- お役立ち記事
- How to develop quality standards and monitoring systems in purchasing contracts
How to develop quality standards and monitoring systems in purchasing contracts
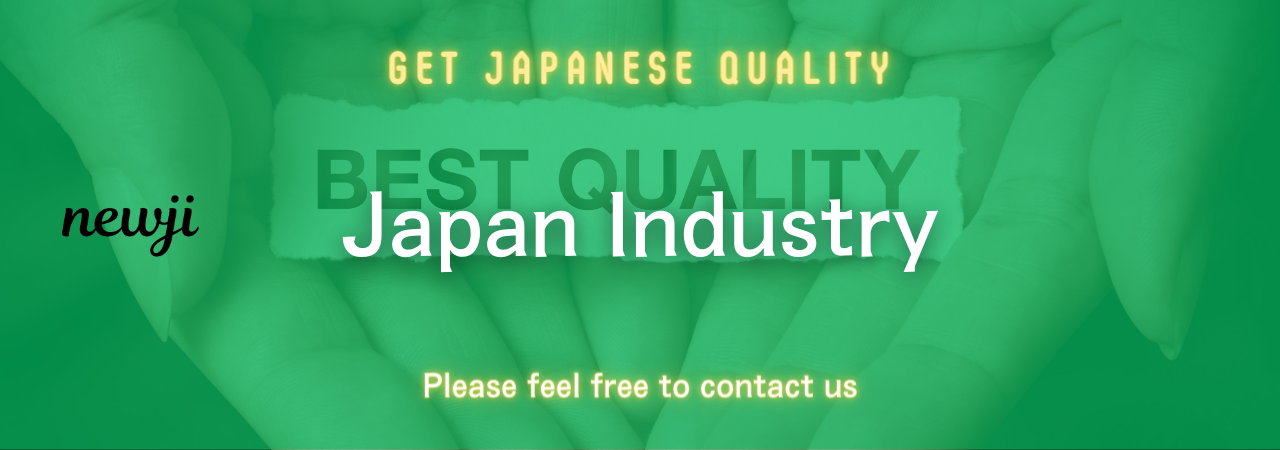
目次
Understanding Quality Standards in Purchasing Contracts
Quality standards are essential components of purchasing contracts that ensure a product or service meets specific requirements before it is accepted.
They provide a benchmark that helps both the buyer and seller understand what is expected from the transaction.
These standards may include specifications regarding materials, dimensions, performance criteria, or compliance with industry standards.
For businesses, developing and implementing quality standards is crucial as it directly affects customer satisfaction and operational efficiency.
Incorporating clear quality standards within purchasing contracts can reduce the chances of disputes and is beneficial in building long-term successful relationships between parties.
Moreover, it helps in maintaining the brand reputation by ensuring consistent product quality over time.
Steps to Develop Quality Standards
Developing quality standards involves several essential steps that ensure clarity and effectiveness.
Identify Requirements
The first step is to clearly identify and define the requirements for the goods or services being procured.
This involves understanding the end-use of the product or service and any necessary specifications that must be met.
Engage with stakeholders, including end-users and technical experts, to gather comprehensive requirements.
Research Industry Standards
Look at existing industry standards and best practices to understand the baseline quality requirements.
These standards often provide a recognized framework that can be tailored to fit the specific needs of your organization.
Reviewing these can also provide insights into mandatory standards you must adhere to, ensuring compliance and reducing risks.
Define the Specific Quality Criteria
Once you understand industry norms and have gathered the requirements, the next step is defining the specific quality criteria.
Set measurable, clear, and achievable standards that the supplier must meet.
These may include precise specifications on the material, construction, functionality, and aesthetic features of the product.
Develop Testing and Inspection Procedures
Create detailed procedures for testing and inspection to evaluate whether the quality standards are met.
These procedures should be consistent and objective, allowing for accurate assessments.
It’s crucial to specify who is responsible for carrying out inspections and how often they should be conducted.
