- お役立ち記事
- “Quality checks” that should be carried out thoroughly at the workplace—the basis for quality maintenance aimed at by management
“Quality checks” that should be carried out thoroughly at the workplace—the basis for quality maintenance aimed at by management
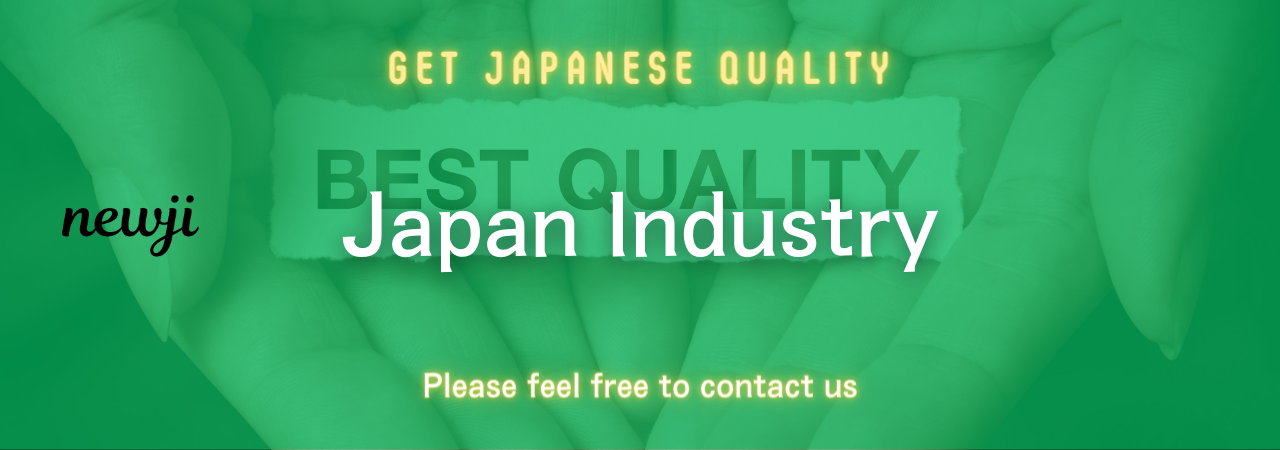
Understanding the Importance of Quality Checks
Quality checks play a crucial role in maintaining the standards of products and services in any workplace.
These checks are not just about meeting compliance requirements; they are central to achieving customer satisfaction and building a trustworthy brand.
When a company consistently delivers quality output, it tends to secure a competitive edge in the market.
Thus, implementing thorough quality checks is a strategic move for management aiming for long-term success.
The Objectives of Quality Checks
The fundamental goal of quality checks is to ensure that the products or services meet the set standards before reaching the customer.
This involves detecting any defects or inconsistencies early in the process, which can save both time and resources.
Moreover, quality checks aim to improve operational efficiency by identifying areas that require improvements.
This proactive approach not only enhances the product but also helps in optimizing the overall production process.
Creating a Comprehensive Quality Check Plan
To implement effective quality checks, it is essential to have a well-structured plan.
The plan should include clear objectives, defined processes, and designated responsibilities.
Firstly, identify critical checkpoints throughout the production or service delivery process.
These are the stages where quality checks will be most beneficial.
Secondly, decide the type of checks necessary—whether they will be manual inspections, automated checks, or a combination of both.
Finally, assign specific roles to qualified personnel who will be responsible for carrying out these checks and reporting their findings.
This could involve routine training and upskilling programs to ensure all personnel are up-to-date with the latest techniques and technologies in quality assurance.
Key Elements of Quality Checks
1. **Standardization:** Establish clear and consistent quality standards that align with the company’s goals.
These standards should be documented and communicated across all departments to ensure everyone is on the same page.
2. **Continuous Monitoring:** Implement systems that allow continuous monitoring of processes.
This can involve real-time data analytics or periodic assessments to track performance and quality.
