- お役立ち記事
- Audit guide to ensure ISO9001 compliant suppliers
Audit guide to ensure ISO9001 compliant suppliers
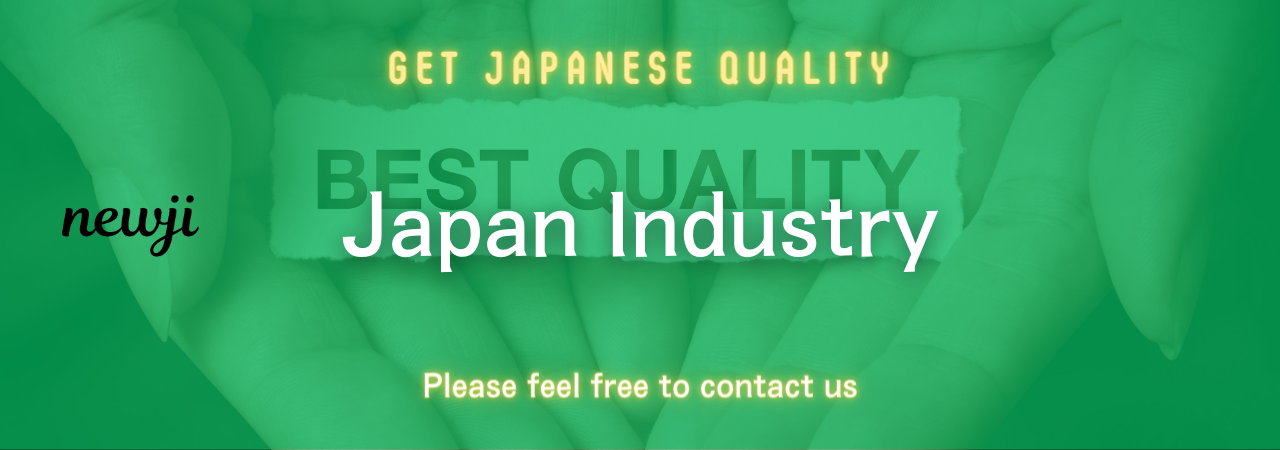
目次
Understanding ISO 9001 Compliance
ISO 9001 is an internationally recognized standard for quality management systems (QMS) that helps organizations deliver consistent quality in their products and services.
It provides a framework that businesses can follow to set up efficient processes and continuous improvement practices.
To ensure compliance, suppliers must adhere to various criteria that guarantee their operations meet the necessary quality standards.
Regular audits help organizations verify that their suppliers maintain these standards, helping them mitigate risks and maintain high levels of customer satisfaction.
The Importance of Supplier Audits
Conducting supplier audits is essential for several reasons.
Firstly, it ensures that suppliers consistently produce high-quality goods and services, aligning with the organization’s quality objectives.
Quality assurance is critical for maintaining the reputation of any business.
Secondly, audits help in identifying potential risks in the supply chain, allowing organizations to address them proactively.
This can prevent disruptions in operations and ensure timely delivery of products and services to customers.
Lastly, regular audits foster continuous improvement among suppliers.
When suppliers receive feedback, it encourages them to enhance their processes, benefiting both the supplier and the organization they serve.
Steps to Conduct a Supplier Audit
Conducting an audit may seem daunting, but breaking it down into clear steps can simplify the process.
Here’s a step-by-step guide to conducting an effective supplier audit:
Preparation
Before conducting a supplier audit, thorough preparation is vital.
Start by defining the scope and objectives of the audit.
Understand what aspects of the supplier’s operations need to be evaluated against ISO 9001 requirements.
Next, gather relevant documents and information, such as previous audit reports, the supplier’s quality manual, and process documentation.
This background information provides a solid foundation to build your audit plan.
Develop an audit checklist that includes the key areas to examine, such as management responsibilities, resource management, product realization, and measurement analysis.
This helps keep the audit focused and ensures all critical areas are covered.
