- お役立ち記事
- A must-see for process engineers in the pharmaceutical manufacturing industry! How to maintain uniformity of formulations in a fluidized bed dryer
A must-see for process engineers in the pharmaceutical manufacturing industry! How to maintain uniformity of formulations in a fluidized bed dryer
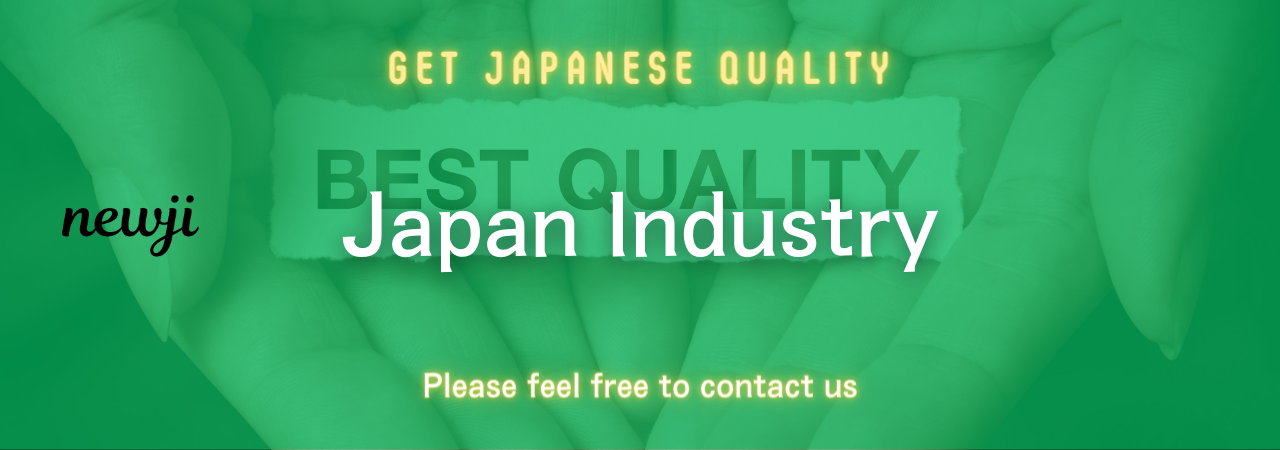
目次
Understanding Fluidized Bed Dryers
In the pharmaceutical manufacturing industry, maintaining uniformity in formulations is a critical task that process engineers often grapple with.
One essential piece of equipment in this domain is the fluidized bed dryer.
This machine plays a pivotal role in drying particulate materials, powder, and granules, all of which are crucial in pharmaceutical formulations.
A fluidized bed dryer operates by suspending solid particles in a gas or air stream, creating a fluid-like state.
This allows for uniform drying, as each particle is exposed to the drying medium equally.
However, achieving and maintaining uniformity in formulations using a fluidized bed dryer is not without challenges.
To ensure consistent quality, understanding the operation and optimization of fluidized bed dryers is key.
Importance of Uniformity in Formulations
Uniformity in pharmaceutical formulations is vital because it ensures that each unit of the product contains the same proportion of components.
This consistency is crucial for the efficacy and safety of the medication.
Patients rely on consistent dosages for their treatments, and any deviation can lead to therapeutic failures or adverse effects.
In addition to patient safety, regulatory compliance is another reason for ensuring uniformity.
Pharmaceutical companies must adhere to strict guidelines and standards set by regulatory bodies such as the FDA.
Uniformity testing is part of the good manufacturing practices (GMP) required for product approval and market release.
Challenges in Maintaining Uniformity
Maintaining uniformity in formulations using a fluidized bed dryer presents several challenges.
The primary issue is the tendency for particle segregation to occur.
Particles of different sizes and densities may separate during drying, leading to non-uniform final products.
Another challenge is the variation in moisture levels within the different areas of the dryer.
Uneven drying can lead to some particles being too dry while others remain damp.
This discrepancy affects the mixing and blending process, where uniformity is crucial.
Key Factors Affecting Uniformity
Several factors can influence the uniformity of formulations in a fluidized bed dryer:
– **Particle Size and Shape**: Uniform particle size and shape ensure consistent fluidization and drying.
– **Airflow and Temperature**: Adequate control of airflow and temperature is crucial for uniform drying conditions.
