- お役立ち記事
- How to shorten lead times and optimize inventory by rebuilding your procurement strategy
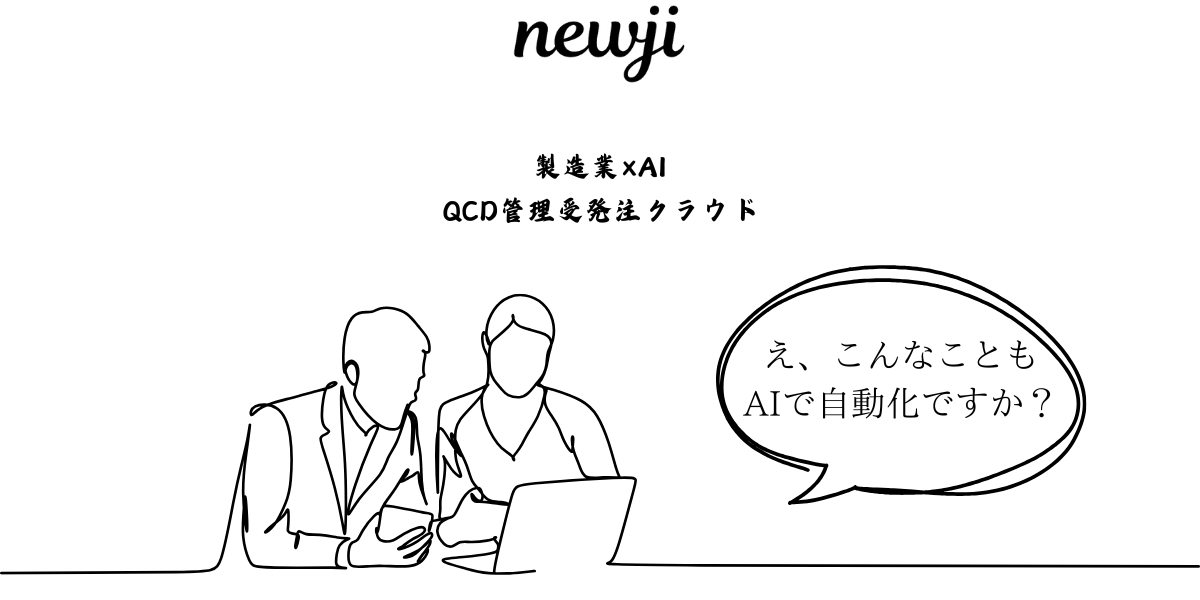
How to shorten lead times and optimize inventory by rebuilding your procurement strategy
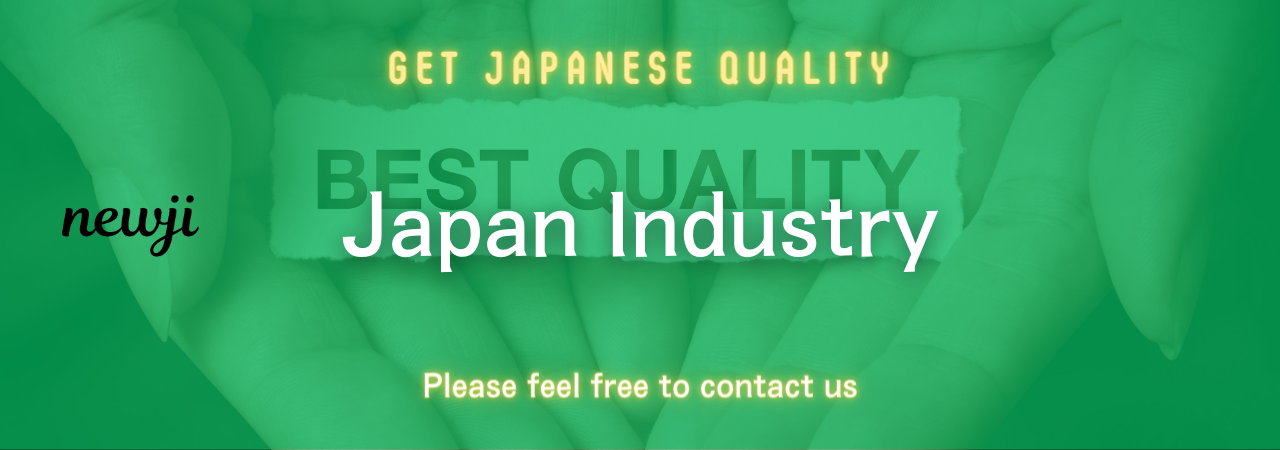
目次
Understanding Lead Times and Inventory
Before delving into strategies for optimizing procurement, it’s essential to understand lead times and inventory management.
Lead times refer to the duration between when an order is placed and when it is received.
Efficiently managing lead times can significantly impact a company’s supply chain, reducing delays and ensuring a smooth flow of goods.
Inventory, on the other hand, is the stock of goods a company holds to meet its current and future needs.
Poor inventory management can lead to excess stock or stockouts, both of which can adversely affect a company’s operations and finances.
The key to overcoming these challenges lies in rebuilding your procurement strategy to shorten lead times and optimize inventory.
