- お役立ち記事
- Unlocking the Power of Zinc in Japanese Manufacturing: Innovations and Global Impact
Unlocking the Power of Zinc in Japanese Manufacturing: Innovations and Global Impact
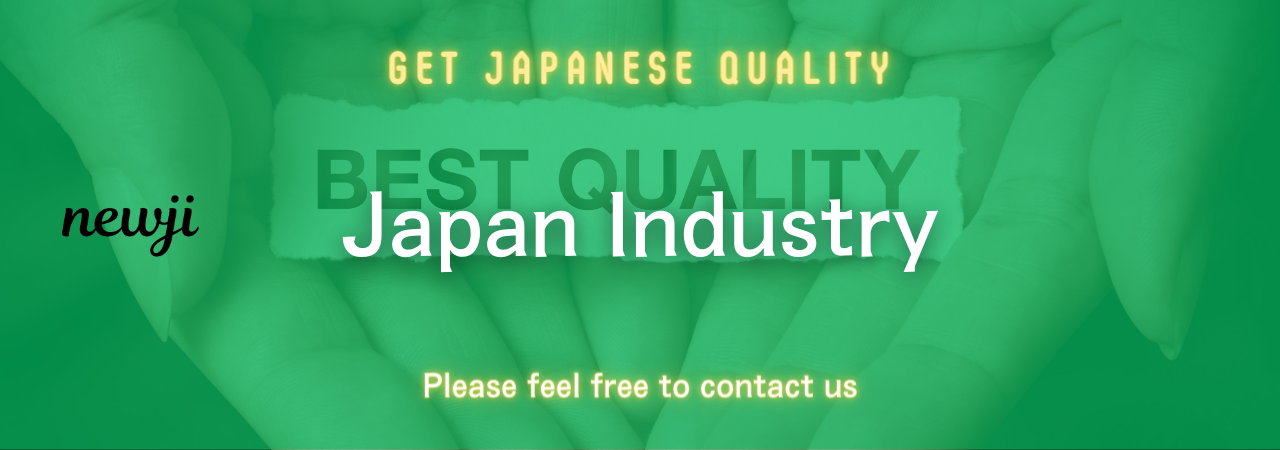
目次
Introduction to Zinc in Japanese Manufacturing
Zinc plays a pivotal role in the manufacturing sector, particularly within Japan’s industrial landscape.
As a versatile metal, zinc is essential in various applications, ranging from corrosion protection to electronics.
Japanese manufacturers have harnessed the unique properties of zinc to drive innovation and maintain a competitive edge in global markets.
This article delves into the significance of zinc in Japanese manufacturing, exploring the advancements, procurement strategies, and the broader global impact.
Overview of Zinc in Japanese Manufacturing
Zinc is integral to numerous manufacturing processes in Japan.
Its primary use in galvanization protects steel and iron from corrosion, ensuring longevity and durability in products.
Beyond galvanization, zinc is employed in die-casting for automotive parts, electronics, and consumer goods.
The metal’s ability to form alloys, such as brass and bronze, further expands its applicability across different industries.
Historical Context
Japan’s manufacturing prowess has long been associated with precision and quality.
Zinc has been a cornerstone in achieving these standards, particularly in the post-war industrial boom.
The integration of zinc in manufacturing processes has contributed to Japan’s reputation for producing reliable and long-lasting products.
Key Industries Utilizing Zinc
Several key industries in Japan rely heavily on zinc.
The automotive industry uses zinc in engine components and body parts to prevent rust.
The electronics sector incorporates zinc in circuit boards and connectors due to its excellent conductive properties.
Additionally, the construction industry benefits from zinc’s durability in roofing and cladding materials.
Innovations in Zinc Processing and Application
Japanese manufacturers are at the forefront of zinc processing technologies, driving efficiency and enhancing product quality.
Advancements in electroplating techniques, for instance, have improved the uniformity and adherence of zinc coatings.
Moreover, innovations in alloy development have led to zinc-based materials with superior mechanical properties, expanding their use in high-performance applications.
Advanced Galvanization Techniques
Traditional galvanization methods are being refined to reduce environmental impact and improve coating performance.
