- お役立ち記事
- How to build traceability during transportation that should be managed by the purchasing department
How to build traceability during transportation that should be managed by the purchasing department
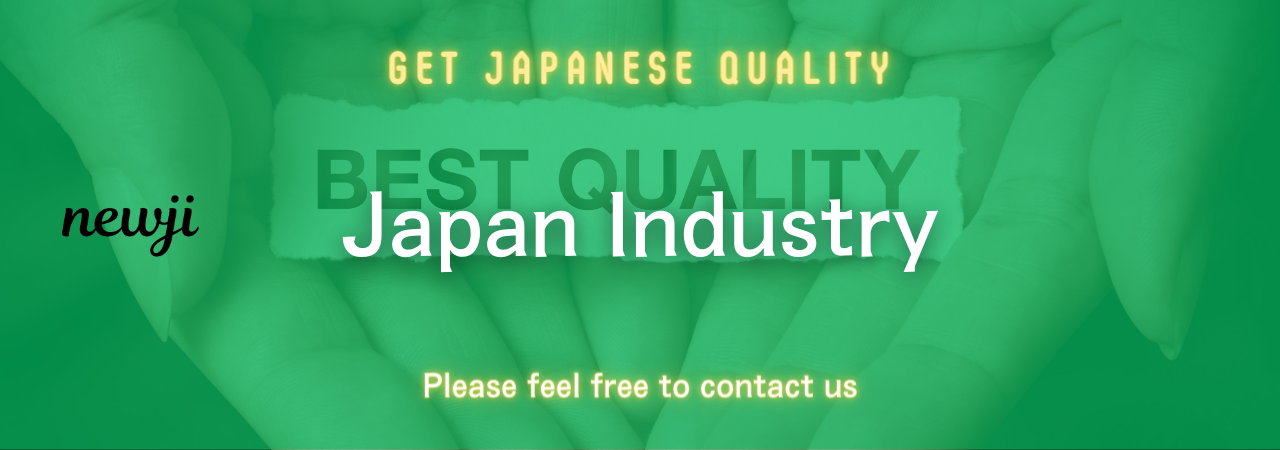
目次
Understanding Traceability in Transportation
Traceability in transportation is an essential aspect of supply chain management, especially for the purchasing department.
It involves tracking the movement of goods from the point of origin to the final destination.
This ensures that every step of the transport process is accounted for, making it easier to manage and resolve any issues that may arise.
Achieving high levels of traceability helps companies maintain transparency, boost customer trust, and improve operational efficiency.
The Importance of Traceability
Traceability provides numerous benefits for businesses.
First and foremost, it allows for greater transparency in the supply chain.
Customers today demand to know where their products come from and how they are transported.
Having a robust traceability system in place satisfies this demand, reinforcing consumer trust and brand loyalty.
Moreover, traceability greatly aids in risk management.
When businesses can trace their products in real-time, they are better equipped to identify and address potential risks or disruptions.
This capability is crucial for minimizing losses due to delays, damages, or other unforeseen issues.
Additionally, a well-established traceability system supports regulatory compliance by providing documented evidence of a product’s journey.
Steps to Build Traceability in Transportation
Building an effective traceability system requires a systematic approach.
Here’s how companies can achieve it:
1. Identify Key Elements to Track
The first step in building traceability is to determine which elements should be tracked.
This typically includes identifying the origins of goods, the shipping routes, and any intermediaries or third-party logistics providers involved.
It also involves noting the methods and conditions of transportation, such as temperature control for perishable items.
By clearly defining what needs to be tracked, companies can set the foundation for a comprehensive traceability system.
2. Implement Robust Tracking Technology
Once the key elements are identified, the next step is to integrate technology that facilitates real-time tracking.
GPS and RFID (Radio Frequency Identification) are popular technologies used to monitor a product’s location and condition throughout the transportation process.
Choosing the right technology depends on the specific needs of the company and the nature of the goods being transported.
Companies should invest in systems that offer reliability, accuracy, and scalability.
