- お役立ち記事
- Blooming Excellence: How Japanese Manufacturing is Transforming Global Industries
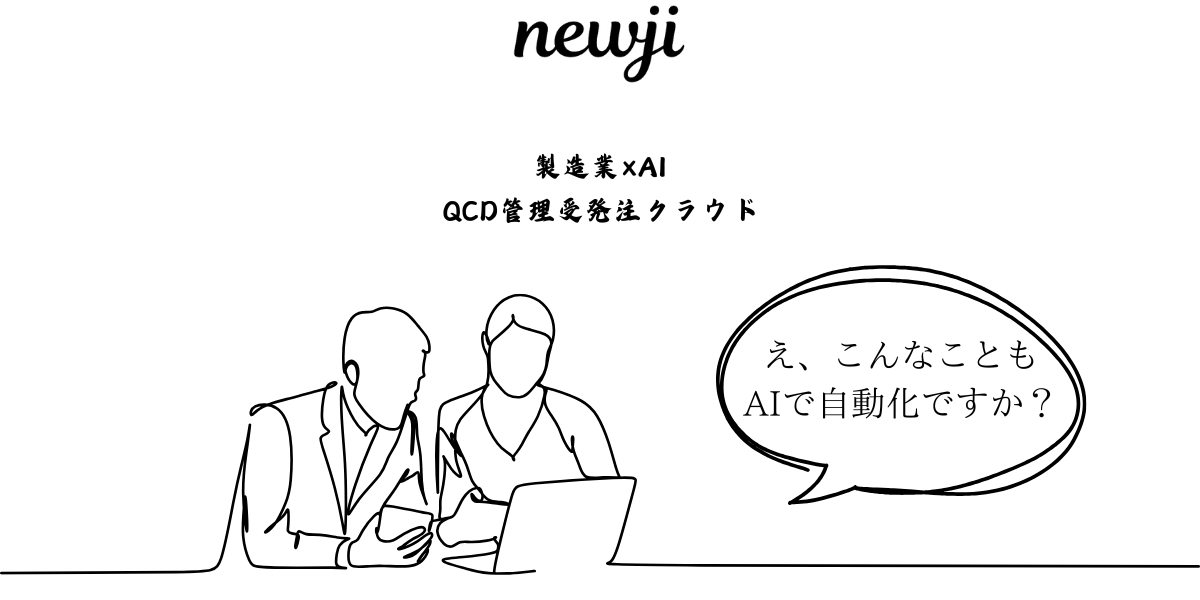
Blooming Excellence: How Japanese Manufacturing is Transforming Global Industries
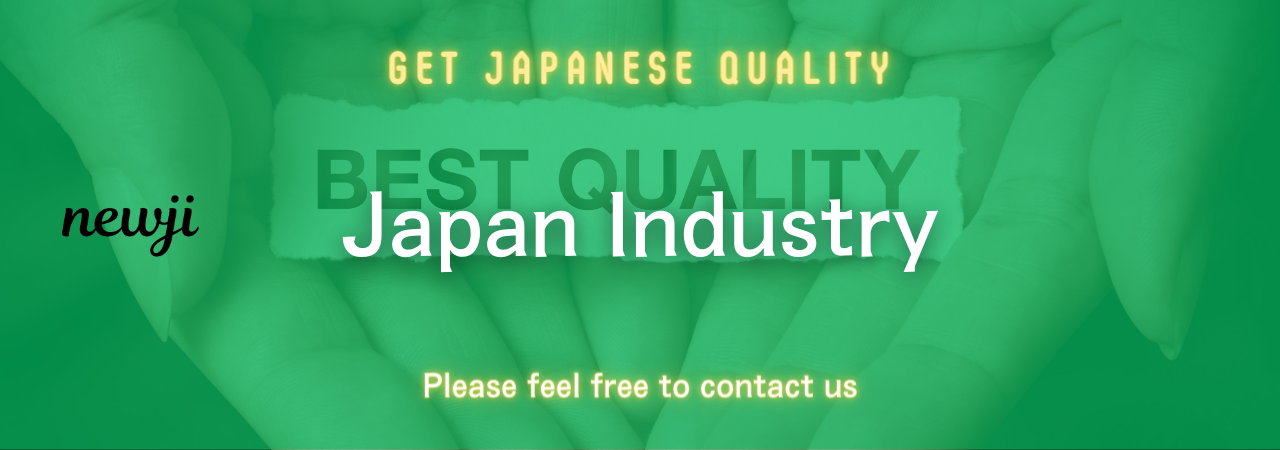
目次
Introduction to Japanese Manufacturing Excellence
Japanese manufacturing has long been synonymous with quality, innovation, and efficiency. Over the decades, Japanese companies have set benchmarks in various industries, transforming global manufacturing standards. This transformation is not merely a result of advanced technology but also stems from deep-rooted practices in procurement, purchasing, and supply chain management. Understanding the intricacies of Japanese manufacturing provides valuable insights for global industries aiming to enhance their own operations.
