- お役立ち記事
- For production engineers in the tableware manufacturing industry! Firing temperature control method to ensure quality of porcelain through high-temperature firing
For production engineers in the tableware manufacturing industry! Firing temperature control method to ensure quality of porcelain through high-temperature firing
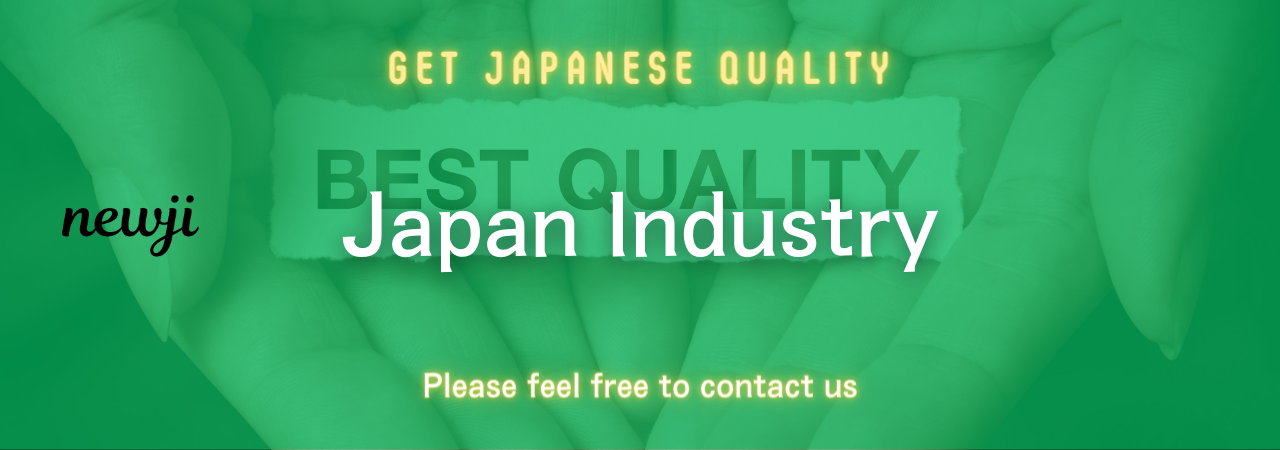
目次
Understanding the Importance of Firing Temperature in Porcelain Manufacturing
In the tableware manufacturing industry, maintaining the quality of porcelain is crucial.
Porcelain, known for its durability and aesthetic appeal, requires precise manufacturing processes.
One of the most critical aspects is controlling the firing temperature.
This process, although seemingly simple, plays a significant role in ensuring the end-quality of porcelain products.
Porcelain must undergo high-temperature firing to achieve its strength and translucency.
Proper firing transforms the raw materials into a solid, glass-like product.
If the temperature is too low, the porcelain may not fully vitrify, resulting in weak and porous tableware.
On the other hand, excessively high temperatures can cause warping or deformation, ruining the product’s shape and look.
The Role of Firing Temperature Control
Firing temperature control is vital for several reasons.
First, it ensures that the materials used are appropriately bonded, providing the necessary hardness and durability to the finished product.
Second, it impacts the appearance, ensuring the color and texture are consistent and appealing.
Inconsistent temperatures can lead to defects in the porcelain, which can be costly for manufacturers.
Therefore, it is essential to maintain precise control over the firing process to minimize waste and maximize quality.
Factors Influencing Firing Temperature
Several factors can influence the firing temperature required for porcelain production.
Firstly, the composition of the raw materials plays a significant role.
Different clays and minerals have unique properties and respond differently to heat.
Therefore, understanding the specific needs of the materials used is pivotal.
Secondly, the kiln’s design and the firing atmosphere are influential factors.
Modern kilns offer precise control over temperature, but older models might require more attention and manual monitoring.
Lastly, the size and thickness of the products can impact the ideal firing temperature.
Thicker pieces may require longer firing times or adjustments in temperature to ensure even heating.