3. **Feedback Loop:** Encourage feedback from all stakeholders involved in the process—including employees and customers.
This helps in identifying potential issues early and provides a basis for continuous improvement.
4. **Corrective Actions:** Develop a protocol for corrective actions when discrepancies are discovered.
The focus should be on understanding the root cause of the problem and implementing solutions to prevent recurrence.
Technological Integration in Quality Checks
With advancements in technology, companies have more tools at their disposal to conduct thorough quality checks.
Automation can significantly enhance the accuracy and efficiency of these checks.
For example, using sensors and data analytics can provide real-time insights into product quality and process performance.
Additionally, software solutions can streamline the quality assurance process by providing a centralized platform for tracking and reporting.
Incorporating artificial intelligence and machine learning can also help in predictive analysis, allowing companies to foresee potential issues before they escalate.
Training and Involvement of Employees
Employees are an integral part of the quality check process.
Their involvement and understanding of quality standards are essential for successful implementation.
Regular training sessions can keep employees informed about the importance of quality checks and provide them with the skills needed to identify quality issues.
It’s also crucial to cultivate a culture that values quality and encourages employees to take ownership of their tasks.
By empowering staff to contribute to quality assurance, companies can benefit from a collective effort towards maintaining high standards.
The Role of Management in Quality Checks
Management has a pivotal role in the enforcement of quality checks.
Their commitment to maintaining quality standards sets the tone for the entire organization.
By allocating the necessary resources and support, management can ensure that quality checks are carried out effectively.
Moreover, management should establish a system for reviewing the outcomes of quality checks and making strategic decisions based on the findings.
Regular audits and reviews allow for the evaluation of current procedures’ effectiveness and adaptation of new strategies when necessary.
Benefits of Thorough Quality Checks
Implementing thorough quality checks leads to numerous benefits.
It reduces the likelihood of product recalls and defective products reaching the customer, thereby preserving the company’s reputation.
Moreover, quality checks can lead to significant cost savings by identifying wasteful processes and encouraging efficient resource utilization.
Customer satisfaction is one of the most considerable advantages, as consistent quality fosters trust and loyalty.
Satisfied customers are more likely to provide repeat business and recommend a company’s products or services to others.
Conclusion
Quality checks are not just a procedural necessity but a strategic approach towards achieving excellence in any workplace.
Through comprehensive planning, employee involvement, and technological integration, companies can maintain and enhance quality standards.
Management plays a significant role in ensuring these checks are implemented effectively and aligned with the organization’s goals.
By prioritizing quality checks, companies set a firm foundation for growth, competitive advantage, and long-term success.
資料ダウンロード
QCD調達購買管理クラウド「newji」は、調達購買部門で必要なQCD管理全てを備えた、現場特化型兼クラウド型の今世紀最高の購買管理システムとなります。
ユーザー登録
調達購買業務の効率化だけでなく、システムを導入することで、コスト削減や製品・資材のステータス可視化のほか、属人化していた購買情報の共有化による内部不正防止や統制にも役立ちます。
NEWJI DX
製造業に特化したデジタルトランスフォーメーション(DX)の実現を目指す請負開発型のコンサルティングサービスです。AI、iPaaS、および先端の技術を駆使して、製造プロセスの効率化、業務効率化、チームワーク強化、コスト削減、品質向上を実現します。このサービスは、製造業の課題を深く理解し、それに対する最適なデジタルソリューションを提供することで、企業が持続的な成長とイノベーションを達成できるようサポートします。
オンライン講座
製造業、主に購買・調達部門にお勤めの方々に向けた情報を配信しております。
新任の方やベテランの方、管理職を対象とした幅広いコンテンツをご用意しております。
お問い合わせ
コストダウンが利益に直結する術だと理解していても、なかなか前に進めることができない状況。そんな時は、newjiのコストダウン自動化機能で大きく利益貢献しよう!
(Β版非公開)