- お役立ち記事
- For process engineers in the electronic component manufacturing industry! How to improve joint quality with solder wettability testing
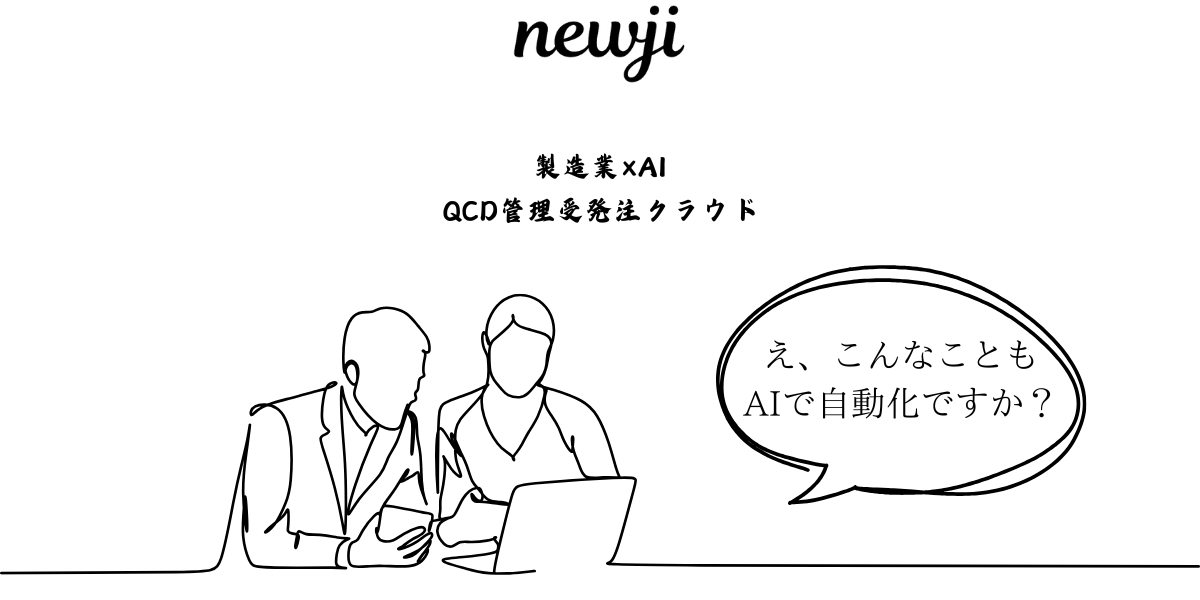
For process engineers in the electronic component manufacturing industry! How to improve joint quality with solder wettability testing
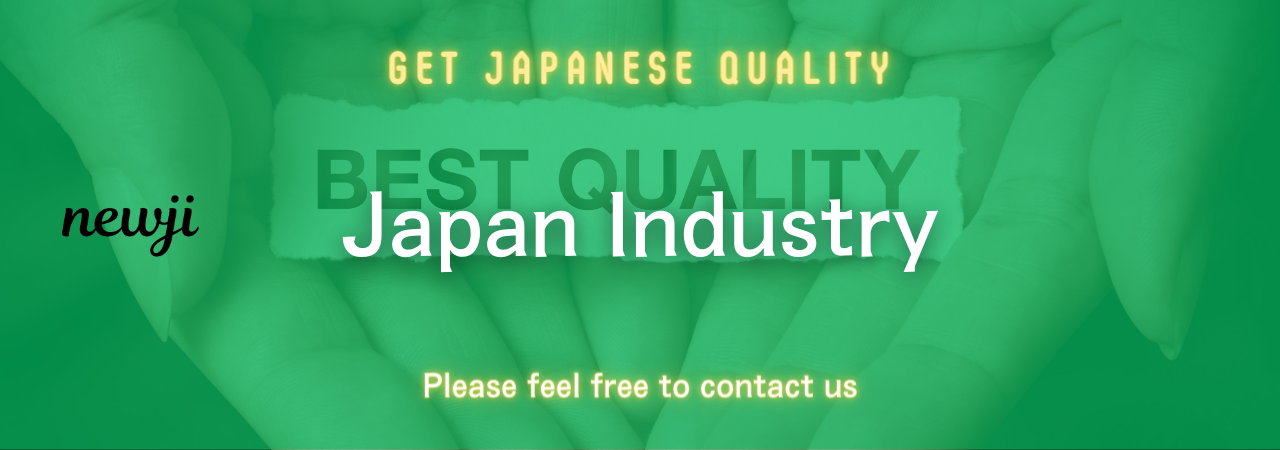
目次
Understanding Solder Wettability
Solder wettability is a critical aspect in the electronic component manufacturing industry.
It refers to the ability of molten solder to spread over a surface, creating a reliable bond between components.
The quality of this bond is essential for ensuring the durability and functionality of electronic devices.
Inadequate solder wettability can lead to weak joints, resulting in malfunctions or failure of electronic components.
Process engineers play a key role in addressing these challenges by implementing effective solder wettability testing procedures.
These tests help identify soldering issues and guide improvements in the manufacturing process.