– **Drying Time**: Sufficient drying time must be allotted to allow for even moisture removal from all particles.
– **Bed Depth**: The thickness of the particle bed affects the level of fluidization and the uniformity of the drying process.
Strategies to Maintain Uniformity
To address these challenges, process engineers can employ several strategies to maintain uniformity in formulations when using a fluidized bed dryer.
Optimize Particle Size Distribution
Controlling the size and shape of particles before entering the fluidized bed dryer is a critical step.
Particles with consistent size and shape will fluidize more uniformly, avoiding segregation and enhancing uniformity in the drying process.
Using milling processes to achieve the desired particle size distribution and sieving out oversized particles can help prevent inconsistencies.
Control of Airflow and Temperature
Precise control of airflow and temperature is essential in maintaining uniform drying conditions throughout the bed.
Establishing consistent and uniform air distribution can help mitigate the risk of uneven drying.
It is also important to ensure that temperature settings are accurate for the specific pharmaceutical formulation being dried.
Too high a temperature can lead to thermal degradation, while too low a temperature could result in insufficient drying.
Adjust Bed Depth and Mixing
Managing the bed depth can improve the uniformity of fluidization and drying.
Shallow beds result in better fluidization and can reduce the risk of particle segregation and uneven drying.
Regular mixing of the bed during drying can further help improve uniformity.
The goal is to maintain consistent exposure of all particles to the drying air.
Utilize Controlled Drying Time
Ensuring that the drying time is adequate for complete moisture removal is another vital control point.
Process engineers must establish the appropriate drying time based on the specific formulation to achieve uniformity.
Testing and validation of drying cycles are recommended to determine the optimal parameters for each batch size and formulation type.
Advanced Technologies and Innovations
The pharmaceutical manufacturing industry is evolving, and advancements in technology have introduced new tools and methodologies to enhance the uniformity of formulations in a fluidized bed dryer.
Process Analytical Technology (PAT)
Incorporating PAT tools into the drying process allows for real-time monitoring and control of critical process parameters.
These technologies provide insights into moisture content, particle size distribution, and drying rate, enabling timely adjustments to maintain uniformity.
Modeling and Simulation
Computational modeling and simulation tools have become valuable resources for process engineers.
These tools enable the prediction of fluidization behavior and the impact of multiple variables on uniformity before large-scale production.
This proactive approach allows for the modeling of different scenarios to optimize process settings and achieve uniform drying conditions.
Conclusion
Maintaining uniformity of formulations in a fluidized bed dryer is a pivotal task for process engineers in the pharmaceutical manufacturing industry.
With a comprehensive understanding of the dryer’s operation and key factors affecting uniformity, engineers can implement strategies to optimize the drying process.
Applying advanced technologies and innovations further enhances the ability to maintain consistent product quality.
By addressing the inherent challenges and employing best practices, pharmaceutical companies can ensure that every batch of medication is safe, effective, and complies with regulatory standards.
資料ダウンロード
QCD調達購買管理クラウド「newji」は、調達購買部門で必要なQCD管理全てを備えた、現場特化型兼クラウド型の今世紀最高の購買管理システムとなります。
ユーザー登録
調達購買業務の効率化だけでなく、システムを導入することで、コスト削減や製品・資材のステータス可視化のほか、属人化していた購買情報の共有化による内部不正防止や統制にも役立ちます。
NEWJI DX
製造業に特化したデジタルトランスフォーメーション(DX)の実現を目指す請負開発型のコンサルティングサービスです。AI、iPaaS、および先端の技術を駆使して、製造プロセスの効率化、業務効率化、チームワーク強化、コスト削減、品質向上を実現します。このサービスは、製造業の課題を深く理解し、それに対する最適なデジタルソリューションを提供することで、企業が持続的な成長とイノベーションを達成できるようサポートします。
オンライン講座
製造業、主に購買・調達部門にお勤めの方々に向けた情報を配信しております。
新任の方やベテランの方、管理職を対象とした幅広いコンテンツをご用意しております。
お問い合わせ
コストダウンが利益に直結する術だと理解していても、なかなか前に進めることができない状況。そんな時は、newjiのコストダウン自動化機能で大きく利益貢献しよう!
(Β版非公開)