- お役立ち記事
- For design leaders in the plastic molding industry! How to minimize molding defects using CAE
For design leaders in the plastic molding industry! How to minimize molding defects using CAE
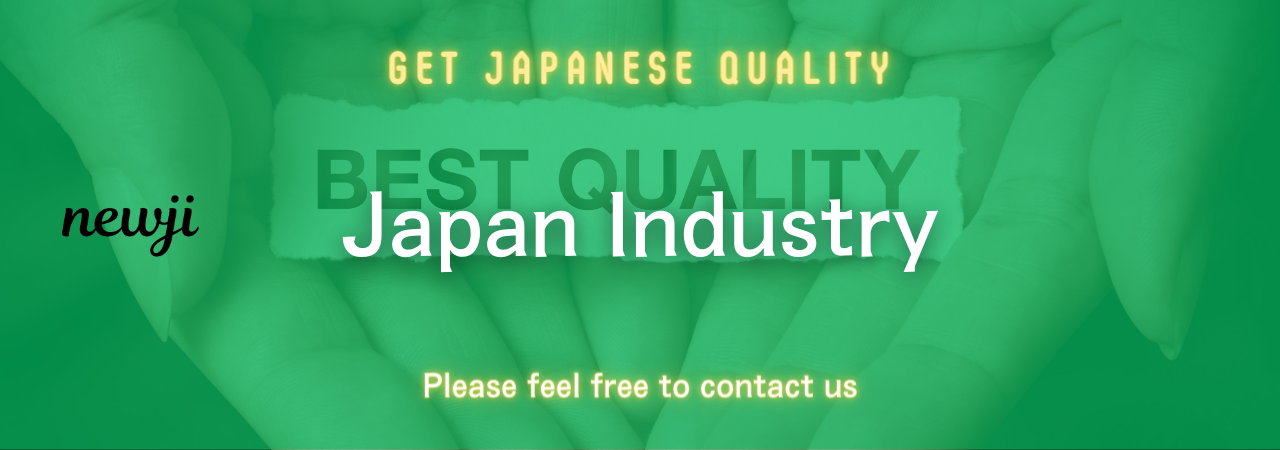
目次
Understanding Plastic Molding Defects
Plastic molding is a crucial process in manufacturing a wide range of products, from simple household items to complex automotive parts.
However, molding defects have long been a challenge within the industry, causing delays, increased costs, and sometimes even compromising the safety or functionality of products.
For design leaders in the plastic molding industry, minimizing these defects is a top priority.
Common defects include warping, sink marks, voids, and burrs, all affecting the quality and appearance of the final product.
These imperfections can result from factors like improper material selection, poor mold design, or issues during the molding process itself.
Addressing these concerns early on is essential for maintaining productivity and customer satisfaction.
The Role of CAE in Reducing Molding Defects
Computer-Aided Engineering (CAE) has revolutionized many aspects of the manufacturing industry, particularly in reducing defects.
CAE tools enable design leaders to simulate and analyze the molding process, predicting potential issues before they become problems in real-world production.
By leveraging CAE, companies can optimize designs, materials, and processes effectively.
Using CAE software, engineers can create virtual models of molds and simulate the injection molding process.
These simulations help identify potential defect types and their causes, allowing for adjustments in the early stages of design.
This proactive approach ensures that by the time the production reaches the molding machine, significant predictive analysis has already been conducted, limiting surprises.
Key Benefits of CAE in Defect Minimization
One of the primary benefits of using CAE in molding is the ability to visualize how materials will behave during the injection process.
With CAE tools, design leaders can anticipate how molten plastic will fill a mold, where it will cool first, and where stresses might occur.
Understanding these dynamics is vital for adjusting the mold design, injection speed, temperature settings, and other parameters that influence quality.
Another advantage is the reduction in physical prototyping costs.
Traditionally, multiple prototypes would have to be produced and tested, a costly and time-consuming process.
