- お役立ち記事
- A must-read for mid-level employees: Thorough risk assessment methods to avoid failure when selecting suppliers
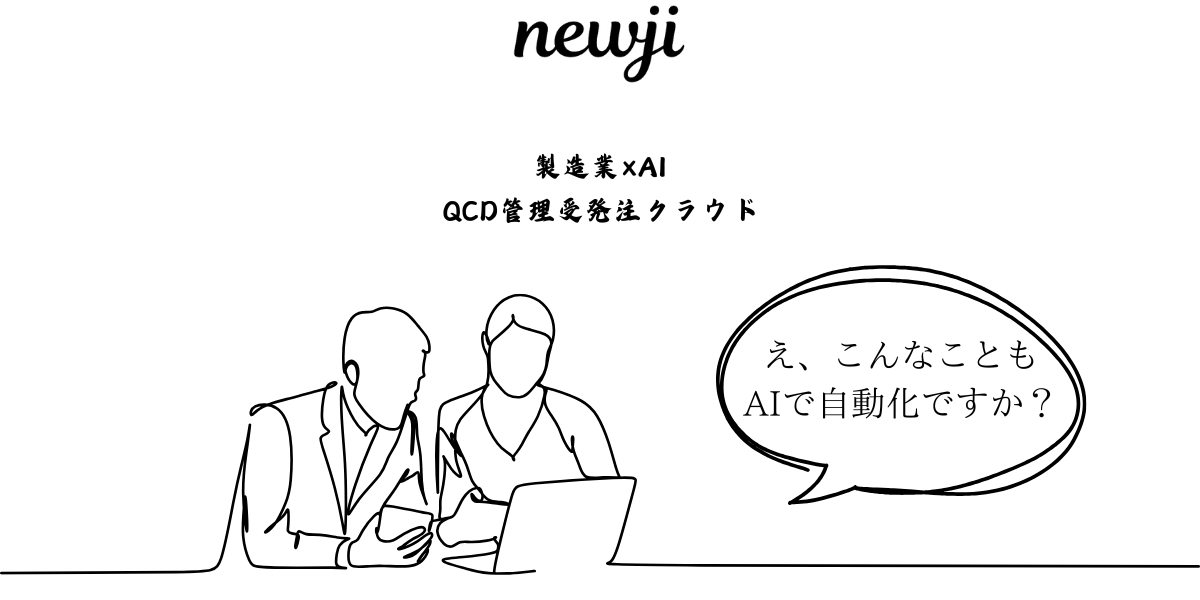
A must-read for mid-level employees: Thorough risk assessment methods to avoid failure when selecting suppliers
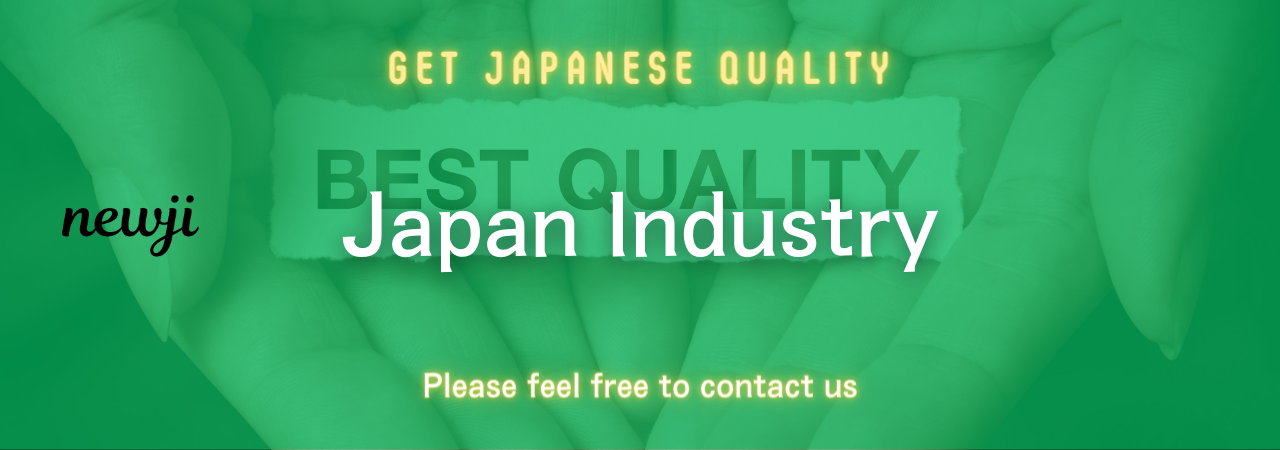
目次
Understanding the Importance of Risk Assessment
Choosing the right suppliers is a critical decision that mid-level employees often face in a company.
With the increasing complexities in supply chains, businesses must adopt thorough risk assessment methods to avoid potential failures.
Understanding the importance of risk assessment can significantly minimize disruptions and ensure smooth operations.
Suppliers play an essential role in delivering raw materials, components, and services crucial for production and business continuity.
Risk assessments help identify any potential issues that may arise from working with particular suppliers.
These issues can include financial instability, non-compliance with regulations, or unreliable delivery schedules.