The Pillars of Japanese Manufacturing
Japanese manufacturing excellence is built upon several foundational pillars that ensure consistent quality and efficiency. These pillars include meticulous procurement processes, strong supplier relationships, continuous improvement practices, and advanced production techniques.
Meticulous Procurement Processes
Procurement in Japanese manufacturing is characterized by a strategic approach that emphasizes quality, reliability, and long-term partnerships. Japanese companies invest significant time in selecting suppliers who adhere to stringent quality standards. This meticulous selection process ensures that the materials and components sourced are of the highest quality, thereby reducing defects and enhancing the overall product quality.
Strong Supplier Relationships
Japanese manufacturers prioritize building strong, long-term relationships with their suppliers. This collaborative approach fosters mutual trust and commitment, enabling both parties to work together towards common goals. By maintaining open communication and sharing best practices, Japanese companies and their suppliers can innovate and improve continuously.
Continuous Improvement (Kaizen)
The concept of Kaizen, or continuous improvement, is deeply ingrained in Japanese manufacturing culture. It involves the ongoing effort to improve products, services, and processes. This philosophy encourages every employee to contribute ideas for enhancements, fostering a culture of constant innovation and efficiency.
Advanced Production Techniques
Japanese manufacturers are pioneers in adopting and developing advanced production techniques such as Just-In-Time (JIT) manufacturing, Total Quality Management (TQM), and Lean Manufacturing. These methodologies focus on minimizing waste, optimizing processes, and ensuring that production systems are flexible and responsive to market demands.
Advantages of Partnering with Japanese Suppliers
Collaborating with Japanese suppliers offers numerous advantages that can significantly benefit global manufacturing operations. These advantages range from superior quality and reliability to innovative technologies and strong ethical standards.
Exceptional Quality Standards
Japanese suppliers are renowned for their commitment to quality. They adhere to rigorous quality control measures and standards such as ISO certifications, ensuring that all products meet or exceed industry benchmarks. This focus on quality reduces the likelihood of defects and enhances the overall reliability of the supply chain.
Reliability and Consistency
Japanese manufacturers are known for their reliability in delivering products on time and within specifications. This consistency is crucial for maintaining smooth production schedules and avoiding costly delays or disruptions.
Innovation and Technology Leadership
Japanese companies are at the forefront of technological innovation. By partnering with Japanese suppliers, global manufacturers can access cutting-edge technologies and innovations that can enhance their own products and processes. This technological leadership provides a competitive edge in the global market.
Strong Ethical Standards
Japanese suppliers typically uphold high ethical standards, including fair labor practices, environmental responsibility, and compliance with regulatory requirements. This adherence to ethics not only ensures legal compliance but also aligns with the growing consumer demand for responsible and sustainable products.
Challenges in Collaborating with Japanese Suppliers
While there are numerous benefits to partnering with Japanese suppliers, there are also challenges that companies may encounter. Understanding these challenges is essential for establishing effective and harmonious business relationships.
Cultural and Communication Differences
Cultural differences can pose significant challenges in international collaborations. Japanese business culture emphasizes hierarchy, respect, and indirect communication, which may differ from the more direct communication styles of Western companies. Misunderstandings can arise if these cultural nuances are not properly navigated.
Language Barriers
Language differences can impede effective communication and lead to misunderstandings. While many Japanese professionals speak English, the level of proficiency can vary, making it essential to have skilled translators or bilingual team members to facilitate clear communication.
Negotiation Styles
Japanese negotiation styles tend to be more consensus-driven and less confrontational compared to Western approaches. This can lead to longer negotiation processes as decisions are made collectively and require approval from multiple levels within the organization. Patience and adaptability are crucial when engaging in negotiations with Japanese suppliers.