Japanese companies have developed more energy-efficient processes that minimize waste and increase the lifespan of zinc coatings.
These advancements not only enhance product quality but also align with global sustainability goals.
Zinc Alloy Development
Research into zinc alloys has resulted in materials that offer better strength-to-weight ratios and enhanced corrosion resistance.
These alloys are particularly valuable in the automotive and aerospace industries, where performance and reliability are paramount.
The ability to tailor zinc alloys for specific applications exemplifies Japanese innovation in materials science.
Global Impact of Japanese Zinc Manufacturing
Japan’s expertise in zinc manufacturing has significant implications on the global stage.
Japanese zinc products are renowned for their quality, reliability, and adherence to international standards.
This reputation has positioned Japan as a key supplier in the global zinc market, influencing pricing, availability, and technological trends.
Export Dynamics
Japanese manufacturers export a substantial volume of zinc products worldwide, catering to diverse industries.
The export of high-quality zinc-coated materials supports infrastructure projects and industrial developments globally.
Japan’s stringent quality control measures ensure that exported zinc products meet the rigorous demands of international markets.
Technological Leadership
Japan’s advancements in zinc processing technologies set benchmarks that other countries often follow.
Collaborations and partnerships with international firms facilitate the transfer of knowledge and promote global standards.
This technological leadership fosters innovation and drives the global zinc manufacturing industry forward.
Procurement and Purchasing in the Zinc Supply Chain
Effective procurement and purchasing strategies are crucial in the zinc supply chain, ensuring the reliability and cost-effectiveness of operations.
Japanese manufacturers employ sophisticated techniques to secure high-quality zinc at competitive prices, maintaining their manufacturing excellence.
Advantages of Japanese Zinc Procurement
Japanese procurement practices emphasize quality, reliability, and long-term partnerships.
By fostering strong relationships with suppliers, Japanese manufacturers benefit from consistent supply and preferential pricing.
Additionally, the focus on continuous improvement ensures that procurement processes remain efficient and responsive to market changes.
Disadvantages and Challenges
Despite the strengths, there are challenges in the zinc procurement process.
Fluctuations in global zinc prices can impact cost predictability.
Moreover, dependence on specific suppliers may pose risks related to supply chain disruptions or geopolitical tensions.
Addressing these challenges requires strategic diversification and robust risk management practices.
Supplier Negotiation Techniques
Japanese manufacturers adopt collaborative negotiation techniques, aiming for win-win outcomes.
Emphasis is placed on building trust and mutual respect, which facilitates smoother negotiations and stronger supplier relationships.
Techniques such as long-term contracts, volume commitments, and shared benefits models are commonly employed to secure favorable terms.
Market Conditions and Trends
Understanding market conditions is essential for effective procurement.
Japanese manufacturers closely monitor global zinc supply and demand dynamics, price trends, and technological developments.
Staying informed about market trends enables proactive decision-making, helping companies anticipate changes and adjust their strategies accordingly.
Best Practices in Zinc Procurement and Purchasing
Adopting best practices in procurement and purchasing can significantly enhance the efficiency and effectiveness of the zinc supply chain.
Japanese manufacturers exemplify these practices through their commitment to quality, innovation, and collaboration.
Strategic Supplier Relationships
Building strategic relationships with key suppliers ensures a reliable supply of high-quality zinc.
These partnerships often involve collaborative planning, joint development initiatives, and shared risk management strategies.
Such relationships contribute to mutual growth and stability in the supply chain.
Integrated Supply Chain Management
Integrating various stages of the supply chain—from procurement to production and distribution—enhances visibility and coordination.
Advanced information systems and real-time data sharing enable Japanese manufacturers to optimize inventory levels, reduce lead times, and respond swiftly to market changes.
Emphasis on Sustainability
Sustainable procurement practices are increasingly important in the zinc supply chain.
Japanese manufacturers prioritize sourcing zinc from environmentally responsible suppliers and adopting eco-friendly processing methods.
This commitment to sustainability not only meets regulatory requirements but also aligns with the values of modern consumers and stakeholders.
