- お役立ち記事
- A multi-supplier strategy to prepare for supplier supply disruptions: A guide for purchasing managers
A multi-supplier strategy to prepare for supplier supply disruptions: A guide for purchasing managers
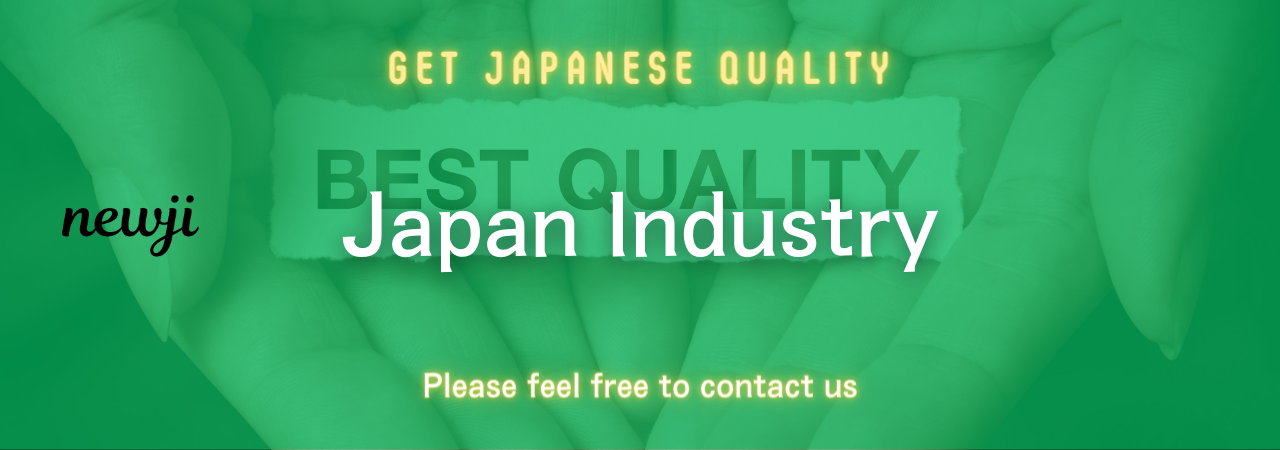
目次
Introduction to Multi-Supplier Strategy
In today’s ever-changing business environment, supply chain disruptions are increasingly common, posing significant challenges for purchasing managers.
A multi-supplier strategy is one of the best approaches to mitigate these risks, enabling organizations to maintain operations even in the face of unforeseen disruptions.
This strategy involves diversifying supplier networks to reduce dependence on a single supplier and to enhance the overall resilience of the supply chain.
Why Consider a Multi-Supplier Strategy?
The advantages of implementing a multi-supplier strategy are numerous.
First and foremost, it provides a safeguard against supply shortages and delivery delays, allowing businesses to continue functioning smoothly without major interruptions.
When reliant on a single supplier, any disruption in their operations can directly impact your ability to deliver products or services to customers.
Moreover, a multi-supplier approach promotes competitive pricing.
Having multiple suppliers can create competition among them to offer the best deals, potentially reducing costs.
Purchasing managers can leverage this competition by negotiating better terms and conditions with suppliers.
Additionally, employing multiple suppliers fosters innovation.
Different suppliers may offer varying quality, technologies, and ideas that could lead to improvements in the products or services provided.
By tapping into a broader supplier network, purchasing managers can harness diverse expertise and innovative solutions.
Evaluating Supplier Options
The first step in developing a multi-supplier strategy is evaluating potential suppliers.
This involves thoroughly researching and assessing their capabilities, quality standards, and reliability.
Factors to consider during evaluation include the supplier’s financial stability, production capacity, technological capabilities, and their history of performance with other clients.
Purchasing managers should also examine the geographic location of suppliers.
Choosing suppliers from different regions can mitigate the risk of regional disruptions, such as natural disasters or political instability.
Additionally, it’s crucial to assess suppliers based on compliance with legal and ethical standards.
