- お役立ち記事
- Imported goods inventory management in response to demand fluctuations Management points that the purchasing department should keep in mind
Imported goods inventory management in response to demand fluctuations Management points that the purchasing department should keep in mind
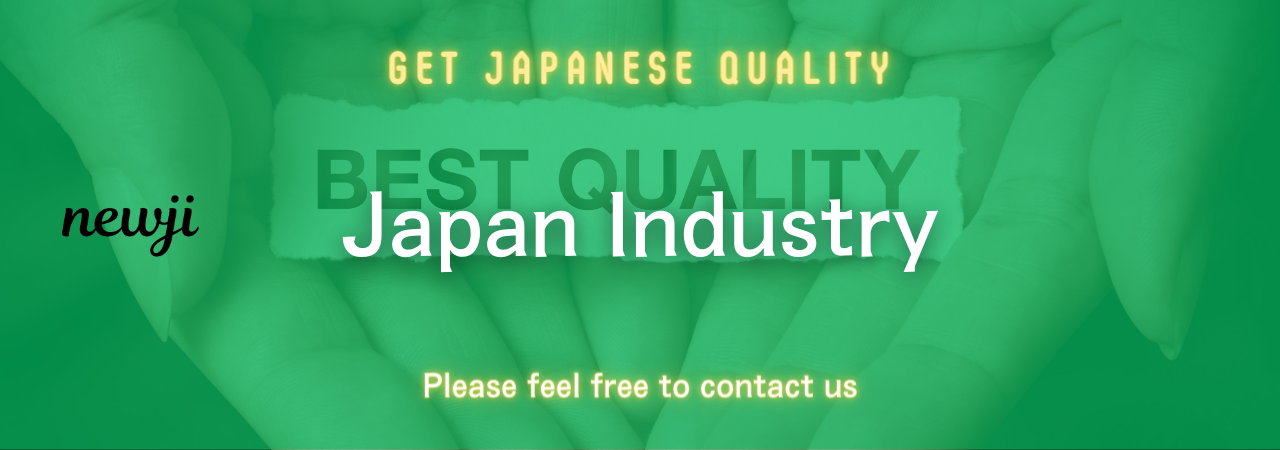
目次
Understanding Demand Fluctuations
Managing imported goods inventory can be a delicate balancing act, primarily due to the frequent demand fluctuations in the market.
It is crucial for purchasing departments to understand these variances to maintain an optimal inventory level, avoiding both deficits and surpluses.
Demand fluctuations can occur due to various reasons such as seasonality, economic changes, consumer trends, or even unforeseen events like natural disasters.
To cope with these changes, businesses need a robust strategy that not only monitors demand but also predicts and responds effectively.
The Impact on Inventory Management
Demand fluctuations significantly impact inventory management practices.
If the demand is underestimated, it can lead to shortages, affecting customer satisfaction and business revenue.
Conversely, overestimating demand can result in overstock, tying up capital and increasing storage costs.
Hence, accurate forecasting and effective inventory practices are essential to balance between these two extremes.
It is through understanding the dynamics of demand fluctuation that purchasing departments can devise strategies to optimize the management of imported goods.
Strategic Inventory Planning
Strategic inventory planning involves setting an inventory management approach that aligns with current and projected demand.
Utilizing data analytics and forecasting tools can provide valuable insights into demand patterns.
This allows businesses to anticipate changes, plan purchases accordingly, and adjust reorder levels.
Additionally, adopting flexible supply chain practices, such as vendor-managed inventory or just-in-time inventory systems, can help in responding swiftly to demand changes.
These systems facilitate direct communication between suppliers and retailers, reducing lead times and minimizing excess stock.
Leveraging Technology for Predictive Analysis
In the era of digital transformation, leveraging technology for predictive analysis can significantly enhance inventory management.
Machine learning algorithms and artificial intelligence tools can help in identifying demand patterns and providing forecasts with higher accuracy.
These technologies analyze historical sales data, market trends, and other economic indicators to predict future demand.
