- お役立ち記事
- Tips for shortening lead times in trade Logistics arrangements and adjustments that should be made by the purchasing department
Tips for shortening lead times in trade Logistics arrangements and adjustments that should be made by the purchasing department
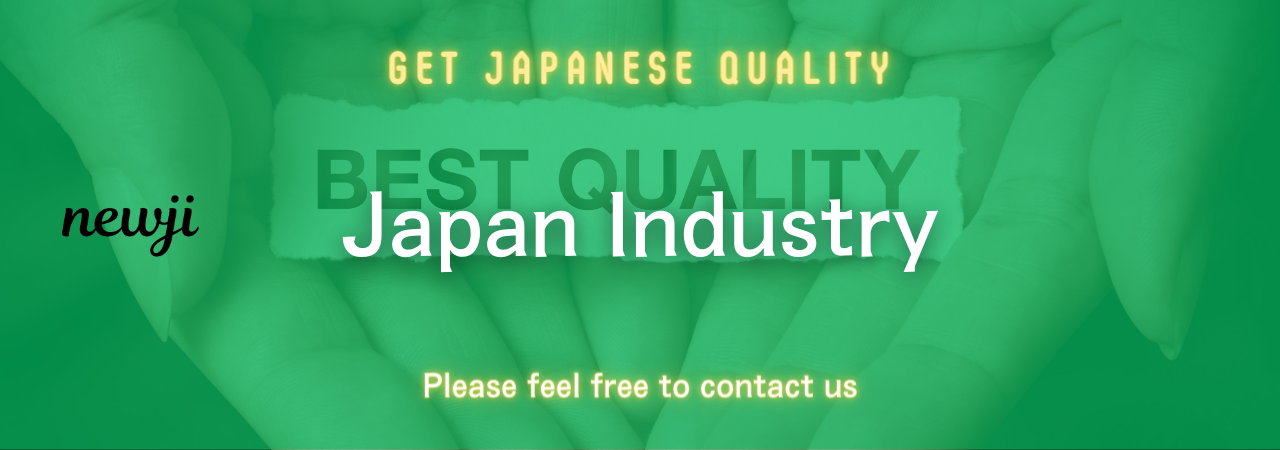
目次
Understanding Lead Times in Trade Logistics
In the world of trade logistics, lead times refer to the duration between the initiation of an order and the fulfillment or delivery of goods.
For businesses engaged in international trade, reducing lead times is crucial as it can significantly impact customer satisfaction and company profitability.
Efficient logistics arrangements and adjustments by the purchasing department are essential to achieving shorter lead times.
Why Reducing Lead Times Matters
Shorter lead times lead to numerous benefits for businesses.
First and foremost, quicker delivery improves customer satisfaction and loyalty by meeting their demand for faster service.
Additionally, it reduces inventory holding costs, which frees up capital for other business operations.
It also enhances a company’s competitiveness in the global market, allowing businesses to respond more swiftly to changes in demand and market conditions.
Strategies for Shortening Lead Times
There are several strategies that purchasing departments can employ to shorten lead times.
These strategies range from optimizing internal processes to leveraging technological advancements in supply chain management.
Streamline Supplier Relationships
Effective supplier relationships are fundamental to reducing lead times.
Building strong, communicative partnerships with suppliers ensures timely access to materials and goods.
To achieve this, the purchasing department should focus on:
– **Collaboration:** Work closely with suppliers to understand their capabilities and constraints, which helps in planning and reducing potential delays.
– **Prioritization:** Identify key suppliers who are critical to the supply chain and establish agreements that prioritize your orders.
– **Performance Monitoring:** Regularly monitor supplier performance and hold them accountable to agreed-upon service levels.
Implementing Just-In-Time Inventory
Just-In-Time (JIT) inventory management is a strategy where materials are ordered and received only as they are needed for production.
Although JIT can be risky, especially with supply chain disruptions, it can significantly reduce lead times if managed correctly.
– **Accurate Forecasting:** Use data analytics to anticipate demand accurately and order inventory accordingly.
