- お役立ち記事
- Practice of equipment testing using reliability engineering that new employees in the equipment engineering department should know
Practice of equipment testing using reliability engineering that new employees in the equipment engineering department should know
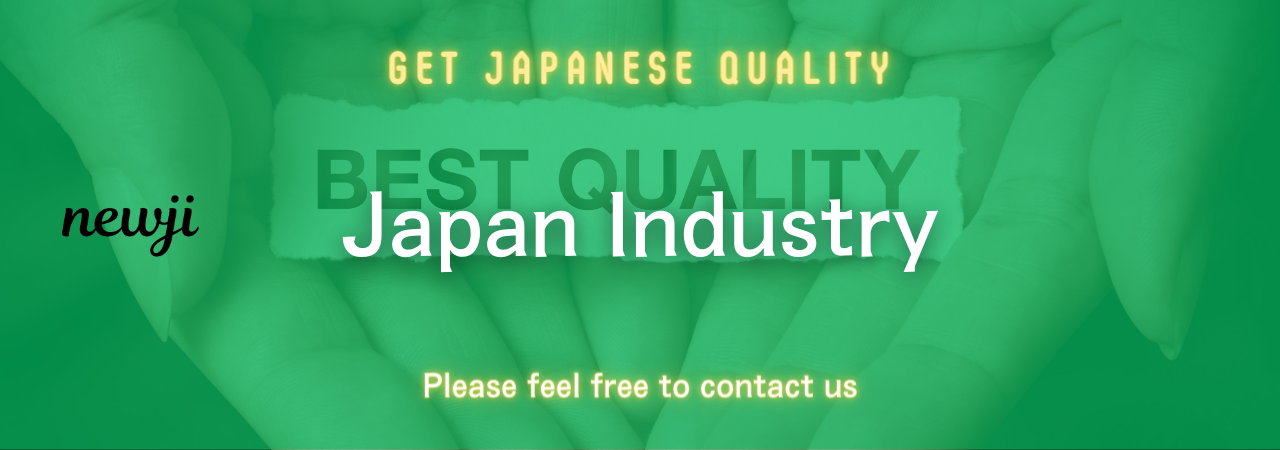
目次
Understanding Reliability Engineering
Reliability engineering is a discipline dedicated to ensuring that equipment and systems perform consistently over time without failures.
For equipment engineers, especially new employees, understanding this concept is crucial for the success of any engineering project.
The goal is to design and maintain systems that meet specific performance standards for the duration of their expected life cycle.
Reliability engineering isn’t just about fixing problems as they arise; it’s about anticipating and minimizing risks before they occur.
The focus is on creating systems that are inherently robust and that can function effectively even in challenging conditions.
By mastering these principles, new engineers can significantly contribute to their teams and projects.
Importance of Equipment Testing
For new employees in the equipment engineering department, equipment testing is a fundamental task that must be approached with great diligence.
Testing helps verify that equipment will perform reliably in real-world conditions.
Without rigorous testing, there’s a risk of deploying equipment that may fail, potentially leading to costly downtime and safety issues.
During testing, engineers simulate various operational scenarios to evaluate how a piece of equipment behaves.
They check for performance thresholds, ensure compliance with technical specifications, and assess safety features.
This detailed evaluation helps uncover any latent issues that need resolving before full-scale deployment.
The Role of Reliability Testing
Reliability testing is a specific type of equipment testing focused on determining how well an equipment performs over time.
It involves subjecting equipment to stress tests that mimic harsh operating conditions.
This procedure helps identify potential weaknesses and areas that might be prone to failure.
Engineers use reliability testing to make necessary adjustments to design or maintenance strategies.
This proactive approach enhances the durability of equipment, reducing the likelihood of unexpected breakdowns once in operation.
For a new employee, understanding the nuances of reliability testing is an essential skill that can help avoid future complications.