Evaluating Your Current Procurement Strategy
Before you can improve your procurement strategy, a thorough evaluation of your current processes is necessary.
Identify Bottlenecks
Look for areas in your supply chain where delays are most frequent.
These could be due to supplier inefficiencies, transportation issues, or internal processes.
Once identified, you can work towards eliminating these bottlenecks.
Assess Supplier Performance
The performance of your suppliers can have a significant impact on lead times.
Consider factors such as delivery punctuality, quality of goods, and response times.
Having reliable suppliers can shorten lead times and reduce the need for holding excess inventory.
Analyze Inventory Levels
Examine your current inventory levels to determine if they align with demand.
Excess inventory can tie up capital, while inadequate inventory can lead to missed sales opportunities.
Striking the right balance is crucial for improving inventory efficiency.
Strategies to Shorten Lead Times
Shortening lead times can offer several advantages, such as improved customer satisfaction and reduced carrying costs.
Here are some strategies to achieve shorter lead times:
Build Strong Supplier Relationships
A strong relationship with suppliers can lead to better communication and cooperation.
Frequent interactions and open dialogues can help resolve issues quickly, improving lead times significantly.
Consider establishing long-term partnerships based on trust and mutual benefits.
Implement Technology
Leveraging technology can streamline the supply chain process.
Implement tools like inventory management software and automated ordering systems to improve efficiency.
These tools can help track inventory levels in real-time and automate reordering processes when stock levels are low, reducing the possibility of delays.
Consider Local Sourcing
Sourcing materials and products locally can drastically reduce lead times.
Local suppliers offer shorter transportation lanes and reduced risk of international shipping disruptions.
Moreover, local sourcing can also promote regional economic growth and environmental sustainability.
Optimizing Inventory for Better Results
Optimizing inventory is essential to ensure a smooth production process and meet customer demand without overstocking.
Adopt a Just-In-Time (JIT) Approach
The JIT inventory method minimizes inventory costs by ordering stock only when needed.
This approach requires precise demand forecasting and excellent supplier coordination but can lead to significant cost savings and improved cash flow.
Utilize Demand Forecasting
Accurate demand forecasting is crucial for maintaining optimized inventory levels.
Use historical data, market trends, and customer insights to predict future demand accurately.
Advanced analytics tools can assist in analyzing large datasets and provide more precise forecasts.
Implement Inventory Control Systems
Inventory control systems allow for better tracking and management of stock levels.
Such systems can alert you to low stock levels and automate reordering processes.
They can also help in identifying slow-moving inventory, allowing for informed decisions about markdowns or discontinuation of unpopular products.
Continuous Improvement and Adaptation
Rebuilding your procurement strategy is not a one-time task but a continuous process.
Monitor and Review Performance
Regularly monitor the performance of your procurement strategy and make necessary adjustments.
Use KPIs such as lead time reduction, order accuracy, and inventory turnover rates to measure success.
Analyzing these metrics can highlight areas for improvement and drive further optimization.
Stay Ahead of Market Trends
Market conditions and customer demands change frequently.
Stay informed about industry developments and be adaptable to changes.
Whether it’s adopting new technology or revising supplier agreements, staying agile can help maintain an optimized procurement strategy.
Foster a Culture of Continuous Improvement
Encourage your team to constantly seek out better methods and practices.
Training your staff and promoting a culture of continuous improvement can lead to innovative solutions and efficient processes.
Keeping your team motivated and aligned with company goals will ensure the long-term success of your procurement strategy.
In conclusion, rebuilding your procurement strategy to shorten lead times and optimize inventory is crucial for remaining competitive.
By evaluating your current processes, implementing effective strategies, and fostering continuous improvement, you can enhance efficiency and drive business success.
Being proactive and adaptable in an ever-changing market will ensure that your supply chain remains resilient and responsive to customer demands.
資料ダウンロード
QCD調達購買管理クラウド「newji」は、調達購買部門で必要なQCD管理全てを備えた、現場特化型兼クラウド型の今世紀最高の購買管理システムとなります。
ユーザー登録
調達購買業務の効率化だけでなく、システムを導入することで、コスト削減や製品・資材のステータス可視化のほか、属人化していた購買情報の共有化による内部不正防止や統制にも役立ちます。
NEWJI DX
製造業に特化したデジタルトランスフォーメーション(DX)の実現を目指す請負開発型のコンサルティングサービスです。AI、iPaaS、および先端の技術を駆使して、製造プロセスの効率化、業務効率化、チームワーク強化、コスト削減、品質向上を実現します。このサービスは、製造業の課題を深く理解し、それに対する最適なデジタルソリューションを提供することで、企業が持続的な成長とイノベーションを達成できるようサポートします。
オンライン講座
製造業、主に購買・調達部門にお勤めの方々に向けた情報を配信しております。
新任の方やベテランの方、管理職を対象とした幅広いコンテンツをご用意しております。
お問い合わせ
コストダウンが利益に直結する術だと理解していても、なかなか前に進めることができない状況。そんな時は、newjiのコストダウン自動化機能で大きく利益貢献しよう!
(Β版非公開)