- お役立ち記事
- Fundamentals of supplier assessment and risk management using digital tools
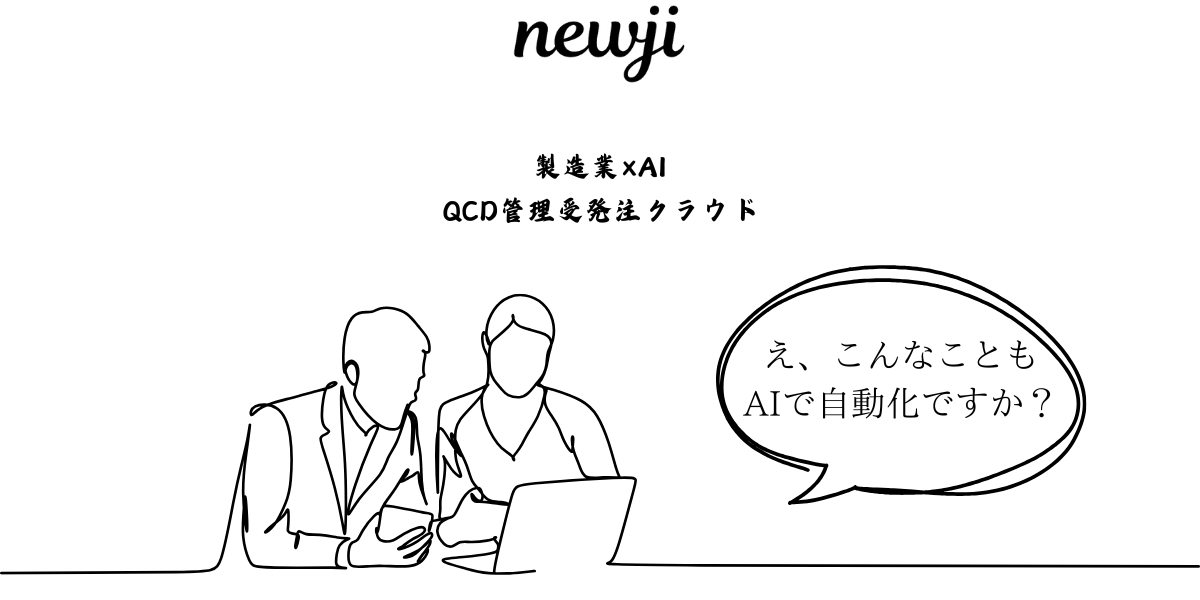
Fundamentals of supplier assessment and risk management using digital tools
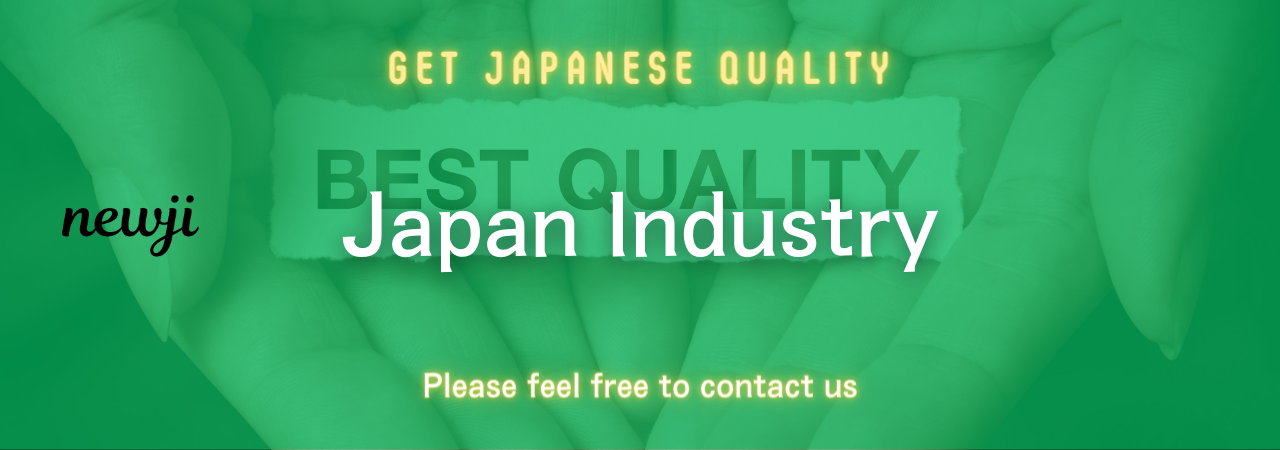
目次
Understanding Supplier Assessment
Supplier assessment is a critical process that ensures businesses choose reliable partners that meet their standards and requirements.
It involves evaluating various aspects of a supplier, such as their financial stability, production capabilities, quality control measures, and compliance with industry standards.
The goal of supplier assessment is to mitigate risks and safeguard the company’s operations by partnering with suppliers who can consistently deliver quality products or services.
Conducting a thorough supplier assessment can help businesses avoid potential problems, such as delayed deliveries, subpar quality, or supplier insolvency.
In today’s complex and globalized market, businesses often rely on a network of suppliers to meet their production or service needs.
As such, a structured approach to supplier assessment can ensure that the entire supply chain operates smoothly and efficiently.
Key Components of Supplier Assessment
When assessing a supplier, businesses typically evaluate several key components:
1. **Financial Health**: Checking a supplier’s financial stability is crucial to ensure they can meet long-term obligations and continue operations without interruption.
2. **Quality Assurance**: Assessing the quality management systems in place helps ensure the products or services meet the desired standards and specifications consistently.
