- お役立ち記事
- Prevent mistakes when selecting suppliers! Risk assessment criteria and their importance
Prevent mistakes when selecting suppliers! Risk assessment criteria and their importance
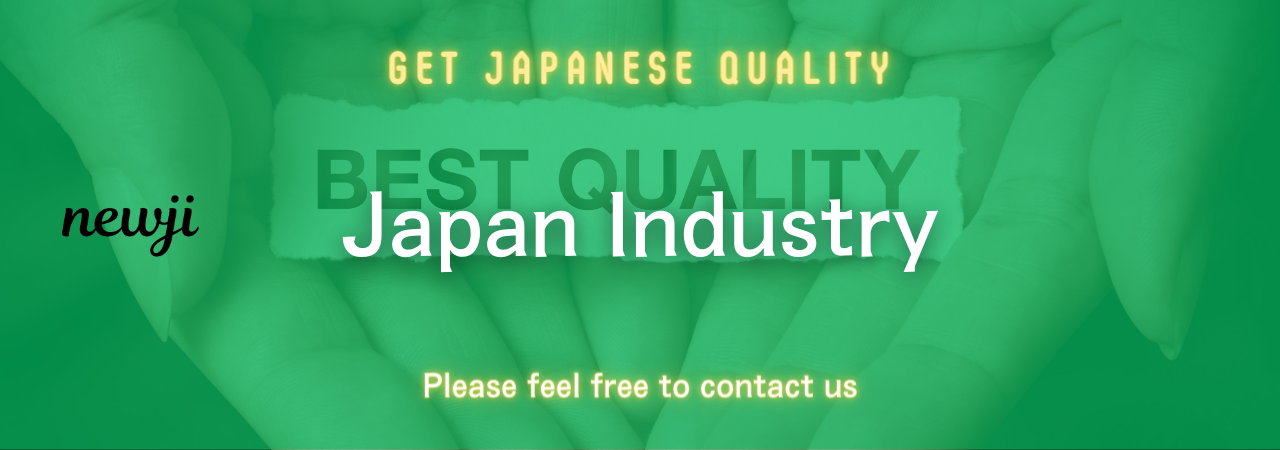
目次
Understanding Supplier Selection
When selecting suppliers, businesses face a critical decision that impacts their operational efficiency and financial success.
Choosing the wrong supplier can lead to numerous challenges, including delays, increased costs, and compromised quality.
Therefore, it is essential to have a systematic approach to evaluate potential suppliers.
This article will explore risk assessment criteria that can prevent mistakes in supplier selection.
The Importance of Risk Assessment
Risk assessment is a vital process that helps businesses identify potential risks and mitigate them effectively.
In the context of supplier selection, risk assessment allows companies to evaluate the reliability and capability of a supplier.
By assessing risks, businesses can avoid potential pitfalls that could impact their supply chain and overall operations.
This process ensures that the company maintains a stable relationship with its suppliers, ensuring uninterrupted production and service delivery.
Key Risk Assessment Criteria for Suppliers
Financial Stability
One of the primary criteria in risk assessment for suppliers is financial stability.
A supplier’s financial health indicates their ability to sustain operations and deliver goods or services consistently.
Before partnering with a supplier, businesses should review their financial statements and credit ratings.
This step helps in understanding the supplier’s financial viability and forecasting any financial risks that may arise.
Quality Assurance
Quality is a non-negotiable aspect when selecting a supplier.
Businesses need assurance that the supplier can meet the required quality standards consistently.
This involves evaluating the supplier’s quality management systems and checking for relevant certifications like ISO standards.
Businesses should request samples or conduct audits to ensure the supplier’s commitment to quality.
Reputation and References
A supplier’s reputation can speak volumes about their reliability and performance.
It’s crucial to check reviews, testimonials, and case studies of past or current clients to gauge satisfaction levels.
Gathering references from other businesses can also provide insight into the supplier’s credibility and trustworthiness.
A strong reputation usually indicates that the supplier is dependable and meets client expectations.
