- お役立ち記事
- Revolutionizing Japanese Manufacturing: How Autonomous Mobile Robots (AMR) are Shaping the Future
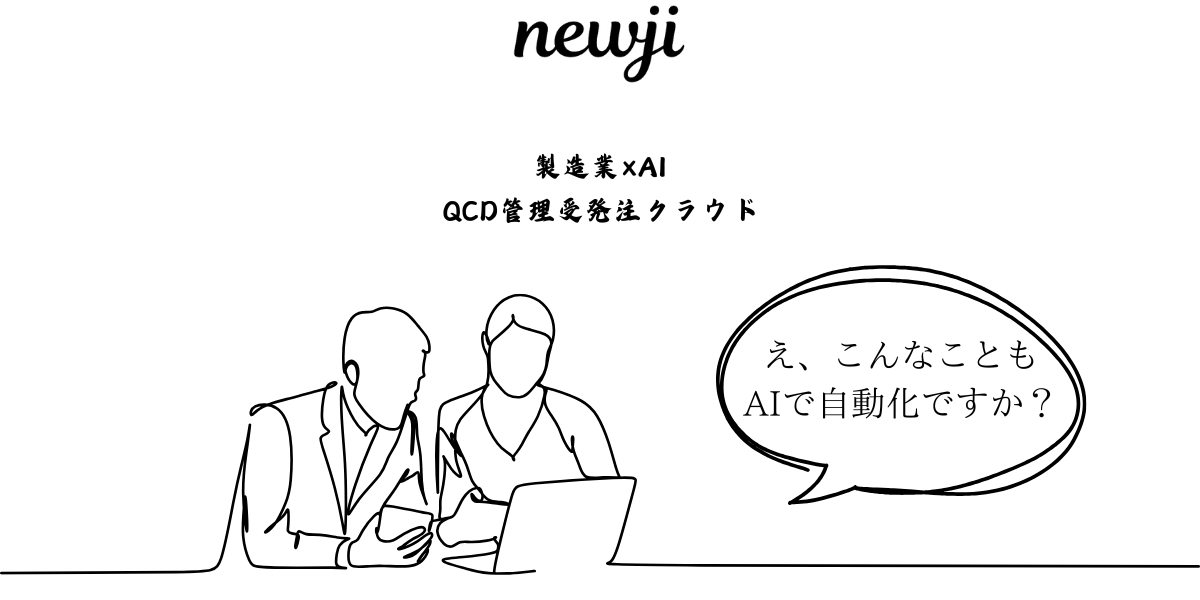
Revolutionizing Japanese Manufacturing: How Autonomous Mobile Robots (AMR) are Shaping the Future
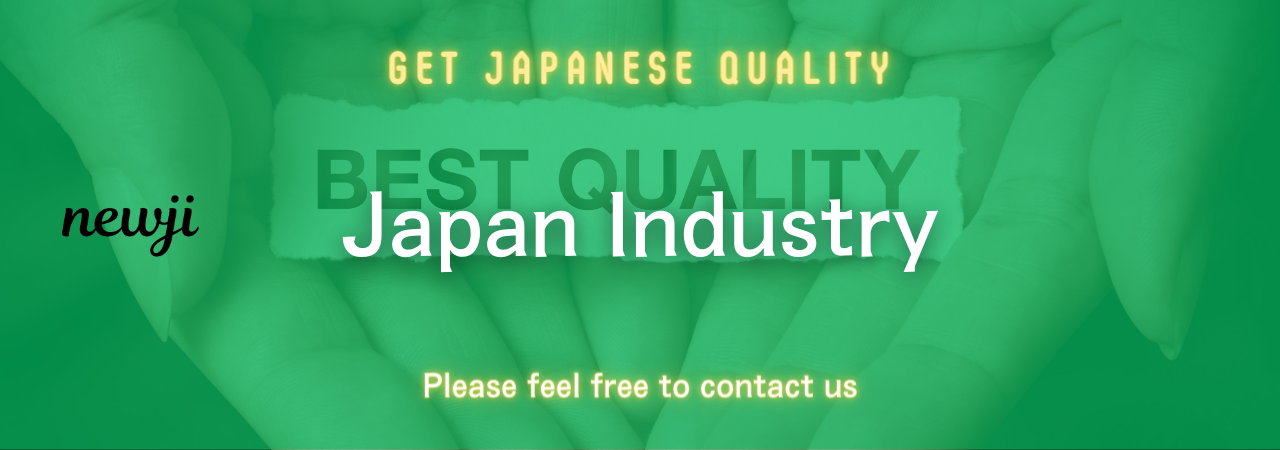
目次
Introduction to Autonomous Mobile Robots (AMR) in Japanese Manufacturing
Autonomous Mobile Robots (AMR) are transforming the landscape of Japanese manufacturing.
