- お役立ち記事
- How to optimize your supply chain to shorten procurement lead times
How to optimize your supply chain to shorten procurement lead times
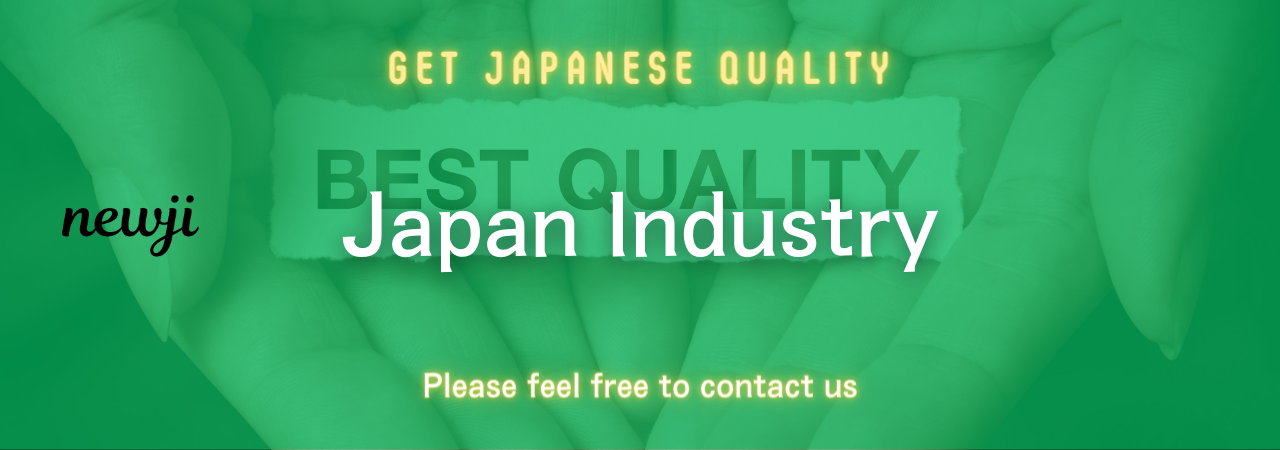
目次
Understanding Procurement Lead Times
Procurement lead time is a critical factor in any supply chain.
It refers to the total time taken from placing an order with a supplier to receiving the goods.
Several stages are involved including order processing, manufacturing or sourcing by the supplier, shipment, and final delivery.
Each stage contributes to the total procurement lead time and offers opportunities for optimization.
Reducing lead times is vital for improving operational efficiency.
This ensures customers receive products in a timely manner, enhancing satisfaction and loyalty.
Let’s explore how you can optimize your supply chain to shorten procurement lead times effectively.
Analyze and Map Out Your Current Supply Chain
Before optimization, it’s crucial to have a comprehensive understanding of your existing supply chain processes.
Start by mapping out each step involved in the procurement process.
Identify stages that are crucial and those that might be redundant or overly complex.
By analyzing your current system, you can identify bottlenecks or inefficiencies causing delays.
Data-driven insights can lead to actionable strategies, reducing overall procurement lead times.
Assess Supplier Performance
Suppliers play an integral role in the supply chain.
Regularly assess their performance to ensure they meet your requirements.
Consider factors such as delivery times, reliability, quality of goods, and communication levels.
If a supplier frequently misses deadlines, it may be time to renegotiate terms or consider alternative options.
Prompt communication with suppliers can help resolve issues quickly and keep your supply chain moving efficiently.
Utilize Technology for Better Forecasting
Incorporating technology offers significant advantages in supply chain management.
Advanced forecasting tools can predict demand more accurately, allowing businesses to plan procurement activities efficiently.
Implementing a robust Enterprise Resource Planning (ERP) system can streamline communications and automate various processes.
Using data analytics can also enhance your understanding of market trends and facilitate more effective inventory management.
Leverage Just-in-Time Inventory
Just-in-time (JIT) inventory is a strategy aimed at reducing waste and increasing efficiency.
