- お役立ち記事
- For production engineers in the pharmaceutical manufacturing industry! Fundamentals and applications of fine particle manufacturing technology using supercritical fluids
For production engineers in the pharmaceutical manufacturing industry! Fundamentals and applications of fine particle manufacturing technology using supercritical fluids
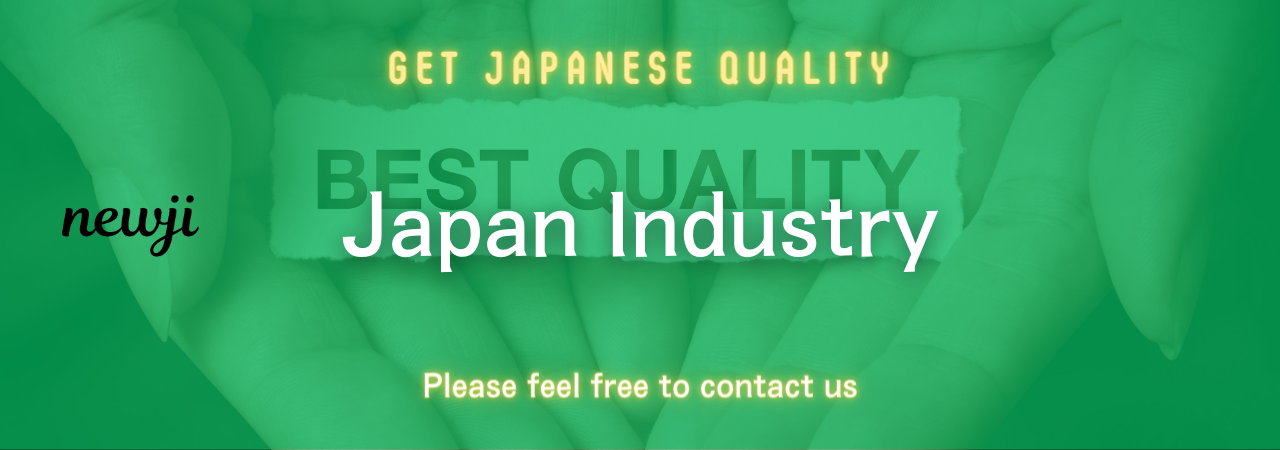
目次
Introduction to Supercritical Fluids in Pharmaceutical Manufacturing
In the pharmaceutical manufacturing industry, the production of fine particles holds great importance.
These particles are crucial for various applications, including drug delivery and formulation.
One innovative method for producing these particles involves the use of supercritical fluids.
Understanding the fundamentals and applications of this technology can provide valuable insights for production engineers in this field.
Supercritical fluids are substances at a temperature and pressure above their critical point, where they exhibit unique properties.
These fluids possess characteristics of both gases and liquids, enabling them to effectively dissolve other substances.
Carbon dioxide is the most commonly used supercritical fluid in the pharmaceutical industry due to its favorable properties and non-toxic nature.
Fundamentals of Supercritical Fluid Technology
Understanding Supercritical Fluids
To grasp the concept of supercritical fluids, it’s important to understand the phase diagram of a substance.
A phase diagram illustrates the different states a substance can exist in, such as solid, liquid, and gas, based on temperature and pressure.
The critical point on this diagram is where the distinction between liquid and gas phases becomes indistinguishable, leading to the formation of a supercritical fluid.
Supercritical fluids offer several advantages in pharmaceutical manufacturing.
They have high density and diffusivity, allowing them to penetrate deeply into solid matrices and dissolve substances that are otherwise difficult to manage.
These properties enable the production of fine particles with uniform size distribution and enhanced purity.
Supercritical Fluid Extraction
Supercritical fluid extraction (SFE) is a key application of supercritical fluids in the pharmaceutical industry.
This technique is widely used for the extraction of bioactive compounds from natural sources.
In SFE, supercritical carbon dioxide is employed to dissolve and extract desired compounds, offering an eco-friendly alternative to traditional solvent extraction methods.
The process of SFE begins by placing the raw material into an extraction vessel.
Supercritical carbon dioxide is then introduced at controlled temperature and pressure conditions, allowing it to penetrate the material and dissolve the target compounds.
The extracted solution is subsequently depressurized, leading to the precipitation of fine particles.
Applications in Pharmaceutical Manufacturing
Particle Formation and Control
Supercritical fluid technology provides precise control over particle formation in pharmaceutical manufacturing.
By manipulating temperature and pressure, production engineers can tailor particle size, shape, and morphology according to specific requirements.
This level of control is particularly advantageous for developing drugs with enhanced bioavailability and targeted delivery systems.
