- お役立ち記事
- Purchasing strategies to minimize quality risks when inspecting imported products
Purchasing strategies to minimize quality risks when inspecting imported products
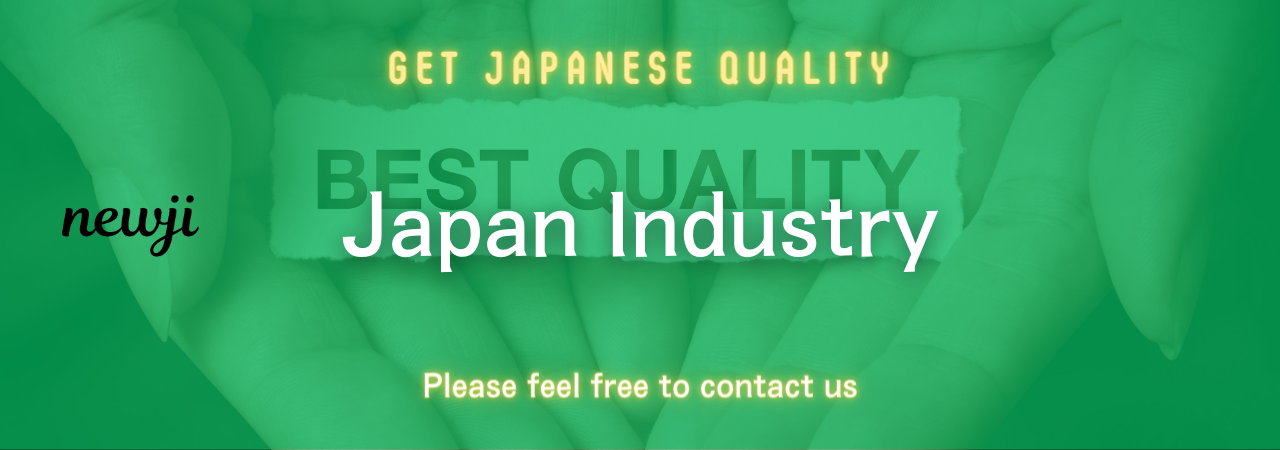
目次
Understanding Quality Risks in Imported Products
When businesses decide to import products, they often face quality risks that could impact their brand reputation and customer satisfaction.
Understanding these risks is the first step in developing effective purchasing strategies.
Quality risks in imported products can arise from several factors including different production standards, lack of real-time oversight during manufacturing, and inconsistent quality control measures in foreign facilities.
These risks can lead to defective products, non-compliance with regulations, and ultimately, loss of trust among consumers.
Identifying Common Quality Risks
Before formulating strategies to minimize these risks, it’s crucial to identify the most common quality concerns associated with imported goods.
Such risks include production defects, material substitutions, and non-compliance with international safety standards.
Production defects can stem from hasty manufacturing processes or inadequate quality control checks.
Materials used might not meet the original specifications, leading to substitutions that can affect the integrity of the product.
Non-compliance with safety standards is another common risk, particularly when manufacturers are unaware or choose to ignore regulations specific to the importer’s country.
Strategies for Mitigating Quality Risks
To minimize these risks, businesses must adopt comprehensive purchasing strategies that focus on assessment, planning, and ongoing monitoring.
Establishing Clear Specifications
An effective strategy begins with establishing clear product specifications and quality criteria with suppliers.
Detailed specifications should include material requirements, design specifications, and compliance with relevant standards.
By clearly defining what is required, businesses can set a strong foundation for quality assurance.
This also helps in creating detailed contracts that bind suppliers to certain quality commitments.
Choosing Reliable Suppliers
Partnering with the right supplier is a critical step in minimizing quality risks.
Conduct thorough research and due diligence before making any commitments.
Evaluate potential suppliers based on past performance, reputation, and their ability to meet quality standards.
It might be beneficial to visit the supplier’s manufacturing site for an on-ground assessment of their capabilities.
Building strong supplier relationships also plays a key role in ensuring quality.
When suppliers understand and are committed to your quality expectations, they are more likely to deliver consistent results.
Implementing Robust Inspection Processes
Regular inspections are crucial in ensuring product quality.
Pre-shipment inspections can detect defects before products leave the manufacturing site.
Consider third-party quality assurance providers who possess the expertise to conduct rigorous inspections.
These providers offer unbiased assessments and help ensure that products meet the required quality standards.
Additionally, in-line inspections during the production process can catch defects early, enabling manufacturers to rectify issues without significant delays or additional costs.
Utilizing Technology for Quality Control
Incorporating technology into quality control processes can greatly enhance effectiveness.
Digital tools and software provide real-time monitoring and data analysis that help identify potential issues quickly.
Some technologies include digital inspections, blockchain for tracking, and collaborative platforms that provide real-time updates between buyers and suppliers.
These technologies offer transparency and improve communication, reducing the likelihood of quality problems.
The Role of Training and Education
Educating both internal and external stakeholders about quality expectations is vital for successful quality control.
Training programs for procurement teams and suppliers ensure everyone understands the quality criteria and standards that must be adhered to.
Providing ongoing training keeps everyone informed about any changes in regulations or quality standards, reducing the risk of non-compliance.
Continuous Improvement and Feedback Loops
Implementing a continuous improvement strategy is essential for long-term success.
Establish feedback loops where you regularly review product performance and quality metrics.
These feedback loops help identify areas for improvement, allowing businesses to refine their purchasing strategies and quality control processes.
Moreover, maintaining open communication with suppliers encourages them to continually improve their processes and meet your quality expectations.
Case Studies and Best Practices
Analyzing case studies or learning from other businesses’ best practices can provide valuable insights on how to effectively implement purchasing strategies.
Success stories often highlight the importance of a strategic approach in minimizing quality risks.
Adopting practices such as rigorous supplier selection, technology integration, and continuous feedback mechanisms are common themes across successful case studies.
Conclusion: A Proactive Approach to Quality Assurance
In conclusion, managing quality risks in imported products requires a proactive and comprehensive approach.
By establishing clear specifications, choosing reliable suppliers, implementing robust inspection processes, and utilizing technology, businesses can significantly reduce quality risks.
Ongoing training and continuous improvement further ensure organizations maintain high-quality standards that meet consumer expectations.
Ultimately, by prioritizing quality in purchasing strategies, businesses protect their brand and build lasting customer trust.
資料ダウンロード
QCD調達購買管理クラウド「newji」は、調達購買部門で必要なQCD管理全てを備えた、現場特化型兼クラウド型の今世紀最高の購買管理システムとなります。
ユーザー登録
調達購買業務の効率化だけでなく、システムを導入することで、コスト削減や製品・資材のステータス可視化のほか、属人化していた購買情報の共有化による内部不正防止や統制にも役立ちます。
NEWJI DX
製造業に特化したデジタルトランスフォーメーション(DX)の実現を目指す請負開発型のコンサルティングサービスです。AI、iPaaS、および先端の技術を駆使して、製造プロセスの効率化、業務効率化、チームワーク強化、コスト削減、品質向上を実現します。このサービスは、製造業の課題を深く理解し、それに対する最適なデジタルソリューションを提供することで、企業が持続的な成長とイノベーションを達成できるようサポートします。
オンライン講座
製造業、主に購買・調達部門にお勤めの方々に向けた情報を配信しております。
新任の方やベテランの方、管理職を対象とした幅広いコンテンツをご用意しております。
お問い合わせ
コストダウンが利益に直結する術だと理解していても、なかなか前に進めることができない状況。そんな時は、newjiのコストダウン自動化機能で大きく利益貢献しよう!
(Β版非公開)