- お役立ち記事
- Checklist for evaluating a supplier’s quality assurance system Practical actions for purchasing departments
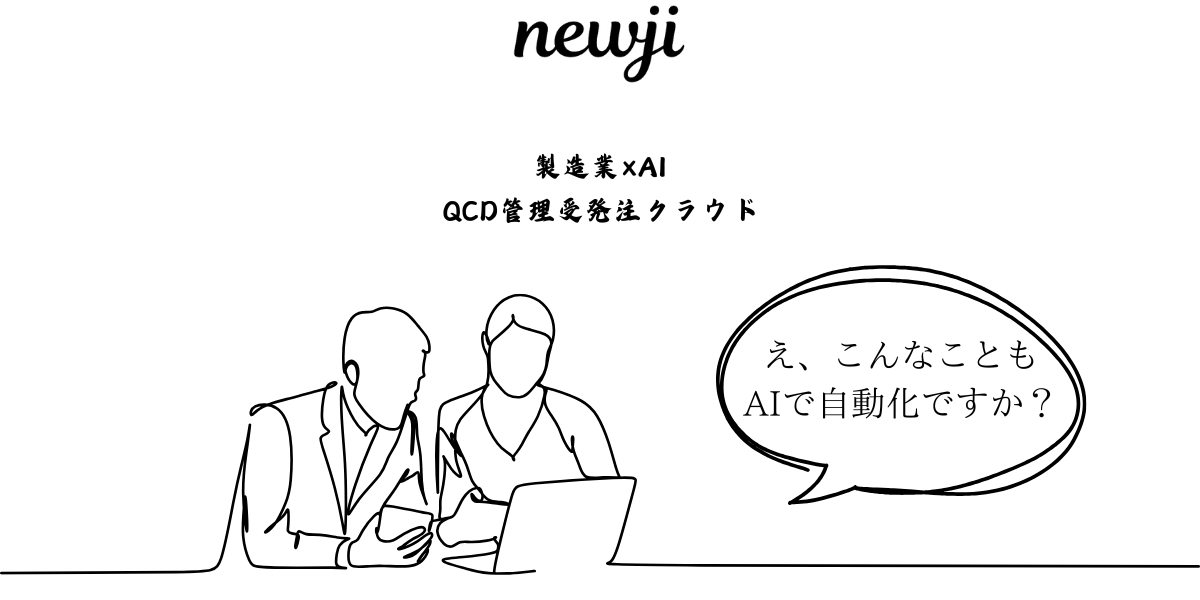
Checklist for evaluating a supplier’s quality assurance system Practical actions for purchasing departments
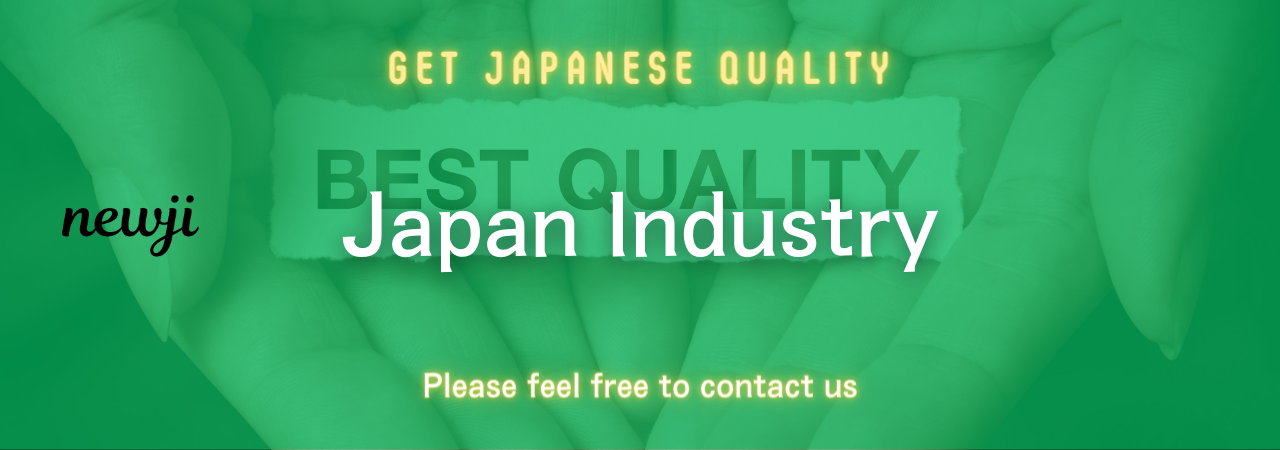
目次
Understanding the Importance of Supplier Quality Assurance
For any organization that relies on external vendors, the quality assurance system of their suppliers is crucial.
A robust supplier quality assurance system ensures that products and services meet predefined standards, reducing the risk of defects and enhancing customer satisfaction.
For purchasing departments, evaluating a supplier’s quality assurance system is of paramount importance to ensure seamless operations.
When a purchasing department selects suppliers, it takes on the responsibility to ensure that the chosen partners adhere to industry standards and regulations.
A thorough evaluation helps in establishing long-term relationships while minimizing risks associated with quality issues.