High Expectations for Quality and Performance
Japanese suppliers often have high expectations for their partners in terms of quality and performance. Meeting these standards may require significant adjustments in processes and practices, which can be challenging for companies not accustomed to such rigorous demands.
Effective Supplier Negotiation Techniques
Negotiating with Japanese suppliers requires a strategic approach that respects cultural norms and leverages mutual interests. Implementing effective negotiation techniques can lead to successful and long-lasting partnerships.
Building Trust and Relationships
In Japanese business culture, building trust and strong relationships is foundational before engaging in negotiations. Investing time in getting to know your suppliers, understanding their business values, and demonstrating commitment can pave the way for more effective negotiations.
Understanding Cultural Norms
Being aware of and respecting Japanese cultural norms is essential. This includes understanding the importance of hierarchy, formality, and indirect communication. Adapting to these norms shows respect and facilitates smoother negotiations.
Clear and Detailed Proposals
Japanese suppliers appreciate clear, detailed, and well-organized proposals. Presenting comprehensive information with thorough explanations demonstrates professionalism and preparedness, making it easier for suppliers to assess and respond to proposals.
Patience and Persistence
Negotiations with Japanese suppliers may take longer due to the consensus-driven decision-making process. Demonstrating patience and persistence without being overly aggressive can help in reaching mutually beneficial agreements.
Emphasizing Long-Term Benefits
Focusing on the long-term benefits of the partnership rather than short-term gains aligns with Japanese business philosophies. Highlighting how the collaboration can lead to sustained growth and innovation for both parties can strengthen the negotiation position.
Market Conditions and Trends in Japanese Manufacturing
Staying informed about the current market conditions and trends in Japanese manufacturing is crucial for effective procurement and purchasing strategies. These insights help in anticipating changes, identifying opportunities, and mitigating potential risks.
Emphasis on Sustainability
Japanese manufacturers are increasingly focusing on sustainability and environmentally friendly practices. This trend is driven by both consumer demand and regulatory requirements. Suppliers are adopting green technologies and sustainable processes to minimize their environmental impact.
Integration of Industry 4.0 Technologies
The adoption of Industry 4.0 technologies, such as the Internet of Things (IoT), artificial intelligence (AI), and automation, is reshaping Japanese manufacturing. These technologies enhance production efficiency, quality control, and supply chain transparency, enabling more responsive and agile manufacturing systems.
Global Supply Chain Resilience
Recent global disruptions have highlighted the importance of supply chain resilience. Japanese manufacturers are investing in diversification of their supply chains, increasing local sourcing, and implementing risk management strategies to mitigate the impact of potential disruptions.
Focus on Customization and Flexibility
There is a growing demand for customized and flexible manufacturing solutions in the Japanese market. Suppliers are developing the capability to offer tailored products and adaptable production processes to meet the specific needs of their clients.
Aging Workforce and Talent Development
Japan faces demographic challenges, including an aging workforce. To address this, companies are investing in talent development, automation, and robotics to maintain productivity levels and ensure the continuity of skilled labor.
Best Practices in Procurement and Purchasing from Japan
Adopting best practices in procurement and purchasing can enhance the effectiveness of collaborations with Japanese suppliers. These practices ensure smooth operations, quality assurance, and sustainable partnerships.
Comprehensive Supplier Evaluation
Conducting thorough evaluations of potential suppliers is crucial. This includes assessing their financial stability, production capabilities, quality standards, and ethical practices. On-site visits and audits can provide valuable insights into the supplier’s operations and reliability.
Establishing Clear Communication Channels
Effective communication is key to successful procurement. Establishing clear and consistent communication channels helps in conveying requirements, resolving issues, and maintaining transparency throughout the partnership.
Implementing Joint Improvement Initiatives
Collaborating on joint improvement initiatives, such as Kaizen projects, can lead to enhanced processes and innovations. These initiatives foster a sense of shared responsibility and commitment to continuous improvement.
Leveraging Technology for Supply Chain Management
Utilizing advanced technologies for supply chain management, such as Enterprise Resource Planning (ERP) systems and supply chain automation tools, can streamline procurement processes, improve inventory management, and enhance overall efficiency.
Ensuring Compliance and Risk Management
Maintaining compliance with international regulations and standards is essential. Implementing robust risk management strategies helps in identifying potential risks and developing contingency plans to address them effectively.