Conducting the Audit
Once you have prepared, it’s time to conduct the audit.
Communicate with the supplier to schedule the audit, ensuring all parties are aware of the dates and expectations.
Begin the audit with an opening meeting to introduce the audit team and explain the purpose and scope.
It’s essential to establish good communication with the supplier to foster a cooperative environment.
As you audit, adhere to the checklist and assess compliance with ISO 9001 standards.
Observe processes, interview employees, and review documents and records.
Take detailed notes about areas of non-compliance or improvement opportunities.
Reporting Findings
After the audit, compile your findings into a clear, concise report.
The report should highlight areas where the supplier complies with ISO 9001 and areas of concern or non-compliance.
Provide a summary of strengths and suggested improvements.
Use objective language and provide evidence to support your findings.
Conclude with an action plan that outlines corrective measures the supplier should take to address issues.
Be sure to include a timeline for these actions to be implemented.
Ensuring Continuous Compliance
A single audit is a snapshot in time; continuous compliance requires ongoing effort.
Here are a few strategies to ensure your suppliers remain ISO 9001 compliant:
Regular Audits
Schedule regular audits to ensure sustained compliance.
This keeps suppliers accountable and encourages continual adherence to quality standards.
Consider varying the frequency based on the supplier’s risk profile.
High-risk suppliers might need more frequent audits compared to those with a strong track record of compliance.
Supplier Training and Development
Invest in supplier training to enhance their understanding of ISO 9001 requirements and quality management practices.
Workshops and seminars can help suppliers improve their processes and align with your organization’s quality standards.
Build Strong Relationships
Develop strong, transparent relationships with suppliers.
Open communication fosters trust and cooperation, making it easier to address compliance issues collaboratively.
Encourage suppliers to reach out with questions or concerns, and be responsive to their needs.
A supportive partnership can lead to better quality outcomes.
Continuous Improvement Culture
Fostering a culture of continuous improvement within both your organization and among your suppliers is crucial.
Encourage suppliers to implement corrective actions promptly and seek innovative solutions for quality challenges.
A collaborative approach to improvement creates a win-win situation, enhancing supplier capabilities and ensuring consistent quality in your supply chain.
Conclusion
Ensuring ISO 9001 compliant suppliers through effective audits is crucial for maintaining quality and achieving business objectives.
By preparing thoroughly, conducting detailed audits, and fostering ongoing relationships and improvement cultures, organizations can manage their supply chains effectively.
Remember, the goal of supplier audits is not only to ensure compliance but also to drive continuous improvement and strengthen partnerships, ultimately resulting in superior products and services for customers.
資料ダウンロード
QCD調達購買管理クラウド「newji」は、調達購買部門で必要なQCD管理全てを備えた、現場特化型兼クラウド型の今世紀最高の購買管理システムとなります。
ユーザー登録
調達購買業務の効率化だけでなく、システムを導入することで、コスト削減や製品・資材のステータス可視化のほか、属人化していた購買情報の共有化による内部不正防止や統制にも役立ちます。
NEWJI DX
製造業に特化したデジタルトランスフォーメーション(DX)の実現を目指す請負開発型のコンサルティングサービスです。AI、iPaaS、および先端の技術を駆使して、製造プロセスの効率化、業務効率化、チームワーク強化、コスト削減、品質向上を実現します。このサービスは、製造業の課題を深く理解し、それに対する最適なデジタルソリューションを提供することで、企業が持続的な成長とイノベーションを達成できるようサポートします。
オンライン講座
製造業、主に購買・調達部門にお勤めの方々に向けた情報を配信しております。
新任の方やベテランの方、管理職を対象とした幅広いコンテンツをご用意しております。
お問い合わせ
コストダウンが利益に直結する術だと理解していても、なかなか前に進めることができない状況。そんな時は、newjiのコストダウン自動化機能で大きく利益貢献しよう!
(Β版非公開)