This approach involves producing and delivering products only as needed, which can significantly reduce procurement lead times.
While JIT requires precise coordination and excellent communication with suppliers, the benefits include lower inventory costs and minimized risk of obsolescence.
Ensure frequent collaboration and maintain clear communication channels to make JIT inventory work effectively.
Strengthen Vendor Relationships
Building strong relationships with your vendors is essential for supply chain optimization.
Develop partnerships based on trust and collaboration.
Open lines of communication can lead to better arrangements and quicker resolutions to any issues.
Consider implementing vendor-managed inventory (VMI) systems where applicable.
Under VMI, the supplier is responsible for maintaining inventory levels, eliminating the need for constant restocking orders.
This can lead to more predictable lead times and reduce administrative burdens.
Streamline Internal Processes
Internal processes, such as order approval and payment, can also contribute to procurement lead times.
Streamline these processes to ensure efficiency.
Automate routine tasks where possible to reduce the manual workload and minimize the risk of errors.
Establish clear guidelines and responsibilities within your team to expedite decision-making and approvals.
Focus on Continuous Improvement
Optimization is not a one-time effort but an ongoing process.
Continuously monitor key performance indicators (KPIs) related to lead times, and be open to implementing changes based on findings.
Encourage feedback from your team and suppliers.
Identify areas of potential improvement, and experiment with innovative solutions.
Regular training and development will ensure your team remains knowledgeable about industry best practices and new technologies.
Enhance Logistics and Transportation
Efficient logistics and transportation are pivotal in reducing procurement lead times.
Evaluate your current logistics providers to ensure they can meet your needs.
Consider multiple modes of transportation and select the most efficient based on cost, reliability, and lead time.
Employ route optimization software to expedite delivery times and improve overall efficiency.
Risk Management and Contingency Planning
Disruptions in the supply chain are inevitable.
Prepare for unexpected events by developing a robust risk management plan.
Identify potential risks, such as supplier failures or transportation delays, and create contingency plans for these scenarios.
Having an alternative supplier network or safety stock can mitigate risks and ensure your supply chain remains nimble and responsive.
Conclusion
Optimizing your supply chain to shorten procurement lead times is an ongoing journey.
By analyzing current processes, leveraging technology, and fostering strong supplier relationships, significant improvements can be achieved.
Streamlining internal processes and focusing on logistics will further enhance efficiency.
Commit to continuous improvement, addressing any areas of concern promptly, and staying informed about industry trends.
With a strategic approach, your supply chain can become a competitive advantage, catering to customer demands swiftly and effectively.
資料ダウンロード
QCD調達購買管理クラウド「newji」は、調達購買部門で必要なQCD管理全てを備えた、現場特化型兼クラウド型の今世紀最高の購買管理システムとなります。
ユーザー登録
調達購買業務の効率化だけでなく、システムを導入することで、コスト削減や製品・資材のステータス可視化のほか、属人化していた購買情報の共有化による内部不正防止や統制にも役立ちます。
NEWJI DX
製造業に特化したデジタルトランスフォーメーション(DX)の実現を目指す請負開発型のコンサルティングサービスです。AI、iPaaS、および先端の技術を駆使して、製造プロセスの効率化、業務効率化、チームワーク強化、コスト削減、品質向上を実現します。このサービスは、製造業の課題を深く理解し、それに対する最適なデジタルソリューションを提供することで、企業が持続的な成長とイノベーションを達成できるようサポートします。
オンライン講座
製造業、主に購買・調達部門にお勤めの方々に向けた情報を配信しております。
新任の方やベテランの方、管理職を対象とした幅広いコンテンツをご用意しております。
お問い合わせ
コストダウンが利益に直結する術だと理解していても、なかなか前に進めることができない状況。そんな時は、newjiのコストダウン自動化機能で大きく利益貢献しよう!
(Β版非公開)