3. Establish Clear and Consistent Documentation
Documentation is a critical component of traceability.
Ensuring there is consistent and accurate documentation at every stage of transportation is vital.
This can include digital records like electronic bills of lading or physical documents.
Every transaction, movement, and inspection should be documented and stored in a centralized system that is accessible to key stakeholders.
This documentation not only acts as a record for the company but also reassures customers and regulatory bodies.
4. Collaborate with Suppliers and Logistics Partners
Traceability requires collaboration with all parties involved in the supply chain.
This includes suppliers, carriers, and any third-party logistics providers.
Building strong partnerships with these entities helps streamline communication and ensures everyone adheres to the same standards and protocols.
Regular audits and compliance checks should be conducted to maintain these relationships and ensure the traceability system is functioning efficiently.
5. Train Employees
Employees play a crucial role in maintaining traceability.
They need to be trained on how to use tracking technologies, manage documentation, and handle any issues that might arise during transportation.
Continuous training programs ensure that staff is up-to-date with the latest protocols and technologies.
Moreover, empowering employees with the knowledge and skills required to uphold traceability standards minimizes human error and enhances overall efficiency.
6. Monitor and Improve Continually
A successful traceability system is dynamic and requires continuous monitoring and improvement.
Businesses should regularly review their processes and technologies to identify any gaps or areas for enhancement.
Leverage data analytics to gain insights into transportation performance and identify trends or patterns.
By doing so, companies can make informed decisions to optimize their transportation strategies.
Challenges in Building Traceability
Despite its importance, achieving traceability in transportation comes with its challenges.
Data Integration
Integrating data from various sources and stakeholders can be complex.
Different systems and platforms might not seamlessly communicate with each other, leading to discrepancies.
Companies need to invest in integrated systems that allow for smooth data exchange and aggregation.
Cost
Implementing traceability systems can be costly, involving the purchase of technologies, training of staff, and ongoing maintenance.
For smaller companies, the financial burden can be significant.
However, the long-term benefits often outweigh these initial costs through improved efficiency and risk mitigation.
Resistance to Change
Some employees and stakeholders might resist changes to the traditional way of doing things.
Effectively communicating the benefits and necessity of traceability can help mitigate resistance.
Involving staff in the change process and soliciting their feedback can also ease transitions and foster a culture that embraces innovation.
Conclusion
Building traceability during transportation is an ongoing process that requires attention and collaboration across various aspects of supply chain management.
By implementing the right technologies, establishing clear protocols, and engaging with all stakeholders, the purchasing department can create a traceable, transparent, and efficient transportation system.
Overcoming initial challenges can pave the way for a future where companies not only meet regulatory demands and consumer expectations but also achieve enhanced operational success.
資料ダウンロード
QCD調達購買管理クラウド「newji」は、調達購買部門で必要なQCD管理全てを備えた、現場特化型兼クラウド型の今世紀最高の購買管理システムとなります。
ユーザー登録
調達購買業務の効率化だけでなく、システムを導入することで、コスト削減や製品・資材のステータス可視化のほか、属人化していた購買情報の共有化による内部不正防止や統制にも役立ちます。
NEWJI DX
製造業に特化したデジタルトランスフォーメーション(DX)の実現を目指す請負開発型のコンサルティングサービスです。AI、iPaaS、および先端の技術を駆使して、製造プロセスの効率化、業務効率化、チームワーク強化、コスト削減、品質向上を実現します。このサービスは、製造業の課題を深く理解し、それに対する最適なデジタルソリューションを提供することで、企業が持続的な成長とイノベーションを達成できるようサポートします。
オンライン講座
製造業、主に購買・調達部門にお勤めの方々に向けた情報を配信しております。
新任の方やベテランの方、管理職を対象とした幅広いコンテンツをご用意しております。
お問い合わせ
コストダウンが利益に直結する術だと理解していても、なかなか前に進めることができない状況。そんな時は、newjiのコストダウン自動化機能で大きく利益貢献しよう!
(Β版非公開)