- お役立ち記事
- Purchasing department screening method to find suppliers capable of short delivery times
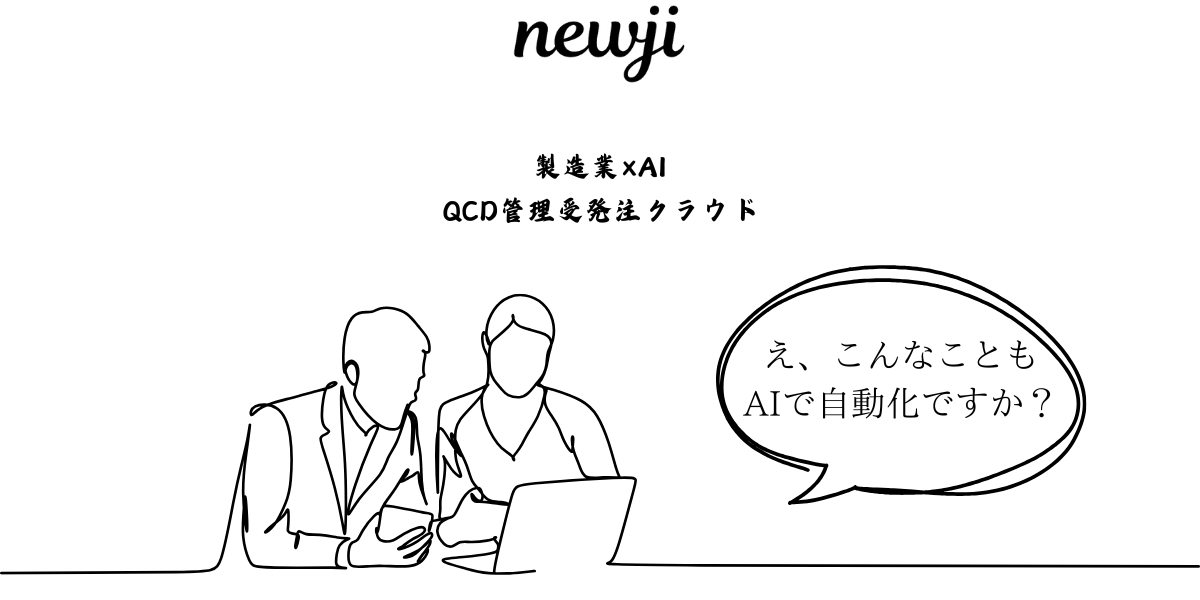
Purchasing department screening method to find suppliers capable of short delivery times
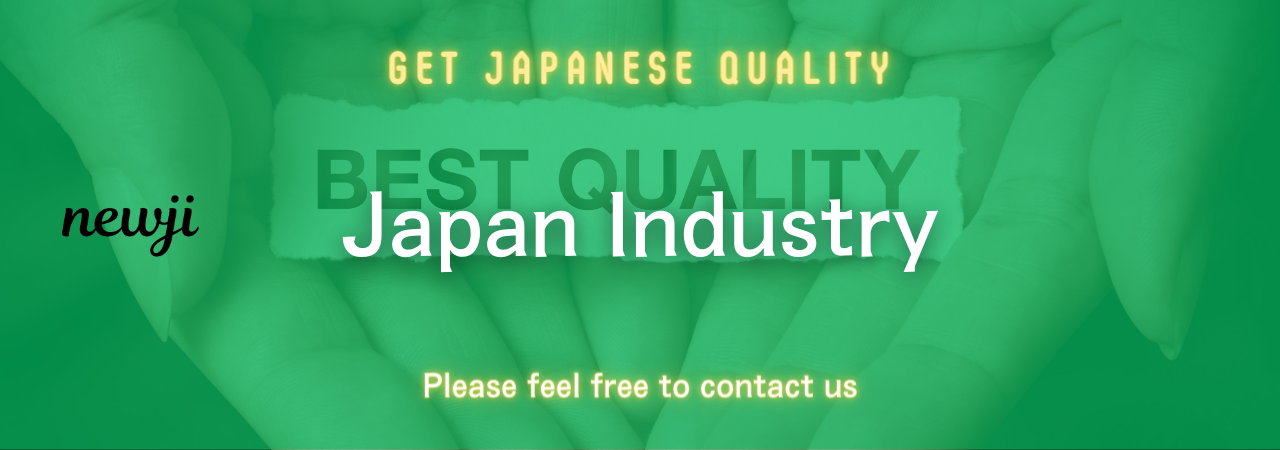
目次
Understanding the Importance of Supplier Selection
Selecting the right suppliers is crucial for any purchasing department aiming to guarantee short delivery times.
A dependable supplier can ensure that goods are delivered on time, which is vital for maintaining smooth operations and meeting customer expectations.
A thorough analysis and screening of potential suppliers are necessary to identify those capable of meeting stringent delivery schedules.
By doing so, businesses can enhance their operational efficiency and improve their overall service delivery.
Factors to Consider When Choosing Suppliers
When screening for potential suppliers, there are several key factors that need consideration.
