- お役立ち記事
- How to minimize the cost impact associated with tariff rate changes Measures that purchasing departments should take
How to minimize the cost impact associated with tariff rate changes Measures that purchasing departments should take
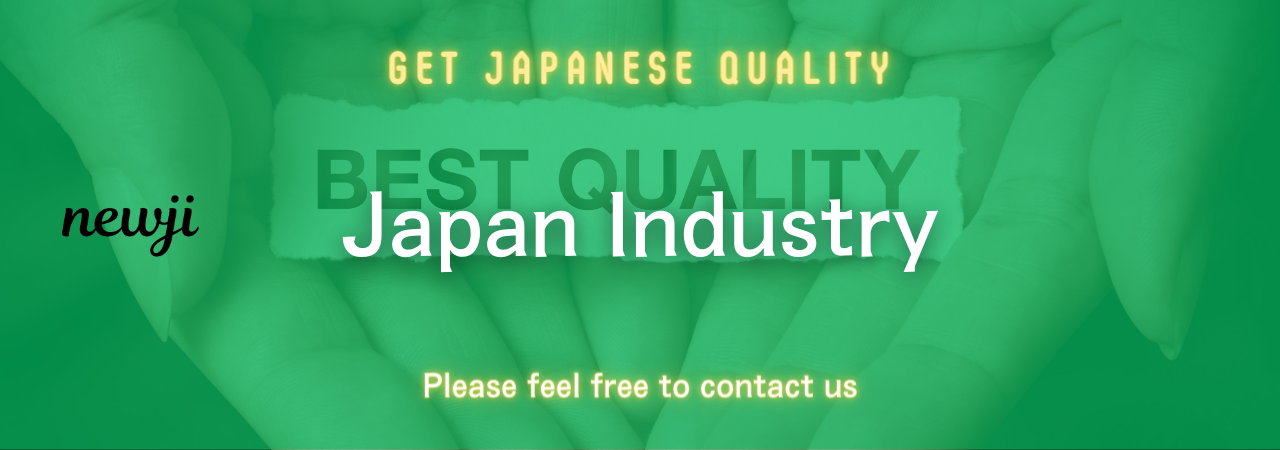
目次
Understanding Tariff Rate Changes
Tariff rate changes are a common occurrence in the global market, often stemming from political shifts, trade agreements, or economic policies.
These changes can have significant impacts on businesses, particularly in terms of cost.
The purchasing department of any organization must be proactive in adapting to these shifts to minimize financial repercussions.
Understanding what tariff rates are and how they affect businesses is the first step in mitigating their impact.
What Are Tariff Rates?
Tariff rates are taxes imposed by governments on goods and services imported from other countries.
They are primarily used to restrict trade by increasing the price of imported goods, making them less competitive against local products.
While they are meant to protect domestic industries, they can also lead to increased costs for businesses that rely on imported goods.
Why Tariff Rate Changes Matter
Fluctuations in tariff rates can significantly affect a company’s bottom line.
An increase in tariffs can raise the cost of raw materials or finished goods, potentially leading to higher operational costs.
This increase might be passed on to consumers through higher prices, potentially reducing competitiveness and demand.
Conversely, a decrease in tariff rates may present an opportunity for cost savings and increased market advantage.
Steps to Minimize Cost Impact
Given the potential financial impact of tariff rate changes, purchasing departments need to be strategic in their approach.
Here are some measures they can take:
1. Stay Informed on Trade Policies
One of the most critical actions is to stay updated with the latest developments in trade policies and tariff changes.
This involves regularly monitoring government announcements, international trade agreements, and global market trends.
Being informed allows companies to anticipate changes and plan accordingly.
2. Diversify Supply Sources
Relying on a single country or supplier for materials can be risky in the face of tariff changes.
Broadening the supplier base across multiple countries can help mitigate the risk of increased costs from any single region.
Diversification ensures that if tariffs rise unexpectedly in one area, the company can quickly pivot to alternative suppliers.