Steps to Ensure Optimal Firing Temperature in Porcelain Production
Ensuring optimal firing temperature begins with selecting appropriate raw materials.
Manufacturers should choose materials with predictable properties for more consistent results.
Pre-production testing helps identify the ideal firing conditions for each batch.
By experimenting with small samples, producers can fine-tune the firing temperature and time, identifying potential issues early on.
During production, maintaining rigorous quality controls is critical.
Monitoring equipment and sensors should be in place to track the temperature inside the kiln.
Continuous data collection and analysis can help identify trends and make necessary adjustments in real-time.
Advanced Technologies for Temperature Control
Technological advancements have greatly enhanced firing temperature control in modern ceramic production.
Automated kilns with computer-controlled systems allow for precise temperature monitoring.
These systems can adjust the heat based on real-time feedback, ensuring more uniform results across all products.
Moreover, the use of infrared thermometers provides a non-contact means to measure surface temperatures accurately during the process.
This technology is particularly useful for identifying hot spots or areas within the kiln that may require adjustment.
Common Challenges and Solutions
Manufacturers often face several challenges when it comes to controlling firing temperature.
One common issue is uneven heating, which can cause problems like cracks or varying colors.
Solutions include ensuring proper airflow within the kiln and using baffles to direct the heat more evenly.
Another challenge is equipment malfunction, which can lead to temperature fluctuations.
Regular maintenance and timely repairs of kilns are essential to avoid unexpected defects.
Furthermore, human error can also play a part in temperature control issues.
Comprehensive training programs for staff can reduce the incidence of errors and ensure that everyone understands the importance of careful monitoring during the firing process.
Benefits of Proper Firing Temperature Control
Maintaining proper firing temperature control provides numerous benefits for porcelain manufacturers.
First and foremost, it leads to a higher quality product, with fewer defects and more consistent finishes.
This results in satisfied customers and a stronger brand reputation.
Additionally, efficient temperature control can improve energy consumption, as kilns operate more effectively when running at optimal conditions.
This not only reduces costs but also minimizes the environmental impact of porcelain production.
Finally, mastering firing temperature control can lead to increased production speeds.
With fewer defective pieces, manufacturers can increase their output without sacrificing quality.
This makes manufacturers more competitive in the marketplace.
Conclusion
For production engineers in the tableware manufacturing industry, understanding and mastering firing temperature control is fundamental.
It ensures that the porcelain produced is of the highest quality, with the desired aesthetic and functional properties.
By leveraging modern technology and rigorous quality controls, manufacturers can overcome common challenges associated with high-temperature firing.
This leads to a product that stands out in the market, satisfying customers and enhancing brand reputation.
Implementing reliable firing temperature control techniques will undoubtedly contribute to the sustained success of porcelain manufacturers.
資料ダウンロード
QCD調達購買管理クラウド「newji」は、調達購買部門で必要なQCD管理全てを備えた、現場特化型兼クラウド型の今世紀最高の購買管理システムとなります。
ユーザー登録
調達購買業務の効率化だけでなく、システムを導入することで、コスト削減や製品・資材のステータス可視化のほか、属人化していた購買情報の共有化による内部不正防止や統制にも役立ちます。
NEWJI DX
製造業に特化したデジタルトランスフォーメーション(DX)の実現を目指す請負開発型のコンサルティングサービスです。AI、iPaaS、および先端の技術を駆使して、製造プロセスの効率化、業務効率化、チームワーク強化、コスト削減、品質向上を実現します。このサービスは、製造業の課題を深く理解し、それに対する最適なデジタルソリューションを提供することで、企業が持続的な成長とイノベーションを達成できるようサポートします。
オンライン講座
製造業、主に購買・調達部門にお勤めの方々に向けた情報を配信しております。
新任の方やベテランの方、管理職を対象とした幅広いコンテンツをご用意しております。
お問い合わせ
コストダウンが利益に直結する術だと理解していても、なかなか前に進めることができない状況。そんな時は、newjiのコストダウン自動化機能で大きく利益貢献しよう!
(Β版非公開)