- お役立ち記事
- How to proceed with supplier audits that purchasing departments should conduct to ensure legal compliance
How to proceed with supplier audits that purchasing departments should conduct to ensure legal compliance
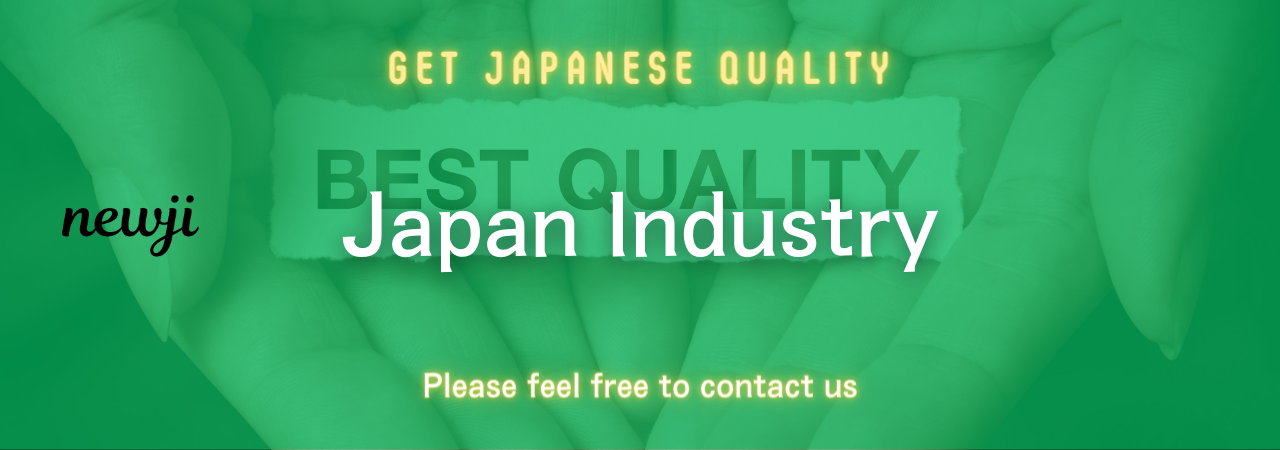
目次
Understanding Supplier Audits
Conducting supplier audits is an essential practice for purchasing departments to ensure that their suppliers comply with legal and regulatory standards.
A supplier audit involves evaluating a supplier’s processes, products, and systems to guarantee they meet required quality, safety, and ethical standards.
This process helps identify any non-compliance issues and fosters a collaborative relationship between the purchasing department and its suppliers.
The Importance of Supplier Audits
Supplier audits play a critical role in managing risks and maintaining compliance within the supply chain.
They help purchasing departments ensure that suppliers adhere to legal requirements, safeguard against financial risks, and protect the company’s reputation.
By proactively addressing compliance issues, companies can avoid potential legal liabilities and enhance their competitiveness in the market.
Moreover, supplier audits help uncover inefficiencies and potential improvements in the entire supply chain process.
Steps to Conduct Supplier Audits
1. Develop an Audit Plan
The first step in conducting supplier audits is developing a comprehensive audit plan.
The audit plan outlines the audit’s scope, objectives, criteria, and schedule.
It should also identify the resources required and the responsibilities of the audit team.
A well-structured audit plan ensures a systematic and organized approach to conducting the audit.
2. Define Audit Criteria
Defining clear audit criteria is crucial for assessing supplier compliance accurately.
Audit criteria may include legal and regulatory requirements, industry standards, and the company’s specific quality and performance expectations.
The criteria should be communicated to the supplier in advance to ensure transparency and mutual understanding.
3. Select the Audit Team
Choosing the right audit team is essential for the success of a supplier audit.
The team should possess the necessary expertise and knowledge to evaluate the supplier’s processes effectively.
Involving team members from different functions, such as quality assurance, procurement, and compliance, can provide diverse perspectives and insights during the audit.
4. Schedule the Audit
Scheduling the audit involves coordinating with the supplier to determine a suitable date and time for the audit.
It’s important to provide the supplier with adequate notice to prepare for the audit.
An agreed-upon schedule ensures minimal disruption to the supplier’s operations while allowing sufficient time for a thorough assessment.
5. Conduct the On-Site Audit
During the on-site audit, the audit team evaluates the supplier’s facilities, processes, and documentation.
This includes conducting interviews with relevant personnel, reviewing quality control practices, and inspecting production lines.
The audit team should use checklists and documentation tools to document findings and observations systematically.
6. Analyze and Report Findings
Once the on-site audit is completed, the audit team analyzes the findings to identify areas of compliance and non-compliance.
The results are compiled into a detailed audit report, which includes observations, recommendations, and action plans for addressing any identified issues.
The report should be communicated clearly to both the purchasing department and the supplier for transparency and accountability.
7. Follow-Up and Continuous Improvement
Following up on the audit findings is crucial to ensure that corrective actions are implemented effectively.
The purchasing department should work closely with the supplier to address any non-compliance issues and support continuous improvement initiatives.
Regular follow-up audits can help monitor progress and maintain ongoing compliance within the supply chain.
Best Practices for Supplier Audits
1. Foster a Collaborative Approach
A successful supplier audit should be seen as a collaborative effort between the purchasing department and the supplier.
Building a partnership based on trust and open communication encourages suppliers to willingly participate in the audit process and work towards improvement.
2. Emphasize Transparency and Fairness
Transparency and fairness are key principles in supplier audits.
Providing suppliers with clear expectations and criteria promotes fairness and helps avoid misunderstandings.
Transparency throughout the audit process builds credibility and strengthens the supplier relationship.
3. Use Data-Driven Insights
Data-driven insights can enhance the effectiveness of supplier audits.
Leveraging analytics and performance metrics can help identify trends and patterns in supplier performance.
This information can guide decision-making and prioritize areas for improvement.
4. Encourage Continuous Learning
Encouraging continuous learning and development within the supply chain is crucial for sustaining compliance and quality improvements.
Offering training and resources to suppliers can help them stay informed about evolving regulations and industry standards.
Conclusion
Supplier audits are a vital component of maintaining legal compliance and quality assurance within the supply chain.
By following a structured audit process and applying best practices, purchasing departments can effectively evaluate their suppliers’ compliance and foster a culture of collaboration and continuous improvement.
This proactive approach not only mitigates risks but also enhances the company’s reputation and competitive advantage.
資料ダウンロード
QCD調達購買管理クラウド「newji」は、調達購買部門で必要なQCD管理全てを備えた、現場特化型兼クラウド型の今世紀最高の購買管理システムとなります。
ユーザー登録
調達購買業務の効率化だけでなく、システムを導入することで、コスト削減や製品・資材のステータス可視化のほか、属人化していた購買情報の共有化による内部不正防止や統制にも役立ちます。
NEWJI DX
製造業に特化したデジタルトランスフォーメーション(DX)の実現を目指す請負開発型のコンサルティングサービスです。AI、iPaaS、および先端の技術を駆使して、製造プロセスの効率化、業務効率化、チームワーク強化、コスト削減、品質向上を実現します。このサービスは、製造業の課題を深く理解し、それに対する最適なデジタルソリューションを提供することで、企業が持続的な成長とイノベーションを達成できるようサポートします。
オンライン講座
製造業、主に購買・調達部門にお勤めの方々に向けた情報を配信しております。
新任の方やベテランの方、管理職を対象とした幅広いコンテンツをご用意しております。
お問い合わせ
コストダウンが利益に直結する術だと理解していても、なかなか前に進めることができない状況。そんな時は、newjiのコストダウン自動化機能で大きく利益貢献しよう!
(Β版非公開)