- お役立ち記事
- Revolutionizing Japanese Manufacturing: The Ultimate Guide to CC-Link Integration
Revolutionizing Japanese Manufacturing: The Ultimate Guide to CC-Link Integration
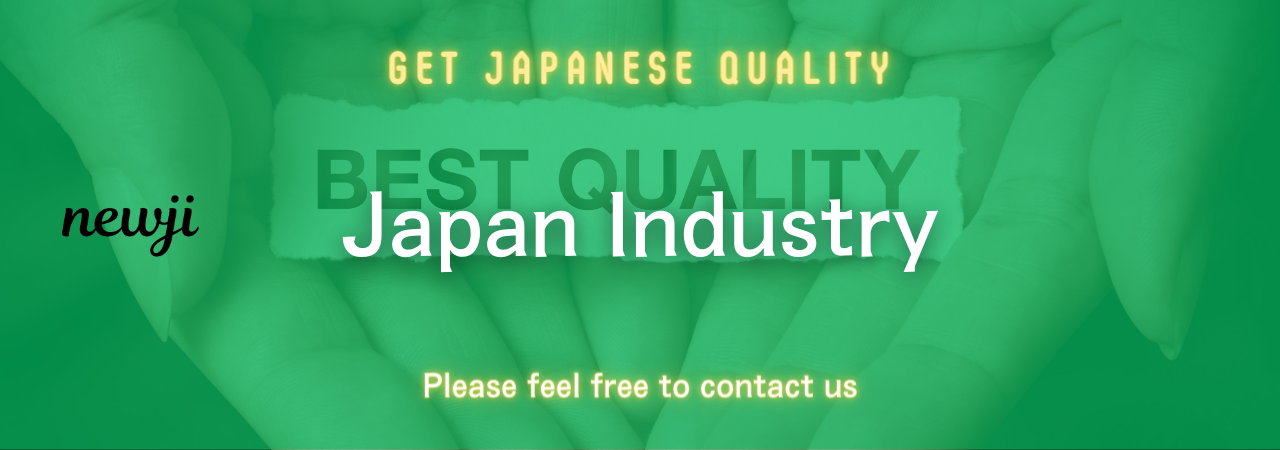
目次
Introduction to CC-Link in Japanese Manufacturing
Japanese manufacturing has long been synonymous with precision, efficiency, and innovation. Central to this reputation is the adoption of advanced communication protocols that streamline operations and enhance productivity. One such protocol that has revolutionized the industry is CC-Link. This guide delves into the intricacies of CC-Link integration, exploring its benefits, challenges, and best practices for procurement and purchasing professionals working with Japanese suppliers.
What is CC-Link?
CC-Link, short for Control & Communication Link, is a high-speed, open industrial networking standard developed in Japan. It facilitates seamless communication between various manufacturing devices, including programmable logic controllers (PLCs), sensors, and actuators. By enabling real-time data exchange, CC-Link enhances automation processes, ensuring synchronized operations across the production floor.
History and Evolution
Introduced in the early 1990s by Mitsubishi Electric, CC-Link was designed to address the growing need for a robust and scalable communication system in manufacturing environments. Over the years, it has evolved to support increasingly complex industrial applications, integrating advanced features such as wireless communication and Ethernet compatibility. Its widespread adoption in Japanese manufacturing underscores its reliability and effectiveness.
Key Features of CC-Link
– **High-Speed Communication:** CC-Link offers data transmission rates that minimize latency, ensuring timely decision-making and rapid response to changes in the production process.
– **Scalability:** The network can support a vast number of devices, making it suitable for both small-scale operations and large, complex manufacturing systems.
– **Open Standard:** Being an open protocol, CC-Link allows for interoperability between equipment from different manufacturers, fostering a flexible and adaptable manufacturing environment.
– **Robustness:** Designed to withstand the harsh conditions of industrial settings, CC-Link ensures consistent performance even in challenging environments.
