- お役立ち記事
- Manufacturing process progress management and delivery date countermeasures that purchasing departments should know about
Manufacturing process progress management and delivery date countermeasures that purchasing departments should know about
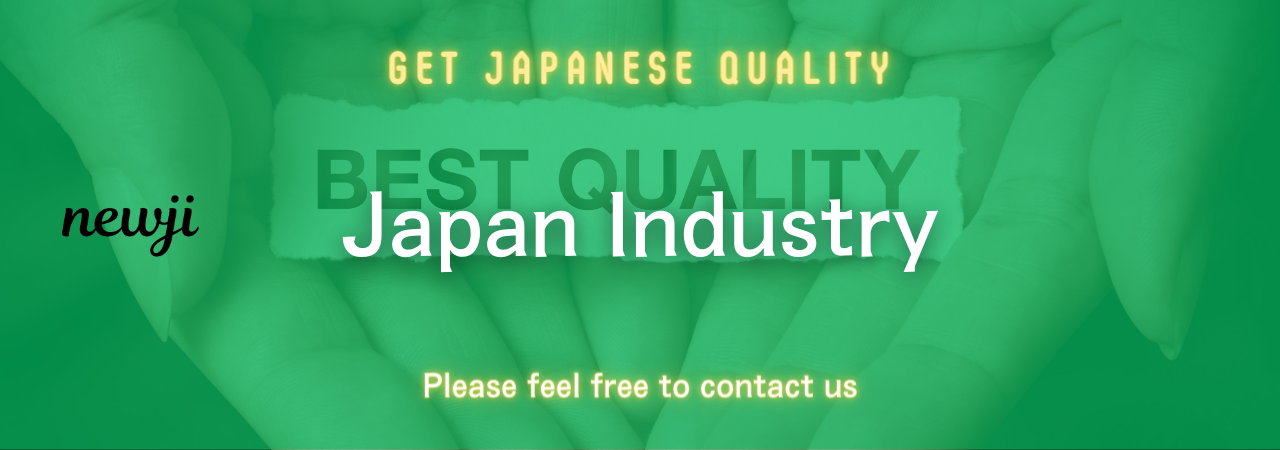
目次
Understanding the Manufacturing Process
In the world of manufacturing, efficiency and timing are everything.
To ensure that products are made correctly and on time, it’s crucial to understand the entire manufacturing process.
This process involves several stages, each of which must be managed effectively to meet deadlines and customer expectations.
From the initial design phase to the final delivery, every step needs careful planning and oversight.
An effective manufacturing process also requires seamless coordination between various departments, especially the production and purchasing teams.
Purchasing departments play a pivotal role in the entire process by procuring the materials needed for production.
Understanding the manufacturing stages can help these departments plan better and prevent potential production delays.
The Importance of Progress Management
Progress management is about keeping track of every stage in the manufacturing process.
It involves monitoring how tasks are completed and ensuring that each step is done according to the set timeline.
By implementing a robust progress management strategy, companies can anticipate bottlenecks and resolve issues before they escalate.
This proactive approach minimizes disruptions, keeps the manufacturing on track, and ensures timely delivery.
For purchasing departments, understanding this concept is vital as it helps them coordinate better with suppliers and manage inventory effectively.
Key Elements of Progress Management
Several key elements contribute to effective progress management, including:
– **Planning and Scheduling**: Detailed planning and scheduling are crucial to ensure that every operation aligns with the overall production timeline.
This involves setting realistic deadlines and allocating resources accordingly.
– **Real-Time Monitoring**: Utilizing technology to monitor progress in real-time helps in identifying any deviations from the plan promptly.
This enables quick corrective actions.
– **Communication and Reporting**: Regular communication between departments and updated reports ensure transparency and aid in decision-making.
It allows all stakeholders to stay informed about the production status.
– **Continuous Improvement**: Regularly revisiting processes and embracing feedback for improvements boosts efficiency and reduces chances of delays.
Delivery Date Countermeasures
Meeting delivery dates is a key performance indicator in the manufacturing industry.
Delays can dent a company’s reputation and lead to financial losses.
