- お役立ち記事
- Logistics network and inventory management methods for successful global procurement
Logistics network and inventory management methods for successful global procurement
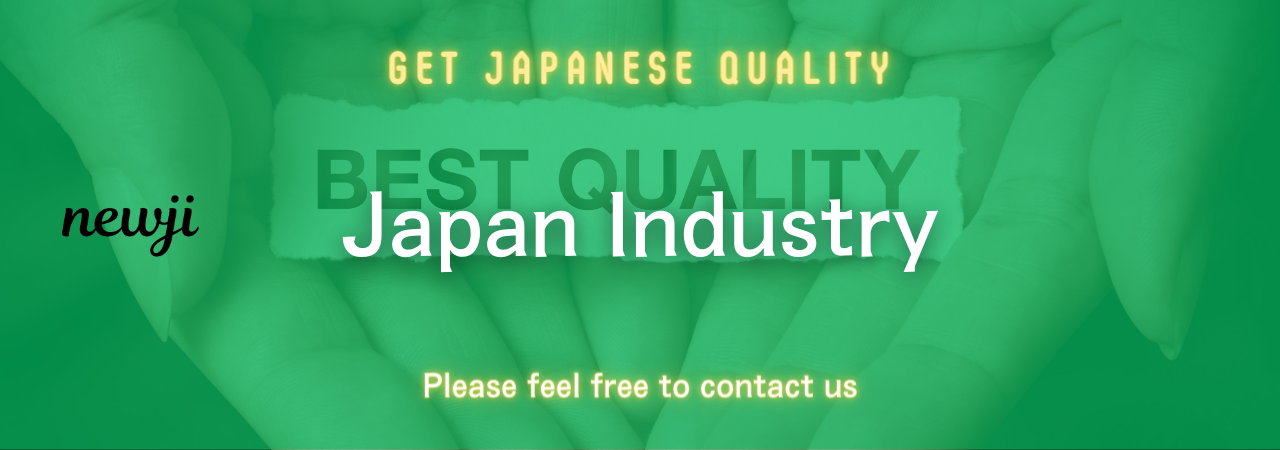
目次
Understanding Global Procurement
Global procurement refers to the process where businesses acquire goods or services beyond national boundaries to capitalize on cost benefits, improved quality, and a broader supplier base.
This complex process involves coordinating various logistical operations, while carefully managing inventory to minimize costs and meet customer demands effectively.
As businesses expand and markets become more interconnected, the focus on enhancing logistics networks and mastering inventory management methods has never been more critical.
The Importance of a Robust Logistics Network
A successful global procurement strategy relies heavily on the strength of a company’s logistics network.
But what exactly makes a logistics network robust?
At its core, a logistics network consists of suppliers, manufacturing facilities, warehouses, distribution centers, and transportation services working together seamlessly.
Businesses need to ensure that these components are well-integrated to streamline operations and reduce transit times.
Fatigued supply lines can result in delays, increased costs, and dissatisfied customers.
Efficient logistics networks enable companies to react quickly to market changes and adapt their supply chain strategies accordingly.
Optimizing Transportation
Transportation optimization is a vital piece of the logistics puzzle.
By choosing the right mix of transportation modes – whether air, sea, road, or rail – businesses can save on costs and ensure timely deliveries.
Utilizing technologies like GPS tracking and route optimization software further enhances visibility and efficiency across the network.
Such tools enable companies to make data-driven decisions, predict disruptions, and optimize routes for cost savings and faster transit times.
Leverage Technology
Technology integration forms the backbone of a modern logistics network.
By leveraging software solutions such as Warehouse Management Systems (WMS), Transportation Management Systems (TMS), and Enterprise Resource Planning (ERP) systems, companies can automate processes, reduce errors, and maintain consistent updates across the supply chain.
These technological improvements contribute significantly to streamlined operations, allowing for real-time tracking, inventory management, and analytics that predict future needs.
Strategic Inventory Management
Inventory management is another cornerstone of successful global procurement.
It involves the strategy of determining the right amount of stock to meet demand without incurring excessive holding costs.
The balance between having enough inventory to fulfill customer orders while minimizing overstock is critical.