These intelligent machines navigate and perform tasks with minimal human intervention.
Japan, renowned for its advanced technology and manufacturing prowess, is at the forefront of integrating AMRs into production lines.
The adoption of AMRs is not just a technological upgrade but a strategic move to enhance efficiency, reduce costs, and maintain Japan’s competitive edge in the global market.
The Role of AMRs in Procurement and Purchasing
AMRs significantly impact the procurement and purchasing departments by streamlining supply chain operations.
They facilitate real-time inventory management, ensuring that materials are ordered and restocked precisely when needed.
This automation reduces human error, minimizes overstocking or stockouts, and optimizes inventory levels.
Furthermore, AMRs can integrate with procurement software to automatically place orders based on predefined thresholds, enhancing the efficiency of the purchasing process.
Advantages of Integrating AMRs in Procurement
The integration of AMRs in procurement offers several advantages.
Firstly, it improves operational efficiency by automating repetitive tasks, allowing procurement professionals to focus on strategic activities.
Secondly, AMRs enhance accuracy in inventory management, leading to better decision-making and reduced costs.
Thirdly, the real-time data collected by AMRs provides valuable insights into supply chain dynamics, enabling more informed purchasing decisions.
Challenges and Disadvantages
Despite their benefits, integrating AMRs presents certain challenges.
The initial investment in AMR technology can be substantial, which may be a barrier for some companies.
Additionally, there is a need for skilled personnel to manage and maintain AMRs, which can lead to increased training costs.
Another potential drawback is the reliance on technology; any system failures or malfunctions can disrupt production processes.
Supplier Negotiation Techniques for AMRs
Effective supplier negotiation is crucial when procuring AMRs.
Building strong relationships with suppliers can lead to better pricing, improved service, and access to the latest technological advancements.
Negotiation strategies should focus on long-term partnerships rather than one-time transactions.
This approach ensures that suppliers are invested in the success and continuous improvement of AMR implementations.
Understanding Supplier Capabilities
Before entering negotiations, it is essential to understand the capabilities and limitations of potential suppliers.
Assessing their technological expertise, production capacity, and reliability can provide a solid foundation for negotiations.
Additionally, evaluating the supplier’s track record in delivering similar projects can help gauge their suitability for your specific needs.
Leveraging Market Conditions
Market conditions play a significant role in supplier negotiations.
Staying informed about the latest trends, demand-supply dynamics, and technological advancements in the AMR market can provide leverage during negotiations.
For instance, if there is a high demand for AMRs, suppliers may offer better terms to secure contracts.
Conversely, in a more competitive market, buyers may have more negotiating power to obtain favorable deals.
Market Conditions Influencing AMR Adoption in Japan
The Japanese manufacturing sector is characterized by its emphasis on precision, quality, and innovation.
Several market conditions are driving the adoption of AMRs in this environment.
Aging Workforce
Japan faces a demographic challenge with an aging workforce.
AMRs offer a solution by automating tasks that are physically demanding or repetitive, thus compensating for labor shortages and extending the productivity of existing workers.
Technological Advancements
Continuous advancements in robotics, artificial intelligence, and machine learning have made AMRs more capable and cost-effective.
These technologies enable AMRs to perform complex tasks with higher efficiency and accuracy, making them indispensable in modern manufacturing setups.
Global Competition
Intense global competition requires Japanese manufacturers to maintain high efficiency and quality standards.
AMRs contribute to these objectives by optimizing production processes, reducing downtime, and ensuring consistent product quality.
Best Practices for Implementing AMRs in Manufacturing
Successful implementation of AMRs requires careful planning and adherence to best practices.
