- お役立ち記事
- Supplier risk assessment and response Risk management basics that purchasing personnel should know
Supplier risk assessment and response Risk management basics that purchasing personnel should know
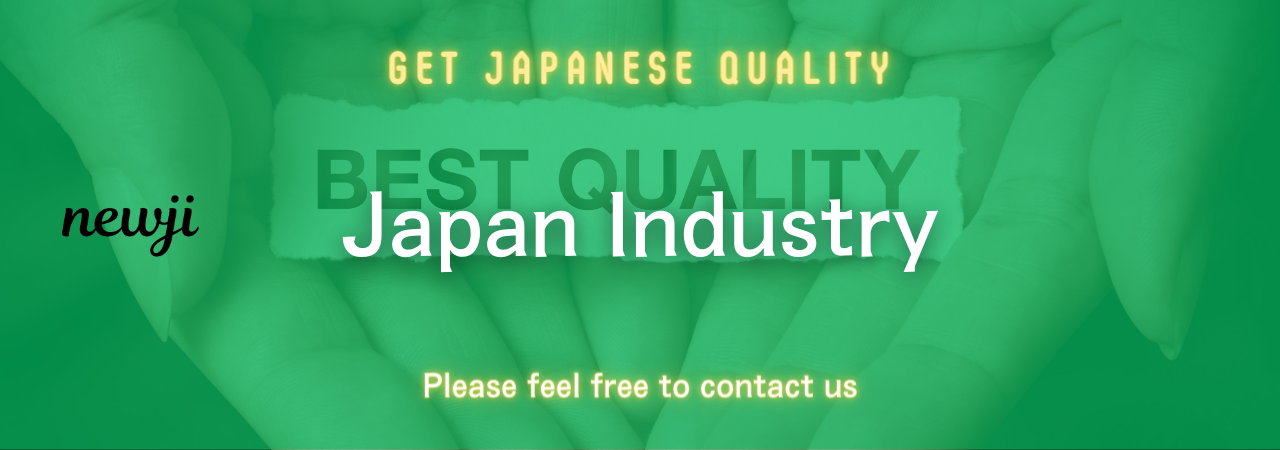
目次
Understanding Supplier Risk Assessment
Purchasing personnel play a pivotal role in ensuring the smooth operation of supply chains.
To do so effectively, they must be equipped with the knowledge of risk management basics.
One of the most crucial aspects of risk management is assessing supplier risk.
Supplier risk assessment is the process of identifying and evaluating potential risks that could impact the supply chain.
These risks can arise from various sources, including financial instability, geopolitical events, or compliance issues.
Conducting a thorough supplier risk assessment helps organizations anticipate issues before they arise, thereby mitigating potential disruptions.
To begin with, purchasing personnel should create a risk profile for each supplier.
This profile should include data on the supplier’s financial health, operational stability, geographical location, and historical performance.
Evaluating these factors helps organizations assess the likelihood and potential impact of risks associated with each supplier.
Key Factors in Supplier Risk Assessment
Several key factors should be considered when conducting a supplier risk assessment.
Firstly, financial assessment is crucial.
A supplier’s financial health can greatly affect their ability to deliver goods and services consistently.
By examining financial statements, credit ratings, and market reputation, purchasing personnel can gauge the supplier’s stability.
Secondly, operational stability is another important factor.
This includes assessing the supplier’s production capacity, technology, and quality control measures.
Understanding these aspects helps identify any potential weaknesses that could lead to supply chain disruptions.
Thirdly, the geographical location of the supplier can also introduce risks.
Suppliers located in regions prone to natural disasters or political instability may pose higher risks.
Understanding the geopolitical climate and its impact on the supplier’s operations is essential.
Lastly, compliance and ethical considerations must not be overlooked.
This involves assessing the supplier’s adherence to legal, environmental, and social standards.
Ensuring that suppliers operate ethically and in compliance with regulations can prevent reputational damage and potential regulatory penalties.