By understanding and implementing strategies to manage delivery dates effectively, companies can fulfill their commitments.
Strategies for Managing Delivery Dates
Here are some strategies that purchasing departments should consider:
– **Effective Supplier Management**: Building strong relationships with reliable suppliers is crucial.
This ensures timely delivery of raw materials, which is the first step in meeting production timelines.
– **Inventory Control**: Maintaining optimal inventory levels to mitigate risks of shortage or excess is essential.
Just-in-Time inventory systems can be beneficial in aligning supplier deliveries with production schedules.
– **Risk Management**: Identifying potential risks ahead of time and having contingency plans in place is vital.
This could include having backup suppliers or alternative materials ready if supply chain disruptions occur.
– **Technology Leverage**: Using advanced software solutions for inventory and supply chain management can significantly enhance prediction accuracy and reduce lead times.
Collaboration Between Departments
Collaboration between the purchasing and production departments is critical to ensure the smooth execution of the manufacturing process.
A silo mentality can hinder progress and lead to misunderstandings that impact delivery dates.
Benefits of Cross-Department Collaboration
Effective collaboration includes:
– **Enhanced Communication**: Ensures that all departments are on the same page regarding timelines and expectations.
– **Shared Goals**: Aligning objectives across departments streamlines efforts and boosts overall productivity.
– **Better Problem-Solving**: Cross-departmental brainstorming can lead to innovative solutions for potential challenges.
– **Increased Flexibility**: With shared resources and information, teams can adapt more quickly to changes or unexpected issues.
The Role of Technology in Manufacturing Management
In today’s digital world, technology plays a significant role in managing manufacturing processes efficiently.
From progress tracking to delivery management, leveraging the right technology can transform operations.
Technological Tools to Enhance Efficiency
Some important technological tools include:
– **ERP Systems**: Enterprise Resource Planning systems integrate various functions across the company, providing real-time insights and enabling better decision-making.
– **IoT Devices**: Internet of Things devices can offer real-time updates and predictive analytics, helping anticipate maintenance needs and optimize operations.
– **Automated Scheduling Software**: Helps in planning and adjusting schedules with efficiency, even when facing unforeseen disruptions.
– **Blockchain**: For transparency and traceability in supply chains, validating the authenticity of materials and ensuring compliance with delivery standards.
Conclusion
For purchasing departments, understanding the manufacturing process, implementing robust progress management, and adopting effective delivery countermeasures is essential.
These strategies help ensure the smooth operation of the manufacturing line and timely product delivery.
By fostering collaboration across departments and leveraging technology, companies can navigate complex manufacturing challenges effectively.
This leads to satisfied customers, improved return on investment, and a competitive edge in the market.
With the right tools and strategies, purchasing departments can significantly contribute to the success of the manufacturing process and the fulfillment of delivery commitments.
資料ダウンロード
QCD調達購買管理クラウド「newji」は、調達購買部門で必要なQCD管理全てを備えた、現場特化型兼クラウド型の今世紀最高の購買管理システムとなります。
ユーザー登録
調達購買業務の効率化だけでなく、システムを導入することで、コスト削減や製品・資材のステータス可視化のほか、属人化していた購買情報の共有化による内部不正防止や統制にも役立ちます。
NEWJI DX
製造業に特化したデジタルトランスフォーメーション(DX)の実現を目指す請負開発型のコンサルティングサービスです。AI、iPaaS、および先端の技術を駆使して、製造プロセスの効率化、業務効率化、チームワーク強化、コスト削減、品質向上を実現します。このサービスは、製造業の課題を深く理解し、それに対する最適なデジタルソリューションを提供することで、企業が持続的な成長とイノベーションを達成できるようサポートします。
オンライン講座
製造業、主に購買・調達部門にお勤めの方々に向けた情報を配信しております。
新任の方やベテランの方、管理職を対象とした幅広いコンテンツをご用意しております。
お問い合わせ
コストダウンが利益に直結する術だと理解していても、なかなか前に進めることができない状況。そんな時は、newjiのコストダウン自動化機能で大きく利益貢献しよう!
(Β版非公開)