- お役立ち記事
- Practical methods for thorough quality control when selecting suppliers
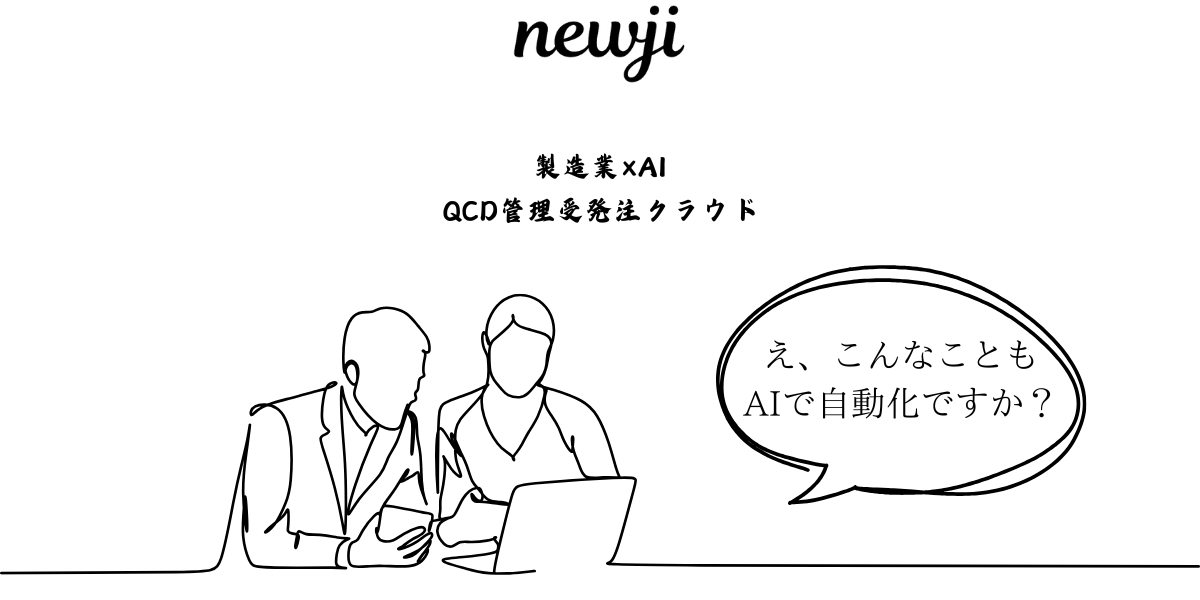
Practical methods for thorough quality control when selecting suppliers
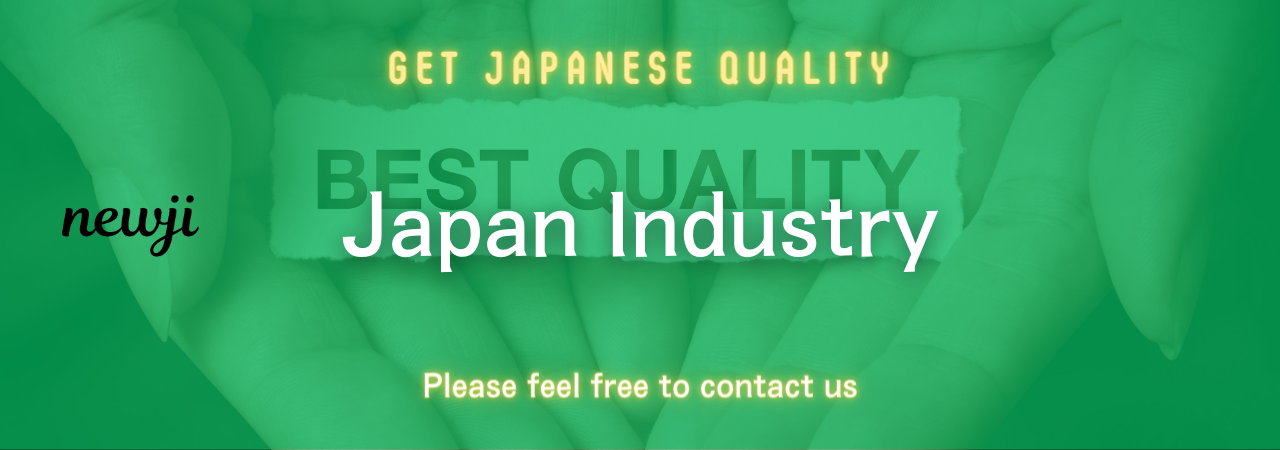
目次
Understanding Quality Control in Supplier Selection
When it comes to managing a business, one of the most crucial components is maintaining quality control during supplier selection.
Selecting the right suppliers can impact your business’s reputation, product quality, and customer satisfaction.
A systematic approach to quality control ensures that your company partners with suppliers who uphold the highest standards and meet your requirements effectively.
Quality control in supplier selection involves thorough assessment, scrutiny, and ongoing evaluation.
It is much more than just reviewing a supplier’s products or services.
Instead, it covers a comprehensive evaluation process to ensure factors such as reliability, compliance, production capabilities, and sustainability are met.
Setting Clear Quality Standards
The first step in implementing solid quality control during supplier selection is setting clear standards.
Having specific criteria helps frame the evaluation process and ensures consistency.
