- お役立ち記事
- Logistics issues in global procurement that purchasing managers should know and how to deal with them
Logistics issues in global procurement that purchasing managers should know and how to deal with them
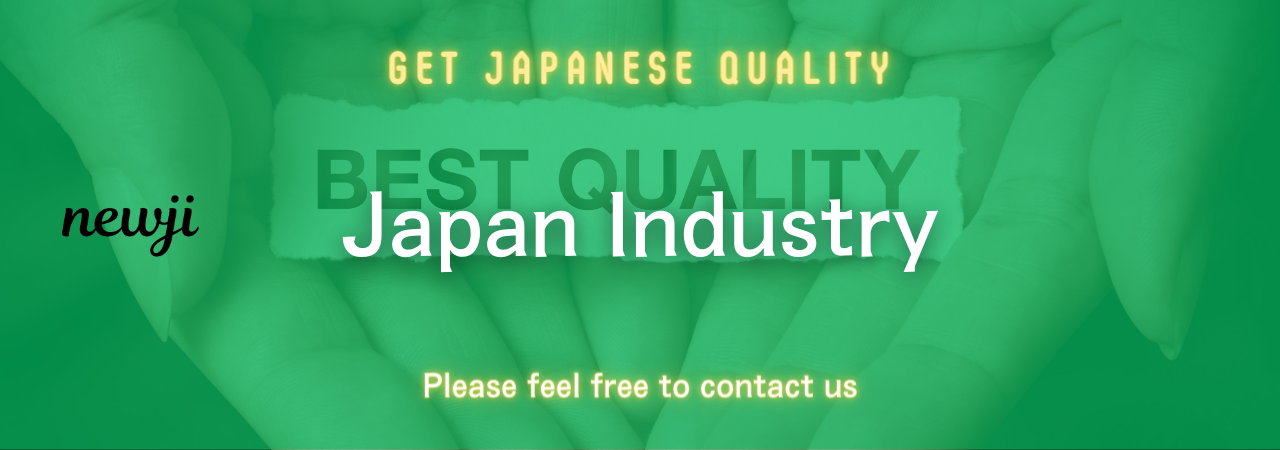
目次
Understanding Global Procurement
The world of global procurement is vast and ever-evolving.
As purchasing managers navigate through this landscape, they encounter numerous challenges.
One of the most critical issues they face is logistics.
Global procurement refers to sourcing materials and services from different parts of the world.
While this approach offers benefits such as cost savings and access to unique products, it also presents logistical complexities.
These complexities can arise due to differences in regulations, geographical barriers, and the coordination needed across multiple time zones.
For anyone involved in global procurement, understanding these challenges and learning to manage them effectively is crucial.
Key Logistics Issues Facing Purchasing Managers
Let’s delve deeper into the significant logistics issues that purchasing managers encounter in global procurement.
Transportation Delays
Transportation delays are one of the most common issues.
Whether it’s due to adverse weather conditions, strikes, or technical failures, goods often take longer to reach their destination.
These delays not only affect supply chains but can also lead to increased costs.
When goods are delayed, companies may have to find quick alternatives or risk disappointing their customers.
Sometimes, the ripple effect of such delays can result in production halts, especially if the delayed goods are critical components.
Customs and Regulatory Compliance
Different countries have varied customs and regulatory requirements.
Purchasing managers must ensure that their shipments comply with all necessary regulations to avoid delays.
Failing to meet these requirements can lead to hefty fines, confiscation of goods, or even legal ramifications.
Understanding the intricacies of international trade laws is paramount.
It involves knowledge about tariffs, documentation, and product labeling requirements.
Ignoring these aspects can result in significant disruptions in the supply chain.
Currency Fluctuations
Global trade means dealing with multiple currencies.
Fluctuations in currency rates can significantly impact the cost of procurement.
A sudden spike in a currency can turn what seemed like a cost-effective purchase into an expensive affair.
Purchasing managers should develop strategies to mitigate the effects of currency fluctuations.
