- お役立ち記事
- For new leaders in equipment maintenance departments in the steel industry! Method for early detection of abnormalities through gearbox lubricant oil diagnosis
For new leaders in equipment maintenance departments in the steel industry! Method for early detection of abnormalities through gearbox lubricant oil diagnosis
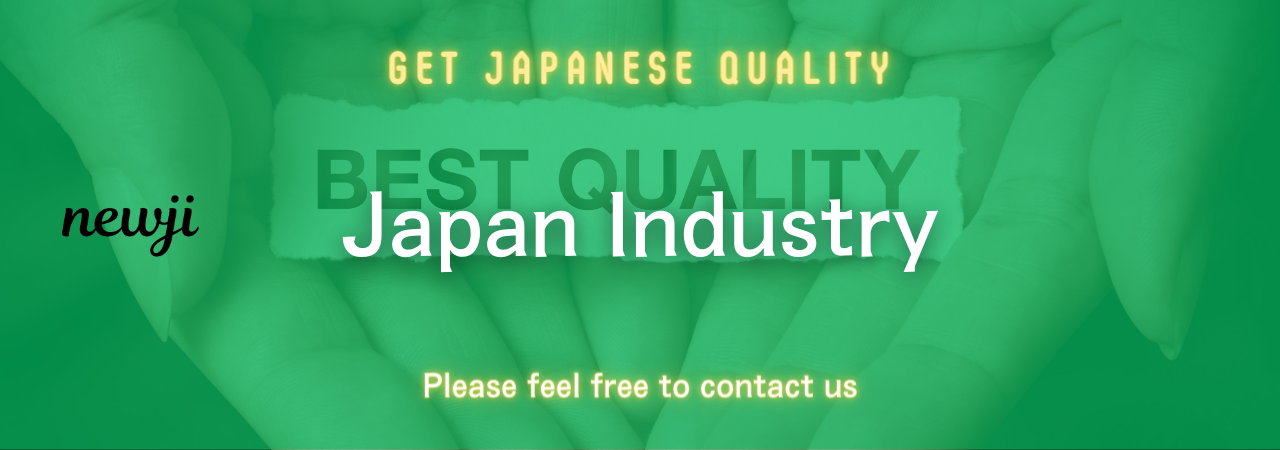
目次
Introduction to Equipment Maintenance in the Steel Industry
In the steel industry, equipment maintenance plays a critical role in ensuring smooth operations and minimizing downtime.
Among various components, gearboxes are vital as they transfer power, affecting the efficiency and longevity of machines.
For new leaders in the maintenance department, understanding the intricacies of gearbox maintenance can be a daunting task.
One of the most effective methods for ensuring the good health of gearboxes is through lubricant oil diagnosis.
By regularly analyzing the lubricant oil, potential abnormalities can be detected early, preventing significant issues and costly repairs.
The Importance of Gearbox Lubricant Oil Diagnosis
Lubricant oil serves as the lifeblood of a gearbox, reducing friction and wear between moving parts.
Over time, however, the lubricant can become contaminated or degrade, leading to increased friction, heat, and wear.
This can have severe consequences for the gearbox and the machinery it operates within.
By performing regular oil analysis, maintenance teams can spot signs of wear and tear, such as the presence of metal particles, water, or other contaminants.
Early detection means problems can be addressed before they escalate, ensuring machines run efficiently with fewer unscheduled downtimes.
How Lubricant Oil Analysis Works
Oil analysis involves several tests to evaluate the condition of the lubricant and the health of the gearbox.
A sample of the oil is taken from the gearbox and sent to a laboratory for examination.
These tests often include viscosity analysis, particle count, and chemical analysis among others.
Viscosity analysis checks if the oil maintains its necessary thickness across varying temperatures, which is crucial for adequate lubrication.
Particle count measures the number and size of particles within the oil, indicating wear or contamination.
Chemical analysis can detect oxidation or presence of unwanted elements in the oil.
Each of these tests provides insights into different aspects of gearbox health.
Benefits of Regular Oil Diagnosis
Regular oil diagnosis offers numerous benefits for maintenance teams in the steel industry.
One of the key advantages is the ability to prevent equipment failures before they occur, reducing unexpected downtimes and costly repairs.
This proactive approach can significantly extend the life of the machinery, maximizing the return on investment for expensive equipment.
Moreover, well-maintained gearboxes contribute to energy efficiency, as machines operate smoother and require less energy to function.
This can lead to substantial savings in energy costs over time.
Additionally, by understanding the typical wear patterns and issues, maintenance teams can enhance their trouble-shooting skills, making them more effective at solving problems when they arise.
Implementing an Oil Analysis Program
For new leaders, establishing a successful oil analysis program involves a series of strategic steps.
Firstly, it’s crucial to select a suitable laboratory that offers comprehensive testing services and provides accurate and timely results.
Partnering with accredited laboratories ensures the reliability of the diagnosis process.
Next, maintenance schedules should be created, detailing how often oil samples should be taken based on the operational intensity of the equipment.
Regular sampling intervals ensure consistent data collection, allowing for trend analysis and early detection of potential issues.
Training maintenance personnel is also essential for a successful program.
They must be familiar with sampling techniques and understand how to interpret analysis reports.
This understanding enables them to make informed decisions about maintenance actions.
Challenges of Oil Diagnosis and How to Overcome Them
While oil analysis is highly beneficial, there are challenges that new leaders might face when implementing this in their departments.
One such challenge is the potential lack of immediate, visible returns, which can make it difficult to justify the costs associated with the analysis program.
It’s important to communicate the long-term benefits and potential cost savings to upper management to gain full support.
Constraints in manpower and time can also pose difficulties.
Automating parts of the data collection and analysis process can alleviate some of these pressures.
Additionally, finding the right expertise either through hiring or training existing staff can be key to effectively managing the program.
Conclusion
In conclusion, gearboxes are integral components within the steel industry, and their maintenance is paramount.
For new leaders in equipment maintenance departments, understanding and implementing lubricant oil diagnosis can be a game-changer.
Through regular oil analysis, abnormalities can be detected early, preventing costly failures and enhancing machine performance.
A successful oil analysis program requires the right tools, strategic planning, and skilled personnel.
By overcoming challenges and embracing this proactive maintenance practice, new leaders can significantly contribute to the efficiency and longevity of their machinery, ensuring smooth operations within their organization.
資料ダウンロード
QCD調達購買管理クラウド「newji」は、調達購買部門で必要なQCD管理全てを備えた、現場特化型兼クラウド型の今世紀最高の購買管理システムとなります。
ユーザー登録
調達購買業務の効率化だけでなく、システムを導入することで、コスト削減や製品・資材のステータス可視化のほか、属人化していた購買情報の共有化による内部不正防止や統制にも役立ちます。
NEWJI DX
製造業に特化したデジタルトランスフォーメーション(DX)の実現を目指す請負開発型のコンサルティングサービスです。AI、iPaaS、および先端の技術を駆使して、製造プロセスの効率化、業務効率化、チームワーク強化、コスト削減、品質向上を実現します。このサービスは、製造業の課題を深く理解し、それに対する最適なデジタルソリューションを提供することで、企業が持続的な成長とイノベーションを達成できるようサポートします。
オンライン講座
製造業、主に購買・調達部門にお勤めの方々に向けた情報を配信しております。
新任の方やベテランの方、管理職を対象とした幅広いコンテンツをご用意しております。
お問い合わせ
コストダウンが利益に直結する術だと理解していても、なかなか前に進めることができない状況。そんな時は、newjiのコストダウン自動化機能で大きく利益貢献しよう!
(Β版非公開)