- お役立ち記事
- Purchasing strategy to improve product quality through supplier evaluation
Purchasing strategy to improve product quality through supplier evaluation
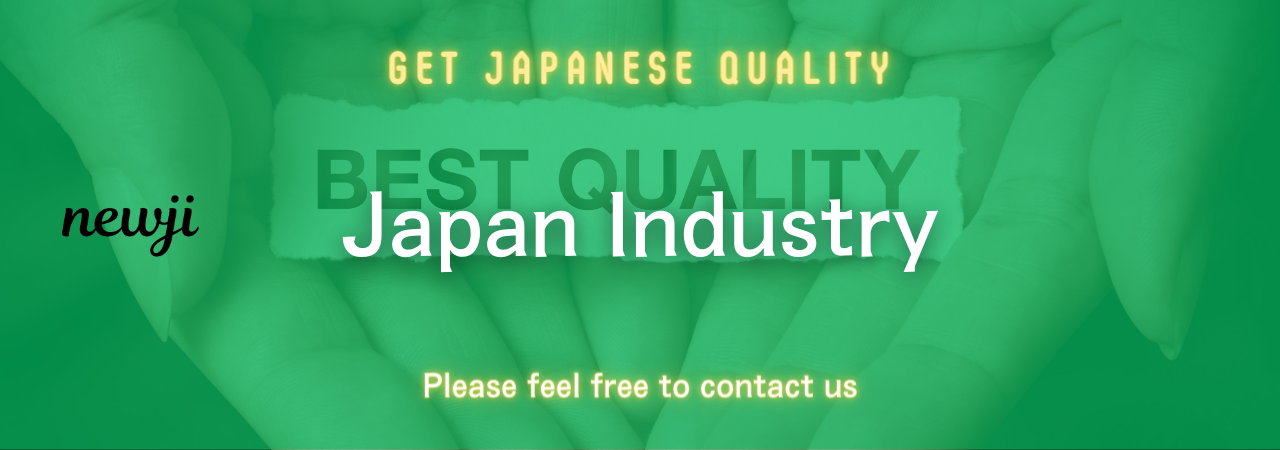
目次
Understanding Supplier Evaluation
A crucial component in the purchasing strategy to improve product quality is supplier evaluation.
It is the process of assessing and approving potential suppliers through quantitative and qualitative assessment measures.
This evaluation not only helps a company ensure that its suppliers meet necessary standards but also builds strong partnerships geared towards maintaining high product quality.
Evaluating suppliers entails examining various factors such as reliability, costs, production capabilities, quality of materials, delivery times, and compliance with regulations.
It’s not a one-time process but rather a continual one, enabling businesses to maintain an ongoing understanding of a supplier’s ability to meet current and future demands.
The Importance of Supplier Evaluation
Supplier evaluation is essential in maintaining consistency and quality across the supply chain.
In an increasingly competitive marketplace, ensuring the highest standards of product quality can set a business apart.
A systematic approach to evaluating suppliers can significantly contribute to the end product’s quality, reduce costs, and improve operational efficiency.
A key reason for conducting supplier evaluations is risk mitigation.
Inadequately assessed suppliers may present risks such as supply chain disruptions, compliance issues, or quality discrepancies.
By regularly evaluating suppliers, businesses can identify potential issues before they become significant problems, allowing them to take proactive measures to prevent negative impacts on their operations.
Components of Effective Supplier Evaluation
To conduct an effective supplier evaluation, businesses must consider a range of factors.
These typically include:
Quality Assurance
One of the primary concerns is the quality of materials or components provided by the supplier.
Businesses should determine whether a supplier has a quality management system in place and whether they comply with relevant industry standards and certifications.
Conducting audits or requesting documentation can ensure that a supplier consistently delivers the quality expected.
Reliability and Timeliness
Reliability can significantly affect the overall supply chain.
A supplier’s ability to deliver products on time, as per the agreed terms, is crucial for maintaining inventory levels and meeting customer expectations.
Businesses should assess the supplier’s history regarding delivery times and their ability to handle changes in demand.