3. **Capacity to Deliver**: Understanding a supplier’s production capacity is vital to determine if they can meet forecasted demand without compromising quality or timelines.
4. **Compliance and Certification**: Verifying that suppliers adhere to industry standards, legal requirements, and environmental regulations helps in maintaining compliance and ethical operations.
5. **Reputation and References**: Gathering feedback from other customers or third-party reviews can provide insights into the supplier’s performance and reliability.
6. **Supply Chain Risks**: Evaluating the potential risks within the supplier’s supply chain, such as geopolitical changes or dependency on single-source suppliers, can forecast future challenges.
The Role of Digital Tools in Supplier Assessment
Digital tools have transformed supplier assessment processes, making them more efficient, accurate, and comprehensive.
Incorporating technology enhances the ability to gather, analyze, and interpret data quickly, allowing for informed decision-making.
Data Analytics and Automation
Data analytics allows businesses to process vast amounts of information related to supplier performance and assess potential risks in real-time.
Automation streamlines repetitive tasks, such as monitoring compliance documents or updating records, freeing up resources for more strategic activities.
The integration of data analytics helps identify patterns that could signal potential risks, enabling companies to act proactively.
Cloud-Based Platforms
Cloud-based platforms centralize all supplier-related data, facilitating collaboration across departments and geographical locations.
These platforms often come with built-in tools for tracking supplier performance, setting alerts for critical measures, and generating comprehensive reports.
The accessibility provided by cloud technology ensures that all stakeholders can access real-time data and insights, speeding up the decision-making process.
Blockchain Technology
Blockchain technology offers a secure and transparent way to track transactions and verify information within the supply chain.
By using blockchain, businesses can ensure the integrity of supplier data and reduce risks related to fraud or tampering.
Additionally, blockchain can enhance traceability, helping identify the origin of materials and confirming compliance with specific standards.
Supplier Assessment Software
Dedicated supplier assessment software solutions can streamline the entire evaluation process, offering tools for everything from initial vetting to ongoing performance monitoring.
These programs often include risk assessment modules, which help in identifying and categorizing potential threats based on various criteria.
By using specialized software, businesses can establish a standardized approach to supplier assessment, ensuring consistency and accuracy.
Implementing Risk Management Strategies
Risk management is an integral part of supplier assessment, focusing on identifying, evaluating, and mitigating risks associated with supplier relationships.
An effective risk management strategy helps protect the business from supply chain disruptions and ensures continuity in operations.
Risk Identification and Analysis
The first step in risk management is identifying potential risks that could impact the supply chain, including financial, operational, and geopolitical risks.
Once identified, these risks need to be analyzed in terms of their likelihood and potential impact on the business.
Risk analysis helps prioritize the most critical threats, allowing companies to allocate resources effectively for mitigation.
Developing a Risk Mitigation Plan
With the analysis in place, businesses can develop a risk mitigation plan to minimize the impact of identified risks.
This may involve establishing contingency plans, diversifying the supplier base, or investing in technology to enhance predictability.
A well-defined mitigation plan ensures that the company is prepared to respond quickly and effectively in the event of a disruption.
Regular Monitoring and Review
Risk management is an ongoing process that requires regular monitoring and review to remain effective.
Businesses should establish mechanisms for continuous assessment of supplier performance and risk exposure, adjusting strategies as needed.
Regular reviews help in identifying new risks that may arise due to changes in the business environment or the supplier’s situation.
Communication and Collaboration
Open communication and collaboration with suppliers play a critical role in managing risks effectively.
By maintaining strong relationships, businesses can foster transparency and trust, ensuring any potential issues are addressed promptly.
Engaging suppliers in risk management discussions can also lead to innovative solutions that benefit both parties.
Conclusion
Incorporating supplier assessment and risk management into a company’s strategic framework is essential for maintaining a robust and efficient supply chain.
The use of digital tools significantly enhances these processes, providing better data insights and streamlined operations.
By understanding the fundamentals of supplier assessment and leveraging technology for risk management, businesses can safeguard against disruptions and promote sustainable growth.
Through continuous evaluation, communication, and adaptation, companies can build strong, reliable partnerships that drive success in a competitive market.
資料ダウンロード
QCD調達購買管理クラウド「newji」は、調達購買部門で必要なQCD管理全てを備えた、現場特化型兼クラウド型の今世紀最高の購買管理システムとなります。
ユーザー登録
調達購買業務の効率化だけでなく、システムを導入することで、コスト削減や製品・資材のステータス可視化のほか、属人化していた購買情報の共有化による内部不正防止や統制にも役立ちます。
NEWJI DX
製造業に特化したデジタルトランスフォーメーション(DX)の実現を目指す請負開発型のコンサルティングサービスです。AI、iPaaS、および先端の技術を駆使して、製造プロセスの効率化、業務効率化、チームワーク強化、コスト削減、品質向上を実現します。このサービスは、製造業の課題を深く理解し、それに対する最適なデジタルソリューションを提供することで、企業が持続的な成長とイノベーションを達成できるようサポートします。
オンライン講座
製造業、主に購買・調達部門にお勤めの方々に向けた情報を配信しております。
新任の方やベテランの方、管理職を対象とした幅広いコンテンツをご用意しております。
お問い合わせ
コストダウンが利益に直結する術だと理解していても、なかなか前に進めることができない状況。そんな時は、newjiのコストダウン自動化機能で大きく利益貢献しよう!
(Β版非公開)