CAE allows for virtual prototypes, which means design changes can be tested within hours, not days, drastically shortening development cycles.
Moreover, CAE tools aid in the material selection process by simulating how different polymers behave under various processing conditions.
This allows engineers to choose the best material for specific product requirements, optimizing cost and performance without compromising quality.
Implementing CAE in Molding Design
Implementing CAE in the plastic molding process begins with selecting the appropriate software based on your company’s needs.
Many CAE tools are available, ranging from general-purpose platforms to those specifically tailored for injection molding simulations.
Once a suitable tool is chosen, training is necessary to ensure it is used effectively.
Having a team that understands how to interpret simulation data and make decisions based on that data is crucial.
This understanding allows the team to tweak designs iteratively, leading to the best outcomes in terms of quality and productivity.
Design leaders must also integrate CAE analysis throughout the product life cycle.
Starting with the initial design stage ensures that potential issues are spotted early.
This integration should continue through the testing and production phases, ensuring that each stage benefits from detailed analytics.
Challenges and Solutions
While CAE offers numerous benefits for minimizing molding defects, it is not without challenges.
The initial cost of software and training can be high, especially for small to medium-sized companies.
However, the long-term benefits, such as reduced defect rates and faster time to market, often outweigh these initial investments.
Another challenge is keeping up with the rapid pace of technology advancements.
Software updates and new tool functionalities mean that ongoing education and training are necessary.
This can be addressed through partnerships with software vendors that offer regular training sessions and technical support.
Data interpretation can also be a hurdle, especially when complex simulations produce vast amounts of information.
It’s essential to have skilled professionals who can accurately interpret this data to refine the molding process.
Building a team with a solid foundation in engineering principles and data analysis skills is key.
Future of CAE in the Molding Industry
The future of CAE in the plastic molding industry looks promising, with continuous advancements in technology making simulations even more accurate and detailed.
Artificial Intelligence and machine learning are expected to play significant roles in this evolution, enhancing the ability to predict molding outcomes and optimize processes autonomously.
Moreover, the integration of CAE with other technologies, such as the Internet of Things (IoT) and Industry 4.0 practices, could provide real-time data and further insights into the molding process.
These advancements could lead to smarter, more efficient production environments, where machines self-adjust based on CAE predictions.
Design leaders who embrace these developments will likely maintain a competitive edge, delivering high-quality products at a lower cost and with greater efficiency than their peers.
By focusing on leveraging CAE tools and technology, you can significantly reduce defects in plastic molding processes, ultimately improving product quality and customer satisfaction.
The adoption of CAE is no longer a mere option but a necessity in keeping up with rapidly evolving industry standards and expectations.
資料ダウンロード
QCD調達購買管理クラウド「newji」は、調達購買部門で必要なQCD管理全てを備えた、現場特化型兼クラウド型の今世紀最高の購買管理システムとなります。
ユーザー登録
調達購買業務の効率化だけでなく、システムを導入することで、コスト削減や製品・資材のステータス可視化のほか、属人化していた購買情報の共有化による内部不正防止や統制にも役立ちます。
NEWJI DX
製造業に特化したデジタルトランスフォーメーション(DX)の実現を目指す請負開発型のコンサルティングサービスです。AI、iPaaS、および先端の技術を駆使して、製造プロセスの効率化、業務効率化、チームワーク強化、コスト削減、品質向上を実現します。このサービスは、製造業の課題を深く理解し、それに対する最適なデジタルソリューションを提供することで、企業が持続的な成長とイノベーションを達成できるようサポートします。
オンライン講座
製造業、主に購買・調達部門にお勤めの方々に向けた情報を配信しております。
新任の方やベテランの方、管理職を対象とした幅広いコンテンツをご用意しております。
お問い合わせ
コストダウンが利益に直結する術だと理解していても、なかなか前に進めることができない状況。そんな時は、newjiのコストダウン自動化機能で大きく利益貢献しよう!
(Β版非公開)