Define your quality expectations clearly.
This may include the material specifications, durability requirements, and any regulatory compliance standards pertinent to your industry.
Having these parameters helps you communicate your expectations to potential suppliers efficiently.
It’s also essential to develop a rubric that assesses various aspects of a supplier’s operations including production capacity, delivery timelines, and financial stability.
A well-rounded assessment framework aids in making more informed decisions.
Creating a Supplier Scorecard
Developing a supplier scorecard is an effective way to measure each supplier against your set standards.
A scorecard should cover several critical areas such as quality of products, price competitiveness, delivery performance, and service quality.
Additionally, the scorecard should sum up each area with a total score which helps compare suppliers effectively.
This quantitative measure assists in identifying which suppliers meet the organizational quality expectations best.
Conducting Thorough Supplier Audits
Supplier audits are a vital component of the supplier selection process to ensure quality control.
These audits assess whether suppliers have the capabilities and standards aligned with your company’s requirements.
An on-site audit examines various elements of a supplier’s operations.
It involves evaluating their production processes, quality management systems, and technology used in their facilities.
During audits, it’s beneficial to observe their manufacturing practices closely, ensuring they meet industry best practices.
Reviewing Supplier Certifications
Verifying that your suppliers have relevant certifications can provide assurance of their quality standards.
Certifications such as ISO 9001 or other industry-specific standards illustrate a supplier’s commitment to maintaining quality management systems.
These certifications are often issued by credible organizations and serve as indicators that a supplier follows documented processes and strives for continual improvement.
Checking for such certifications can supplement your quality control efforts.
Building Strong Relationships with Suppliers
Quality control is not just a one-time activity but rather an ongoing process that benefits from strong relationships with suppliers.
Cultivating transparent and honest relationships fosters trust and smoothens operations.
Communication is the cornerstone of building strong relationships.
Maintain open channels with your suppliers, providing feedback, and discussing any quality issues that may arise.
This leads to proactive problem solving and ensures both parties are on the same page.
Collaborative Improvement Initiatives
Encouraging collaborative improvement initiatives can enhance quality control measures.
Work closely with suppliers to identify improvement areas and jointly develop solutions.
Such collaborations often lead to optimized processes and cost efficiencies.
Additionally, offering training programs can be beneficial.
Investing in educational initiatives, such as workshops or webinars, offers suppliers the knowledge to improve their operations aligning them with your company’s quality demands.
Establishing Continuous Monitoring Systems
Once a supplier has been selected, quality control does not end.
The key to maintaining high standards of quality lies in continuous monitoring and evaluation.
Set metrics to regularly assess supplier performance.
Monitoring can include tracking delivery times, assessing product quality upon arrival, and evaluating cost fluctuations.
Regular reviews ensure suppliers remain accountable to your quality expectations.
Implementing Corrective Actions
In the event of any quality issues, swift corrective actions are necessary.
Identify the root cause of quality deviations and collaborate with suppliers to rectify the situation promptly.
Having a corrective action plan allows issues to be addressed quickly, avoiding potential disruptions.
Furthermore, conducting periodic reviews of corrective actions helps ensure that similar issues do not recur and that performance consistently aligns with expectations.
Leveraging Technology for Enhanced Quality Control
Modern technology provides numerous tools that facilitate enhanced quality control during supplier selection.
Supply chain management software can help streamline communication, manage supplier data, and analyze performance metrics more effectively.
Such systems integrate with existing operations, offering real-time monitoring and reporting capabilities.
Adopting technologies that support supplier relationship management also allows better tracking of compliance and collaborative opportunities, significantly enhancing the supply chain’s efficiency and reliability.
Conclusion
Thorough quality control in supplier selection is integral to building a strong, reliable supply chain.
By setting clear standards, conducting audits, fostering strong relationships, and leveraging technology, businesses can ensure their suppliers align with their quality benchmarks.
This strategic approach not only minimizes risk but also contributes to achieving superior product quality and maintaining customer satisfaction.
資料ダウンロード
QCD調達購買管理クラウド「newji」は、調達購買部門で必要なQCD管理全てを備えた、現場特化型兼クラウド型の今世紀最高の購買管理システムとなります。
ユーザー登録
調達購買業務の効率化だけでなく、システムを導入することで、コスト削減や製品・資材のステータス可視化のほか、属人化していた購買情報の共有化による内部不正防止や統制にも役立ちます。
NEWJI DX
製造業に特化したデジタルトランスフォーメーション(DX)の実現を目指す請負開発型のコンサルティングサービスです。AI、iPaaS、および先端の技術を駆使して、製造プロセスの効率化、業務効率化、チームワーク強化、コスト削減、品質向上を実現します。このサービスは、製造業の課題を深く理解し、それに対する最適なデジタルソリューションを提供することで、企業が持続的な成長とイノベーションを達成できるようサポートします。
オンライン講座
製造業、主に購買・調達部門にお勤めの方々に向けた情報を配信しております。
新任の方やベテランの方、管理職を対象とした幅広いコンテンツをご用意しております。
お問い合わせ
コストダウンが利益に直結する術だと理解していても、なかなか前に進めることができない状況。そんな時は、newjiのコストダウン自動化機能で大きく利益貢献しよう!
(Β版非公開)