Advantages of CC-Link Integration
Integrating CC-Link into manufacturing operations offers numerous advantages that can significantly enhance efficiency and competitiveness.
Enhanced Automation and Control
CC-Link enables precise control over manufacturing processes by facilitating real-time communication between devices. This leads to improved synchronization, reduced downtime, and higher product quality.
Cost Efficiency
By streamlining communication and reducing the need for extensive wiring, CC-Link can lower installation and maintenance costs. Its scalability also ensures that manufacturers can expand their systems without incurring substantial additional expenses.
Interoperability and Flexibility
The open nature of CC-Link allows for seamless integration with a wide range of devices and systems from different manufacturers. This flexibility enables manufacturers to customize their setups to meet specific operational needs without being locked into a single supplier.
Improved Data Management
With CC-Link, manufacturers can collect and analyze vast amounts of data in real-time. This capability supports informed decision-making, predictive maintenance, and continuous improvement initiatives.
Challenges and Considerations
While CC-Link offers numerous benefits, successful integration requires careful planning and consideration of potential challenges.
Initial Investment
The upfront costs associated with implementing CC-Link can be significant, especially for smaller manufacturers. Investments may include purchasing compatible devices, training personnel, and upgrading existing infrastructure.
Technical Expertise
Effective CC-Link integration demands a high level of technical expertise. Manufacturers may need to invest in training or hire specialists to manage and maintain the network.
Compatibility Issues
Ensuring compatibility between CC-Link and existing systems is crucial. Manufacturers must assess their current infrastructure and identify any modifications needed to facilitate seamless integration.
Maintenance and Support
Ongoing maintenance is essential to sustain the performance of a CC-Link network. Manufacturers should establish robust support systems, including regular updates and troubleshooting protocols.
Supplier Negotiation Techniques for CC-Link Integration
Negotiating with Japanese suppliers for CC-Link integration requires a strategic approach, emphasizing mutual benefits and long-term partnerships.
Understanding Supplier Capabilities
Before entering negotiations, it’s essential to thoroughly understand the capabilities and limitations of potential suppliers. This includes evaluating their expertise with CC-Link, their track record in similar projects, and their ability to provide ongoing support.
Building Strong Relationships
Japanese business culture places a high value on trust and long-term relationships. Investing time in building rapport with suppliers can lead to more favorable terms and collaborative problem-solving.
Leveraging Market Conditions
Being aware of the current market conditions can provide leverage during negotiations. For instance, understanding supply and demand dynamics can help in negotiating better pricing or more flexible terms.
Emphasizing Mutual Benefits
Highlight how the partnership benefits both parties. For example, successful CC-Link integration can lead to increased production efficiency, which benefits the manufacturer and provides ongoing business for the supplier.
Negotiating Terms and Conditions
Clearly define the scope of work, delivery timelines, payment terms, and support services. Ensuring that all parties have a shared understanding can prevent future disputes and ensure smooth project execution.
Market Conditions and Trends
Staying abreast of market conditions and emerging trends is crucial for effective CC-Link integration and procurement strategies.
Technological Advancements
The manufacturing sector is rapidly adopting Industry 4.0 technologies. CC-Link continues to evolve, incorporating features like wireless communication and enhanced cybersecurity measures to stay relevant in a digital age.
Global Supply Chain Dynamics
Global supply chain disruptions can impact the availability and cost of CC-Link-compatible devices. Diversifying suppliers and establishing contingency plans can mitigate these risks.
Regulatory Changes
Manufacturers must stay informed about regulatory changes that affect communication protocols and industrial standards. Compliance with these regulations is essential to avoid legal issues and ensure smooth operation.
Sustainability Initiatives
There is a growing emphasis on sustainability in manufacturing. CC-Link can support these initiatives by enabling more efficient energy use and reducing waste through optimized production processes.
Best Practices for CC-Link Integration
Implementing CC-Link effectively requires adherence to best practices that ensure maximum benefits and minimal disruptions.
