- お役立ち記事
- Efficient Japanese Techniques: Redefining Process Management in Manufacturing
Efficient Japanese Techniques: Redefining Process Management in Manufacturing
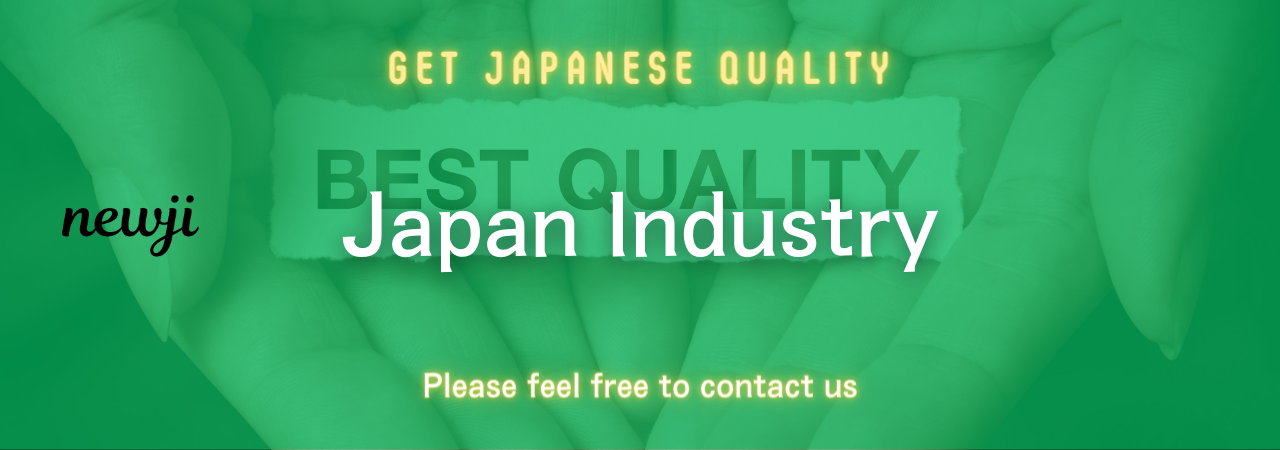
目次
Introduction
Efficient process management is the backbone of successful manufacturing operations. Japanese manufacturing, renowned globally for its excellence, has pioneered techniques that redefine how processes are managed. These methodologies have not only elevated product quality but have also optimized operational efficiency. This article delves into the core aspects of Japanese process management techniques, exploring their advantages, challenges, and practical applications in procurement and purchasing. By understanding these strategies, manufacturing companies can harness the benefits of Japanese efficiency, enhance their competitive edge, and foster sustainable growth.
Overview of Japanese Process Management Techniques
Japanese process management encompasses a range of methodologies designed to streamline operations, minimize waste, and ensure high-quality output. Key among these techniques are Lean Manufacturing, Just-In-Time (JIT) production, Total Quality Management (TQM), and Kaizen.
Lean Manufacturing
Lean Manufacturing focuses on eliminating waste within the manufacturing process. Waste is categorized into seven types: defects, overproduction, waiting, non-utilized talent, transportation, inventory, and motion. By addressing these areas, companies can create more value with fewer resources, leading to increased efficiency and reduced costs.
Just-In-Time (JIT) Production
JIT production aims to produce only what is needed, when it is needed, and in the quantity needed. This approach minimizes inventory costs and reduces waste by ensuring that materials and products move through the production process seamlessly. JIT requires precise coordination with suppliers and a flexible manufacturing system capable of responding to demand fluctuations.
Total Quality Management (TQM)
TQM is an organization-wide approach focused on continuous improvement in quality. It involves every employee in the quality improvement process, emphasizing customer satisfaction, process optimization, and defect prevention. TQM integrates quality principles into all aspects of operations, fostering a culture of excellence.
