- お役立ち記事
- Supplier selection criteria for purchasing departments to help with crisis management planning
Supplier selection criteria for purchasing departments to help with crisis management planning
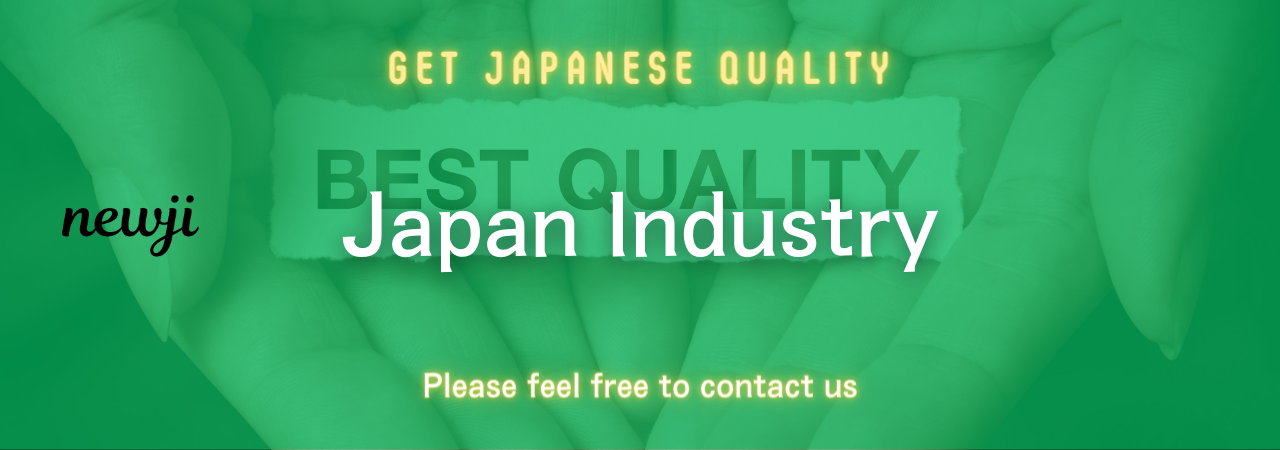
目次
Understanding Supplier Selection in Crisis Management
Purchasing departments play a pivotal role in ensuring smooth business operations.
A significant facet of their responsibilities involves the careful selection of suppliers.
Choosing the right suppliers becomes particularly crucial during times of crisis.
Effective crisis management planning is often the backbone that supports companies through challenging times.
In such situations, having reliable suppliers can make the difference between overcoming adversity and facing severe operational setbacks.
The Importance of Supplier Selection
During a crisis, the supply chain can be severely disrupted.
Delays, product shortages, and decreased quality may become daily challenges.
With a robust supplier selection process, purchasing departments can mitigate these issues effectively.
Thus, systematic supplier evaluation isn’t just a best practice—it’s an essential strategy for crisis readiness and resilience.
Key Criteria for Selecting Suppliers
When it comes to supplier selection, there are several critical criteria that departments should prioritize.
These factors help ensure that suppliers will support, not hinder, your crisis management efforts.
Reliability and Consistency
A supplier’s reliability plays an essential role during any disruption.
Purchasing departments must evaluate past relationships and supplier histories to gauge consistency.
Reliable suppliers consistently deliver products on time and meet the quality standards required by your company.
Flexibility and Adaptability
In a crisis, circumstances change rapidly.
Suppliers should demonstrate flexibility and the ability to adapt to changing conditions.
This capability helps maintain the continuity of supply, even when unforeseen challenges arise.
Quality Assurance
Maintaining high-quality standards is vital, even in challenging times.
Suppliers should have stringent quality control measures in place to ensure products meet your specifications.
Substandard products can lead to further complications, including customer dissatisfaction and compliance issues.
Financial Stability
The financial health of a supplier is a crucial consideration.
Financially stable suppliers are more likely to weather crises without ceasing operations or significantly increasing prices.