– **Supplier Readiness:** Ensure that suppliers can provide materials swiftly to support the JIT model.
Optimizing Internal Processes
To achieve shorter lead times, the purchasing department must also focus on optimizing internal processes.
Enhancing Communication Across Departments
Effective communication is vital for smooth operations.
Ensuring that all departments are aligned and informed can help to reduce the time taken to process orders.
– **Integrated Systems:** Use integrated software systems so that departments share and access real-time data, preventing delays caused by miscommunication.
– **Regular Updates:** Hold regular meetings to discuss ongoing projects and potential bottlenecks.
Automating Purchase Orders
Manual processing of purchase orders is time-consuming and can lead to errors.
Automation can significantly reduce the time required to generate and process orders.
– **Implement Software:** Use purchase order management software to automate the ordering process, from order creation to order approval.
– **E-procurement Platforms:** Consider adopting e-procurement platforms that facilitate online transactions, speeding up the procurement process.
Technological Advancements in Trade Logistics
Leveraging technology is essential for modernizing logistics and shortening lead times.
Supply Chain Management Software
Investing in advanced supply chain management software can provide visibility into the entire supply chain.
– **Real-Time Tracking:** Use software that offers real-time tracking of shipments, enabling the purchasing department to anticipate and address delays efficiently.
– **Predictive Analytics:** Utilize analytics to predict potential disruptions and make data-driven decisions to mitigate risks.
Digital Payment Solutions
Digital payment solutions minimize the time taken for financial transactions, which can be a common bottleneck in international trade.
– **Faster Transactions:** Use blockchain or fintech solutions to speed up payment processing, ensuring timely payments to suppliers.
– **Reduced Errors:** Automated payment systems reduce human error and ensure accuracy in financial dealings.
Continuous Improvement and Adaptation
Finally, it is essential for the purchasing department to regularly review and adjust its processes.
Continuous improvement should be a key focus to ensure ongoing reduction in lead times.
Conduct Regular Audits
Regular audits help to identify inefficiencies within the supply chain.
– **Process Evaluation:** Evaluate each step of the procurement process for potential improvements.
– **Feedback Loop:** Establish a feedback mechanism with suppliers and internal teams to gather insights on possible enhancements.
Stay Updated on Industry Trends
The trade logistics landscape is ever-evolving, with new technologies and methodologies emerging frequently.
– **Training and Workshops:** Encourage teams to participate in training sessions and workshops to gain knowledge about the latest trends and tools.
– **Benchmarking:** Compare company practices against industry standards and competitors to uncover areas for improvement.
In conclusion, reducing lead times in trade logistics requires a proactive approach by the purchasing department.
By focusing on supplier relationships, optimizing processes, leveraging technology, and committing to continuous improvement, businesses can achieve more efficient operations and deliver better service to customers.
資料ダウンロード
QCD調達購買管理クラウド「newji」は、調達購買部門で必要なQCD管理全てを備えた、現場特化型兼クラウド型の今世紀最高の購買管理システムとなります。
ユーザー登録
調達購買業務の効率化だけでなく、システムを導入することで、コスト削減や製品・資材のステータス可視化のほか、属人化していた購買情報の共有化による内部不正防止や統制にも役立ちます。
NEWJI DX
製造業に特化したデジタルトランスフォーメーション(DX)の実現を目指す請負開発型のコンサルティングサービスです。AI、iPaaS、および先端の技術を駆使して、製造プロセスの効率化、業務効率化、チームワーク強化、コスト削減、品質向上を実現します。このサービスは、製造業の課題を深く理解し、それに対する最適なデジタルソリューションを提供することで、企業が持続的な成長とイノベーションを達成できるようサポートします。
オンライン講座
製造業、主に購買・調達部門にお勤めの方々に向けた情報を配信しております。
新任の方やベテランの方、管理職を対象とした幅広いコンテンツをご用意しております。
お問い合わせ
コストダウンが利益に直結する術だと理解していても、なかなか前に進めることができない状況。そんな時は、newjiのコストダウン自動化機能で大きく利益貢献しよう!
(Β版非公開)