Capacity and Capability
A supplier must have the necessary capacity and capability to meet demand, both now and in the future.
Assessing a supplier’s production capacity will ensure they can deliver the required volume without compromising quality or causing delays.
Evaluating their capability involves understanding their technical expertise, facilities, and resources necessary to produce the goods or services needed.
Delivery and Lead Time
Timely delivery is crucial for maintaining a smooth supply chain.
Businesses must assess a supplier’s ability to meet lead times and deliver products promptly.
Factors to consider include the supplier’s location, shipping methods, and past performance in terms of delivery timelines.
Reliable suppliers should consistently meet deadlines and address any delays proactively.
Compliance and Certification
Compliance with legal and industry standards is vital in supplier selection.
Suppliers should adhere to applicable regulations and possess necessary certifications.
These include environmental, safety, and labor standards, among others.
Ensuring compliance minimizes risks related to legal penalties and protects the company’s brand reputation.
Cost Implications
While cost should not be the only factor, it remains a critical consideration when assessing suppliers.
Businesses need a cost-effective supplier that strikes a balance between price and quality.
Detailed cost analysis allows companies to understand the total cost of ownership, including shipping, customs, and other associated costs.
This helps in negotiating favorable terms that align with the company’s budget.
The Benefits of Thorough Supplier Assessment
Conducting a comprehensive risk assessment enables businesses to make informed decisions when selecting suppliers.
This process reduces the likelihood of errors and ensures collaboration with suppliers that align with organizational goals.
A systematic evaluation of potential risks fosters long-term partnerships, enhancing operational efficiency and profitability.
Enhanced Supply Chain Management
Choosing the right supplier optimizes supply chain management by ensuring that raw materials and products are delivered on time and meet quality standards.
A reliable supplier minimizes interruptions and contributes to a seamless production process, allowing the company to meet customer demands consistently.
Improved Brand Reputation
Partnering with reputable suppliers safeguards the company’s brand reputation by ensuring high-quality products and compliance with regulations.
This is crucial for maintaining customer trust and loyalty, which drives sales and market growth.
Cost Savings and Risk Mitigation
An effective risk assessment helps identify potential pitfalls, allowing businesses to mitigate risks proactively.
This prevents unexpected costs, such as those arising from late deliveries or substandard products.
Choosing a supplier with transparent cost structures and reliable service ultimately leads to significant cost savings.
Conclusion
Incorporating a well-structured risk assessment procedure in supplier selection is essential for businesses aiming to thrive in competitive markets.
By evaluating financial stability, quality assurance, reputation, capability, delivery, compliance, and cost implications, companies can choose the right partners.
This strategic approach not only reduces risks but also supports growth and operational excellence.
資料ダウンロード
QCD調達購買管理クラウド「newji」は、調達購買部門で必要なQCD管理全てを備えた、現場特化型兼クラウド型の今世紀最高の購買管理システムとなります。
ユーザー登録
調達購買業務の効率化だけでなく、システムを導入することで、コスト削減や製品・資材のステータス可視化のほか、属人化していた購買情報の共有化による内部不正防止や統制にも役立ちます。
NEWJI DX
製造業に特化したデジタルトランスフォーメーション(DX)の実現を目指す請負開発型のコンサルティングサービスです。AI、iPaaS、および先端の技術を駆使して、製造プロセスの効率化、業務効率化、チームワーク強化、コスト削減、品質向上を実現します。このサービスは、製造業の課題を深く理解し、それに対する最適なデジタルソリューションを提供することで、企業が持続的な成長とイノベーションを達成できるようサポートします。
オンライン講座
製造業、主に購買・調達部門にお勤めの方々に向けた情報を配信しております。
新任の方やベテランの方、管理職を対象とした幅広いコンテンツをご用意しております。
お問い合わせ
コストダウンが利益に直結する術だと理解していても、なかなか前に進めることができない状況。そんな時は、newjiのコストダウン自動化機能で大きく利益貢献しよう!
(Β版非公開)