- お役立ち記事
- For production engineers in the chemical manufacturing industry! How to enhance process safety with flow-through reactors
For production engineers in the chemical manufacturing industry! How to enhance process safety with flow-through reactors
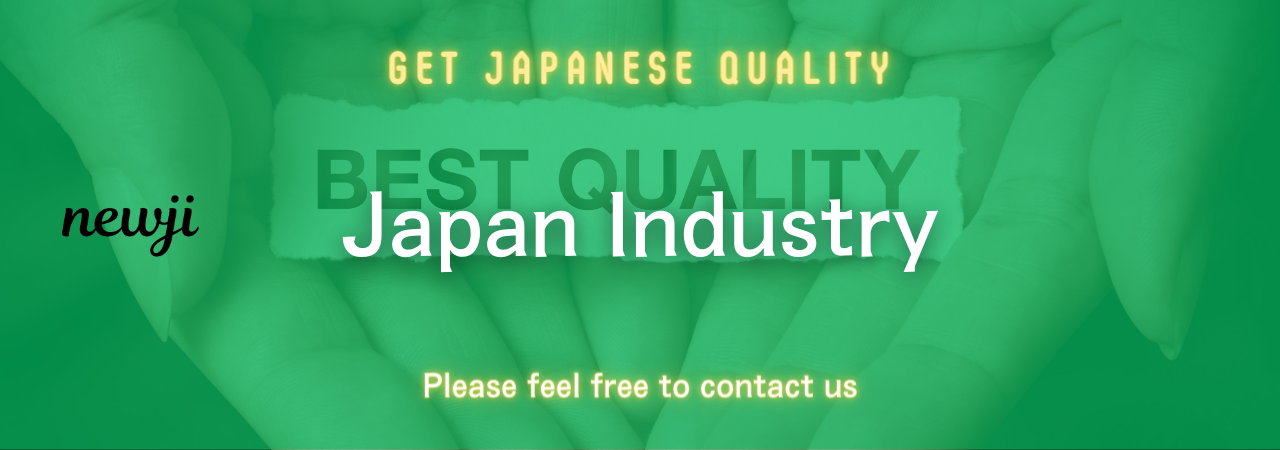
目次
Introduction to Process Safety in Chemical Manufacturing
Process safety is a critical aspect of the chemical manufacturing industry.
Ensuring that chemical reactions are controlled and operated safely helps to prevent accidents and environmental hazards.
In the ever-evolving world of chemical manufacturing, enhancing safety standards is paramount, and one of the innovative solutions making a significant impact is the use of flow-through reactors.
Understanding Flow-Through Reactors
Flow-through reactors, also known as continuous flow reactors, are systems where reactants are continuously fed into the reactor and products are continuously removed.
This approach contrasts with traditional batch reactors, where reactants are mixed in a single vessel and allowed to react over a set period.
Advantages of Flow-Through Reactors
1. **Improved Safety**: Flow-through reactors offer enhanced safety measures compared to batch reactors.
Since these systems operate continuously, the volume of reactants within the reactor at any given time is lower, reducing the risk of runaway reactions or explosions.
2. **Enhanced Control**: With flow-through systems, engineers have better control over reaction conditions such as temperature, pressure, and reaction time.
This precision allows for more predictable and safer chemical processes.
3. **Consistent Quality**: Continuous operation allows for a steady output of product, minimizing variations in product quality.
This consistency can reduce the likelihood of unsafe byproducts or impurities.
Implementing Flow-Through Reactors in Chemical Manufacturing
Transitioning from batch to flow-through reactors may seem daunting.
However, the benefits in terms of safety and efficiency can make the change worthwhile.
Assessing Compatibility with Existing Processes
Before implementing flow-through reactors, it is crucial to assess their compatibility with existing manufacturing processes.
This assessment should include evaluating the types of chemical reactions being performed and the required reaction conditions.
Some reactions may naturally lend themselves to continuous processes, while others may require significant modification.
Designing a Flow-Through System
Design is a critical step in successfully implementing flow-through reactors.
The design process should take into consideration the following factors:
– **Reactor Size and Throughput**: Engineers need to determine the appropriate reactor size and throughput rates.
This includes calculating the optimal flow rates to ensure that reactions proceed efficiently and safely.
– **Material Selection**: The choice of materials for constructing the reactor must be guided by the chemical compatibility and stability with the reactants and products.
This helps in preventing corrosion and maintaining the integrity of the reactor.
– **Instrumentation and Control Systems**: Advanced sensors and control systems are integral to maintaining safe operation of flow-through reactors.
These systems monitor parameters such as temperature, flow rate, and pressure in real-time.
Training and Operational Expertise
For successful operation of flow-through reactors, staffing must include trained personnel who understand the nuances of continuous processing.
Training should cover the operation of the reactors, troubleshooting potential issues, and emergency response procedures to ensure the safety of the plant and personnel.
Monitoring and Maintenance
Continuous systems require regular monitoring and maintenance to ensure their reliable operation.
Routine inspections and maintenance can preempt potential problems that may compromise safety.
Regular Inspections
Regular inspections should include checking for leaks, corrosion, and wear in the reactor system.
Instruments and sensors must also undergo routine calibration to maintain their accuracy and reliability.
Implementing Predictive Maintenance
Predictive maintenance technology, which uses data and predictive algorithms to anticipate equipment failures before they happen, can further enhance the safety of flow-through reactors.
By predicting failures, maintenance can be scheduled to replace parts or address potential issues before they lead to more significant problems.
Conclusion: The Future of Process Safety in Chemical Manufacturing
Flow-through reactors represent a promising advancement in process safety for the chemical manufacturing industry.
Their ability to offer enhanced control, consistent product quality, and improved safety make them a viable option for many chemical processes.
By thoroughly assessing compatibility, designing suitable systems, and ensuring adequate training and maintenance, chemical manufacturers can successfully integrate these novel technologies into their operations.
The transition to flow-through reactors not only promotes safer working conditions but also aligns with the industry’s goals for more efficient and sustainable manufacturing practices.
Embracing these advancements could set a new standard for safety and innovation in the chemical manufacturing sector.
資料ダウンロード
QCD調達購買管理クラウド「newji」は、調達購買部門で必要なQCD管理全てを備えた、現場特化型兼クラウド型の今世紀最高の購買管理システムとなります。
ユーザー登録
調達購買業務の効率化だけでなく、システムを導入することで、コスト削減や製品・資材のステータス可視化のほか、属人化していた購買情報の共有化による内部不正防止や統制にも役立ちます。
NEWJI DX
製造業に特化したデジタルトランスフォーメーション(DX)の実現を目指す請負開発型のコンサルティングサービスです。AI、iPaaS、および先端の技術を駆使して、製造プロセスの効率化、業務効率化、チームワーク強化、コスト削減、品質向上を実現します。このサービスは、製造業の課題を深く理解し、それに対する最適なデジタルソリューションを提供することで、企業が持続的な成長とイノベーションを達成できるようサポートします。
オンライン講座
製造業、主に購買・調達部門にお勤めの方々に向けた情報を配信しております。
新任の方やベテランの方、管理職を対象とした幅広いコンテンツをご用意しております。
お問い合わせ
コストダウンが利益に直結する術だと理解していても、なかなか前に進めることができない状況。そんな時は、newjiのコストダウン自動化機能で大きく利益貢献しよう!
(Β版非公開)