Comprehensive Needs Assessment
Before deploying AMRs, conduct a thorough needs assessment to identify areas where automation can provide the most significant benefits.
This involves analyzing current workflows, identifying bottlenecks, and determining the specific tasks that AMRs can perform effectively.
Integration with Existing Systems
Ensure that AMRs can seamlessly integrate with existing manufacturing systems and software.
Compatibility with enterprise resource planning (ERP) and manufacturing execution systems (MES) is crucial for smooth operations and data synchronization.
Employee Training and Change Management
Implementing AMRs necessitates training employees to work alongside these robots.
Effective change management strategies should be in place to address resistance, ensure smooth transitions, and maximize the benefits of AMR integration.
Continuous Monitoring and Optimization
Post-implementation, continuously monitor the performance of AMRs and gather feedback to identify areas for improvement.
Regular maintenance and updates are essential to keep AMRs operating at peak efficiency and adapting to evolving manufacturing needs.
Quality Control and AMR Deployment
Quality control is a critical aspect of Japanese manufacturing, and AMRs play a vital role in enhancing it.
Consistency and Precision
AMRs ensure consistency and precision in tasks such as material handling, assembly, and inspection.
Their ability to perform repetitive tasks with high accuracy reduces the likelihood of errors and defects, thereby improving overall product quality.
Data-Driven Quality Assurance
AMRs collect and analyze data in real-time, providing valuable insights into production processes.
This data-driven approach enables proactive quality assurance measures, allowing manufacturers to identify and address potential issues before they escalate.
Enhancing Factory Efficiency through AMRs
AMRs contribute significantly to factory efficiency by optimizing various operational aspects.
Optimized Material Flow
AMRs streamline material flow within the factory by autonomously transporting materials between different stages of production.
This automation reduces transit times, minimizes handling costs, and ensures timely delivery of components, thereby accelerating the overall production cycle.
Reduced Downtime
By performing routine tasks and maintenance, AMRs help reduce downtime.
They can monitor equipment performance, predict maintenance needs, and even perform certain maintenance tasks, ensuring that production lines remain operational and minimizing interruptions.
Energy Efficiency
AMRs can also contribute to energy efficiency by optimizing their routes and operations to reduce energy consumption.
Efficient energy use not only lowers operational costs but also aligns with sustainability goals, which are increasingly important in modern manufacturing.
Automation and the Future of Japanese Manufacturing
The integration of AMRs is a cornerstone of the broader automation trend reshaping Japanese manufacturing.
Smart Factories
AMRs are integral to the development of smart factories, which utilize interconnected systems and real-time data to enhance manufacturing processes.
In smart factories, AMRs operate in harmony with other automated systems, creating a cohesive and highly efficient production environment.
Scalability and Flexibility
AMRs provide scalability and flexibility, allowing manufacturers to adapt quickly to changing market demands.
They can be reprogrammed or redeployed to perform different tasks as needed, enabling manufacturers to respond swiftly to new opportunities or challenges.
Sustainability and Environmental Impact
Automation through AMRs can also contribute to sustainability efforts.
By optimizing resource use, reducing waste, and improving energy efficiency, AMRs help manufacturers minimize their environmental footprint.
Case Studies: Successful AMR Implementations in Japan
Examining successful AMR implementations provides valuable insights into best practices and the tangible benefits of automation.
Automotive Manufacturing
A leading Japanese automotive manufacturer integrated AMRs into its assembly line to transport heavy components.
This implementation resulted in a 20% increase in production efficiency and a significant reduction in workplace injuries related to material handling.
Electronics Production
In the electronics sector, a major manufacturer deployed AMRs for precise component placement and inspection.
The use of AMRs enhanced product quality, reduced defect rates by 15%, and shortened the overall production cycle time.
Food and Beverage Processing
A Japanese food processing company utilized AMRs to automate the packaging and sorting processes.
This led to improved hygiene standards, faster processing times, and the ability to meet growing demand without compromising quality.
Future Trends in AMR Technology
The future of AMRs in Japanese manufacturing is promising, with several emerging trends set to further revolutionize the industry.
Advanced AI and Machine Learning
The integration of advanced AI and machine learning will enable AMRs to perform more complex tasks, adapt to changing environments, and make autonomous decisions with greater accuracy.