Continuous Improvement and Innovation
A culture of continuous improvement drives innovation in procurement and purchasing.
Japanese manufacturers regularly assess and refine their procurement processes, seeking ways to enhance efficiency, reduce costs, and improve quality.
Investments in technology and training further support ongoing advancements in procurement practices.
Case Studies: Japanese Manufacturers Excelling in Zinc Utilization
Examining specific case studies highlights how Japanese manufacturers effectively leverage zinc for competitive advantage.
Toyota’s Automotive Innovations
Toyota incorporates advanced zinc alloys in its vehicle components to enhance durability and performance.
By utilizing high-strength zinc materials, Toyota achieves lighter and more fuel-efficient vehicles without compromising quality.
This approach not only meets consumer demands but also adheres to stringent environmental standards.
Panasonic’s Electronics Manufacturing
Panasonic employs zinc in various electronic components, benefiting from its excellent conductive and thermal properties.
The company’s focus on precision and quality ensures that zinc-based components meet the high reliability standards of the electronics industry.
Innovations in zinc processing have enabled Panasonic to develop cutting-edge electronic devices with enhanced performance.
Hitachi’s Industrial Applications
Hitachi utilizes zinc in industrial machinery and infrastructure projects, taking advantage of its corrosion resistance and strength.
Zinc-coated products from Hitachi contribute to the longevity and reliability of industrial installations, reducing maintenance costs and downtime.
The company’s commitment to quality and innovation ensures that its zinc applications remain at the forefront of industrial engineering.
Global Strategies and Future Outlook
Japan’s zinc manufacturing sector is poised for continued growth and global influence.
Strategic investments in research and development, coupled with expanding international partnerships, will drive future advancements.
Expanding International Partnerships
Collaborating with global partners enables Japanese manufacturers to access new markets and share technological expertise.
These partnerships facilitate the exchange of best practices and promote the adoption of advanced zinc processing techniques worldwide.
Technological Advancements and Automation
Investments in automation and Industry 4.0 technologies enhance the efficiency and precision of zinc manufacturing processes.
Artificial intelligence, robotics, and data analytics are increasingly integrated into production systems, driving innovation and reducing operational costs.
Sustainability and Environmental Responsibility
The future of zinc manufacturing in Japan will increasingly focus on sustainability.
Developing eco-friendly processing methods and recycling initiatives will be crucial in minimizing environmental impact and meeting global sustainability goals.
Conclusion
Zinc remains a cornerstone of Japanese manufacturing, underpinning a wide array of industries with its versatile properties.
Through continuous innovation, strategic procurement, and a commitment to quality and sustainability, Japanese manufacturers have unlocked the full potential of zinc.
Their global impact extends beyond production, influencing market trends and setting standards for excellence in the zinc supply chain.
As Japan continues to lead in zinc manufacturing, the benefits of their expertise and practices will resonate throughout the global industrial landscape.
資料ダウンロード
QCD調達購買管理クラウド「newji」は、調達購買部門で必要なQCD管理全てを備えた、現場特化型兼クラウド型の今世紀最高の購買管理システムとなります。
ユーザー登録
調達購買業務の効率化だけでなく、システムを導入することで、コスト削減や製品・資材のステータス可視化のほか、属人化していた購買情報の共有化による内部不正防止や統制にも役立ちます。
NEWJI DX
製造業に特化したデジタルトランスフォーメーション(DX)の実現を目指す請負開発型のコンサルティングサービスです。AI、iPaaS、および先端の技術を駆使して、製造プロセスの効率化、業務効率化、チームワーク強化、コスト削減、品質向上を実現します。このサービスは、製造業の課題を深く理解し、それに対する最適なデジタルソリューションを提供することで、企業が持続的な成長とイノベーションを達成できるようサポートします。
オンライン講座
製造業、主に購買・調達部門にお勤めの方々に向けた情報を配信しております。
新任の方やベテランの方、管理職を対象とした幅広いコンテンツをご用意しております。
お問い合わせ
コストダウンが利益に直結する術だと理解していても、なかなか前に進めることができない状況。そんな時は、newjiのコストダウン自動化機能で大きく利益貢献しよう!
(Β版非公開)