- お役立ち記事
- How to contract with multiple suppliers to reduce procurement risks
How to contract with multiple suppliers to reduce procurement risks
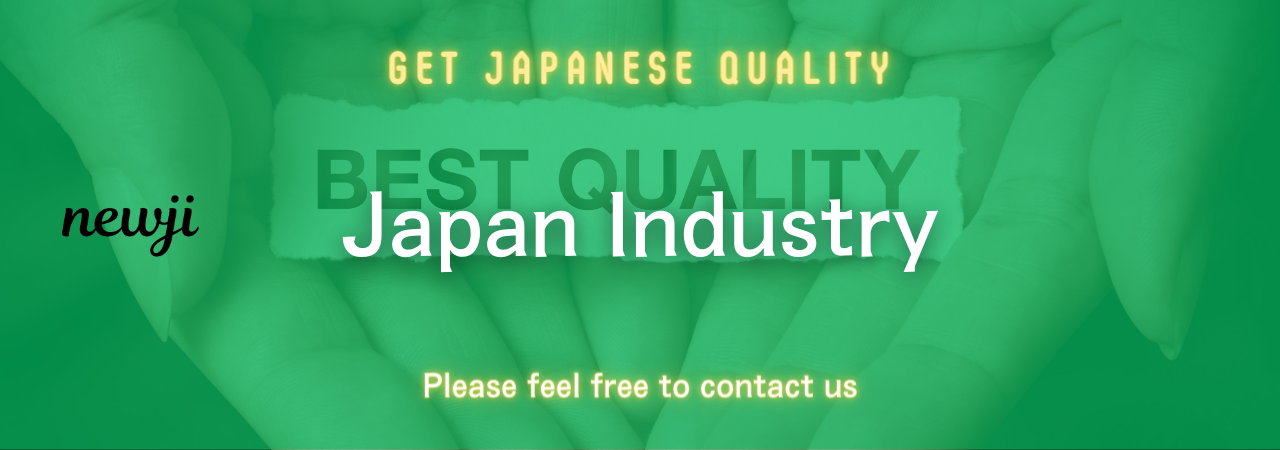
目次
Understanding Procurement Risks
In the world of procurement, risks are an inevitable part of the process.
These risks can arise from various sources, including supplier reliability, market fluctuations, geopolitical tensions, and more.
Effective procurement strategies aim to mitigate these risks to ensure a smooth supply chain and stable business operations.
One of the most effective methods to reduce procurement risks is to contract with multiple suppliers.
This strategic approach distributes risk and provides a safety net should one supplier encounter issues.
Before diving into the details of contracting with multiple suppliers, it is essential to understand the nature of procurement risks and their potential impact on a business.
Types of Procurement Risks
Procurement risks can be broadly categorized into several types:
1. **Supplier Risks**: These involve the potential failure of a supplier to deliver goods or services as agreed.
Factors such as financial instability, operational disruptions, or quality issues can lead to supplier risks.
2. **Market Risks**: These are associated with changes in market conditions, such as price volatility, changes in demand, or new regulations that can affect procurement.
3. **Operational Risks**: These risks include internal issues within an organization, such as inefficient processes or technology failures that can affect the procurement process.
4. **Geopolitical Risks**: Factors such as political instability, trade wars, or regulatory changes in a supplier’s country can significantly impact procurement.
5. **Natural Disasters**: Unpredictable events like earthquakes, floods, or other natural disasters can disrupt the supply chain.
The Benefits of Contracting with Multiple Suppliers
Contracting with multiple suppliers is a strategy that can offer numerous benefits:
– **Risk Mitigation**: By diversifying suppliers, a business reduces its dependency on a single supplier, minimizing the risk of supply chain disruptions.
– **Better Negotiation Power**: Engaging multiple suppliers can enhance a company’s bargaining position, leading to more competitive pricing and terms.
– **Increased Flexibility**: With multiple suppliers, businesses can quickly adapt to changes in demand or supply chain interruptions.
– **Innovation and Quality Improvement**: Access to a broader pool of suppliers increases the potential for innovative solutions and improved product quality.