Collaborative Robots (Cobots)
The development of collaborative robots that can work alongside human workers safely and efficiently will enhance the versatility and applicability of AMRs in various manufacturing settings.
Enhanced Connectivity and IoT Integration
Greater connectivity through the Internet of Things (IoT) will allow AMRs to communicate seamlessly with other devices and systems, facilitating a more interconnected and responsive manufacturing ecosystem.
Strategic Considerations for Manufacturers
When adopting AMRs, manufacturers must consider several strategic factors to ensure successful implementation and long-term benefits.
Cost-Benefit Analysis
Conduct a comprehensive cost-benefit analysis to evaluate the financial implications of AMR integration.
Consider both the upfront costs and the long-term savings in labor, efficiency, and quality improvements.
Customization and Scalability
Ensure that the AMR solutions you choose can be customized to fit your specific manufacturing needs and are scalable to accommodate future growth and technological advancements.
Partnerships and Collaborations
Forge strategic partnerships with AMR suppliers, technology providers, and industry experts to leverage their expertise and stay ahead of technological trends.
Impact on Workforce and Organizational Culture
The introduction of AMRs influences the workforce and organizational culture, necessitating thoughtful management and adaptation.
Workforce Transformation
AMRs automate certain tasks, which may lead to workforce transformation rather than job displacement.
Employees can be retrained to manage and operate AMRs, as well as to focus on more strategic and value-added activities within the organization.
Cultural Shift Towards Innovation
Embracing AMRs fosters a culture of innovation and continuous improvement.
Encouraging employees to collaborate with robotic systems and embrace new technologies can drive organizational growth and agility.
Regulatory and Compliance Considerations
Compliance with regulatory standards is essential when implementing AMRs in manufacturing processes.
Safety Standards
Ensure that AMRs adhere to safety standards and regulations to protect workers and maintain a safe working environment.
This includes implementing appropriate safety protocols and conducting regular safety audits.
Data Privacy and Security
With AMRs collecting and processing vast amounts of data, it is crucial to address data privacy and security concerns.
Implement robust cybersecurity measures to protect sensitive information and prevent unauthorized access to AMR systems.
Conclusion
Autonomous Mobile Robots are revolutionizing Japanese manufacturing by enhancing efficiency, quality, and competitiveness.
Their integration into procurement and purchasing processes optimizes supply chain operations, while their role in production management streamlines workflows and reduces costs.
Despite challenges such as initial investment and the need for skilled personnel, the advantages of AMRs—ranging from improved accuracy to data-driven decision-making—are undeniable.
As technology continues to advance, AMRs will become even more integral to manufacturing processes, driving innovation and sustainability.
By adopting best practices, fostering strategic partnerships, and addressing workforce and regulatory considerations, Japanese manufacturers can fully harness the potential of AMRs, securing their position as leaders in the global manufacturing landscape.
資料ダウンロード
QCD調達購買管理クラウド「newji」は、調達購買部門で必要なQCD管理全てを備えた、現場特化型兼クラウド型の今世紀最高の購買管理システムとなります。
ユーザー登録
調達購買業務の効率化だけでなく、システムを導入することで、コスト削減や製品・資材のステータス可視化のほか、属人化していた購買情報の共有化による内部不正防止や統制にも役立ちます。
NEWJI DX
製造業に特化したデジタルトランスフォーメーション(DX)の実現を目指す請負開発型のコンサルティングサービスです。AI、iPaaS、および先端の技術を駆使して、製造プロセスの効率化、業務効率化、チームワーク強化、コスト削減、品質向上を実現します。このサービスは、製造業の課題を深く理解し、それに対する最適なデジタルソリューションを提供することで、企業が持続的な成長とイノベーションを達成できるようサポートします。
オンライン講座
製造業、主に購買・調達部門にお勤めの方々に向けた情報を配信しております。
新任の方やベテランの方、管理職を対象とした幅広いコンテンツをご用意しております。
お問い合わせ
コストダウンが利益に直結する術だと理解していても、なかなか前に進めることができない状況。そんな時は、newjiのコストダウン自動化機能で大きく利益貢献しよう!
(Β版非公開)