Evaluating these factors can help in determining the suppliers best suited to meet the company’s delivery expectations.
1. Supplier’s Delivery Performance
A supplier’s past delivery performance is a strong indicator of their ability to meet delivery deadlines.
Checking references and looking into historical data about their delivery times can provide insights into their reliability.
Suppliers with a consistent track record of on-time deliveries should be prioritized over those with frequent delays.
2. Supplier’s Capacity and Resources
The capacity and resources of a supplier play a crucial role in their ability to meet your short delivery timelines.
Understanding their manufacturing capacities, inventory levels, and resource allocation can give a clear picture of how they might handle your order volume and frequency.
Suppliers with ample resources and a well-managed workflow are better equipped to ensure timely deliveries.
3. Flexibility and Scalability
A supplier’s flexibility and ability to scale operations when required can be vital for meeting urgent delivery demands.
In times of fluctuating demand, having suppliers who can adjust and deliver effectively without compromising quality is essential.
Assess the supplier’s ability to ramp up operations in response to sudden increases in demand or emergency situations.
4. Communication and Reliability
Efficient communication is essential for ensuring that operations run smoothly.
Assess the supplier’s responsiveness and willingness to keep you informed about the status of your orders.
Reliable suppliers maintain transparent channels of communication and provide timely updates.
5. Geographic Proximity
The geographic location of a supplier can impact delivery times.
Suppliers situated closer to your business location generally mean shorter transit times and lower shipping costs.
Consider proximity when prioritizing potential suppliers, as this can have a significant effect on meeting tight delivery schedules.
6. Technological Integration
With technological advancements, many suppliers now employ sophisticated systems to oversee production and inventory management.
Suppliers utilizing technology such as Enterprise Resource Planning (ERP) systems or real-time tracking solutions might offer more reliable and efficient delivery times.
Such technology can facilitate better alignment with your own business systems and enhance overall supply chain efficiency.
The Screening Process
Once you have identified potential suppliers, it is essential to conduct a well-structured screening process.
This can involve multiple steps and assessment techniques to ensure you select the most suitable supplier for your needs.
Develop a Supplier Evaluation Framework
Create a standardized framework that involves all the criteria that are important to your organization.
This might include delivery performance metrics, flexibility scores, and assessments of financial stability.
Having a consistent evaluation method allows for a fair comparison among different suppliers.
Request for Proposal (RFP) or Request for Quotation (RFQ)
Use RFPs or RFQs to gather formal proposals or quotations from potential suppliers.
Such requests should be detailed, setting out all expectations regarding delivery times and service quality.
Analyze the responses carefully, paying close attention to delivery schedules, pricing, and any additional terms offered.
Site Visits and Audits
Conducting site visits or audits can provide a firsthand look into the supplier’s operations and capabilities.
Observing the facilities can reveal how efficiently they manage production, quality control, and logistics.
These visits can also offer insights into their management style and company culture, which can impact their reliability.
Trial Orders
Implement trial orders with potential suppliers to gauge their performance in real-world scenarios.
Use these orders to assess delivery punctuality, quality consistency, and communication responsiveness.
Trial orders are an effective way to ascertain if a supplier matches up to their claims.
Building Collaborative Supplier Relationships
Once you have selected suitable suppliers, ongoing collaboration and relationship management are essential.
Establish clear communication lines and work closely with suppliers to address any issues promptly.
Establish performance metrics and review them regularly to maintain high standards of delivery.
Conclusion
Selecting suppliers capable of short delivery times demands a thorough and systematic screening process.
By focusing on delivery performance, capacity, flexibility, and communication, you can identify suppliers best suited to meet your needs.
Implementing a rigorous screening and evaluation method ensures operational efficiency and helps your business meet its objectives.
Always remember, fostering strong supplier relationships is key to maintaining consistent delivery performance and aiding long-term business success.
資料ダウンロード
QCD調達購買管理クラウド「newji」は、調達購買部門で必要なQCD管理全てを備えた、現場特化型兼クラウド型の今世紀最高の購買管理システムとなります。
ユーザー登録
調達購買業務の効率化だけでなく、システムを導入することで、コスト削減や製品・資材のステータス可視化のほか、属人化していた購買情報の共有化による内部不正防止や統制にも役立ちます。
NEWJI DX
製造業に特化したデジタルトランスフォーメーション(DX)の実現を目指す請負開発型のコンサルティングサービスです。AI、iPaaS、および先端の技術を駆使して、製造プロセスの効率化、業務効率化、チームワーク強化、コスト削減、品質向上を実現します。このサービスは、製造業の課題を深く理解し、それに対する最適なデジタルソリューションを提供することで、企業が持続的な成長とイノベーションを達成できるようサポートします。
オンライン講座
製造業、主に購買・調達部門にお勤めの方々に向けた情報を配信しております。
新任の方やベテランの方、管理職を対象とした幅広いコンテンツをご用意しております。
お問い合わせ
コストダウンが利益に直結する術だと理解していても、なかなか前に進めることができない状況。そんな時は、newjiのコストダウン自動化機能で大きく利益貢献しよう!
(Β版非公開)