- お役立ち記事
- Key points for shortening lead times by streamlining the procurement process
Key points for shortening lead times by streamlining the procurement process
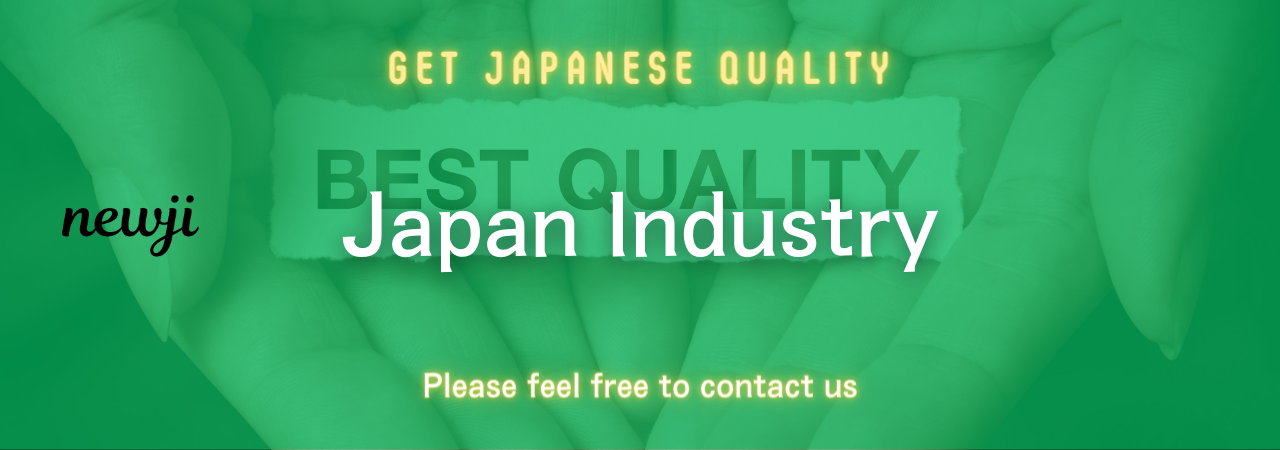
目次
Understanding the Procurement Process
The procurement process is a critical function in any organization that involves the acquisition of goods and services from external sources.
It is a series of activities that ranges from identifying needs to purchasing and receiving goods or services.
A streamlined procurement process ensures that these steps are performed efficiently, which helps in reducing overall lead times.
In essence, it is about getting the right goods or services at the right time, in the correct quantity, and at the best possible cost.
An efficient procurement process can significantly affect an organization’s bottom line and operational efficiency.
Key Components of Procurement
To shorten lead times, it’s crucial to understand the different components of procurement:
1. **Identification of Needs**: This is the initial step where requirements are clearly defined.
2. **Supplier Selection**: Selecting the right suppliers ensures quality, timeliness, and cost-effectiveness.
3. **Purchase Orders**: Proper documentation is vital for tracking and accountability.
4. **Receiving and Inspection**: This stage ensures that the goods received meet specified standards and conditions.
5. **Payment and Record-Keeping**: Timely payments and meticulous records are important for supplier relationships and audit trails.
Each of these stages offers opportunities for optimization, which can lead to shortened lead times and improved efficiencies.
Strategies for Streamlining the Procurement Process
Successfully streamlining the procurement process requires strategic planning and continuous improvement.
The following strategies can help organizations achieve this goal:
Leveraging Technology
Technology plays a significant role in optimizing the procurement process.
Implementing advanced procurement software allows for the automation of repetitive tasks, reduces errors, and improves communication between departments and suppliers.
Features such as real-time tracking, e-auctions, and supplier management modules can reduce procurement cycles and improve decision-making.
Supplier Relationship Management
Building and maintaining strong relationships with suppliers can significantly impact lead times.
Communicating clearly and maintaining open channels can ensure that suppliers understand expectations and can adjust their operations accordingly.