Kaizen
Kaizen, meaning “continuous improvement,” is a philosophy that encourages incremental enhancements in processes. It involves all employees, from top management to the shop floor, in identifying and implementing improvements. Kaizen promotes a proactive approach to problem-solving and innovation, ensuring that processes evolve to meet changing demands and conditions.
Advantages of Japanese Techniques in Manufacturing
Adopting Japanese process management techniques offers numerous benefits, enhancing both operational efficiency and product quality. These advantages contribute to the overall competitiveness and sustainability of manufacturing businesses.
Enhanced Efficiency
Japanese techniques streamline manufacturing processes, reducing unnecessary steps and optimizing workflow. This leads to faster production times, lower operational costs, and increased output without compromising quality. Enhanced efficiency translates into better resource utilization and higher profitability.
Improved Quality
Emphasizing quality at every stage of production ensures that products meet stringent standards. Techniques like TQM and Kaizen foster a culture of excellence, where continuous improvement and defect prevention are prioritized. High-quality products enhance customer satisfaction and loyalty, driving repeat business and positive brand reputation.
Reduced Waste
Lean Manufacturing and JIT focus on minimizing waste, whether it be excess inventory, overproduction, or inefficient use of resources. Reducing waste not only lowers costs but also contributes to environmental sustainability by minimizing the ecological footprint of manufacturing operations.
Flexibility and Responsiveness
Japanese process management techniques foster a flexible and responsive manufacturing system. The ability to adapt to changing market demands and respond swiftly to supply chain disruptions ensures that businesses remain competitive and can seize new opportunities promptly.
Employee Engagement and Morale
Involving employees in continuous improvement initiatives empowers them and enhances job satisfaction. When employees are actively engaged in optimizing processes, they take ownership of their work, leading to higher morale, reduced turnover, and a more committed workforce.
Challenges and Disadvantages
While Japanese process management techniques offer significant advantages, their implementation can present challenges. Understanding these potential drawbacks is essential for organizations considering adopting these methodologies.
Cultural Differences
Japanese process management is deeply rooted in cultural values such as teamwork, respect, and continuous improvement. Organizations outside Japan may find it challenging to replicate these cultural aspects, which are integral to the success of these techniques. Adapting these methodologies to fit different cultural contexts requires careful consideration and may necessitate organizational changes.
Initial Implementation Costs
Implementing Japanese process management techniques often involves upfront investments in training, process redesign, and technology. These initial costs can be a barrier for organizations with limited financial resources. However, the long-term benefits typically outweigh the initial expenses by enhancing efficiency and reducing ongoing operational costs.
Resistance to Change
Employees and management may resist changes to established processes and workflows. Overcoming this resistance requires effective change management strategies, clear communication of benefits, and active involvement of all stakeholders in the transition process. Without addressing resistance, the implementation of Japanese techniques may face significant hurdles.
Dependency on Supplier Relationships
Techniques like JIT rely heavily on strong relationships with suppliers to ensure timely delivery of materials. Any disruption in the supply chain can have a cascading effect on the entire production process. Building and maintaining reliable supplier partnerships is crucial but can be challenging, especially in volatile market conditions.
Procurement and Purchasing in Japanese Manufacturing
Procurement and purchasing are critical components of Japanese manufacturing process management. These functions ensure the timely acquisition of high-quality materials and components, supporting the overall efficiency and quality of production.
Strategic Supplier Partnerships
Japanese manufacturers prioritize building long-term, strategic relationships with suppliers. These partnerships are based on mutual trust, collaboration, and shared objectives. By working closely with suppliers, companies can ensure consistent quality, secure favorable terms, and foster innovation through joint development initiatives.
Supplier Selection and Evaluation
Selecting the right suppliers is crucial for maintaining the standards of Japanese process management. Rigorous evaluation criteria are applied, including assessments of quality systems, production capabilities, financial stability, and adherence to continuous improvement practices. Regular performance reviews and audits help maintain high standards and address any issues proactively.