The Role of a Purchasing Department
The purchasing department serves as a gatekeeper in any organization.
Their task is to procure high-quality materials and services at cost-effective prices.
To achieve this, they must thoroughly assess each supplier’s quality assurance processes.
This assessment includes examining the supplier’s track record, certifications, quality control measures, and approach to problem-solving.
A detailed checklist for evaluating a supplier’s quality assurance system can significantly enhance the purchasing process.
Creating an Evaluation Checklist
Before diving into the evaluation process, it is critical to establish a comprehensive checklist.
This checklist will guide the purchasing department in assessing the effectiveness and reliability of the supplier’s quality assurance system.
The following sections outline practical actions to build such a checklist.
1. Compliance with Industry Standards
One of the first steps is to ensure that the supplier complies with industry standards and regulations.
Look for certifications such as ISO 9001, which indicate that the supplier adheres to recognized quality management systems.
This compliance ensures that the supplier follows systematic procedures for maintaining quality.
2. Quality Control Processes
Thoroughly evaluate the supplier’s quality control processes.
Investigate how they test and inspect their products.
Are there checks at every stage of production?
Ask for detailed documentation of their quality control methods and any corrective actions they’ve implemented in the past.
This documentation reflects the supplier’s commitment to maintaining high standards.
3. Supplier’s Track Record
Investigate the supplier’s history with past clients.
Gather information about any quality issues they may have encountered and how they were resolved.
A supplier with a strong track record of timely deliveries and resolutions to past problems is likely to be more reliable.
4. Continuous Improvement Initiatives
Suppliers who engage in continuous improvement efforts show a dedication to enhancing their processes.
Inquire about any initiatives they have undertaken to improve quality, reduce waste, or increase efficiency.
Continuous improvement is a hallmark of a proactive and responsible supplier.
5. Communication and Transparency
Effective communication between the supplier and your organization is crucial.
Evaluate how transparent the supplier is when discussing their processes, potential issues, and delivery status.
Transparent suppliers will keep you informed and involve you in problem-solving processes, rather than concealing issues.
6. Customer Feedback and Reviews
Seek feedback from other customers who have worked with the supplier.
Reviews and testimonials can provide real-world insights into their performance and quality standards.
This feedback is invaluable in making an informed decision.
Implementing the Evaluation Process
With a well-defined checklist in place, the purchasing department is better equipped to evaluate potential suppliers.
However, implementing this evaluation requires a systematic approach.
Initial Screening
Begin with an initial screening process to shortlist potential suppliers.
Use the checklist to filter out suppliers who do not meet basic quality standards.
Site Visits and Audits
Where possible, conduct site visits or audits of supplier facilities.
Observing the supplier’s processes firsthand gives a clearer picture of their quality assurance practices.
Assess the cleanliness, organization, and efficiency of their operations during these visits.
Supplier Assessment Meetings
Schedule formal meetings with suppliers to discuss their quality assurance systems in detail.
Use these meetings to go through your checklist point by point and address any queries you may have.
These interactions can also help gauge the supplier’s willingness to work towards mutual goals.
Continuous Monitoring
Even after selecting a supplier, continuous monitoring is essential to ensure ongoing compliance with quality standards.
Regular updates and assessments should be part of the supplier relationship management strategy.
This monitoring ensures that quality standards are consistently met.
Conclusion
A supplier’s quality assurance system can make or break the success of a purchasing department’s objectives.
By establishing a thorough checklist and implementing a structured evaluation process, purchasing departments can significantly reduce risk and enhance their supply chain’s efficiency.
Selecting the right supplier involves time and effort, but the benefits far outweigh the challenges.
In the long run, robust supplier evaluation leads to improved product quality, enhanced customer satisfaction, and strengthened supplier relationships.
Always remember that investing in the right suppliers is investing in the future success of your organization.
資料ダウンロード
QCD調達購買管理クラウド「newji」は、調達購買部門で必要なQCD管理全てを備えた、現場特化型兼クラウド型の今世紀最高の購買管理システムとなります。
ユーザー登録
調達購買業務の効率化だけでなく、システムを導入することで、コスト削減や製品・資材のステータス可視化のほか、属人化していた購買情報の共有化による内部不正防止や統制にも役立ちます。
NEWJI DX
製造業に特化したデジタルトランスフォーメーション(DX)の実現を目指す請負開発型のコンサルティングサービスです。AI、iPaaS、および先端の技術を駆使して、製造プロセスの効率化、業務効率化、チームワーク強化、コスト削減、品質向上を実現します。このサービスは、製造業の課題を深く理解し、それに対する最適なデジタルソリューションを提供することで、企業が持続的な成長とイノベーションを達成できるようサポートします。
オンライン講座
製造業、主に購買・調達部門にお勤めの方々に向けた情報を配信しております。
新任の方やベテランの方、管理職を対象とした幅広いコンテンツをご用意しております。
お問い合わせ
コストダウンが利益に直結する術だと理解していても、なかなか前に進めることができない状況。そんな時は、newjiのコストダウン自動化機能で大きく利益貢献しよう!
(Β版非公開)