prevent damage while also providing a comfortable writing experience.
Employees should regularly test pH levels and adjust the ink formulation accordingly, using buffers and stabilizers as needed to maintain consistency.
The Role of Additives in Ink Formulation
Additives are crucial components that can enhance or modify the ink’s characteristics for improved writing comfort.
These include anti-smudging agents, which help ink dry faster, or viscosity modifiers, which help achieve the perfect ink flow.
For example, humectants can be added to prevent the ink from drying out too quickly, thus providing a smoother writing experience.
Meanwhile, surfactants can aid in adjusting surface tension for better ink distribution on paper.
By experimenting with various additives, research and development employees can fine-tune inks to meet specific requirements, ensuring they cater to different writing preferences.
Collaborating with Design Teams for Better Product Development
Active collaboration between research and development employees and design teams can significantly enhance the final product’s quality.
By understanding design considerations, such as pen grip and nib size, R&D teams can tailor ink formulations that best suit the ergonomic designs of new writing instruments.
Regular meetings should be scheduled to discuss design feedback and ink performance.
Such collaborations ensure that the ink complements the mechanical setup and aesthetics of the pen, contributing to overall user comfort and satisfaction.
Conducting User Testing for Satisfaction and Comfort
User testing is an integral part of developing comfortable writing instruments.
Allowing end users to test prototypes provides essential feedback on the writing experience, including comfort, ease of use, and whether their needs are being met.
Surveys and focus groups can reveal valuable insights into user preferences and any issues they encounter.
By incorporating this feedback, new employees in research and development can make informed adjustments to ensure that the final product is well-received in the market.
Continuous Improvement and Innovation in Ink Formulation
Innovating and improving ink formulations is an ongoing process.
Research and development employees should stay informed about new materials, technologies, and market trends to maintain a competitive edge.
Participating in industry workshops, attending conferences, and collaborating with universities can provide fresh ideas and techniques.
By adopting a mindset of continuous innovation, new employees can contribute significantly to developing writing instruments that offer ultimate comfort and performance.
In conclusion, new employees in the R&D departments of stationery manufacturing companies play a vital role in adjusting ink compositions for improved comfort in writing instruments.
By understanding aspects such as viscosity, pigments, solvents, pH levels, and additives, and collaborating effectively with other professionals, they can create products that delight users and enhance their writing experiences.
資料ダウンロード
QCD調達購買管理クラウド「newji」は、調達購買部門で必要なQCD管理全てを備えた、現場特化型兼クラウド型の今世紀最高の購買管理システムとなります。
ユーザー登録
調達購買業務の効率化だけでなく、システムを導入することで、コスト削減や製品・資材のステータス可視化のほか、属人化していた購買情報の共有化による内部不正防止や統制にも役立ちます。
NEWJI DX
製造業に特化したデジタルトランスフォーメーション(DX)の実現を目指す請負開発型のコンサルティングサービスです。AI、iPaaS、および先端の技術を駆使して、製造プロセスの効率化、業務効率化、チームワーク強化、コスト削減、品質向上を実現します。このサービスは、製造業の課題を深く理解し、それに対する最適なデジタルソリューションを提供することで、企業が持続的な成長とイノベーションを達成できるようサポートします。
オンライン講座
製造業、主に購買・調達部門にお勤めの方々に向けた情報を配信しております。
新任の方やベテランの方、管理職を対象とした幅広いコンテンツをご用意しております。
お問い合わせ
コストダウンが利益に直結する術だと理解していても、なかなか前に進めることができない状況。そんな時は、newjiのコストダウン自動化機能で大きく利益貢献しよう!
(Β版非公開)