- お役立ち記事
- Fundamentals of inventory management that purchasing departments should understand: Reduce costs with the EOQ model
Fundamentals of inventory management that purchasing departments should understand: Reduce costs with the EOQ model
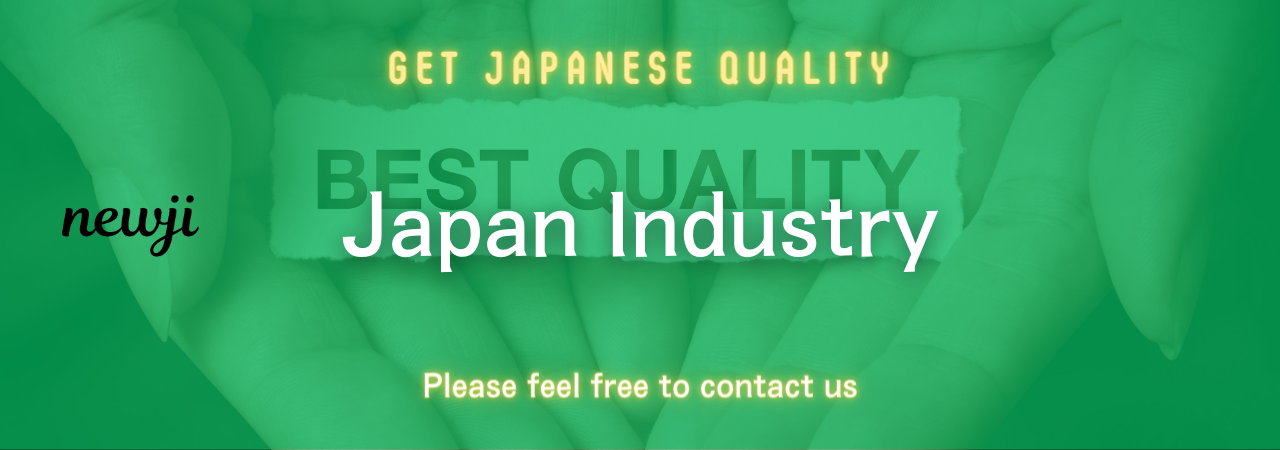
目次
Understanding Inventory Management
Inventory management is a crucial aspect of any business that deals with products.
It involves overseeing the procurement, storage, and utilization of a company’s inventory.
For purchasing departments, understanding the fundamentals of inventory management is essential as it directly impacts the cost efficiency and profitability of the business.
Effective inventory management ensures that a business has the right products in the right quantity available at the right time.
This helps in meeting customer demand without unnecessary overstock or stockouts.
Balancing these factors requires precise planning and strategy, which are fundamental roles for the purchasing department.
The Role of Purchasing Departments in Inventory Management
The purchasing department plays a pivotal role in inventory management.
Its core responsibilities include selecting suppliers, negotiating prices, and ensuring timely delivery of goods.
A well-managed purchasing department can significantly reduce costs and improve the supply chain’s efficiency.
Understanding inventory management processes helps in making informed decisions on order quantities and timings, which are crucial for maintaining optimal inventory levels.
Key Components of Inventory Management
Several components are central to effective inventory management:
Demand Forecasting
Demand forecasting involves predicting future customer demand using historical data, market trends, and other influencing factors.
Accurate demand forecasting helps purchasing departments make informed decisions on order quantities, minimizing the risks of overstocking or stockouts.
Inventory Tracking
Inventory tracking is essential for maintaining accurate inventory records.
Technological solutions like barcode systems, RFID tags, and inventory management software help track inventory in real-time, providing accurate data for decision-making.
Order Management
Order management is the process of tracking orders from placement to fulfillment.
This involves managing order processing, packaging, and delivery.
Efficient order management ensures timely fulfillment and helps in maintaining customer satisfaction.
Supplier Management
Building strong relationships with suppliers is key to successful inventory management.
Purchasing departments must evaluate supplier performance, negotiate favorable terms, and establish consistent communication to ensure a smooth supply chain.
Reducing Costs with the EOQ Model
The Economic Order Quantity (EOQ) model is a fundamental tool that helps purchasing departments optimize inventory management.
This model determines the ideal order quantity that minimizes the total costs associated with ordering and holding inventory.
Understanding the EOQ Model
The EOQ model calculates the most cost-effective quantity of inventory to order by balancing the costs of ordering and holding inventory.
It considers factors such as demand rate, ordering costs, and holding costs to determine the optimal order size.
Benefits of the EOQ Model
Implementing the EOQ model offers several benefits:
– **Cost Reduction:** By calculating the optimal order quantity, businesses can minimize both ordering and holding costs, leading to substantial cost savings.
– **Efficient Inventory Management:** The EOQ model helps in maintaining the perfect balance between inventory availability and associated costs, leading to more efficient inventory management.
– **Improved Cash Flow:** Reduced inventory costs mean more available cash for other business operations, improving overall cash flow.
Calculating EOQ
The EOQ formula is:
\[ EOQ = \sqrt{\frac{{2DS}}{H}} \]
Where:
– **D** = Demand rate (units per period)
– **S** = Ordering cost per order
– **H** = Holding cost per unit
This formula helps in determining the order quantity that minimizes the total yearly cost of inventory.
Implementing the EOQ Model
When implementing the EOQ model, it’s essential to gather accurate data on demand rate, ordering costs, and holding costs.
Having this information will enable the purchasing department to make precise calculations and adjustments.
Monitoring and reviewing the EOQ are also crucial as market conditions, demand rates, or costs may change over time, requiring updates to the model.
Challenges in Implementing EOQ
While the EOQ model provides valuable insights, it’s not without challenges.
It assumes constant demand and doesn’t account for variability in lead times or the presence of bulk discounts.
Businesses must adapt the model to fit their specific conditions and constraints.
Conclusion
Understanding the fundamentals of inventory management and effectively utilizing models like EOQ is vital for purchasing departments seeking to reduce costs and enhance efficiency.
Proper inventory management ensures that businesses remain competitive by meeting customer needs while minimizing unnecessary expenses.
By mastering these concepts, purchasing departments can significantly contribute to the overall success and sustainability of their companies.
資料ダウンロード
QCD調達購買管理クラウド「newji」は、調達購買部門で必要なQCD管理全てを備えた、現場特化型兼クラウド型の今世紀最高の購買管理システムとなります。
ユーザー登録
調達購買業務の効率化だけでなく、システムを導入することで、コスト削減や製品・資材のステータス可視化のほか、属人化していた購買情報の共有化による内部不正防止や統制にも役立ちます。
NEWJI DX
製造業に特化したデジタルトランスフォーメーション(DX)の実現を目指す請負開発型のコンサルティングサービスです。AI、iPaaS、および先端の技術を駆使して、製造プロセスの効率化、業務効率化、チームワーク強化、コスト削減、品質向上を実現します。このサービスは、製造業の課題を深く理解し、それに対する最適なデジタルソリューションを提供することで、企業が持続的な成長とイノベーションを達成できるようサポートします。
オンライン講座
製造業、主に購買・調達部門にお勤めの方々に向けた情報を配信しております。
新任の方やベテランの方、管理職を対象とした幅広いコンテンツをご用意しております。
お問い合わせ
コストダウンが利益に直結する術だと理解していても、なかなか前に進めることができない状況。そんな時は、newjiのコストダウン自動化機能で大きく利益貢献しよう!
(Β版非公開)