- お役立ち記事
- How to proceed with joint development with suppliers necessary to improve the quality of procured products
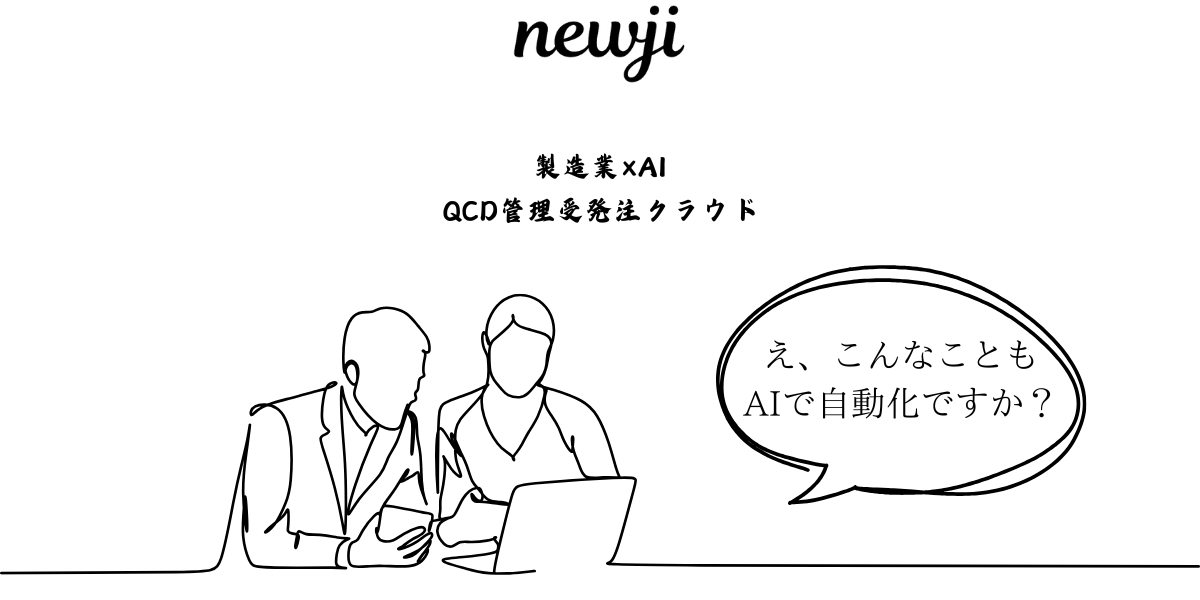
How to proceed with joint development with suppliers necessary to improve the quality of procured products
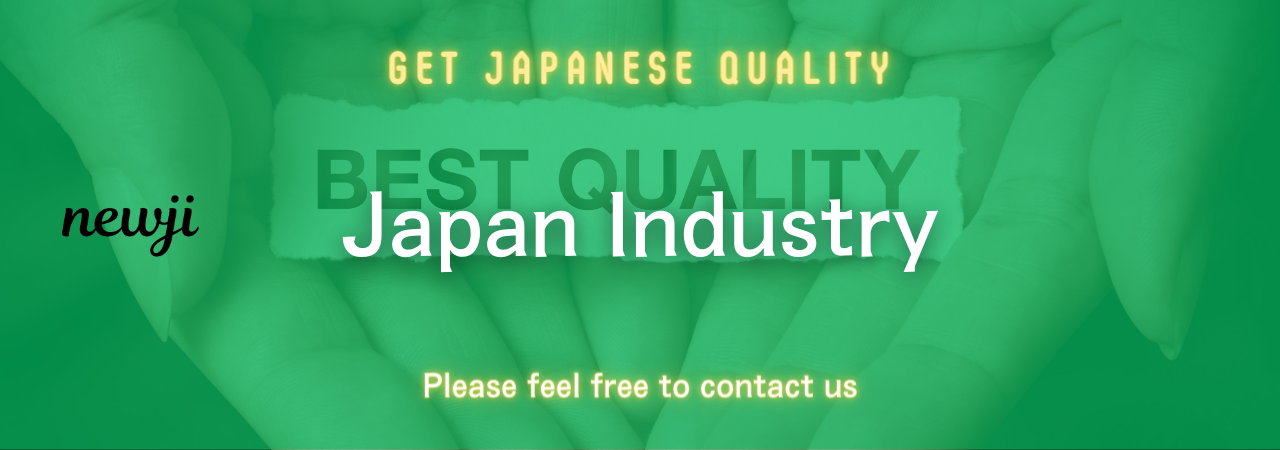
目次
Understanding Joint Development
Joint development involves collaboration between a company and its suppliers to improve the quality of procured products.
This approach ensures that all parties contribute their expertise, resources, and insights to create a product that meets or exceeds quality standards.
By working together, companies and suppliers can share risks and rewards, foster innovation, and streamline processes.
The Importance of Clear Communication
Clear communication is a cornerstone of successful joint development.
Both parties must clearly articulate their objectives, expectations, and timelines.
Regular meetings and open communication channels help to address potential issues early on.
It is crucial that everyone involved is on the same page to minimize misunderstandings and ensure that the project progresses smoothly.
