- お役立ち記事
- On-site audit to confirm supplier quality Checkpoints that purchasing department should perform
On-site audit to confirm supplier quality Checkpoints that purchasing department should perform
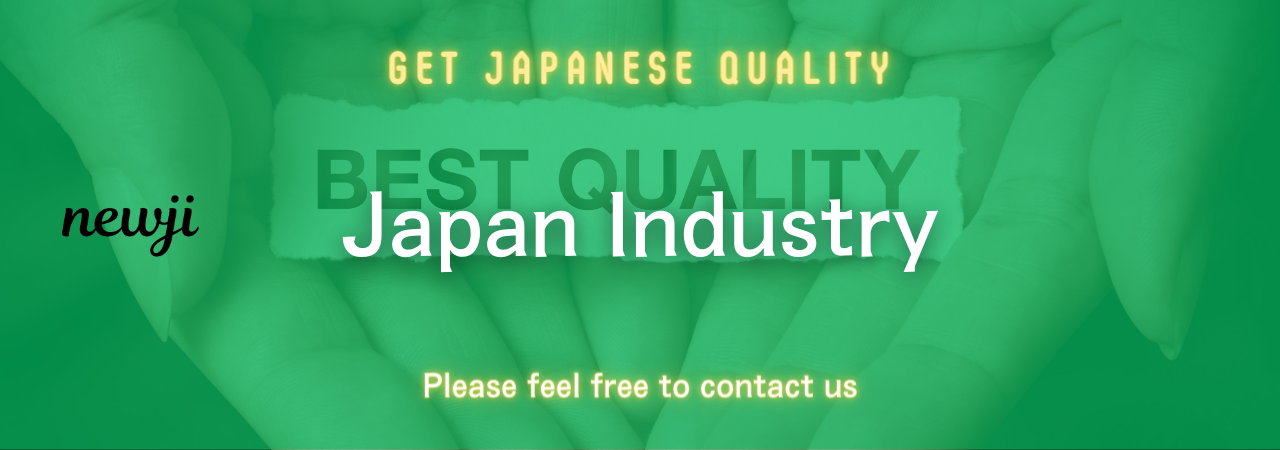
目次
Understanding the Importance of On-Site Audits
In today’s competitive business landscape, maintaining supplier quality is crucial for any organization.
A key strategy employed by purchasing departments to ensure the quality of products and services is conducting on-site audits.
These audits provide firsthand insight into a supplier’s operations, allowing buyers to verify that quality standards are met consistently.
The process typically involves visiting the supplier’s facility and examining various aspects of their operations.
On-site audits serve as a proactive approach to identify potential issues that might affect the supply chain.
Key Checkpoints for Conducting On-Site Audits
When a purchasing department plans an on-site audit, it’s essential to focus on several key checkpoints.
These checkpoints help assess the supplier’s ability to deliver quality products and services.
Let’s explore these important aspects:
1. Evaluate Quality Systems and Processes
The first checkpoint involves evaluating the supplier’s quality management systems.
This includes reviewing documentation such as quality manuals, standard operating procedures, and performance records.
Purchasing departments should verify if the supplier complies with industry standards, like ISO certifications, which indicate a commitment to maintaining high-quality processes.
2. Inspect Production Lines
Assessing the supplier’s production lines provides valuable insights into the manufacturing process.
Auditors should observe the workflow, check equipment maintenance, and ensure that workers follow safety protocols.
Any inconsistencies or areas for improvement should be documented for follow-up discussions.
3. Assess Inventory Management
How a supplier manages its inventory can directly affect product quality and delivery times.
During the audit, inspect how raw materials and finished goods are stored.
Look for evidence of proper labeling, rotation practices, and storage conditions that prevent damage or contamination.
4. Verify Quality Control Measures
Quality control is pivotal in ensuring that only products meeting specifications reach the market.
Examine the supplier’s quality control stations to understand how they conduct checks at various stages of production.
