- お役立ち記事
- For design department leaders in the auto parts manufacturing industry! How to proceed with vibration analysis using CAE
For design department leaders in the auto parts manufacturing industry! How to proceed with vibration analysis using CAE
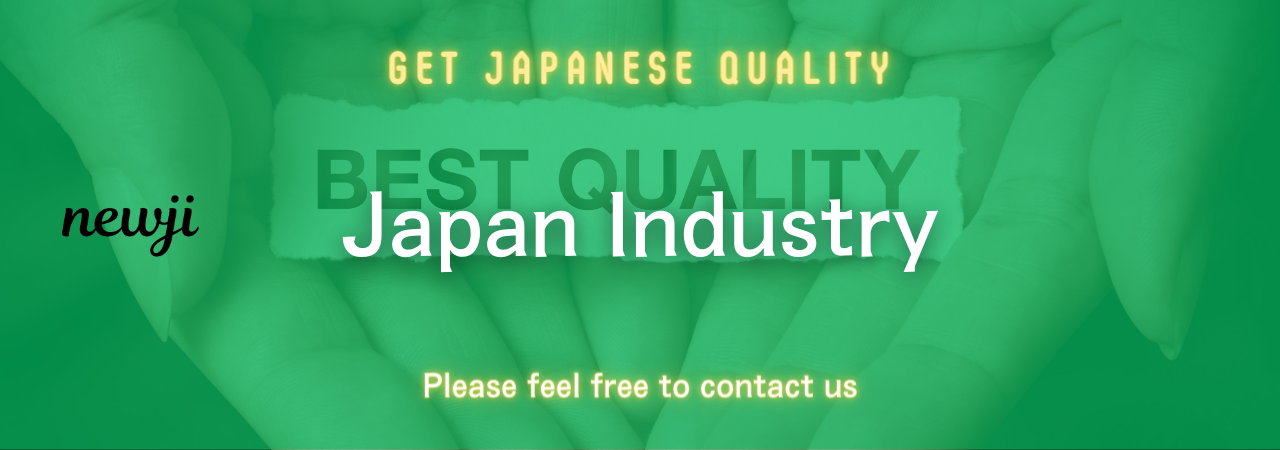
目次
Understanding Vibration Analysis in Auto Parts Manufacturing
Vibration analysis is a crucial aspect of auto parts manufacturing, especially when aiming to improve product durability and reliability.
The automotive industry demands high-performance parts, and understanding how these components behave under real-world conditions is key.
This is where Computer-Aided Engineering (CAE) becomes invaluable.
In the context of auto parts manufacturing, CAE enables engineers to simulate vibration effects and analyze how different variables influence the overall performance of a component.
The Importance of Vibration Analysis
Vibration analysis helps in identifying potential issues that can lead to product failure.
It allows engineers to understand the dynamic behavior of auto parts, and prevents costly production errors by predicting how components will behave under various conditions.
By mastering vibration analysis, you ensure the longevity and reliability of the parts produced, leading to increased customer satisfaction and reduced warranty claims.
Introducing CAE: A Powerful Tool
CAE serves as a comprehensive software tool that models, simulates, and analyzes engineering designs.
In the field of vibration analysis, it helps engineers visualize complex structures and their interactions with external forces.
This powerful tool enables the testing of each component under different stress levels without needing a physical prototype, saving both time and costs.
Steps to Performing Vibration Analysis Using CAE
Mastering the art of vibration analysis using CAE can seem daunting at first.
However, by systematically approaching the task, you can simplify the process and achieve accurate results.
1. Define the Objective
The first step involves clearly defining the objective of your analysis.
Are you investigating a specific vibration-related problem, like noise reduction or improving fatigue resistance?
Identifying a clear goal helps streamline the analysis process and ensures that the necessary data is collected.
2. Gather the Necessary Data
Your next step is to gather all relevant data, which may include material properties, environmental conditions, and operational parameters.
This information forms the backbone of your simulation model and is critical in achieving accurate analysis results.