Ensuring that suppliers align with your company’s values and meet required certifications can prevent legal issues and damage to your organization’s reputation.
Integrating a Risk Management Plan
A critical component of a multi-supplier strategy is integrating an effective risk management plan.
This plan should outline procedures for assessing and mitigating risks associated with each supplier.
By identifying potential risks in advance, purchasing managers can develop contingency plans to address supplier disruptions swiftly and effectively.
It is also important to continuously monitor the performance of all suppliers and conduct regular risk assessments.
This ongoing evaluation will help to detect issues early and maintain a robust supply chain.
Building Strong Supplier Relationships
While having multiple suppliers is beneficial, maintaining strong relationships with them is equally important.
Collaboration and communication are key to ensuring smooth operations.
Purchasing managers should foster open lines of communication with suppliers, ensuring expectations are clear from the outset.
This includes discussing quality standards, delivery timelines, pricing structures, and any other essential details.
Establishing mutual trust and respect can lead to long-term partnerships and a more reliable supply chain.
Furthermore, it’s beneficial to engage in collaborative planning with suppliers.
Working together to forecast demand, align production schedules, and address potential challenges enhances the overall efficiency and consistency of the supply chain.
Implementing a Supplier Performance Measurement System
To ensure that all suppliers meet expectations, establish a performance measurement system.
This system should include key performance indicators (KPIs) relevant to your industry and supply chain needs.
Common KPIs may include delivery accuracy, quality of goods, responsiveness, and compliance with agreements.
Regularly reviewing supplier performance against these KPIs will help identify areas for improvement and hold suppliers accountable.
It also facilitates informed decision-making regarding supplier selection or retention.
Adapting to Market Changes
The business landscape is dynamic, with market conditions and consumer demands constantly evolving.
As such, a multi-supplier strategy should be flexible enough to adapt to these changes.
Purchasing managers need to stay informed about industry trends and anticipate shifts that may impact the supply chain.
Being proactive and adapting supplier networks accordingly can help ensure continued quality and cost-effectiveness.
Moreover, fostering innovation within the supplier network can support adaptation.
Suppliers that prioritize research and development might offer new solutions that better align with emerging market trends and technological advancements.
Conclusion: Strengthening Supply Chain Resilience
Implementing a multi-supplier strategy is a proactive approach that purchasing managers can take to enhance supply chain resilience.
By diversifying supplier networks, evaluating and managing risks, and building solid relationships, organizations can better withstand supply disruptions.
As the market changes, maintaining flexibility and a proactive attitude will ensure that supply chains remain robust and efficient.
Ultimately, a well-executed multi-supplier strategy can provide significant competitive advantages, safeguarding businesses against unforeseen challenges and positioning them for sustainable success.
資料ダウンロード
QCD調達購買管理クラウド「newji」は、調達購買部門で必要なQCD管理全てを備えた、現場特化型兼クラウド型の今世紀最高の購買管理システムとなります。
ユーザー登録
調達購買業務の効率化だけでなく、システムを導入することで、コスト削減や製品・資材のステータス可視化のほか、属人化していた購買情報の共有化による内部不正防止や統制にも役立ちます。
NEWJI DX
製造業に特化したデジタルトランスフォーメーション(DX)の実現を目指す請負開発型のコンサルティングサービスです。AI、iPaaS、および先端の技術を駆使して、製造プロセスの効率化、業務効率化、チームワーク強化、コスト削減、品質向上を実現します。このサービスは、製造業の課題を深く理解し、それに対する最適なデジタルソリューションを提供することで、企業が持続的な成長とイノベーションを達成できるようサポートします。
オンライン講座
製造業、主に購買・調達部門にお勤めの方々に向けた情報を配信しております。
新任の方やベテランの方、管理職を対象とした幅広いコンテンツをご用意しております。
お問い合わせ
コストダウンが利益に直結する術だと理解していても、なかなか前に進めることができない状況。そんな時は、newjiのコストダウン自動化機能で大きく利益貢献しよう!
(Β版非公開)