Supplier Risk Response Strategies
After conducting a supplier risk assessment, purchasing personnel must develop strategies to respond to identified risks.
There are several strategies that organizations can employ to mitigate supplier risks effectively.
Diversification of Suppliers
One of the most effective strategies is diversifying the supplier base.
Relying on a single supplier can expose an organization to significant risk.
By working with multiple suppliers, organizations can reduce the impact of any single supplier’s failure.
This approach not only minimizes risk but also enhances supply chain resilience.
Developing Contingency Plans
Having contingency plans in place is crucial for managing supplier risks.
These plans outline specific actions to be taken in the event of a disruption.
Contingency plans may include identifying alternative suppliers, increasing inventory levels, or temporarily adjusting production schedules.
Effective contingency planning ensures that organizations can continue operations even in the face of unexpected supplier disruptions.
Supplier Performance Monitoring
Continuous monitoring of supplier performance is essential for managing risks.
By establishing key performance indicators (KPIs), purchasing personnel can track supplier performance against agreed-upon standards.
This helps identify any deviations or potential issues early, allowing organizations to address them proactively.
Regular audits and evaluations also contribute to effective supplier performance monitoring.
These audits assess various aspects of supplier operations, including quality control, compliance, and delivery timelines.
The insights gained from these evaluations help organizations make informed decisions and maintain strong supplier relationships.
The Role of Technology in Supplier Risk Management
Advancements in technology have significantly improved the ability to manage supplier risks.
Various tools and platforms are available to streamline supplier risk assessment and response processes.
Data Analytics and Risk Assessment Tools
Data analytics plays a vital role in supplier risk management.
By analyzing vast amounts of data, organizations can gain insights into supplier performance, market trends, and potential risks.
Risk assessment tools leverage data analytics to provide real-time information on supplier risks, enabling purchasing personnel to make data-driven decisions.
Supply Chain Management Software
Supply chain management software offers a centralized platform for managing supplier relationships, contracts, and performance metrics.
These tools provide end-to-end visibility across the supply chain, allowing organizations to monitor supplier activities and assess risks promptly.
Features such as automated alerts and reporting help purchasing personnel stay informed and respond quickly to potential threats.
Conclusion: Empowering Purchasing Personnel
Understanding supplier risk assessment and response is essential for purchasing personnel.
By evaluating key risk factors, developing robust response strategies, and leveraging technology, organizations can effectively manage supplier risks.
Implementing these risk management basics equips purchasing personnel with the knowledge and tools needed to ensure the resilience and success of the supply chain.
By fostering strong supplier relationships and proactively addressing potential threats, organizations can thrive in an ever-changing global marketplace.
資料ダウンロード
QCD調達購買管理クラウド「newji」は、調達購買部門で必要なQCD管理全てを備えた、現場特化型兼クラウド型の今世紀最高の購買管理システムとなります。
ユーザー登録
調達購買業務の効率化だけでなく、システムを導入することで、コスト削減や製品・資材のステータス可視化のほか、属人化していた購買情報の共有化による内部不正防止や統制にも役立ちます。
NEWJI DX
製造業に特化したデジタルトランスフォーメーション(DX)の実現を目指す請負開発型のコンサルティングサービスです。AI、iPaaS、および先端の技術を駆使して、製造プロセスの効率化、業務効率化、チームワーク強化、コスト削減、品質向上を実現します。このサービスは、製造業の課題を深く理解し、それに対する最適なデジタルソリューションを提供することで、企業が持続的な成長とイノベーションを達成できるようサポートします。
オンライン講座
製造業、主に購買・調達部門にお勤めの方々に向けた情報を配信しております。
新任の方やベテランの方、管理職を対象とした幅広いコンテンツをご用意しております。
お問い合わせ
コストダウンが利益に直結する術だと理解していても、なかなか前に進めることができない状況。そんな時は、newjiのコストダウン自動化機能で大きく利益貢献しよう!
(Β版非公開)