Monitoring currency trends and possibly locking in exchange rates in advance are essential tactics in shielding businesses from unforeseen price hikes.
Supplier Reliability
Sourcing from different parts of the world means dealing with various suppliers, each with its standards and reliability.
Two suppliers in different regions might provide the same product, but the quality and adherence to deadlines can vary vastly.
Purchasing managers should place a premium on building strong relationships with reliable suppliers.
It often involves vetting suppliers thoroughly and periodically evaluating them to ensure they meet the company’s standards.
Strategies to Overcome Logistics Challenges
Managing logistics issues require strategic planning and foresight.
Here are some effective strategies that purchasing managers can adopt:
Leverage Technology
Technology can be a game-changer in managing logistics.
Various tools and software can help track shipments, manage inventory, and predict potential disruptions.
Implementing an advanced supply chain management system can streamline operations, providing real-time data about shipments and potential hurdles.
Using technology to its fullest can give purchasing managers a competitive edge, enabling them to act swiftly when issues arise.
Build Strong Supplier Relationships
As mentioned earlier, having trusted and reliable suppliers is invaluable.
Building strong relationships with suppliers can lead to improved communication and collaboration.
It can also provide leverage in negotiating better terms and quicker turnarounds.
Purchasing managers should ensure that they maintain open lines of communication with their suppliers, sharing their demand forecasts and any potential changes in requirements.
This approach not only reduces misunderstandings but can also pave the way for innovative solutions to overcome logistics challenges.
Optimize Inventory Management
An efficient inventory management strategy can buffer the effects of potential logistics issues.
Purchasing managers should aim to balance having enough stock to meet demand without overstocking.
Strategies like Just-In-Time (JIT) inventory management can reduce the burden of holding excess inventory.
However, managers must weigh the risks associated with JIT, especially when considering potential transportation delays or disruptions.
Risk Management and Contingency Planning
Proactively planning for risks is vital.
Purchasing managers should develop contingency plans that address potential logistics disruptions.
This planning might include diversifying suppliers to avoid over-reliance on a single source or establishing agreements with alternate transportation providers.
By having contingency plans in place, companies can react swiftly and minimize disruptions to their supply chain.
Conclusion
Global procurement offers tremendous opportunities but comes with its set of challenges.
Logistics issues, if not managed correctly, can significantly impact the efficiency and cost-effectiveness of procurement operations.
Purchasing managers should prioritize understanding these challenges and adopt strategies to mitigate their impact.
Leveraging technology, maintaining strong supplier relationships, optimizing inventory, and having robust contingency plans can make a difference.
As the global landscape continues to evolve, staying informed and adaptable will ensure that purchasing managers can navigate the complexities of global procurement with ease and confidence.
By doing so, they can harness the full potential of global sourcing, ensuring seamless operations and satisfied customers.
資料ダウンロード
QCD調達購買管理クラウド「newji」は、調達購買部門で必要なQCD管理全てを備えた、現場特化型兼クラウド型の今世紀最高の購買管理システムとなります。
ユーザー登録
調達購買業務の効率化だけでなく、システムを導入することで、コスト削減や製品・資材のステータス可視化のほか、属人化していた購買情報の共有化による内部不正防止や統制にも役立ちます。
NEWJI DX
製造業に特化したデジタルトランスフォーメーション(DX)の実現を目指す請負開発型のコンサルティングサービスです。AI、iPaaS、および先端の技術を駆使して、製造プロセスの効率化、業務効率化、チームワーク強化、コスト削減、品質向上を実現します。このサービスは、製造業の課題を深く理解し、それに対する最適なデジタルソリューションを提供することで、企業が持続的な成長とイノベーションを達成できるようサポートします。
オンライン講座
製造業、主に購買・調達部門にお勤めの方々に向けた情報を配信しております。
新任の方やベテランの方、管理職を対象とした幅広いコンテンツをご用意しております。
お問い合わせ
コストダウンが利益に直結する術だと理解していても、なかなか前に進めることができない状況。そんな時は、newjiのコストダウン自動化機能で大きく利益貢献しよう!
(Β版非公開)