- お役立ち記事
- For production engineers in the apparel manufacturing industry! A method to achieve both product quality and productivity by increasing the efficiency of sewing lines
For production engineers in the apparel manufacturing industry! A method to achieve both product quality and productivity by increasing the efficiency of sewing lines
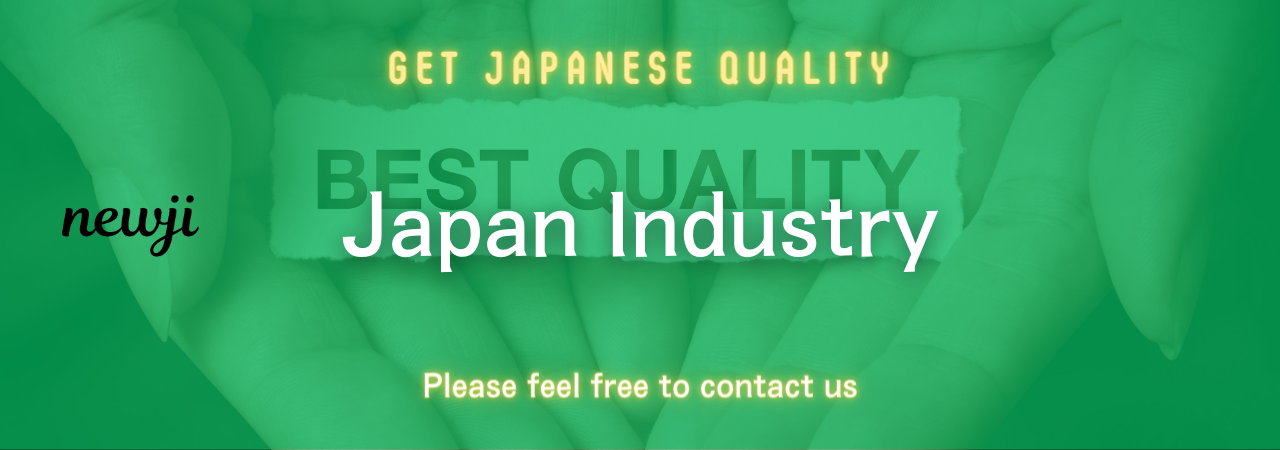
目次
Introduction
In the fast-paced world of apparel manufacturing, production engineers face the challenging task of balancing product quality with productivity.
The efficiency of sewing lines is a critical factor that can significantly impact this balance.
Effective strategies that streamline operations without compromising quality can lead to success in this competitive industry.
This article explores practical methods to enhance sewing line efficiency, ensuring high-quality output and increased productivity.
Understanding Sewing Line Efficiency
Sewing line efficiency refers to the smooth flow of garment production processes with minimal downtime and waste.
An efficient sewing line maximizes the use of resources, including time, labor, and materials.
Improving efficiency not only boosts productivity but also maintains the high standards of product quality essential for brand reputation and customer satisfaction.
Identifying Bottlenecks
The first step in improving sewing line efficiency is to identify bottlenecks.
Bottlenecks are points in the production process where the workflow slows down.
They can occur due to various reasons, such as machine malfunctions, skill gaps among workers, or inefficient layout designs.
By conducting a thorough analysis, production engineers can pinpoint these obstacles and implement corrective actions.
Strategies for Increasing Sewing Line Efficiency
Several strategies can be employed by production engineers to enhance the efficiency of sewing lines:
1. Lean Manufacturing Techniques
Lean manufacturing techniques focus on eliminating waste and optimizing processes.
By adopting lean principles, production engineers can streamline workflows, reduce overproduction, and minimize inventory.
This not only enhances sewing line efficiency but also contributes to sustainable manufacturing practices.
2. Standardization of Processes
Standardizing procedures across sewing lines ensures consistency and uniformity in production.
Creating standard operating procedures (SOPs) for each task helps reduce variability and errors.
This leads to faster training of new employees and improves overall line efficiency.
3. Advanced Training Programs
Investing in advanced training programs for sewing line workers can have a significant impact on efficiency.
Training programs should focus on enhancing technical skills, problem-solving abilities, and teamwork.
Skilled workers can execute tasks more quickly and accurately, reducing errors and increasing productivity.
4. Utilization of Cutting-Edge Technology
Incorporating technology in sewing lines can revolutionize production processes.
Automation, for instance, can handle repetitive tasks with precision, freeing up human resources for more complex tasks.
Additionally, the use of data analytics tools can provide real-time insights into line performance, enabling prompt decision-making.
5. Optimal Layout Design
The layout of a sewing line plays a vital role in its efficiency.
An optimal layout minimizes unnecessary movement and transportation, ensuring a smooth and continuous workflow.
Production engineers should evaluate and redesign sewing line layouts based on ergonomic principles and process flow diagrams to enhance productivity.
6. Quality Control Integration
Integrating quality control mechanisms within the sewing line, rather than at the end of the process, prevents defects from progressing through the production line.
This proactive approach to quality control saves time and resources, ensuring that only high-quality products reach the next stage of production.
Balancing Quality and Productivity
While increasing sewing line efficiency is crucial for productivity, maintaining product quality should remain a top priority.
A balanced approach involves:
1. Continuous Monitoring and Improvement
Production engineers should implement systems for continuous monitoring of sewing line performance.
Regular feedback loops allow for quick identification and resolution of issues, maintaining both quality and productivity.
2. Collaborating with Cross-Functional Teams
Collaboration between production engineers, quality assurance teams, and other departments ensures that efficiency improvements are aligned with quality goals.
Effective communication and teamwork facilitate the integration of new strategies and technologies seamlessly into existing workflows.
3. Setting Realistic Targets
Setting achievable efficiency targets that do not compromise quality is essential.
Overambitious goals can lead to cutting corners and potentially sacrificing quality.
Performance metrics should be reviewed regularly, and goals adjusted as necessary to balance efficiency with product standards.
Conclusion
Enhancing the efficiency of sewing lines in the apparel manufacturing industry is a continuous process that requires strategic planning and execution.
By adopting lean manufacturing techniques, standardizing processes, investing in training, utilizing technology, optimizing layouts, and integrating quality control, production engineers can achieve an optimal balance between productivity and product quality.
As a result, apparel manufacturers can thrive in a competitive market, delivering high-quality products efficiently and effectively.
資料ダウンロード
QCD調達購買管理クラウド「newji」は、調達購買部門で必要なQCD管理全てを備えた、現場特化型兼クラウド型の今世紀最高の購買管理システムとなります。
ユーザー登録
調達購買業務の効率化だけでなく、システムを導入することで、コスト削減や製品・資材のステータス可視化のほか、属人化していた購買情報の共有化による内部不正防止や統制にも役立ちます。
NEWJI DX
製造業に特化したデジタルトランスフォーメーション(DX)の実現を目指す請負開発型のコンサルティングサービスです。AI、iPaaS、および先端の技術を駆使して、製造プロセスの効率化、業務効率化、チームワーク強化、コスト削減、品質向上を実現します。このサービスは、製造業の課題を深く理解し、それに対する最適なデジタルソリューションを提供することで、企業が持続的な成長とイノベーションを達成できるようサポートします。
オンライン講座
製造業、主に購買・調達部門にお勤めの方々に向けた情報を配信しております。
新任の方やベテランの方、管理職を対象とした幅広いコンテンツをご用意しております。
お問い合わせ
コストダウンが利益に直結する術だと理解していても、なかなか前に進めることができない状況。そんな時は、newjiのコストダウン自動化機能で大きく利益貢献しよう!
(Β版非公開)