Integrated Supply Chain Management
Integration of the supply chain is a hallmark of Japanese manufacturing. This involves seamless coordination between suppliers, manufacturers, and distributors to ensure smooth material flow and timely product delivery. Advanced information systems and collaborative planning tools facilitate real-time communication and coordination, enhancing supply chain efficiency.
Cost Management and Value Creation
While cost management is important, Japanese procurement practices emphasize value creation beyond mere cost reduction. This includes focusing on total cost of ownership, which considers factors like quality, reliability, and long-term benefits. By prioritizing value, companies can achieve sustainable cost savings and enhance overall productivity.
Supplier Negotiation Techniques
Effective supplier negotiation is essential for securing favorable terms and ensuring the reliability of the supply chain. Japanese manufacturers employ specific negotiation techniques that reflect their emphasis on long-term relationships and mutual benefit.
Win-Win Approach
Japanese negotiation strategies focus on creating win-win scenarios where both parties benefit. This approach fosters trust and long-term collaboration, as opposed to adversarial tactics that can damage relationships. By seeking mutually beneficial outcomes, companies can establish stable and dependable supplier partnerships.
Emphasis on Relationship Building
Building strong relationships with suppliers is a cornerstone of Japanese negotiation practices. Regular communication, face-to-face meetings, and cultural understanding are integral to fostering trust and cooperation. These relationships enable more effective negotiations and smoother resolution of conflicts when they arise.
Long-Term Commitment
Japanese manufacturers often demonstrate a commitment to long-term partnerships rather than seeking short-term gains. This long-term perspective encourages suppliers to invest in quality improvements and innovation, knowing that their efforts will be rewarded with sustained business.
Transparency and Open Communication
Transparency in negotiations helps build trust and facilitate smoother agreements. Japanese negotiation techniques prioritize open communication about needs, constraints, and expectations. This honesty helps prevent misunderstandings and ensures that both parties are aligned in their objectives.
Flexibility and Adaptability
Flexibility in negotiations allows for adjustments based on changing circumstances. Japanese companies are willing to adapt terms and share risks to maintain strong supplier relationships. This adaptability ensures that partnerships can withstand market fluctuations and other external pressures.
Market Conditions and Trends
Understanding market conditions and trends is vital for effective process management and procurement strategies. Japanese manufacturers continuously monitor and adapt to global market dynamics to maintain their competitive edge.
Globalization and Supply Chain Complexity
Globalization has increased the complexity of supply chains, with materials and components sourced from diverse geographic locations. Japanese manufacturers address this complexity through robust supply chain management practices, ensuring reliability and flexibility despite the challenges of operating in a global market.
Technological Advancements
Advancements in technology, such as automation, artificial intelligence, and the Internet of Things (IoT), are transforming manufacturing processes. Japanese companies leverage these technologies to enhance precision, reduce human error, and optimize production workflows. Staying abreast of technological trends is essential for maintaining process efficiency and competitiveness.
Sustainability and Environmental Concerns
Sustainability has become a critical focus in manufacturing. Japanese process management techniques incorporate environmentally friendly practices, such as waste reduction, energy efficiency, and sustainable sourcing. These initiatives not only comply with regulatory standards but also meet the growing consumer demand for sustainable products.
Economic Fluctuations and Resilience
Economic fluctuations can impact supply and demand, affecting manufacturing operations. Japanese techniques emphasize building resilient processes that can adapt to economic changes. Strategies include maintaining flexibility in production schedules, diversifying supplier bases, and implementing risk management practices to mitigate the impact of economic uncertainties.
Shift Towards Customization
Consumers increasingly demand customized products tailored to their specific needs. Japanese process management techniques, with their emphasis on flexibility and efficiency, are well-suited to accommodate customization. Techniques like JIT and Lean Manufacturing enable manufacturers to produce customized products without sacrificing efficiency or quality.
Best Practices in Implementing Japanese Process Management
Successfully implementing Japanese process management techniques requires a strategic approach that considers organizational culture, employee engagement, and continuous improvement. Here are some best practices for integrating these methodologies into manufacturing operations.