Importance of Solder Wettability Testing
Testing the wettability of solder is crucial for maintaining high-quality production standards.
By assessing solder wettability, manufacturers can ensure joints are robust and meet industry specifications.
Poor wettability can cause defects like non-wet openings or voids in solder joints, adversely affecting product performance.
For process engineers, effective solder wettability testing leads to reduced rework and scrap rates.
This enhances productivity while minimizing costs associated with defective components.
Consequently, maintaining a consistent testing regimen is vital for achieving long-term production efficiency.
Enhancing Joint Quality Through Testing
Solder wettability testing is instrumental in improving joint quality by identifying potential issues early in the process.
Process engineers can utilize different methods to evaluate solder performance, such as contact angle measurements and wetting balance tests.
Contact angle measurements involve calculating the angle between the solder surface and the substrate.
A smaller contact angle indicates better wettability, translating into stronger joints.
Wetting balance tests measure the force exerted on a component when dipped into molten solder.
These readings help determine how well the solder adheres to and covers the component.
Regular testing and monitoring allow process engineers to make data-driven decisions.
This leads to optimized soldering parameters, ensuring reliable and durable component connections.
Factors Affecting Solder Wettability
Understanding the factors influencing solder wettability is vital for process engineers.
Several elements can affect how well solder adheres to surfaces, including temperature, solder type, and surface cleanliness.
Temperature plays a significant role in solder wettability.
Proper temperature control during soldering ensures the solder melts and flows correctly, allowing it to form strong bonds.
Surface tension decreases with increased temperature, improving wettability.
However, excessive heat can lead to oxidation, which may impede solder flow.
The type of solder also impacts wettability.
Different solder compositions have varying levels of flux, which helps facilitate the wetting process.
Process engineers must select appropriate solder materials based on desired joint characteristics and application needs.
Surface cleanliness is another critical factor.
Contaminants such as oxides or residues inhibit solder flow and bonding.
Implementing effective cleaning protocols ensures surfaces are free from impurities, improving solderability.
Implementing Effective Testing Strategies
Process engineers should employ a systematic approach to solder wettability testing.
Establishing a comprehensive testing strategy involves setting clear objectives, selecting appropriate testing methods, and analyzing results.
First, define the goals of the testing process.
Consider factors like product specifications, industry standards, and performance requirements.
Clear objectives guide the selection of suitable testing methods and facilitate meaningful analysis.
Next, choose the most effective testing techniques.
Evaluate the compatibility of methods such as contact angle measurements and wetting balance tests for your production context.
Consider equipment availability, cost constraints, and training requirements when determining the best approach.
Regularly analyze and interpret test results to identify trends and areas for improvement.
Document findings and implement process adjustments as needed to enhance solder wettability.
Continuous improvement fosters operational efficiency and product quality.
The Role of Advanced Technologies
Incorporating advanced technologies can significantly enhance solder wettability testing.
Innovations such as automated inspection systems and AI-driven analysis provide more accurate and efficient testing processes.
Automated systems improve precision by eliminating human error, ensuring consistent test conditions and reliable data collection.
They enable rapid identification of defects, allowing for timely intervention and process adjustments.
AI-driven analysis offers sophisticated data interpretation, revealing insights beyond conventional analysis methods.
These technologies facilitate predictive maintenance, optimizing soldering processes and reducing downtime.
Process engineers should stay informed about emerging technologies and consider their potential benefits.
Integrating advanced tools supports more effective solder wettability testing and overall production excellence.
Conclusion
Solder wettability testing is a vital process for improving joint quality in the electronic component manufacturing industry.
By understanding the importance and factors affecting solder wettability, process engineers can implement effective testing strategies.
Advanced technologies further enhance testing accuracy and efficiency, contributing to optimized soldering processes.
Through continuous improvement and innovation, process engineers can ensure reliable, high-quality electronic components.
This reinforces the integrity of devices and supports the industry’s advancement.
資料ダウンロード
QCD調達購買管理クラウド「newji」は、調達購買部門で必要なQCD管理全てを備えた、現場特化型兼クラウド型の今世紀最高の購買管理システムとなります。
ユーザー登録
調達購買業務の効率化だけでなく、システムを導入することで、コスト削減や製品・資材のステータス可視化のほか、属人化していた購買情報の共有化による内部不正防止や統制にも役立ちます。
NEWJI DX
製造業に特化したデジタルトランスフォーメーション(DX)の実現を目指す請負開発型のコンサルティングサービスです。AI、iPaaS、および先端の技術を駆使して、製造プロセスの効率化、業務効率化、チームワーク強化、コスト削減、品質向上を実現します。このサービスは、製造業の課題を深く理解し、それに対する最適なデジタルソリューションを提供することで、企業が持続的な成長とイノベーションを達成できるようサポートします。
オンライン講座
製造業、主に購買・調達部門にお勤めの方々に向けた情報を配信しております。
新任の方やベテランの方、管理職を対象とした幅広いコンテンツをご用意しております。
お問い合わせ
コストダウンが利益に直結する術だと理解していても、なかなか前に進めることができない状況。そんな時は、newjiのコストダウン自動化機能で大きく利益貢献しよう!
(Β版非公開)