With this information, purchasing departments can make informed decisions on procurement volumes, avoiding both overstock and stockouts.
Furthermore, integrating these technological solutions with inventory management systems can automate the forecasting process, ensuring real-time adjustments to inventory levels.
Enhancing Supplier Relationships
Maintaining strong relationships with suppliers is critical in managing imported goods inventory.
A reliable supplier network can provide the flexibility needed to navigate demand fluctuations.
When demand spikes, suppliers who understand your business needs can expedite deliveries.
Alternatively, they can hold stock during periods of decreased demand to avoid unnecessary inventory buildup.
Open communication and regular collaboration with suppliers create a resilient supply chain that is responsive to changes in demand.
Establishing strategic partnerships and sharing demand forecasts with suppliers can lead to a more synchronized and efficient supply chain management.
Implementing a Buffer Stock Strategy
A buffer stock strategy is a valuable tool in managing inventory levels during demand fluctuations.
This involves maintaining a safety stock — an extra quantity of goods kept on hand to mitigate the risk of stockouts.
The buffer stock provides a cushion against sudden increases in demand.
However, the key is determining the appropriate level of safety stock, as excessive buffer stock can lead to increased holding costs.
Using historical data, purchasing departments can calculate the right amount of buffer stock required in varying demand scenarios.
By doing so, businesses can ensure product availability without incurring unnecessary costs.
Adopting an Agile Supply Chain
An agile supply chain is responsive, flexible, and can adapt quickly to changes in the market.
This approach focuses on reducing lead times, increasing delivery speed, and improving inventory visibility.
To develop an agile supply chain, businesses should consider diversifying their supplier base, which reduces dependence on a single source and increases adaptability to changes.
Additionally, implementing real-time tracking systems provides better inventory visibility, facilitating quick decisions based on current demand and supply levels.
The Role of Inventory Audits
Regular inventory audits play an essential part in efficient inventory management.
Conducting periodic audits helps in identifying discrepancies, understanding product turnover rates, and ensuring the accuracy of inventory records.
These audits provide valuable insights into which products overstay in the warehouse and which ones move faster, enabling better demand forecasting and inventory planning.
By routinely assessing inventory performance, purchasing departments can optimize stock levels, enhancing efficiency and reducing wastage in the supply chain.
Conclusion
Managing imported goods inventory amidst demand fluctuations demands a proactive and strategic approach.
By leveraging technology, enhancing supplier relationships, and adopting agile supply chain practices, purchasing departments can navigate the challenges posed by demand fluctuations effectively.
Optimal inventory management not only supports business growth but also ensures customer satisfaction and operational efficiency.
In an ever-changing market, these strategies serve as a foundation for businesses aiming to maintain a competitive edge and achieve long-term sustainability.
資料ダウンロード
QCD調達購買管理クラウド「newji」は、調達購買部門で必要なQCD管理全てを備えた、現場特化型兼クラウド型の今世紀最高の購買管理システムとなります。
ユーザー登録
調達購買業務の効率化だけでなく、システムを導入することで、コスト削減や製品・資材のステータス可視化のほか、属人化していた購買情報の共有化による内部不正防止や統制にも役立ちます。
NEWJI DX
製造業に特化したデジタルトランスフォーメーション(DX)の実現を目指す請負開発型のコンサルティングサービスです。AI、iPaaS、および先端の技術を駆使して、製造プロセスの効率化、業務効率化、チームワーク強化、コスト削減、品質向上を実現します。このサービスは、製造業の課題を深く理解し、それに対する最適なデジタルソリューションを提供することで、企業が持続的な成長とイノベーションを達成できるようサポートします。
オンライン講座
製造業、主に購買・調達部門にお勤めの方々に向けた情報を配信しております。
新任の方やベテランの方、管理職を対象とした幅広いコンテンツをご用意しております。
お問い合わせ
コストダウンが利益に直結する術だと理解していても、なかなか前に進めることができない状況。そんな時は、newjiのコストダウン自動化機能で大きく利益貢献しよう!
(Β版非公開)