Comprehensive Training and Education
Educating employees about Japanese process management techniques is crucial for successful implementation. Training programs should cover the principles of Lean Manufacturing, JIT, TQM, and Kaizen, ensuring that all team members understand their roles in the process. Continuous education fosters a culture of improvement and empowers employees to contribute effectively.
Leadership Commitment
Leadership plays a pivotal role in driving the adoption of process management techniques. Leaders must demonstrate commitment by actively supporting initiatives, allocating resources, and leading by example. Their dedication sets the tone for the entire organization, encouraging employees to embrace change and strive for excellence.
Employee Involvement and Empowerment
Involving employees in decision-making and improvement initiatives enhances ownership and accountability. Encouraging suggestions and providing platforms for feedback empower employees to identify and address inefficiencies. This collaborative approach fosters a sense of responsibility and drives continuous improvement from within the workforce.
Clear Objective Setting
Setting clear, measurable objectives aligns the organization towards common goals. Objectives should be specific, achievable, relevant, and time-bound (SMART), providing a roadmap for implementing process management techniques. Regularly reviewing and adjusting these objectives ensures that the organization remains focused and adaptable to changing circumstances.
Utilization of Technology
Leveraging technology can significantly enhance the effectiveness of process management techniques. Advanced software for supply chain management, data analytics, and process automation can streamline operations, provide real-time insights, and facilitate better decision-making. Investing in the right technology supports the seamless integration of Japanese methodologies.
Continuous Monitoring and Evaluation
Regular monitoring and evaluation are essential for assessing the effectiveness of implemented techniques. Key performance indicators (KPIs) should be established to measure progress and identify areas for improvement. Continuous evaluation ensures that processes remain efficient and that the organization can quickly address any emerging issues.
Adaptation to Local Context
While Japanese process management techniques offer proven benefits, adapting them to fit the local context is crucial for success. Consider cultural, regulatory, and operational differences when implementing these methodologies. Tailoring the approaches to align with the organization’s unique environment ensures smoother integration and better outcomes.
Conclusion
Japanese process management techniques have revolutionized manufacturing, setting benchmarks for efficiency, quality, and continuous improvement. By adopting methodologies such as Lean Manufacturing, JIT, TQM, and Kaizen, companies can significantly enhance their operational performance and competitiveness. However, successful implementation requires addressing cultural differences, managing change effectively, and fostering strong supplier relationships. Understanding and applying these best practices in procurement and purchasing can unlock the full potential of Japanese efficiencies, driving sustainable growth and excellence in the manufacturing sector.
資料ダウンロード
QCD調達購買管理クラウド「newji」は、調達購買部門で必要なQCD管理全てを備えた、現場特化型兼クラウド型の今世紀最高の購買管理システムとなります。
ユーザー登録
調達購買業務の効率化だけでなく、システムを導入することで、コスト削減や製品・資材のステータス可視化のほか、属人化していた購買情報の共有化による内部不正防止や統制にも役立ちます。
NEWJI DX
製造業に特化したデジタルトランスフォーメーション(DX)の実現を目指す請負開発型のコンサルティングサービスです。AI、iPaaS、および先端の技術を駆使して、製造プロセスの効率化、業務効率化、チームワーク強化、コスト削減、品質向上を実現します。このサービスは、製造業の課題を深く理解し、それに対する最適なデジタルソリューションを提供することで、企業が持続的な成長とイノベーションを達成できるようサポートします。
オンライン講座
製造業、主に購買・調達部門にお勤めの方々に向けた情報を配信しております。
新任の方やベテランの方、管理職を対象とした幅広いコンテンツをご用意しております。
お問い合わせ
コストダウンが利益に直結する術だと理解していても、なかなか前に進めることができない状況。そんな時は、newjiのコストダウン自動化機能で大きく利益貢献しよう!
(Β版非公開)