Cost Management
While cost is a crucial part in supplier evaluation, it should not overshadow other factors such as quality and reliability.
Evaluating suppliers based on pricing should involve a total cost assessment, including hidden costs, such as transport, handling fees, and long-term partnership value.
Financial Stability
Assessing financial stability helps to predict whether a supplier will be able to remain operational long-term.
Businesses should review the supplier’s financial records to ensure stability.
A financially stable supplier is less likely to experience disruptions, ensuring continuous supply.
Compliance and Ethics
The ever-growing emphasis on sustainability and ethical sourcing requires businesses to evaluate suppliers based on their compliance with environmental standards and ethical practices.
Adhering to regulations and ethical standards not only aligns with corporate responsibility but can also affect the market perception of the end product.
Steps to Implement Supplier Evaluation
Implementing a structured supplier evaluation process requires several methodical steps:
Define Evaluation Criteria
Firstly, establish clear and precise evaluation criteria that align with your business objectives and quality standards.
The criteria should encompass all factors important to the business, from quality and cost to compliance and risk management.
Develop an Evaluation System
Create an evaluation system or framework that allows for the objective and standardized assessment of suppliers.
This system can utilize scoring models or objective indicators to ensure a fair analysis of each supplier’s capabilities and performance.
Collect and Analyze Data
Collect comprehensive data from both internal and external sources.
Feedback from different departments, performance history, audits, and market research should all contribute to forming a complete picture of the supplier’s reliability and performance.
Conduct Supplier Audits
Supplier audits can be instrumental in evaluating the operational capabilities and processes of a supplier.
Regular audits allow businesses to verify information, assess compliance with standards, and identify areas for improvement.
Review and Feedback
Regular review of supplier performance is necessary.
Businesses should maintain open communication with their suppliers, providing constructive feedback to foster long-term relationships and quality improvement.
Benefits of a Robust Supplier Evaluation Process
An effective supplier evaluation process offers several advantages.
It enhances product quality, minimizes risks, and optimizes costs.
Moreover, it fosters stronger supplier relationships, leading to better collaboration, innovation, and consistency in supply chain performance.
When suppliers understand that consistent evaluation is part of the business relationship, it encourages them to improve their processes and maintain high standards.
This mutual focus on continuous improvement benefits both parties and ultimately elevates the quality of products reaching consumers.
Conclusion
Implementing a strategic purchasing approach by improving product quality through systematic supplier evaluation is vital in today’s competitive markets.
Through rigorous assessments, businesses can ensure suppliers align with their quality, reliability, and ethical standards.
By doing so, they secure not only the quality of their products but also the efficiency and sustainability of their operations.
In conclusion, an effective supplier evaluation process is an essential tool in achieving a competitive advantage while safeguarding the integrity of the supply chain.
資料ダウンロード
QCD調達購買管理クラウド「newji」は、調達購買部門で必要なQCD管理全てを備えた、現場特化型兼クラウド型の今世紀最高の購買管理システムとなります。
ユーザー登録
調達購買業務の効率化だけでなく、システムを導入することで、コスト削減や製品・資材のステータス可視化のほか、属人化していた購買情報の共有化による内部不正防止や統制にも役立ちます。
NEWJI DX
製造業に特化したデジタルトランスフォーメーション(DX)の実現を目指す請負開発型のコンサルティングサービスです。AI、iPaaS、および先端の技術を駆使して、製造プロセスの効率化、業務効率化、チームワーク強化、コスト削減、品質向上を実現します。このサービスは、製造業の課題を深く理解し、それに対する最適なデジタルソリューションを提供することで、企業が持続的な成長とイノベーションを達成できるようサポートします。
オンライン講座
製造業、主に購買・調達部門にお勤めの方々に向けた情報を配信しております。
新任の方やベテランの方、管理職を対象とした幅広いコンテンツをご用意しております。
お問い合わせ
コストダウンが利益に直結する術だと理解していても、なかなか前に進めることができない状況。そんな時は、newjiのコストダウン自動化機能で大きく利益貢献しよう!
(Β版非公開)