- お役立ち記事
- For production engineers in the agitator manufacturing industry for concrete mixers! Design methods to increase wear resistance and mixing efficiency
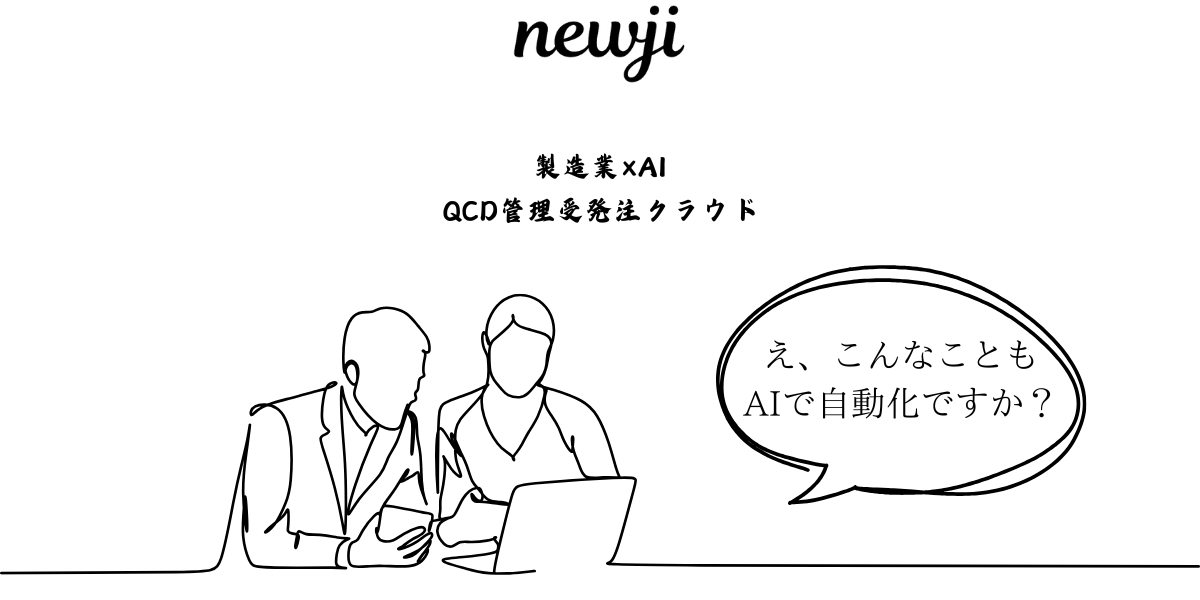
For production engineers in the agitator manufacturing industry for concrete mixers! Design methods to increase wear resistance and mixing efficiency
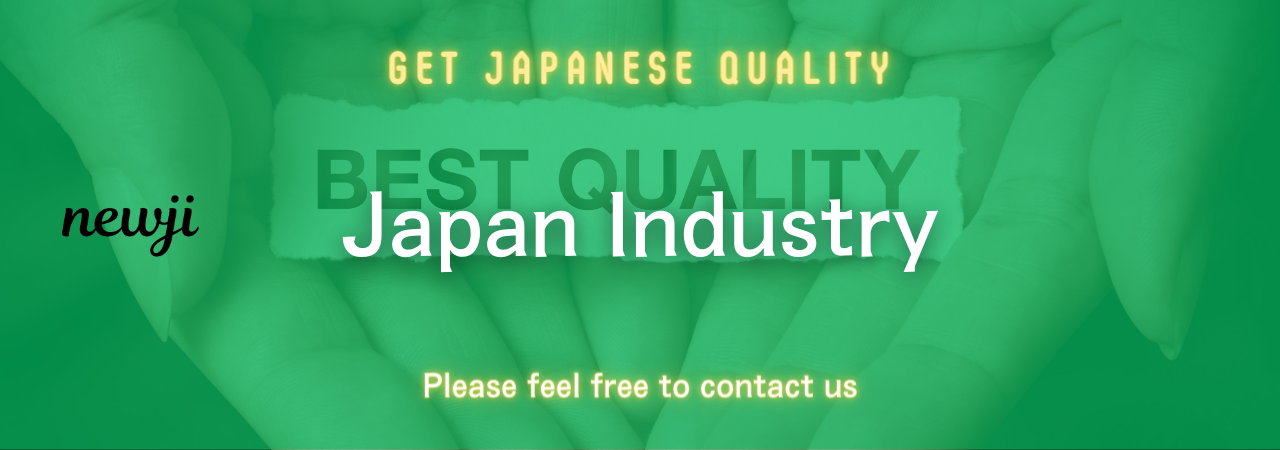
目次
Understanding the Basics of Concrete Mixer Design
Concrete mixers are essential tools in the construction industry.
These machines ensure that concrete is mixed thoroughly, creating a consistent, durable material suitable for a wide variety of applications.
The agitator within a concrete mixer is a crucial component that influences the quality of the mix.
For production engineers in the agitator manufacturing industry, enhancing the wear resistance and mixing efficiency of these vital parts is a top priority.
