- お役立ち記事
- What are the important indicators for purchasing departments to evaluate supplier performance?
What are the important indicators for purchasing departments to evaluate supplier performance?
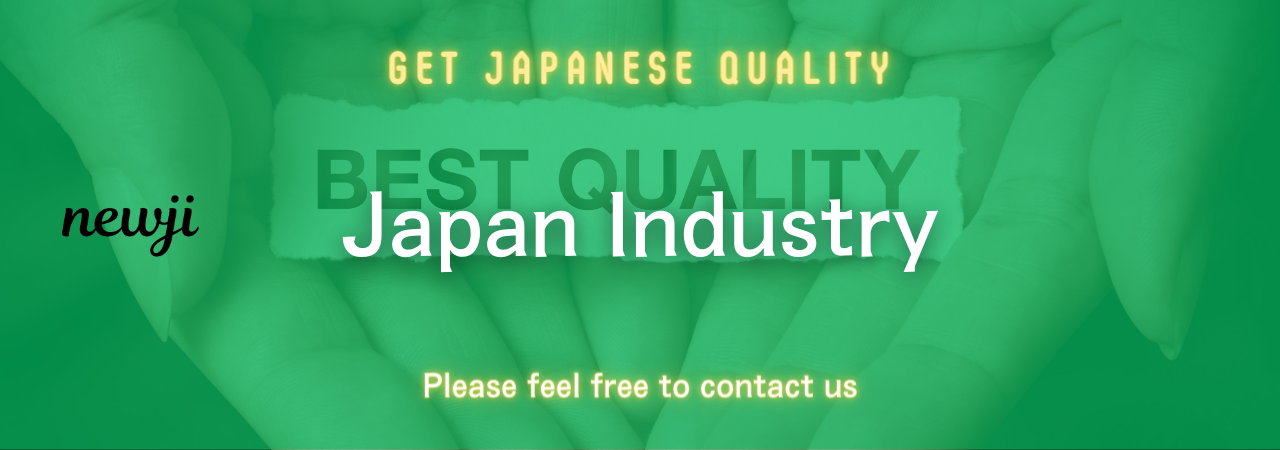
目次
Understanding Supplier Performance Evaluation
For any business, especially those with a dedicated purchasing department, evaluating supplier performance is a critical task.
Ensuring that suppliers meet their obligations and maintain consistent quality can significantly impact a company’s operations and customer satisfaction.
Thus, having clear indicators to assess supplier performance is essential.
Why is Supplier Performance Important?
Supplier performance directly affects a company’s bottom line and overall customer service experience.
Efficient and effective suppliers help businesses operate smoothly by delivering products on time, maintaining quality, and sometimes even providing innovative solutions.
Poor performance, on the other hand, can lead to production delays, increased costs, and dissatisfied customers.
Therefore, regularly evaluating supplier performance helps in establishing long-term, productive business relationships.
Key Indicators to Evaluate Supplier Performance
To accurately assess supplier performance, purchasing departments should consider several key indicators.
These metrics provide a comprehensive view of how a supplier is performing and where improvements might be needed.
1. Delivery Performance
Punctuality in deliveries is a fundamental aspect of good supplier performance.
The ability of a supplier to deliver goods on or before the agreed-upon time indicates reliability.
Purchasing departments should monitor delivery schedules, calculate the percentage of on-time deliveries, and analyze any recurring patterns of delays.
2. Quality of Products
Consistent quality is essential for maintaining a good reputation and meeting customer expectations.
To measure this, purchasing departments can look at the defect rates and the number of returns.
Quality audits and compliance with industry standards also provide insight into a supplier’s commitment to quality.
3. Cost Competitiveness
While minimizing costs shouldn’t compromise quality, evaluating whether a supplier offers competitive pricing is important.
This includes analyzing the cost-to-value ratio and comparing it with other potential suppliers.
Cost transparency and the ability to provide cost breakdowns also help in evaluating this indicator.
4. Communication and Responsiveness
Effective communication is the backbone of any successful supplier relationship.
Assessing how promptly and effectively a supplier responds to inquiries, issues, or order changes is crucial.
A responsive supplier helps in quickly resolving problems and making necessary adjustments to meet changing demands.
5. Flexibility and Adaptability
In the fast-paced business environment, the ability of a supplier to adapt to changes is invaluable.
This includes adjusting to increased demand, modifying orders, or accommodating special requests.
Suppliers who exhibit flexibility are better partners because they can help navigate unforeseen circumstances smoothly.
6. Compliance with Regulations
Suppliers must adhere to all relevant legal and regulatory standards.
This includes health and safety regulations, environmental laws, and labor practices.
Non-compliance can result in legal ramifications and damage to the company’s reputation.
Therefore, regular checks and adherence to compliance standards are imperative.
7. Relationship and Support
Beyond transactions, building strong supplier relationships can lead to strategic advantages.
Assess how supportive and cooperative a supplier is in terms of contributing to your company’s goals.
This might involve joint planning meetings, strategic alignment, or value-added services.
Implementing a Supplier Evaluation System
Implementing a structured supplier evaluation system can streamline the evaluation process.
Here are some steps that purchasing departments can take:
1. Develop a Scoring System
Create a scoring system based on the chosen indicators.
Assign weights to each indicator based on their importance to your specific business needs.
This provides a quantified basis to compare and rank suppliers.
2. Regular Performance Reviews
Conduct regular performance reviews to keep track of supplier performance over time.
These reviews should be documented and used for ongoing assessments to identify trends and areas for improvement.
3. Feedback and Communication
After evaluating suppliers, provide them with constructive feedback.
Open communication about strengths and areas for improvement can foster better relationships and performance.
4. Use Technology
Leverage technology and software tools to automate and simplify the supplier evaluation process.
Digital dashboards can help track performance indicators in real time, providing instant visibility into supplier performance.
Conclusion
Evaluating supplier performance is an ongoing process that requires attention to various indicators.
By focusing on delivery performance, quality, cost competitiveness, communication, flexibility, compliance, and relationship building, purchasing departments can choose and maintain the best suppliers for their needs.
Implementing a structured evaluation system ensures informed decisions and enhances the supply chain’s overall efficiency and reliability.
Through consistent evaluation and communication, companies can foster stronger supplier partnerships that contribute to long-term success.
資料ダウンロード
QCD調達購買管理クラウド「newji」は、調達購買部門で必要なQCD管理全てを備えた、現場特化型兼クラウド型の今世紀最高の購買管理システムとなります。
ユーザー登録
調達購買業務の効率化だけでなく、システムを導入することで、コスト削減や製品・資材のステータス可視化のほか、属人化していた購買情報の共有化による内部不正防止や統制にも役立ちます。
NEWJI DX
製造業に特化したデジタルトランスフォーメーション(DX)の実現を目指す請負開発型のコンサルティングサービスです。AI、iPaaS、および先端の技術を駆使して、製造プロセスの効率化、業務効率化、チームワーク強化、コスト削減、品質向上を実現します。このサービスは、製造業の課題を深く理解し、それに対する最適なデジタルソリューションを提供することで、企業が持続的な成長とイノベーションを達成できるようサポートします。
オンライン講座
製造業、主に購買・調達部門にお勤めの方々に向けた情報を配信しております。
新任の方やベテランの方、管理職を対象とした幅広いコンテンツをご用意しております。
お問い合わせ
コストダウンが利益に直結する術だと理解していても、なかなか前に進めることができない状況。そんな時は、newjiのコストダウン自動化機能で大きく利益貢献しよう!
(Β版非公開)