Steps to Implement a Multi-Supplier Strategy
To successfully implement a multi-supplier strategy, businesses should follow these essential steps:
1. Identify and Assess Suppliers
The first step is to identify potential suppliers and evaluate their capabilities.
This assessment should consider factors such as financial stability, production capacity, quality standards, and reliability.
Conduct thorough due diligence to ensure each supplier meets your business requirements.
2. Define Criteria for Supplier Selection
Clearly define the criteria for selecting suppliers.
These criteria should align with your business goals, such as cost-effectiveness, quality, lead time, and risk tolerance.
Weighted scoring systems can help in making objective decisions.
3. Develop Contracts with Clear Terms
Once suppliers are selected, develop contracts that outline clear terms and conditions.
Ensure that the contracts include clauses for quality standards, delivery schedules, and contingencies in case of supply chain disruptions.
Flexibility clauses can be beneficial to adapt to changing circumstances without renegotiating the entire agreement.
4. Monitor and Evaluate Supplier Performance
Regularly monitor supplier performance to ensure compliance with contractual terms.
Establish key performance indicators (KPIs) to evaluate performance metrics such as delivery times, quality, and responsiveness.
Engage in regular communication with suppliers to address any issues promptly.
5. Foster Strong Supplier Relationships
Building strong relationships with suppliers is crucial for long-term success.
Maintain open lines of communication, offer feedback, and work collaboratively to resolve challenges.
Mutually beneficial relationships can lead to improved service levels and collaboration on innovative solutions.
Challenges of Managing Multiple Suppliers
While contracting with multiple suppliers has its advantages, it also presents challenges:
– **Complexity**: Managing multiple supplier relationships can be complex and time-consuming.
It requires dedicated resources to handle communication, negotiations, and performance monitoring.
– **Integration Issues**: Integrating multiple suppliers into existing procurement processes and systems can pose challenges, especially if suppliers use different technologies or processes.
– **Risk of Quality Variation**: With multiple suppliers, there is a potential risk of inconsistent quality across different suppliers, which requires careful monitoring.
– **Potential Increase in Costs**: While competition among suppliers can reduce costs, having multiple suppliers may lead to increased administrative expenses.
Conclusion
Procurement is a critical aspect of business operations, and effective risk management is essential to ensure a stable and reliable supply chain.
Contracting with multiple suppliers is a proven strategy to mitigate procurement risks and enhance flexibility and competitiveness.
By carefully selecting suppliers, defining clear terms, and fostering strong relationships, businesses can successfully implement a multi-supplier strategy.
While challenges exist, the benefits of distributing risk across multiple suppliers often outweigh the complexities involved.
Ultimately, a well-executed multi-supplier approach can lead to improved resilience and operational efficiency, positioning a business for long-term success.
資料ダウンロード
QCD調達購買管理クラウド「newji」は、調達購買部門で必要なQCD管理全てを備えた、現場特化型兼クラウド型の今世紀最高の購買管理システムとなります。
ユーザー登録
調達購買業務の効率化だけでなく、システムを導入することで、コスト削減や製品・資材のステータス可視化のほか、属人化していた購買情報の共有化による内部不正防止や統制にも役立ちます。
NEWJI DX
製造業に特化したデジタルトランスフォーメーション(DX)の実現を目指す請負開発型のコンサルティングサービスです。AI、iPaaS、および先端の技術を駆使して、製造プロセスの効率化、業務効率化、チームワーク強化、コスト削減、品質向上を実現します。このサービスは、製造業の課題を深く理解し、それに対する最適なデジタルソリューションを提供することで、企業が持続的な成長とイノベーションを達成できるようサポートします。
オンライン講座
製造業、主に購買・調達部門にお勤めの方々に向けた情報を配信しております。
新任の方やベテランの方、管理職を対象とした幅広いコンテンツをご用意しております。
お問い合わせ
コストダウンが利益に直結する術だと理解していても、なかなか前に進めることができない状況。そんな時は、newjiのコストダウン自動化機能で大きく利益貢献しよう!
(Β版非公開)