3. Build Strong Relationships with Suppliers
Establishing and maintaining strong relationships with suppliers can lead to better negotiation outcomes.
Suppliers may be willing to absorb some of the increased costs or offer discounts as a result of long-term partnerships.
Building these relationships requires regular communication and a mutual understanding of business needs and pressures.
4. Negotiate Long-Term Contracts
Negotiating long-term contracts with suppliers can provide price stability.
These contracts can include clauses that protect against sudden price increases due to tariffs.
Regularly reviewing and updating these contracts ensures they remain advantageous under changing economic conditions.
Strategic Planning and Innovation
Beyond immediate actions, purchasing departments should engage in strategic planning and innovation to prepare for long-term tariff rate challenges.
5. Implement Cost-Control Strategies
Cost-control strategies such as cost re-engineering and process optimization can help offset the increased expenses associated with tariffs.
Purchasing departments can work closely with other departments to identify areas for cost reduction and efficiency improvement.
6. Embrace Technology
Leveraging technology like procurement software can significantly enhance the ability to manage costs effectively.
Such tools offer capabilities like analytics and forecasting, which help decision-makers understand the potential impact of tariff changes and make informed choices.
7. Foster Lean Inventory Practices
Adopting lean inventory practices can help reduce carrying costs and mitigate the impact of increased tariffs.
By maintaining just-in-time inventory systems and optimizing stock levels, businesses can reduce waste and maintain flexibility.
8. Explore Alternative Materials or Products
In some cases, switching to alternative materials that are less impacted by tariffs can be a cost-effective strategy.
This requires research and development efforts to ensure that any substitutes meet quality standards while offering cost benefits.
Collaborative Efforts
Collaboration is key when dealing with tariff rate changes.
Working together with industry peers, trade associations, and governmental agencies can provide additional support and insights.
9. Participate in Industry Forums
Engaging in industry forums and trade associations fosters knowledge exchange and provides a platform to voice concerns and challenges.
These platforms can also offer insights into upcoming policy changes and collective strategies to address tariff-related issues.
10. Partner with Supply Chain Experts
Partnering with supply chain consultants or experts offers an external perspective and specialized expertise in managing tariff impacts.
These professionals can assist in identifying risks and developing comprehensive strategies tailored to specific business needs.
Conclusion
Tariff rate changes can pose significant challenges for businesses, impacting costs and competitive positioning.
However, by implementing strategic measures, purchasing departments can minimize these impacts and maintain operational efficiency.
Staying informed, diversifying supply sources, building strong supplier relationships, and leveraging technology are vital steps in navigating the complexities of tariff rate changes.
Through collaborative efforts and proactive planning, businesses can ensure resilience and adaptability in the face of shifting economic landscapes.
資料ダウンロード
QCD調達購買管理クラウド「newji」は、調達購買部門で必要なQCD管理全てを備えた、現場特化型兼クラウド型の今世紀最高の購買管理システムとなります。
ユーザー登録
調達購買業務の効率化だけでなく、システムを導入することで、コスト削減や製品・資材のステータス可視化のほか、属人化していた購買情報の共有化による内部不正防止や統制にも役立ちます。
NEWJI DX
製造業に特化したデジタルトランスフォーメーション(DX)の実現を目指す請負開発型のコンサルティングサービスです。AI、iPaaS、および先端の技術を駆使して、製造プロセスの効率化、業務効率化、チームワーク強化、コスト削減、品質向上を実現します。このサービスは、製造業の課題を深く理解し、それに対する最適なデジタルソリューションを提供することで、企業が持続的な成長とイノベーションを達成できるようサポートします。
オンライン講座
製造業、主に購買・調達部門にお勤めの方々に向けた情報を配信しております。
新任の方やベテランの方、管理職を対象とした幅広いコンテンツをご用意しております。
お問い合わせ
コストダウンが利益に直結する術だと理解していても、なかなか前に進めることができない状況。そんな時は、newjiのコストダウン自動化機能で大きく利益貢献しよう!
(Β版非公開)