Comprehensive Planning
Develop a detailed integration plan that outlines objectives, timelines, resource allocation, and risk management strategies. Comprehensive planning lays the foundation for successful implementation.
Selecting the Right Equipment
Choose CC-Link-compatible devices that meet your operational requirements. Consider factors such as scalability, compatibility, and vendor support when selecting equipment.
Training and Development
Invest in training programs to equip your team with the necessary skills to manage and maintain the CC-Link network. Well-trained personnel are essential for effective operation and troubleshooting.
Testing and Validation
Before full-scale deployment, conduct thorough testing to ensure that all components of the CC-Link network function as intended. Validation helps identify and address potential issues early in the process.
Continuous Monitoring and Optimization
Implement monitoring systems to track the performance of the CC-Link network continuously. Use the collected data to optimize processes, enhance efficiency, and address any emerging issues proactively.
Case Studies: Successful CC-Link Integration
Examining real-world examples of successful CC-Link integration provides valuable insights into best practices and common challenges.
Automotive Manufacturing
A leading Japanese automotive manufacturer integrated CC-Link to synchronize assembly line operations. The result was a significant reduction in production downtime and an increase in overall output quality.
Electronics Production
An electronics producer adopted CC-Link to enhance communication between its automated testing equipment and production lines. This integration led to faster testing cycles and improved product reliability.
Food and Beverage Industry
A food processing company utilized CC-Link to streamline its packaging and labeling processes. The integration improved operational efficiency and ensured consistent product quality across batches.
Future Outlook for CC-Link in Manufacturing
As manufacturing continues to evolve, CC-Link is poised to play a pivotal role in shaping the future of the industry.
Integration with Industry 4.0
CC-Link’s ability to support real-time data exchange and connectivity aligns perfectly with Industry 4.0 principles. Its integration with smart factory technologies will further enhance automation and data analytics capabilities.
Advancements in AI and Machine Learning
The incorporation of AI and machine learning with CC-Link can lead to more intelligent manufacturing systems. Predictive maintenance, quality control, and process optimization are areas that can benefit significantly from these advancements.
Expansion into New Markets
CC-Link is expected to expand its presence beyond Japan, catering to global manufacturing hubs. Its adaptability and open standard make it an attractive choice for diverse industrial applications worldwide.
Conclusion
CC-Link integration represents a transformative step for Japanese manufacturing, offering enhanced automation, cost efficiencies, and improved data management. While the initial investment and technical challenges may pose hurdles, the long-term benefits make it a worthwhile endeavor. By adopting best practices, building strong supplier relationships, and staying attuned to market trends, manufacturers can leverage CC-Link to achieve operational excellence and maintain their competitive edge in the global market.
資料ダウンロード
QCD調達購買管理クラウド「newji」は、調達購買部門で必要なQCD管理全てを備えた、現場特化型兼クラウド型の今世紀最高の購買管理システムとなります。
ユーザー登録
調達購買業務の効率化だけでなく、システムを導入することで、コスト削減や製品・資材のステータス可視化のほか、属人化していた購買情報の共有化による内部不正防止や統制にも役立ちます。
NEWJI DX
製造業に特化したデジタルトランスフォーメーション(DX)の実現を目指す請負開発型のコンサルティングサービスです。AI、iPaaS、および先端の技術を駆使して、製造プロセスの効率化、業務効率化、チームワーク強化、コスト削減、品質向上を実現します。このサービスは、製造業の課題を深く理解し、それに対する最適なデジタルソリューションを提供することで、企業が持続的な成長とイノベーションを達成できるようサポートします。
オンライン講座
製造業、主に購買・調達部門にお勤めの方々に向けた情報を配信しております。
新任の方やベテランの方、管理職を対象とした幅広いコンテンツをご用意しております。
お問い合わせ
コストダウンが利益に直結する術だと理解していても、なかなか前に進めることができない状況。そんな時は、newjiのコストダウン自動化機能で大きく利益貢献しよう!
(Β版非公開)