3. Create the Simulation Model
Using the data you’ve gathered, create a simulation model within your chosen CAE software.
This process involves defining the geometric dimensions, material characteristics, and operating conditions of the part.
Ensure that your model accurately represents the real-world component to gain meaningful insights from your analysis.
4. Run the Simulations
Once your model is complete, the next step is to run simulations.
Ensure that you test the component under various conditions to understand how it behaves under different stress levels.
Modify and refine your model as necessary to reflect any new insights gained during these simulations.
5. Analyze the Results
After running the simulations, analyze the results to identify any potential issues or areas for improvement.
Look for patterns or anomalies in the data that could indicate underlying problems, such as resonant frequencies that might lead to failure.
Use this analysis to make informed decisions on design modifications or material changes.
6. Implement Improvements
Based on your analysis, implement necessary design changes.
CAE allows for iterative testing, which means you can continually refine your design until optimal performance is achieved.
This step is crucial to ensuring the long-term reliability and efficiency of auto parts.
Benefits of Using CAE for Vibration Analysis
Vibration analysis using CAE offers numerous advantages to auto parts manufacturers.
Firstly, it significantly reduces the time and costs associated with physical prototyping.
Instead of building multiple prototypes, engineers can simulate and test designs virtually.
Additionally, CAE provides a comprehensive understanding of a component’s behavior under various conditions, leading to more informed design decisions.
This increased insight helps in fine-tuning products for improved performance, safety, and customer satisfaction.
Moreover, using CAE tools enables engineers to identify potential problems early in the design process, allowing for timely interventions before full-scale production begins.
This proactive approach minimizes production delays and reduces the risk of costly recalls.
Challenges in Implementing CAE
While CAE is highly beneficial, implementing these systems can present challenges.
One significant obstacle is the steep learning curve associated with mastering CAE tools, which requires a solid understanding of both engineering principles and software capabilities.
Additionally, the accuracy of CAE simulations depends heavily on the quality of input data and the assumptions made during the modeling process.
Poor data can lead to incorrect conclusions, undermining the reliability of the analysis.
Finally, integrating CAE into existing workflows demands ongoing collaboration between different departments, posing organizational challenges that require strategic planning to overcome.
Conclusion
For leaders in the design department of auto parts manufacturers, mastering vibration analysis using CAE technologies can revolutionize how products are developed and tested.
By comprehensively simulating real-world conditions, engineers can innovate and improve parts, ultimately delivering high-quality components that stand up to the rigorous demands of the automotive industry.
While the journey may present challenges, the benefits of shorter testing phases and reduced costs make CAE an invaluable investment in the future of auto parts manufacturing.
資料ダウンロード
QCD調達購買管理クラウド「newji」は、調達購買部門で必要なQCD管理全てを備えた、現場特化型兼クラウド型の今世紀最高の購買管理システムとなります。
ユーザー登録
調達購買業務の効率化だけでなく、システムを導入することで、コスト削減や製品・資材のステータス可視化のほか、属人化していた購買情報の共有化による内部不正防止や統制にも役立ちます。
NEWJI DX
製造業に特化したデジタルトランスフォーメーション(DX)の実現を目指す請負開発型のコンサルティングサービスです。AI、iPaaS、および先端の技術を駆使して、製造プロセスの効率化、業務効率化、チームワーク強化、コスト削減、品質向上を実現します。このサービスは、製造業の課題を深く理解し、それに対する最適なデジタルソリューションを提供することで、企業が持続的な成長とイノベーションを達成できるようサポートします。
オンライン講座
製造業、主に購買・調達部門にお勤めの方々に向けた情報を配信しております。
新任の方やベテランの方、管理職を対象とした幅広いコンテンツをご用意しております。
お問い合わせ
コストダウンが利益に直結する術だと理解していても、なかなか前に進めることができない状況。そんな時は、newjiのコストダウン自動化機能で大きく利益貢献しよう!
(Β版非公開)