Purchasing departments should seek suppliers with strong financial profiles to minimize the risk of disruptions.
Communication and Responsiveness
Efficient communication is necessary to deal with the rapid pace of change during a crisis.
Suppliers should have good communication lines and must be responsive to inquiries and requests.
Strong communication enables quick resolution of issues and helps in proactive planning.
Compliance and Ethical Considerations
Another important factor is whether suppliers comply with industry regulations and ethical standards.
During a crisis, adherence to these norms ensures that collaborations do not lead to legal or reputational issues.
Purchasing departments should verify certifications, permits, and ethical practices during the selection process.
Developing a Strategic Supplier Relationship
Once the right suppliers have been identified using these criteria, maintaining and developing a strategic relationship with them is crucial.
Long-term partnerships with suppliers that align with your business goals will enhance the overall resilience of your supply chain.
Regular Performance Evaluations
Regular assessment of supplier performance helps maintain high standards and address any emerging issues.
These evaluations should focus on reliability, product quality, and responsiveness to requirements.
Building a feedback loop enables suppliers to improve and align their processes with your needs.
Collaborative Approach
Encouraging open dialogue and fostering collaboration between your company and suppliers ensures alignment on objectives.
Joint planning exercises and crisis simulations can further strengthen this relationship, ensuring preparedness for any situation.
Contractual Agreements
Establishing clear and comprehensive contracts with suppliers is essential.
These contracts should outline expectations, performance metrics, and contingency plans for crisis situations.
A detailed contract can prevent misunderstandings and provide a clear course of action when disruptions occur.
The Role of Technology in Supplier Selection
Leveraging technology to aid supplier selection is increasingly important.
Advanced software tools allow purchasing departments to analyze vast amounts of data, thereby enhancing decision-making capabilities.
Data Analysis and Insights
Technology can help in collecting and analyzing supplier data, providing insights into their performance, reliability, and financial stability.
With data-driven decision-making, purchasing departments can make informed choices and reduce risk.
Supply Chain Automation
Automation tools can streamline communication and operational processes with suppliers.
By reducing manual processes, companies can increase efficiency and respond more swiftly to changes.
Automating supply chain management tasks allows teams to focus more on strategic planning and less on routine tasks.
Conclusion
In conclusion, supplier selection is a multifaceted process with a direct impact on crisis management effectiveness.
By evaluating suppliers based on reliability, flexibility, quality, financial health, communication, and compliance, purchasing departments can build a resilient supply chain.
The development of strategic supplier relationships and the use of technology further enhance a company’s preparedness for crises.
Ultimately, thoughtful supplier selection not only ensures continuity during disruptions but also strengthens a company’s overall operational framework.
資料ダウンロード
QCD調達購買管理クラウド「newji」は、調達購買部門で必要なQCD管理全てを備えた、現場特化型兼クラウド型の今世紀最高の購買管理システムとなります。
ユーザー登録
調達購買業務の効率化だけでなく、システムを導入することで、コスト削減や製品・資材のステータス可視化のほか、属人化していた購買情報の共有化による内部不正防止や統制にも役立ちます。
NEWJI DX
製造業に特化したデジタルトランスフォーメーション(DX)の実現を目指す請負開発型のコンサルティングサービスです。AI、iPaaS、および先端の技術を駆使して、製造プロセスの効率化、業務効率化、チームワーク強化、コスト削減、品質向上を実現します。このサービスは、製造業の課題を深く理解し、それに対する最適なデジタルソリューションを提供することで、企業が持続的な成長とイノベーションを達成できるようサポートします。
オンライン講座
製造業、主に購買・調達部門にお勤めの方々に向けた情報を配信しております。
新任の方やベテランの方、管理職を対象とした幅広いコンテンツをご用意しております。
お問い合わせ
コストダウンが利益に直結する術だと理解していても、なかなか前に進めることができない状況。そんな時は、newjiのコストダウン自動化機能で大きく利益貢献しよう!
(Β版非公開)