In addition to size control, supercritical fluid technology enables the production of particles with improved solubility.
Many pharmaceutical compounds suffer from poor solubility in aqueous solutions, limiting their effectiveness.
Supercritical fluid processes can enhance the solubility of poorly water-soluble compounds, increasing their bioavailability and efficacy.
Drug Encapsulation and Delivery
Another significant application of supercritical fluid technology in the pharmaceutical industry is drug encapsulation and delivery.
This process involves encapsulating active pharmaceutical ingredients (APIs) within biodegradable polymers or other delivery carriers.
Supercritical fluids facilitate the formation of these carriers by enabling rapid solvent removal and particle formation.
Encapsulating drugs in this manner provides several benefits.
It can protect sensitive APIs from degradation, allow controlled release over time, and improve patient compliance.
Moreover, it enables the development of innovative delivery systems, such as inhalable formulations and sustained-release implants.
Purification and Separation
Supercritical fluids are also employed in purification and separation processes in pharmaceutical manufacturing.
These fluids can efficiently separate impurities, residual solvents, or undesirable by-products from the final product.
This ensures high purity and quality, meeting the stringent standards required for pharmaceutical applications.
Using supercritical fluid chromatography, production engineers can achieve precise separation of complex mixtures.
This technique allows for the isolation and purification of specific compounds, eliminating impurities that may affect the safety or efficacy of the final product.
Advantages and Challenges
Advantages of Supercritical Fluid Technology
The adoption of supercritical fluid technology in pharmaceutical manufacturing offers numerous advantages.
One of the key benefits is the green nature of the process.
Being a solvent-free or low-solvent technique, it significantly reduces the environmental impact and safety concerns associated with traditional solvent extraction methods.
Additionally, supercritical fluid processes are highly efficient and scalable.
The ability to operate at relatively low temperatures preserves the integrity of temperature-sensitive compounds, making it suitable for heat-sensitive APIs.
Moreover, the scalability of these processes allows production engineers to seamlessly transition from small-scale research to large-scale manufacturing.
Challenges and Limitations
Despite the many advantages, some challenges are associated with implementing supercritical fluid technology in pharmaceutical manufacturing.
One common challenge is the high initial investment cost required for setting up the necessary equipment and infrastructure.
However, this cost can be offset over time by the long-term benefits and cost savings achieved through improved efficiency and reduced waste.
Another challenge lies in optimizing process parameters and understanding the behavior of materials under supercritical conditions.
Each system may require specific experimentation to determine optimal temperature, pressure, and concentration for achieving desired results.
Collaboration between researchers and production engineers is crucial for overcoming these challenges and harnessing the full potential of this technology.
Conclusion
Supercritical fluid technology represents an innovative and sustainable approach to fine particle manufacturing in the pharmaceutical industry.
By understanding the fundamentals and applications of this technology, production engineers can optimize processes, improve product quality, and achieve desired outcomes.
The versatility, environmental benefits, and potential for particle size control make supercritical fluid technology a valuable tool in pharmaceutical manufacturing.
While challenges exist, ongoing research and development efforts continue to enhance its applicability and overcome limitations.
With a deeper understanding and exploration of supercritical fluid processes, production engineers can drive advancements and unlock new opportunities in pharmaceutical manufacturing.
資料ダウンロード
QCD調達購買管理クラウド「newji」は、調達購買部門で必要なQCD管理全てを備えた、現場特化型兼クラウド型の今世紀最高の購買管理システムとなります。
ユーザー登録
調達購買業務の効率化だけでなく、システムを導入することで、コスト削減や製品・資材のステータス可視化のほか、属人化していた購買情報の共有化による内部不正防止や統制にも役立ちます。
NEWJI DX
製造業に特化したデジタルトランスフォーメーション(DX)の実現を目指す請負開発型のコンサルティングサービスです。AI、iPaaS、および先端の技術を駆使して、製造プロセスの効率化、業務効率化、チームワーク強化、コスト削減、品質向上を実現します。このサービスは、製造業の課題を深く理解し、それに対する最適なデジタルソリューションを提供することで、企業が持続的な成長とイノベーションを達成できるようサポートします。
オンライン講座
製造業、主に購買・調達部門にお勤めの方々に向けた情報を配信しております。
新任の方やベテランの方、管理職を対象とした幅広いコンテンツをご用意しております。
お問い合わせ
コストダウンが利益に直結する術だと理解していても、なかなか前に進めることができない状況。そんな時は、newjiのコストダウン自動化機能で大きく利益貢献しよう!
(Β版非公開)