To achieve these improvements, a deep understanding of the materials and mechanics involved in the manufacturing process is necessary.
This includes selecting the right materials, designing robust structures, and utilizing advanced technologies for improved performance.
Let’s explore these areas in depth.
Material Selection for Wear Resistance
Choosing the right material for the agitator is paramount when focusing on wear resistance.
The materials used must withstand the abrasive nature of concrete, including its sand, gravel, and aggregate components.
High-hardness steels and alloy cast irons are popular choices due to their durability and ability to resist wear.
Additionally, applying wear-resistant coatings can enhance longevity.
Techniques such as carbide coating or polyurethane can create a protective layer on the agitator’s surface, reducing degradation.
When selecting materials, production engineers must balance wear resistance with cost-effectiveness to meet both performance and budgetary requirements.
Innovative Design Techniques for Mixing Efficiency
Designing an agitator with improved mixing efficiency involves considering the geometry and operational dynamics of the mixer.
Optimizing the paddle configuration within the drum is crucial.
A spiral or helix configuration can ensure more consistent and faster mixing by promoting three-dimensional flow patterns.
Utilizing baffles can also aid in preventing materials from stagnating at the bottom of the mixer and improve the overall mixing action.
Understanding the rotational speed and its effect on the mix quality is vital.
Too slow and the mix will not be homogenous; too fast and you may introduce air bubbles, compromising the concrete’s integrity.
A variable speed drive can offer flexibility in fine-tuning the mixing process according to specific requirements.
Advanced Technologies in Agitator Design
Innovations such as computational fluid dynamics (CFD) simulations can significantly aid in designing more efficient agitators.
CFD allows engineers to simulate mixing processes and predict the performance of different designs before physical prototypes are created.
This can reduce the time and cost of development while enhancing the understanding of fluid dynamics within the mixer.
Integration of smart technologies and sensors can provide real-time data on the mixing process.
This data-driven approach enables engineers to make immediate adjustments and continuously optimize the mixer’s performance.
Monitoring factors such as vibration, torque, and temperature can provide insights into potential wear and efficiency issues.
Strategies to Extend Agitator Lifespan
In addition to selecting durable materials and innovative design techniques, engineers should consider preventative maintenance strategies.
Regular inspection and maintenance schedules can identify early signs of wear and address issues before they lead to significant problems.
Training for operators on best practices can ensure that agitators are used correctly and not subject to undue stress.
Implementing a lubrication system can reduce friction, further extending the agitator’s operational life.
Additionally, ensuring that the mixer is not overloaded and is used within its capacity limits can prevent premature wear and tear.
Cost-Effective Solutions
While high-performance materials and complex designs can lead to better outcomes, they often come with higher costs.
Balancing performance with budget constraints is a challenge production engineers regularly face.
To achieve cost-effectiveness, they can explore alternative materials that provide a reasonable level of wear resistance at a lower cost or negotiate with suppliers for bulk discounts.
Simplifying the design without sacrificing quality can also contribute to cost savings.
Collaborating with other departments, such as procurement and finance, can ensure that cost considerations are aligned with performance goals.
Conclusion: The Path Forward
For production engineers in the agitator manufacturing industry, improving wear resistance and mixing efficiency is key to creating reliable and durable concrete mixers.
By carefully selecting materials, embracing innovative design techniques, utilizing advanced technologies, and implementing effective maintenance strategies, they can achieve these goals.
As the industry evolves, staying informed of the latest advancements and maintaining a commitment to continuous improvement will ensure that these essential machines continue to meet the demands of modern construction projects.
Ultimately, the pursuit of excellence in agitator design not only enhances performance but also contributes to the safety and quality of construction worldwide.
資料ダウンロード
QCD調達購買管理クラウド「newji」は、調達購買部門で必要なQCD管理全てを備えた、現場特化型兼クラウド型の今世紀最高の購買管理システムとなります。
ユーザー登録
調達購買業務の効率化だけでなく、システムを導入することで、コスト削減や製品・資材のステータス可視化のほか、属人化していた購買情報の共有化による内部不正防止や統制にも役立ちます。
NEWJI DX
製造業に特化したデジタルトランスフォーメーション(DX)の実現を目指す請負開発型のコンサルティングサービスです。AI、iPaaS、および先端の技術を駆使して、製造プロセスの効率化、業務効率化、チームワーク強化、コスト削減、品質向上を実現します。このサービスは、製造業の課題を深く理解し、それに対する最適なデジタルソリューションを提供することで、企業が持続的な成長とイノベーションを達成できるようサポートします。
オンライン講座
製造業、主に購買・調達部門にお勤めの方々に向けた情報を配信しております。
新任の方やベテランの方、管理職を対象とした幅広いコンテンツをご用意しております。
お問い合わせ
コストダウンが利益に直結する術だと理解していても、なかなか前に進めることができない状況。そんな時は、newjiのコストダウン自動化機能で大きく利益貢献しよう!
(Β版非公開)