Collaboration with suppliers to plan and forecast demand can also prevent delays and increase efficiency in the supply chain.
Demand Forecasting
Accurate demand forecasting is essential to streamline procurement.
By anticipating needs, organizations can make informed purchasing decisions and avoid overstocking or understocking.
Using historical data, trends, and market analysis helps organizations order the right quantity of goods and reduce lead times by ensuring availability.
Standardizing Processes
Standardizing procurement processes across departments ensures consistency and reduces the time taken to complete each procurement task.
By having a set of guidelines and procedures, organizations can minimize misunderstandings and the repetition of work.
Process standardization can also aid in training new staff and improving overall efficiency.
Performance Metrics and KPIs
Establishing key performance indicators (KPIs) and regularly monitoring them helps identify areas that need improvement.
Metrics such as procurement cycle time, supplier performance, and cost savings can provide valuable insights into the effectiveness of the procurement process.
By analyzing these metrics, organizations can make data-driven decisions to further streamline their procurement efforts.
The Benefits of Streamlining Procurement
Organizations stand to gain numerous advantages by streamlining their procurement processes.
First and foremost, reduced lead times can enhance customer satisfaction by ensuring timely delivery of goods and services.
Improved efficiency lowers costs through better negotiation, reduced wastage, and minimized inventory holding.
Additionally, enhanced supplier relationships can lead to favorable terms and priority service, which further benefits both parties.
A streamlined procurement process also mitigates risks associated with delays, quality issues, and compliance failures by ensuring robust procedures are in place.
Challenges and Considerations
While streamlining the procurement process offers multiple benefits, it does come with its set of challenges.
Organizations may face resistance to change from employees accustomed to traditional methods.
Investing in new technologies may require a substantial initial investment, and the transition may disrupt day-to-day operations temporarily.
Moreover, ensuring data security and privacy when dealing with both suppliers and internal information is critical.
Organizations must also consider the global nature of supply chains, where geopolitical factors and natural disasters can impact procurement activities.
To overcome these challenges, leadership commitment, and a phased implementation approach are essential.
Providing training and support to employees during transitions can facilitate smoother adoption of new systems and processes.
Conclusion
In conclusion, streamlining the procurement process is a vital step toward shortening lead times and improving operational efficiency.
Through the use of technology, improved supplier relationships, accurate demand forecasting, standardized processes, and performance metrics, organizations can optimize their procurement functions.
While challenges exist, careful planning and commitment can lead to significant rewards in terms of cost savings, enhanced efficiency, and greater customer satisfaction.
As the business landscape continues to evolve with technological advancements, organizations that prioritize streamlining procurement will be better positioned to thrive in competitive markets.
資料ダウンロード
QCD調達購買管理クラウド「newji」は、調達購買部門で必要なQCD管理全てを備えた、現場特化型兼クラウド型の今世紀最高の購買管理システムとなります。
ユーザー登録
調達購買業務の効率化だけでなく、システムを導入することで、コスト削減や製品・資材のステータス可視化のほか、属人化していた購買情報の共有化による内部不正防止や統制にも役立ちます。
NEWJI DX
製造業に特化したデジタルトランスフォーメーション(DX)の実現を目指す請負開発型のコンサルティングサービスです。AI、iPaaS、および先端の技術を駆使して、製造プロセスの効率化、業務効率化、チームワーク強化、コスト削減、品質向上を実現します。このサービスは、製造業の課題を深く理解し、それに対する最適なデジタルソリューションを提供することで、企業が持続的な成長とイノベーションを達成できるようサポートします。
オンライン講座
製造業、主に購買・調達部門にお勤めの方々に向けた情報を配信しております。
新任の方やベテランの方、管理職を対象とした幅広いコンテンツをご用意しております。
お問い合わせ
コストダウンが利益に直結する術だと理解していても、なかなか前に進めることができない状況。そんな時は、newjiのコストダウン自動化機能で大きく利益貢献しよう!
(Β版非公開)