Case Studies: Success Stories in Japanese Manufacturing Partnerships
Examining real-world examples of successful partnerships with Japanese manufacturers can provide valuable lessons and inspire best practices.
Toyota’s Just-In-Time (JIT) Manufacturing
Toyota revolutionized the automotive industry with its Just-In-Time manufacturing system. By synchronizing production with demand and minimizing inventory, Toyota achieved unprecedented efficiency and responsiveness. This approach has been widely adopted across various industries, highlighting the effectiveness of JIT in enhancing supply chain performance.
Canon’s Supplier Integration
Canon has excelled in integrating its suppliers into its production processes. By involving suppliers in the design and development stages, Canon ensures that components are optimized for performance and quality. This collaborative approach has resulted in high-quality products and strong supplier relationships.
Panasonic’s Emphasis on Sustainability
Panasonic has committed to sustainability by implementing eco-friendly practices throughout its supply chain. From sourcing renewable materials to reducing carbon emissions, Panasonic’s efforts demonstrate how sustainability can be integrated into procurement and manufacturing processes, benefiting both the environment and the company’s reputation.
Strategies for Enhancing Factory Efficiency and Automation
Enhancing factory efficiency and leveraging automation are critical for maintaining competitiveness in the global market. Japanese manufacturers are leaders in these areas, employing strategies that can be emulated by companies worldwide.
Lean Manufacturing Principles
Adopting lean manufacturing principles helps in eliminating waste, optimizing processes, and improving overall efficiency. By focusing on value-added activities and minimizing non-value-added steps, manufacturers can streamline operations and reduce costs.
Automation and Robotics
Integrating automation and robotics into production lines increases precision, speed, and consistency. Automated systems can handle repetitive tasks, allowing human workers to focus on more complex and creative aspects of production.
Data-Driven Decision Making
Utilizing data analytics and real-time monitoring enables manufacturers to make informed decisions. By analyzing production data, companies can identify bottlenecks, predict maintenance needs, and optimize resource allocation.
Flexible Manufacturing Systems
Implementing flexible manufacturing systems allows for quick adjustments to production processes to meet changing market demands. This adaptability is essential for responding to customer needs and maintaining competitiveness.
Employee Training and Development
Investing in employee training and development ensures that the workforce is skilled in the latest technologies and best practices. Continuous training fosters a culture of excellence and equips employees with the knowledge needed to operate advanced manufacturing systems efficiently.
Conclusion
Japanese manufacturing continues to be a driving force in transforming global industries through its unwavering commitment to quality, innovation, and efficiency. By adopting Japanese procurement and purchasing practices, companies can establish strong, reliable partnerships, enhance their supply chains, and achieve long-term success. While challenges such as cultural differences and high expectations exist, the advantages of collaborating with Japanese suppliers far outweigh the obstacles. Embracing best practices, leveraging advanced technologies, and fostering continuous improvement are key strategies for capitalizing on the benefits of Japanese manufacturing excellence. As global industries evolve, the lessons from Japanese manufacturers will remain invaluable in navigating the complexities of modern manufacturing and procurement.
資料ダウンロード
QCD調達購買管理クラウド「newji」は、調達購買部門で必要なQCD管理全てを備えた、現場特化型兼クラウド型の今世紀最高の購買管理システムとなります。
ユーザー登録
調達購買業務の効率化だけでなく、システムを導入することで、コスト削減や製品・資材のステータス可視化のほか、属人化していた購買情報の共有化による内部不正防止や統制にも役立ちます。
NEWJI DX
製造業に特化したデジタルトランスフォーメーション(DX)の実現を目指す請負開発型のコンサルティングサービスです。AI、iPaaS、および先端の技術を駆使して、製造プロセスの効率化、業務効率化、チームワーク強化、コスト削減、品質向上を実現します。このサービスは、製造業の課題を深く理解し、それに対する最適なデジタルソリューションを提供することで、企業が持続的な成長とイノベーションを達成できるようサポートします。
オンライン講座
製造業、主に購買・調達部門にお勤めの方々に向けた情報を配信しております。
新任の方やベテランの方、管理職を対象とした幅広いコンテンツをご用意しております。
お問い合わせ
コストダウンが利益に直結する術だと理解していても、なかなか前に進めることができない状況。そんな時は、newjiのコストダウン自動化機能で大きく利益貢献しよう!
(Β版非公開)