Common Methods of Reliability Testing
Several methods are commonly used in reliability testing to ensure equipment meets international standards.
Accelerated Life Testing
Accelerated Life Testing (ALT) is a technique where equipment is subjected to increased stress levels to accelerate failure.
By doing so, engineers can quickly gather data on potential failure modes within a shorter timeframe.
The data obtained helps predict the natural life span of the equipment under normal conditions.
Failure Modes and Effects Analysis
Failure Modes and Effects Analysis (FMEA) is a systematic approach used to identify potential failure points within a system.
It examines each part of the equipment to determine how it might fail and what the consequences would be.
Through FMEA, engineers can prioritize issues based on severity and address them accordingly.
Highly Accelerated Life Tests
Highly Accelerated Life Tests (HALT) aim to discover the limits of equipment performance.
This testing technique exposes the equipment to extreme conditions, far beyond typical operational standards.
It helps engineers understand the absolute limits of equipment capability and build safer, more reliable products.
Data Collection and Analysis
Reliability testing’s success depends heavily on how well data is collected and analyzed.
During the testing phase, vast amounts of data are generated, detailing how the equipment responds to different stresses.
New employees should be proficient with data analysis tools and methodologies to make sense of this information.
Engineers analyze data to identify trends, calculate probability of failure, and make necessary improvements.
By studying failure trends, engineers can predict future behavior and make informed decisions on maintenance schedules or design changes.
This data-driven approach to reliability engineering forms the basis of crafting robust equipment strategies.
Implementing Reliability Engineering in Workplace
New employees can implement reliability engineering principles effectively by taking a structured approach toward testing and analysis.
Start by familiarizing yourself with the specific equipment and its operational requirements.
Understand the manual, technical specifications, and previous testing results if available.
Communicate effectively with colleagues to understand ongoing projects and any recurring issues.
Participation in cross-departmental meetings can provide insights into challenges faced and allow you to contribute fresh perspectives.
Participate in training programs focused on reliability engineering methods.
Continuous learning ensures you stay updated with cutting-edge practices and standards.
This initiative demonstrates a proactive approach and commitment to ensuring high-quality equipment performance.
Conclusion
Reliability engineering is essential for ensuring the optimal performance of equipment, especially in industries where precision and reliability are critical.
For new employees in the equipment engineering department, developing a strong foundation in reliability engineering principles is invaluable.
Through diligent equipment testing, identifying potential failures, and implementing robust solutions, engineers can make significant contributions to the success of their teams.
By adopting a systematic approach to equipment testing and reliability analysis, new engineers can help create more reliable systems, ultimately leading to improved safety, efficiency, and cost savings for their organizations.
資料ダウンロード
QCD調達購買管理クラウド「newji」は、調達購買部門で必要なQCD管理全てを備えた、現場特化型兼クラウド型の今世紀最高の購買管理システムとなります。
ユーザー登録
調達購買業務の効率化だけでなく、システムを導入することで、コスト削減や製品・資材のステータス可視化のほか、属人化していた購買情報の共有化による内部不正防止や統制にも役立ちます。
NEWJI DX
製造業に特化したデジタルトランスフォーメーション(DX)の実現を目指す請負開発型のコンサルティングサービスです。AI、iPaaS、および先端の技術を駆使して、製造プロセスの効率化、業務効率化、チームワーク強化、コスト削減、品質向上を実現します。このサービスは、製造業の課題を深く理解し、それに対する最適なデジタルソリューションを提供することで、企業が持続的な成長とイノベーションを達成できるようサポートします。
オンライン講座
製造業、主に購買・調達部門にお勤めの方々に向けた情報を配信しております。
新任の方やベテランの方、管理職を対象とした幅広いコンテンツをご用意しております。
お問い合わせ
コストダウンが利益に直結する術だと理解していても、なかなか前に進めることができない状況。そんな時は、newjiのコストダウン自動化機能で大きく利益貢献しよう!
(Β版非公開)