- お役立ち記事
- Concept of optimizing inventory management in the purchasing department, which is directly connected to the production process
Concept of optimizing inventory management in the purchasing department, which is directly connected to the production process
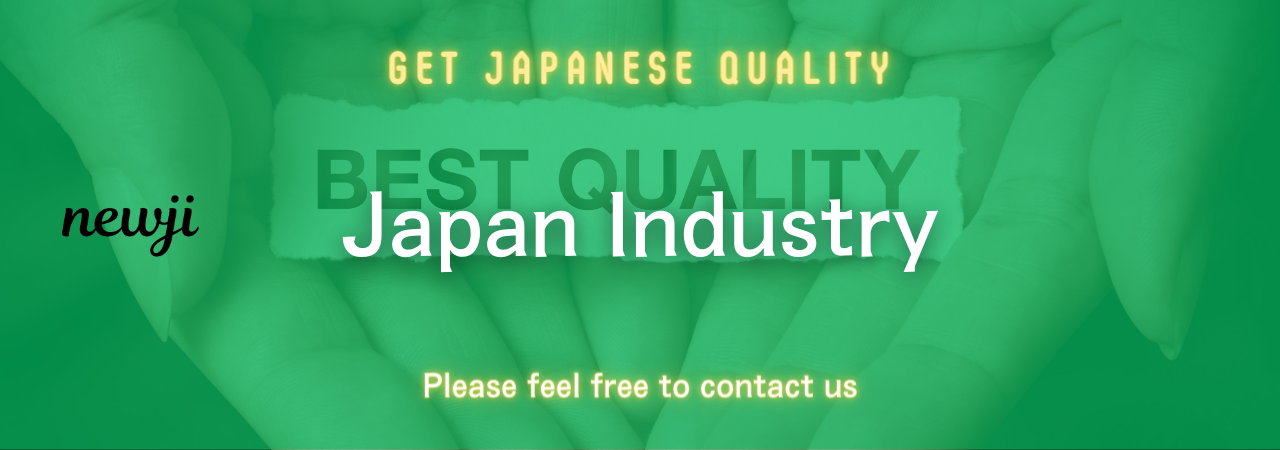
目次
Understanding Inventory Management
Inventory management is a critical function within the purchasing department of any organization, particularly those directly connected to the production process.
It involves the planning, organizing, and controlling of all inventory activities to ensure that production runs smoothly, costs are minimized, and customer demands are met effectively.
At its core, inventory management ensures that the right amount of stock is available at the right time and place, keeping production lines running without interruption.
The success of inventory management hinges on striking a delicate balance between overstocking, which can tie up capital and increase storage costs, and understocking, which can lead to production delays and customer dissatisfaction.
Importance of Inventory Management in the Production Process
Effective inventory management is crucial for maintaining the seamless flow of materials from suppliers to the production floor.
It plays a vital role in enabling organizations to respond promptly to changes in market demand, thereby enhancing their competitive edge.
Mismanagement in this area can result in significant financial losses and operational bottlenecks.
In the context of production, inventory management facilitates the availability of critical components and raw materials.
This ensures there is no disruption in the manufacturing cycles, thereby optimizing productivity and maintaining a steady pace that aligns with production schedules.
Challenges in Inventory Management
While inventory management is crucial, it comes with its set of challenges.
These include demand forecasting inaccuracies, lead time variability, and the complexity of dealing with a wide variety of products and suppliers.
Balancing these factors with efficient use of space, cost constraints, and avoiding obsolescence adds to the intricacy of inventory management.
Another significant challenge is the integration of inventory systems with other departments like logistics, sales, and production planning.
This integration is necessary for maintaining an up-to-date status of all inventory levels and avoids miscommunication across departments.
Demand Forecasting
Accurate demand forecasting is a cornerstone of successful inventory management.
It requires analyzing past sales data, market trends, and consumer behavior to predict future product demand.
Mistakes in forecasting can lead to overproduction or stockouts, impacting the production process directly.
Companies often invest in sophisticated software and analytical tools to improve the precision of demand forecasts.
This investment helps in reducing the margin of error and contributes to maintaining optimal inventory levels.
Lead Time Management
Lead time, the time taken from placing an order to receiving it, is another crucial factor in inventory management.
Variations in lead time can disrupt the production schedule, especially if the procurement process is not synchronized properly with production needs.
To minimize issues related to lead time, businesses often work closely with suppliers, establish safety stock levels, and optimize reorder points to ensure inventory availability.
Optimizing Inventory Management
Optimization of inventory management involves employing strategies and practices that streamline operations and improve efficiency.
One common approach is the Just-In-Time (JIT) inventory system, where materials are ordered and received only as needed in the production process.
This method significantly reduces holding costs and requires precise coordination with suppliers but can be risky if not implemented correctly.
Technology Integration
Integrating technology into inventory management processes can greatly enhance efficiency.
Advanced inventory management systems provide real-time data on stock levels, facilitate automated reordering, and enable seamless communication across various departments.
Furthermore, technologies like RFID and IoT devices can offer precise tracking and monitoring of inventory, leading to better decision-making and resource allocation.
Supplier Relationship Management
Building strong relationships with suppliers is essential for optimizing inventory management.
This involves working collaboratively to ensure timely deliveries, negotiating favorable terms, and even sharing demand forecasts.
These partnerships can lead to joint planning initiatives, further aligning inventory levels with production requirements while reducing variability in supply.
Employee Training and Development
Training and developing the skills of employees involved in inventory management can have a huge impact on the optimization process.
Well-trained staff can better handle inventory-related challenges, anticipate potential issues, and implement effective solutions.
Investments in regular training programs and workshops keep employees updated with the latest industry practices and technological advancements.
Conclusion
Optimizing inventory management in the purchasing department is a strategic imperative for any organization, especially those directly tied to production processes.
By addressing challenges like demand forecasting, lead time management, and technology integration, companies can ensure their inventory systems support rather than hinder the production cycle.
Efficiency in inventory management not only cuts costs but also enhances the organization’s ability to serve its customers promptly and reliably.
In this dynamic market where demands fluctuate continuously, a streamlined inventory management system becomes a significant competitive advantage.
資料ダウンロード
QCD調達購買管理クラウド「newji」は、調達購買部門で必要なQCD管理全てを備えた、現場特化型兼クラウド型の今世紀最高の購買管理システムとなります。
ユーザー登録
調達購買業務の効率化だけでなく、システムを導入することで、コスト削減や製品・資材のステータス可視化のほか、属人化していた購買情報の共有化による内部不正防止や統制にも役立ちます。
NEWJI DX
製造業に特化したデジタルトランスフォーメーション(DX)の実現を目指す請負開発型のコンサルティングサービスです。AI、iPaaS、および先端の技術を駆使して、製造プロセスの効率化、業務効率化、チームワーク強化、コスト削減、品質向上を実現します。このサービスは、製造業の課題を深く理解し、それに対する最適なデジタルソリューションを提供することで、企業が持続的な成長とイノベーションを達成できるようサポートします。
オンライン講座
製造業、主に購買・調達部門にお勤めの方々に向けた情報を配信しております。
新任の方やベテランの方、管理職を対象とした幅広いコンテンツをご用意しております。
お問い合わせ
コストダウンが利益に直結する術だと理解していても、なかなか前に進めることができない状況。そんな時は、newjiのコストダウン自動化機能で大きく利益貢献しよう!
(Β版非公開)