Just-in-Time (JIT) Approach
The Just-in-Time inventory system is a proactive method that maintains minimal inventory levels.
JIT philosophy is built on the idea of minimizing waste by receiving goods only as they are needed in the production process.
This approach necessitates close coordination with suppliers to ensure components are delivered precisely when required, reducing storage costs and waste.
However, JIT requires robust relationships and constant communication with suppliers to mitigate any risk from supply chain disruptions.
ABC Analysis
ABC analysis is a method of categorizing inventory based on its value and significance to the business.
Classifying items into three categories—A (high value, low quantity), B (moderate value, moderate quantity), and C (low value, high quantity)—helps businesses prioritize their focus.
Category A items require stringent management due to their impact on profitability, while Category C items, although numerous, demand less scrutiny.
By conducting regular ABC analyses, companies can ensure efficient allocation of resources and better inventory controls.
Effective Supplier Relationships
Successful global procurement hinges on cultivating strong relationships with suppliers.
Building strategic partnerships can lead to better negotiation terms, improved quality, and reduced lead times.
Supplier Evaluation
Conducting thorough supplier evaluations allows businesses to assess a supplier’s capability, reliability, and performance.
Key factors to consider include quality standards, pricing consistency, logistics capability, and financial stability.
Evaluating these factors helps in identifying trustworthy suppliers who can support the company’s global procurement strategy effectively.
Supplier Collaboration
Fostering collaboration beyond transactional interactions with suppliers can lead to innovative solutions and enhanced efficiency.
Joint efforts in process improvements, product innovation, and risk management can result in mutual benefits.
Regular communication and feedback loops with suppliers ensure alignment with procurement objectives and mutual understanding of challenges and opportunities.
Challenges in Global Procurement
Despite the potential benefits, global procurement comes with its own set of challenges, including:
Regulatory Compliance
Navigating international trade regulations requires awareness of different countries’ tariffs, duties, and legal restrictions.
Businesses must stay informed about regulatory changes that could impact procurement strategies, supply chain operations, and cost.
Currency Fluctuations
Currency exchange rate fluctuations can significantly affect procurement costs.
Companies can employ hedging strategies to mitigate risks associated with volatile currency markets.
Implementing forward contracts or currency options can stabilize financial outcomes.
Cultural Differences
Engaging with international suppliers often means dealing with diverse cultural norms and practices.
Being sensitive to cultural differences and understanding business etiquettes help in building healthy relationships and avoiding miscommunications.
Conclusion
Navigating the complexities of global procurement requires astute management of logistics networks and inventory strategies.
By investing in robust logistics networks, leveraging technology, optimizing transportation, and mastering inventory management methods such as JIT and ABC analysis, businesses can thrive in the global marketplace.
Strong supplier relationships, keen awareness of international challenges, and adaptability to market changes further enhance procurement success.
Ultimately, businesses that deploy these strategies effectively are better positioned to capitalize on the opportunities in global procurement.
資料ダウンロード
QCD調達購買管理クラウド「newji」は、調達購買部門で必要なQCD管理全てを備えた、現場特化型兼クラウド型の今世紀最高の購買管理システムとなります。
ユーザー登録
調達購買業務の効率化だけでなく、システムを導入することで、コスト削減や製品・資材のステータス可視化のほか、属人化していた購買情報の共有化による内部不正防止や統制にも役立ちます。
NEWJI DX
製造業に特化したデジタルトランスフォーメーション(DX)の実現を目指す請負開発型のコンサルティングサービスです。AI、iPaaS、および先端の技術を駆使して、製造プロセスの効率化、業務効率化、チームワーク強化、コスト削減、品質向上を実現します。このサービスは、製造業の課題を深く理解し、それに対する最適なデジタルソリューションを提供することで、企業が持続的な成長とイノベーションを達成できるようサポートします。
オンライン講座
製造業、主に購買・調達部門にお勤めの方々に向けた情報を配信しております。
新任の方やベテランの方、管理職を対象とした幅広いコンテンツをご用意しております。
お問い合わせ
コストダウンが利益に直結する術だと理解していても、なかなか前に進めることができない状況。そんな時は、newjiのコストダウン自動化機能で大きく利益貢献しよう!
(Β版非公開)