A comprehensive assessment aids in the early detection of problems, allowing companies to mitigate them before they escalate.
It ensures the selection of suppliers who align with the company’s standards and expectations, thus safeguarding the business from unnecessary losses.
Key Components of Risk Assessment
When conducting a risk assessment for supplier selection, several key components should be considered.
These components ensure a robust and thorough evaluation process.
Financial Stability
Evaluating a supplier’s financial stability is crucial.
It provides insights into their ability to fulfill orders reliably and on time.
This includes assessing their financial statements, credit ratings, and market reputation.
Financially unstable suppliers may face difficulties in meeting commitments, posing a significant risk to your supply chain.
Quality Assurance
Quality assurance is another vital component.
Ensure that potential suppliers have stringent quality control processes in place.
This involves checking their production capabilities, certifications, and customer feedback.
Suppliers who fail to meet quality standards can damage a company’s reputation and result in costly returns or delays.
Compliance and Regulatory Adherence
Compliance with industry regulations and standards is non-negotiable.
A supplier who does not adhere to environmental, safety, and labor regulations can expose your company to legal risks.
It is essential to verify their compliance records and any certifications they hold to ensure they meet required regulatory criteria.
Operational Capacity and Reliability
Determine the supplier’s operational capacity and reliability by evaluating their production processes, delivery timelines, and past performance.
This assessment helps to gauge whether they can meet your demands consistently.
A reliable supplier will have a history of meeting deadlines and a track record of maintaining operational efficiency.
Technological Capability and Innovation
Assess the supplier’s technological capabilities and innovation potential.
Suppliers who invest in technology are often more efficient, adaptable, and able to provide innovative solutions.
Their readiness to implement new technologies can indicate their commitment to continuous improvement and competitiveness in the market.
Steps for Conducting a Supplier Risk Assessment
By following a structured approach, businesses can conduct a comprehensive risk assessment for supplier selection.
Identify Risks
Begin by identifying potential risks associated with the supplier.
This includes financial risks, quality risks, operational risks, compliance risks, and reputational risks.
Listing these risks provides a foundation for further assessment and prioritization.
Research and Data Collection
Collect data on the potential supplier.
This can involve researching their history, financial documents, customer reviews, and industry news.
Gathering comprehensive data helps in creating an informed profile of the supplier.
Analyze and Evaluate Risks
Evaluate the data collected to analyze the risks.
Assess the significance of each risk and its potential impact on your business.
This may involve quantitative risk analysis tools or expert judgment to estimate the probability and consequence of risks.
Create a Risk Mitigation Plan
Develop a plan to mitigate identified risks.
This may involve negotiating contractual terms, diversifying your supplier base, or implementing monitoring systems.
Having a contingency plan is crucial to address any issues that might arise, minimizing disruptions.
Monitor and Review
Once a supplier is selected, continuous monitoring is essential.
Regularly review the supplier’s performance against agreed-upon metrics and adjust the risk mitigation plan as needed.
This dynamic approach ensures that any emerging risks are managed promptly.
The Benefits of Effective Risk Assessment
Implementing effective risk assessment methods offers numerous benefits.
It enhances decision-making by providing a clearer understanding of potential risks and their impacts.
It also promotes strong supplier relationships, as it is easier to build trust with suppliers who meet your standards and expectations.
Additionally, risk assessments contribute to business resilience, protecting the company from unexpected challenges and fostering long-term success.
Conclusion
Conducting thorough risk assessments when selecting suppliers is not merely a best practice but a necessity.
For mid-level employees, understanding and applying effective risk assessment methods can prevent costly failures and ensure strategic supplier partnerships.
By considering financial stability, quality, compliance, operational capacity, and technological capability, businesses can identify reliable suppliers who support their growth objectives.
Following structured assessment steps ensures a robust evaluation process, ultimately safeguarding the company’s interests.
In an ever-evolving market, being proactive and diligent in supplier risk assessments is key to sustained success.
資料ダウンロード
QCD調達購買管理クラウド「newji」は、調達購買部門で必要なQCD管理全てを備えた、現場特化型兼クラウド型の今世紀最高の購買管理システムとなります。
ユーザー登録
調達購買業務の効率化だけでなく、システムを導入することで、コスト削減や製品・資材のステータス可視化のほか、属人化していた購買情報の共有化による内部不正防止や統制にも役立ちます。
NEWJI DX
製造業に特化したデジタルトランスフォーメーション(DX)の実現を目指す請負開発型のコンサルティングサービスです。AI、iPaaS、および先端の技術を駆使して、製造プロセスの効率化、業務効率化、チームワーク強化、コスト削減、品質向上を実現します。このサービスは、製造業の課題を深く理解し、それに対する最適なデジタルソリューションを提供することで、企業が持続的な成長とイノベーションを達成できるようサポートします。
オンライン講座
製造業、主に購買・調達部門にお勤めの方々に向けた情報を配信しております。
新任の方やベテランの方、管理職を対象とした幅広いコンテンツをご用意しております。
お問い合わせ
コストダウンが利益に直結する術だと理解していても、なかなか前に進めることができない状況。そんな時は、newjiのコストダウン自動化機能で大きく利益貢献しよう!
(Β版非公開)