Establishing a shared platform for communication can further facilitate information exchange.
Setting Joint Development Goals
Before beginning a joint development project, it is essential to establish specific, measurable, attainable, relevant, and time-bound (SMART) goals.
These goals should align with the overall business objectives of both the company and the supplier.
By setting clear goals, both parties can remain focused and accountable, and monitor progress effectively.
Including milestones and key performance indicators (KPIs) in the goals can also help in tracking developments.
Building Trust and Collaborative Relationships
Trust is fundamental in any collaboration with suppliers.
Creating a relationship based on mutual respect and transparency encourages open dialogue and cooperation.
One way to build trust is by demonstrating a long-term commitment to the partnership.
This includes honoring agreements, delivering on promises, and ensuring that both parties benefit from the collaboration.
Regular face-to-face meetings, site visits, and collaborative workshops can strengthen the partnership further.
Selecting the Right Supplier
Not every supplier is suitable for joint development projects.
It is crucial to select a supplier that shares the company’s quality standards, values, and vision.
Conducting a thorough evaluation of potential suppliers is essential to finding the right fit for a joint development project.
Assess the supplier’s technical capabilities, experience, and resources.
Additionally, consider their track record in terms of quality, innovation, and responsiveness.
Defining Roles and Responsibilities
Clearly defining roles and responsibilities is vital for the success of joint development projects.
This includes specifying who is responsible for what tasks, and ensuring that both teams understand their individual and collective responsibilities.
By delineating roles, companies and suppliers can avoid duplication of efforts, minimize conflicts, and enhance the team’s efficiency.
Developing a detailed project plan can serve as a guide and reference throughout the joint development process.
Resource Allocation and Risk Management
Joint development requires adequate allocation of resources including personnel, technology, and finances.
Both the company and the supplier must be willing to invest the necessary resources to achieve desired outcomes.
Effective resource management enables projects to stay on schedule and within budget.
Additionally, establishing a risk management strategy is indispensable.
Identify potential risks, assess their impact, and devise mitigation plans to address uncertainties.
This proactive approach minimizes disruptions and ensures project continuity.
Leveraging Technology and Innovation
Utilizing technology can greatly enhance the joint development process.
From design software to virtual collaboration platforms, technology enables teams to work efficiently and effectively.
Investing in innovative tools and techniques can also lead to improved product quality and faster project completion times.
Moreover, fostering a culture of innovation among both teams encourages creative solutions and continuous improvement.
Monitoring Progress and Performance
Constant monitoring of progress and performance is key to ensuring that joint development projects stay on track.
Regular assessments help identify areas of improvement and measure success against established goals and KPIs.
Both parties should participate in reviewing progress and addressing any issues that arise.
Utilizing a project management tool can simplify the tracking and reporting process.
Continuous Improvement and Feedback Loops
The journey of joint development does not end with the launch of a product.
Continuous improvement is essential for long-term success.
Both the company and supplier should establish feedback loops to gather input from customers and stakeholders.
Analyzing feedback can reveal valuable insights that inform future projects and foster further innovation.
Encouraging open dialogue and learning from past experiences contribute to stronger, more successful collaborations moving forward.
The Benefits of Joint Development
There are numerous advantages to engaging in joint development with suppliers.
Collaborative projects often result in higher-quality products due to combined expertise and resources.
This approach also facilitates faster time-to-market, as development processes are streamlined.
Additionally, companies can gain valuable insights into supplier capabilities and processes, leading to better decision-making in future collaborations.
Last but not least, joint development strengthens the relationship between companies and suppliers, paving the way for long-term success and mutual benefits.
Joint development is a powerful strategy that can significantly improve the quality of procured products.
By fostering a collaborative environment, focusing on communication, and embracing a shared commitment to success, companies and suppliers can achieve great outcomes together.
This synergy not only enhances product quality but also builds lasting partnerships that contribute to business growth and innovation.
資料ダウンロード
QCD調達購買管理クラウド「newji」は、調達購買部門で必要なQCD管理全てを備えた、現場特化型兼クラウド型の今世紀最高の購買管理システムとなります。
ユーザー登録
調達購買業務の効率化だけでなく、システムを導入することで、コスト削減や製品・資材のステータス可視化のほか、属人化していた購買情報の共有化による内部不正防止や統制にも役立ちます。
NEWJI DX
製造業に特化したデジタルトランスフォーメーション(DX)の実現を目指す請負開発型のコンサルティングサービスです。AI、iPaaS、および先端の技術を駆使して、製造プロセスの効率化、業務効率化、チームワーク強化、コスト削減、品質向上を実現します。このサービスは、製造業の課題を深く理解し、それに対する最適なデジタルソリューションを提供することで、企業が持続的な成長とイノベーションを達成できるようサポートします。
オンライン講座
製造業、主に購買・調達部門にお勤めの方々に向けた情報を配信しております。
新任の方やベテランの方、管理職を対象とした幅広いコンテンツをご用意しております。
お問い合わせ
コストダウンが利益に直結する術だと理解していても、なかなか前に進めることができない状況。そんな時は、newjiのコストダウン自動化機能で大きく利益貢献しよう!
(Β版非公開)