Assess the adequacy of testing methods and the calibration of equipment used for quality assessment.
5. Review Employee Training and Competence
A skilled workforce is crucial for maintaining quality standards.
Purchasing departments should review training programs to ensure employees are adequately trained for their roles.
This includes understanding critical processes, operating machinery, and identifying quality issues.
6. Analyze Supplier Performance Metrics
Check the supplier’s performance metrics such as defect rates, on-time delivery, and customer satisfaction scores.
These metrics provide a quantitative measure of the supplier’s overall performance and offer insights into areas requiring improvement.
7. Evaluate Environmental and Safety Practices
Inspect the supplier’s compliance with environmental and safety regulations.
This includes waste management, emissions controls, and the use of sustainable materials.
A supplier with strong environmental and safety practices is more likely to maintain consistent quality.
Developing an Effective Audit Plan
An effective audit plan is essential for a comprehensive on-site assessment.
The plan should include a detailed schedule, list of checkpoints, and a team of experienced auditors.
Good preparation ensures that the audit is thorough and productive.
Prioritize Communication
Prior to the audit, communicate the objectives and agenda to the supplier.
Transparency in expectations fosters a cooperative environment, which can help mitigate resistance or defensiveness from the supplier.
Assign Roles Clearly
Ensure that each member of the auditing team has a clear role and responsibility.
This streamlines the process and ensures that all key areas are scrutinized.
Conduct Follow-Up and Reporting
After the audit, compile findings into a comprehensive report.
Highlight any deviations from quality standards and offer recommendations for improvements.
Engage in a follow-up discussion with the supplier to address these findings and agree on corrective actions.
Building Strong Supplier Relationships
Conducting on-site audits should not be seen solely as a fault-finding mission.
Instead, it is an opportunity to strengthen relationships with suppliers through constructive feedback.
When suppliers understand the buyer’s commitment to quality, they are more motivated to enhance their processes.
Encourage Continuous Improvement
By identifying areas for improvement, suppliers can work on enhancing their processes.
Encourage them to adopt best practices and invest in technology or training that boosts their quality capabilities.
Foster Open Communication
Maintaining open lines of communication helps build trust between buyers and suppliers.
Regular dialogue ensures that suppliers remain aligned with the company’s quality expectations.
Conclusion
On-site audits are a powerful tool for purchasing departments aiming to ensure the quality of their supply chain.
By focusing on key checkpoints, developing a thorough audit plan, and fostering strong supplier relationships, companies can maintain high standards of quality.
This not only benefits the purchasing department but also enhances customer satisfaction and brand reputation in the long run.
資料ダウンロード
QCD調達購買管理クラウド「newji」は、調達購買部門で必要なQCD管理全てを備えた、現場特化型兼クラウド型の今世紀最高の購買管理システムとなります。
ユーザー登録
調達購買業務の効率化だけでなく、システムを導入することで、コスト削減や製品・資材のステータス可視化のほか、属人化していた購買情報の共有化による内部不正防止や統制にも役立ちます。
NEWJI DX
製造業に特化したデジタルトランスフォーメーション(DX)の実現を目指す請負開発型のコンサルティングサービスです。AI、iPaaS、および先端の技術を駆使して、製造プロセスの効率化、業務効率化、チームワーク強化、コスト削減、品質向上を実現します。このサービスは、製造業の課題を深く理解し、それに対する最適なデジタルソリューションを提供することで、企業が持続的な成長とイノベーションを達成できるようサポートします。
オンライン講座
製造業、主に購買・調達部門にお勤めの方々に向けた情報を配信しております。
新任の方やベテランの方、管理職を対象とした幅広いコンテンツをご用意しております。
お問い合わせ
コストダウンが利益に直結する術だと理解していても、なかなか前に進めることができない状況。そんな時は、newjiのコストダウン自動化機能で大きく利益貢献しよう!
(Β版非公開)