Include Quality Standards in Contracts
Incorporate the developed quality standards into the purchasing contracts.
Ensure these standards are clearly communicated to the supplier, along with any penalties for non-compliance.
Detail the corrective actions in the event of deviations from the agreed-upon quality standards.
Establishing Monitoring Systems
To ensure adherence to established quality standards, setting up robust monitoring systems is essential.
These systems should help track compliance and analyze performance over time.
Regular Supplier Audits
Conduct regular audits of suppliers to verify compliance with quality standards.
Audits provide an opportunity to review processes, identify areas for improvement, and address any non-compliance issues proactively.
Attach importance to both on-site audits and documentation reviews to form a comprehensive assessment.
Use of Technology
Utilize technology to monitor and control quality.
Implement electronic quality management systems (eQMS) to streamline the processes of tracking and analyzing quality performance.
Automation can improve accuracy, efficiency, and consistency in monitoring activities.
Feedback Mechanism
Develop a feedback mechanism to capture insights from stakeholders, including end-users and suppliers, about the quality performance.
Collect and analyze feedback regularly to identify trends and areas of concern.
This information can help you make informed decisions on improvements and realign standards to meet evolving needs.
Performance Metrics
Define and track key performance metrics related to quality.
These might include defect rates, delivery times, and customer satisfaction scores.
Regularly review these metrics to ensure they align with your quality objectives and adjust your strategies accordingly.
Continuous Improvement
Quality management is an ongoing process that requires consistent review and improvement.
Implement a continuous improvement approach to stay proactive and responsive to changes in the market and technology advancements.
Regular Reviews
Schedule regular reviews of quality standards and monitoring systems.
Consider feedback, new regulations, and market dynamics when updating quality standards.
By maintaining flexibility, businesses can adapt to new challenges and continue to meet customer expectations.
Training and Development
Invest in training and development for your employees and suppliers to ensure they understand and can meet the required quality standards.
Regular training sessions help in familiarizing the teams with new technologies, processes, and changes in quality requirements.
Supplier Relationship Management
Develop strong relationships with your suppliers to foster open communication and collaboration.
A good relationship helps in addressing quality issues quickly and reduces the potential for conflict.
Engage in joint problem-solving initiatives with suppliers to drive improvements effectively.
Conclusion
Developing quality standards and monitoring systems in purchasing contracts is crucial for any organization aiming to deliver consistent value.
These processes help ensure that products and services meet desired specifications and contribute to maintaining a positive brand image.
By following a structured approach and focusing on continuous improvement, businesses can minimize risks and optimize their procurement processes effectively.
資料ダウンロード
QCD調達購買管理クラウド「newji」は、調達購買部門で必要なQCD管理全てを備えた、現場特化型兼クラウド型の今世紀最高の購買管理システムとなります。
ユーザー登録
調達購買業務の効率化だけでなく、システムを導入することで、コスト削減や製品・資材のステータス可視化のほか、属人化していた購買情報の共有化による内部不正防止や統制にも役立ちます。
NEWJI DX
製造業に特化したデジタルトランスフォーメーション(DX)の実現を目指す請負開発型のコンサルティングサービスです。AI、iPaaS、および先端の技術を駆使して、製造プロセスの効率化、業務効率化、チームワーク強化、コスト削減、品質向上を実現します。このサービスは、製造業の課題を深く理解し、それに対する最適なデジタルソリューションを提供することで、企業が持続的な成長とイノベーションを達成できるようサポートします。
オンライン講座
製造業、主に購買・調達部門にお勤めの方々に向けた情報を配信しております。
新任の方やベテランの方、管理職を対象とした幅広いコンテンツをご用意しております。
お問い合わせ
コストダウンが利益に直結する術だと理解していても、なかなか前に進めることができない状況。そんな時は、newjiのコストダウン自動化機能で大きく利益貢献しよう!
(Β版非公開)